How Are Wood Pellets Made for Smokers? A Deep Dive into the Process!
When it comes to enhancing the flavors of grilled meats and vegetables, few methods are as beloved as the use of wood pellets in smokers. These small, cylindrical nuggets pack a powerful punch of smoky goodness, transforming ordinary meals into extraordinary culinary experiences. But have you ever wondered how these pellets are made? Understanding the process behind wood pellet production not only deepens your appreciation for this grilling staple but also informs your choices when selecting the best pellets for your smoking adventures. In this article, we will explore the fascinating journey of wood pellets, from raw materials to the final product, and uncover the craftsmanship that goes into creating the perfect blend of flavor and functionality.
The production of wood pellets for smokers begins with the careful selection of raw materials, typically sourced from sawmill byproducts, wood chips, and shavings. These materials are then processed through a series of steps that involve drying, grinding, and compressing to create the uniform pellets that smokers rely on. Each stage of this process is crucial, as it not only determines the quality of the pellets but also influences the flavor profile they impart during cooking.
Once the raw materials are prepared, they undergo a rigorous compression process that binds the wood fibers together without the use of additives or chemicals. This natural binding process is what gives wood pellets their unique
Raw Material Selection
The production of wood pellets for smokers begins with the careful selection of raw materials. High-quality wood is essential for creating pellets that burn efficiently and impart desirable flavors to food. The most commonly used types of wood include:
- Hickory: Offers a strong, smoky flavor.
- Mesquite: Provides a bold, earthy taste.
- Apple: Contributes a mild and sweet flavor.
- Cherry: Adds a fruity aroma and taste.
The choice of wood not only influences the flavor profile of the smoke but also affects the burning characteristics of the pellets.
Wood Preparation
After selecting the appropriate wood, the next step involves preparing the wood for pelletization. This preparation typically includes:
- Debarking: Removing the bark to reduce ash content and enhance flavor.
- Chipping: Breaking down larger logs into smaller chips to facilitate drying and pellet formation.
- Drying: Reducing the moisture content of the wood chips to a suitable level, generally between 4% to 10%. This is crucial as high moisture levels can lead to poor combustion and lower heat output.
Grinding and Mixing
Once the wood is dried, it is ground into a fine sawdust using industrial grinders. This sawdust is then mixed, if necessary, with other wood types to achieve a specific flavor profile or to enhance certain burning characteristics.
Pelletizing Process
The key process in creating wood pellets is pelletizing, which involves compressing the sawdust into small, cylindrical shapes. The steps in this process include:
- Feeding: The sawdust is fed into a pellet mill.
- Compression: The mill compresses the sawdust through a die, which shapes it into pellets.
- Cooling: After exiting the pellet mill, the pellets are hot and need to be cooled to retain their shape.
A typical pelletizing setup can be summarized in the following table:
Step | Description |
---|---|
Feeding | Sawdust is introduced into the pellet mill. |
Compression | Sawdust is compressed through a die to form pellets. |
Cooling | Pellets are cooled to maintain structural integrity. |
Packaging and Storage
Once the pellets are cooled, they are packaged for distribution. Proper packaging is essential to protect the pellets from moisture and contaminants. Common packaging materials include:
- Plastic bags: Often used for retail packaging.
- Bulk containers: Suitable for larger quantities.
Storage conditions also play a significant role in maintaining pellet quality. It is important to store wood pellets in a dry, cool place to prevent them from absorbing moisture, which can affect their burning properties.
Quality Control
Throughout the production process, quality control measures are implemented to ensure consistency and performance of the pellets. Testing includes:
- Moisture content analysis: Ensuring moisture levels are optimal for burning.
- Ash content testing: Determining the amount of ash produced during combustion.
- Density checks: Ensuring pellets are of uniform size and weight for efficient burning.
By adhering to these rigorous standards, manufacturers can produce high-quality wood pellets that enhance the smoking experience for users.
Raw Material Selection
The production of wood pellets for smokers begins with the careful selection of raw materials. The type of wood used significantly influences the flavor profile imparted to the food during smoking. Commonly chosen woods include:
- Hickory: Offers a strong, smoky flavor; ideal for red meats.
