Can You Hydro Dip Wood? Exploring the Possibilities and Techniques!
Can You Hydro Dip Wood?
In the world of DIY projects and creative craftsmanship, hydro dipping has emerged as a captivating technique that allows artists and hobbyists to apply intricate designs and vibrant colors to a variety of surfaces. While most commonly associated with materials like plastic and metal, the question arises: can you hydro dip wood? This intriguing inquiry opens the door to a realm of possibilities, where traditional woodworking meets modern artistic expression. Whether you’re looking to revitalize an old piece of furniture or add a unique touch to your home decor, understanding the nuances of hydro dipping wood can unlock a new level of creativity.
Hydro dipping, also known as water transfer printing, involves immersing an object in a water-based solution that carries a film of paint or pattern. This method creates a stunning, seamless design that adheres to the contours of the item being dipped. While many people are familiar with hydro dipping plastic items like helmets or phone cases, applying this technique to wood introduces a different set of challenges and considerations. The porous nature of wood, combined with its varying finishes and textures, requires a careful approach to ensure a successful outcome.
As we delve deeper into the process of hydro dipping wood, we will explore the necessary preparations, the types of finishes that work best, and tips for
Understanding Hydro Dipping on Wood
Hydro dipping, also known as water transfer printing, is a method used to apply designs to various surfaces, including wood. This technique involves floating a patterned film on water, which is then transferred to the object by immersing it. While hydro dipping is commonly associated with plastics and metals, it can also be applied to wood, provided certain considerations are taken into account.
Preparation Steps for Hydro Dipping Wood
Before starting the hydro dipping process, proper preparation of the wood surface is crucial to ensure adherence and a quality finish. The following steps should be followed:
- Clean the Surface: Remove any dirt, grease, or existing finishes. This can be achieved by sanding the wood and using a suitable cleaner.
- Prime the Wood: Applying a base coat or primer specifically designed for hydro dipping enhances the adhesion of the film to the wood. Choose a color that contrasts with the film for better visibility of the design.
- Drying Time: Allow the primer to dry completely before moving on to the hydro dipping process.
Hydro Dipping Process for Wood
The actual hydro dipping process involves several key steps, each requiring precision and care. Below is a breakdown of the procedure:
- Film Selection: Choose a hydrographic film that suits your design preferences. Ensure it is compatible with wood surfaces.
- Water Temperature: Fill a container with water and maintain a temperature between 80°F and 100°F (27°C to 38°C) for optimal film activation.
- Film Activation: Lay the film on the surface of the water and spray a specialized activator to dissolve the film and prepare it for transfer.
- Dipping: Immerse the prepared wood piece at a consistent angle to allow the film to wrap around the surface evenly.
- Rinsing: After the wood is removed from the water, rinse it to remove any excess film residue.
Post-Dipping Finishing Touches
Once the hydro dipping is complete, finishing touches are essential to protect the design and enhance durability.
- Clear Coating: Apply a clear coat to seal the design and provide a protective layer against scratches and moisture.
- Curing Time: Allow the clear coat to cure fully as per the manufacturer’s recommendations to achieve maximum hardness and durability.
Table of Hydro Dipping Materials
The following table outlines the materials typically used in the hydro dipping process for wood:
Material | Purpose |
---|---|
Hydrographic Film | Design transfer |
Activator Spray | Film activation |
Primer | Base coat for adhesion |
Clear Coat | Protection and durability |
Water Container | For film application |
By understanding these steps and considerations, individuals can successfully hydro dip wood, achieving unique and customized finishes suitable for various projects.
Understanding Hydro Dipping on Wood
Hydro dipping, also known as water transfer printing, is a versatile technique often associated with plastics and metals. However, it can also be applied to wood, provided certain considerations are taken into account. The process involves transferring a printed design onto the surface of an object through a water-based film.
Preparation of the Wood Surface
Proper surface preparation is crucial for successful hydro dipping on wood. This process enhances adhesion and ensures a smooth finish.
- Sanding: Begin by sanding the wood surface to remove any imperfections. Use fine-grit sandpaper for a smooth finish.
- Cleaning: After sanding, clean the surface with a lint-free cloth to eliminate dust and debris.
- Sealing: Applying a wood primer or sealer is recommended to prevent water absorption, which can distort the wood and affect the final appearance.
Choosing the Right Hydro Dipping Film
Selecting an appropriate film is essential for achieving the desired outcome. The film should be compatible with the wood’s surface and the intended design.
- Types of Films:
- Polyester Films: Commonly used for hydro dipping; they adhere well to sealed wood surfaces.
- Water-Soluble Films: These can be used but may require a specific type of sealer to enhance durability.
The Hydro Dipping Process for Wood
The hydro dipping process involves several steps to ensure optimal results.
- Preparation of the Dipping Station:
- Fill a container with water, ensuring it’s deep enough for the item being dipped.
- Maintain a stable temperature to avoid film distortion.
- Applying the Hydrographic Film:
- Lay the film on the water surface, allowing it to expand and activate for a few seconds.
- Use a spray activator to prepare the film for the transfer.
- Dipping the Wood:
- Submerge the wood piece at a consistent angle to ensure an even application.
- Move the piece slowly to avoid bubbles and ensure complete coverage.
- Rinsing and Drying:
- After dipping, rinse the wood under clean water to remove any residual film.
- Allow it to dry completely before applying a clear coat.
Finishing Touches
After the hydro dipping process, several finishing steps are necessary to enhance durability and appearance.
- Clear Coating: Apply a clear polyurethane or acrylic coat to protect the design from scratches and moisture.
- Curing: Allow the clear coat to cure as per the manufacturer’s instructions to ensure maximum durability.
- Final Inspection: Check for any imperfections or bubbles in the finish and address them as needed.
Advantages of Hydro Dipping Wood
Hydro dipping offers several benefits when applied to wood, including:
- Versatility: A wide range of designs and colors can be used, from camouflage to intricate patterns.
- Customizability: Each piece can be uniquely designed, allowing for personalized creations.
- Durability: When properly sealed, the finish is resistant to wear and tear.
Challenges and Considerations
Despite its advantages, there are challenges to consider:
- Moisture Sensitivity: Wood is inherently porous; improper sealing can lead to warping or damage.
- Skill Level: Hydro dipping requires practice to master the technique effectively.
- Cost: Initial setup for hydro dipping can be expensive due to equipment and materials.
By understanding the intricacies of hydro dipping wood and following proper techniques, you can achieve stunning and long-lasting results in your projects.
Expert Insights on Hydro Dipping Wood
Dr. Emily Carter (Materials Scientist, WoodTech Innovations). “Hydro dipping wood is indeed possible, but it requires careful preparation. The wood must be properly sealed to prevent water absorption, which can compromise the finish and durability of the design. Additionally, using the right type of paint is crucial for achieving a vibrant and lasting effect.”
Mark Thompson (DIY Specialist, Crafting Today Magazine). “While hydro dipping is often associated with plastics and metals, wood can also be successfully used in this technique. However, it is essential to consider the grain and texture of the wood, as these factors can affect the final appearance. A smooth surface will yield better results.”
Lisa Nguyen (Artistic Finishing Expert, Creative Woodworks). “To hydro dip wood effectively, one must ensure that the wood is completely dry and free from any contaminants. The dipping process can create unique patterns, but achieving consistency across multiple pieces may require practice and experimentation with different paint combinations and techniques.”
Frequently Asked Questions (FAQs)
Can you hydro dip wood?
Yes, you can hydro dip wood. This process allows for unique designs and finishes on wooden surfaces by applying a water transfer printing technique.
What materials are needed for hydro dipping wood?
The materials required include a hydro dipping film, a container filled with water, an activator spray, and a clear coat for sealing the finished product.
How do you prepare wood for hydro dipping?
Preparation involves sanding the wood surface to ensure it is smooth, cleaning it to remove dust and oils, and applying a base coat of paint if desired.
What types of wood are best for hydro dipping?
Softwoods and hardwoods can both be used for hydro dipping, but it is advisable to use wood that has a smooth surface and is free of knots for optimal results.
How durable is the hydro dip finish on wood?
The durability of the hydro dip finish largely depends on the quality of the materials used and the application process. When properly sealed, it can be quite resilient against wear and tear.
Can hydro dipping be done outdoors?
While hydro dipping can technically be done outdoors, it is recommended to perform the process in a controlled environment to avoid contamination from dust, debris, or weather conditions.
hydro dipping wood is indeed a feasible and creative technique that allows for the application of intricate designs and patterns onto wooden surfaces. This process involves submerging the wood into a water-based solution containing paint, which adheres to the surface, resulting in a unique and visually appealing finish. It is essential to prepare the wood properly by sanding and priming it to ensure optimal adhesion of the paint and to achieve the desired aesthetic outcome.
Moreover, the hydro dipping process requires careful attention to detail, including the selection of appropriate paints and the use of a clear sealant to protect the final product. While hydro dipping can be performed at home with the right materials and techniques, it is advisable for beginners to practice on less valuable pieces to perfect their skills. This method not only enhances the appearance of wooden items but also allows for personalization, making it a popular choice among DIY enthusiasts and artisans.
Key takeaways from the discussion include the importance of surface preparation, the need for quality materials, and the protective measures necessary to ensure durability. Hydro dipping offers a versatile solution for transforming wood into custom pieces, thus expanding creative possibilities in woodworking and home decor. Overall, with proper execution, hydro dipping can yield stunning results that elevate the aesthetic appeal
Author Profile
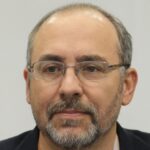
-
Darryl Norman is a seasoned entrepreneur and industry expert with a deep understanding of wood truss manufacturing and construction materials. As the President of Timberlake TrussWorks, LLC, Darryl played a pivotal role in shaping the company’s reputation for quality and precision. His leadership ensured that each truss met rigorous structural standards, providing builders with dependable components essential to their projects.
Beginning in 2025, Darryl Norman has shifted his focus to education and knowledge-sharing through an informative blog dedicated to wood truss manufacturing. Drawing from his extensive experience in the field, he provides in-depth insights into truss design, material selection, and construction techniques. This blog serves as a valuable resource for builders, contractors, and homeowners seeking practical guidance on truss systems and structural integrity.
Latest entries
- March 18, 2025General Wood TopicsWhat Color Is Ebony Wood? Unveiling the Rich Hues of This Luxurious Timber
- March 18, 2025Construction & FrameworkHow Can You Effectively Mount a Headboard to Your Wall?
- March 18, 2025General Wood TopicsCan Bees Really Eat Wood? Unraveling the Myths and Facts
- March 18, 2025General Wood TopicsDo Rabbits Really Chew on Wood? Exploring Their Eating Habits!