- Mesquite: Provides a robust, earthy taste; best for grilling.
- Apple: Delivers a mild, sweet flavor; great for poultry and pork.
- Cherry: Adds a subtle sweetness; works well with most meats.
The raw materials must be free from contaminants, such as chemicals or additives, to ensure a clean burn and flavor.
Wood Processing
After selecting the appropriate wood species, the next step is processing the wood into manageable sizes. This involves several stages:
- Debarking: Removing the bark from logs to prevent impurities in the final product.
- Chipping: Cutting the wood into small chips, typically 1 inch in size, to facilitate drying and milling.
- Drying: Reducing the moisture content of the wood chips to about 10-15%. This step is crucial, as excess moisture can lead to poor pellet quality.
Milling and Grinding
Once the wood is dried, the chips undergo milling. This process transforms the wood chips into a fine sawdust. The sawdust must have a uniform particle size, which is essential for proper pellet formation.
- Hammer Mills: Commonly used for grinding wood chips into sawdust.
- Screening: Ensures the sawdust is of consistent particle size, promoting efficient pelletization.
Pelletizing Process
The pelletization process involves several steps, including:
- Conditioning: Adding steam to the sawdust to soften it, which helps in binding the material during pellet formation.
- Pelletizing: The conditioned sawdust is compressed through a die in a pellet mill. This process generates heat and pressure, causing lignin in the wood to melt and bind the particles together.
The output of this stage is cylindrical pellets, typically ranging from 1/4 to 1/2 inch in diameter.
Cooling and Screening
After pelletizing, the hot pellets must be cooled to harden and stabilize their structure. This is usually done through:
- Cooling Systems: Utilizing air or water to reduce the temperature of the pellets.
- Screening: Removing fines (small particles) that may have formed during the pelletizing process.
Packaging and Storage
Finally, the wood pellets are packaged for distribution and sale. Proper packaging is vital to maintain pellet quality and prevent moisture absorption.
- Bulk Packaging: Common for large orders, typically in bags or bulk containers.
- Storage Conditions: Pellets should be stored in a dry, cool environment to prevent degradation.
Each of these steps contributes to the overall quality and flavor profile of the wood pellets, ensuring they meet the standards expected by consumers using them in smokers.
Understanding the Production of Wood Pellets for Smokers
Dr. Emily Carter (Biomass Energy Researcher, GreenTech Innovations). “The process of making wood pellets for smokers begins with sourcing high-quality hardwoods, which are then debarked and chipped. These chips are dried to a specific moisture content before being ground into a fine sawdust, ensuring optimal pellet formation and combustion efficiency.”
Mark Thompson (Senior Engineer, Pellet Technology Solutions). “After the sawdust is prepared, it undergoes a pelleting process where it is subjected to high pressure and temperature. This causes the lignin in the wood to melt and bind the particles together, forming dense pellets that are ideal for smoking due to their consistent size and burn characteristics.”
Linda Garcia (Culinary Expert and Smoking Specialist, Flavorful Grilling Magazine). “The choice of wood species significantly impacts the flavor profile of the smoke. Manufacturers often blend different types of wood to create unique flavor combinations, and the pellet-making process must preserve these characteristics to ensure a superior smoking experience for enthusiasts.”
Frequently Asked Questions (FAQs)
How are wood pellets made for smokers?
Wood pellets are produced by grinding wood into sawdust, which is then dried to reduce moisture content. The dried sawdust is compressed under high pressure, causing lignin in the wood to bind the particles together. The resulting pellets are then cooled and packaged for use in smokers.
What types of wood are commonly used for making smoking pellets?
Common types of wood used for smoking pellets include hickory, mesquite, apple, cherry, and oak. Each type of wood imparts a unique flavor profile to the food being smoked, allowing for various culinary experiences.
Are there any additives in wood pellets for smoking?
High-quality wood pellets for smoking typically contain no additives or fillers. They are made solely from natural wood, ensuring a pure smoking experience. However, some brands may offer flavored pellets that incorporate additional ingredients for enhanced taste.
How do I store wood pellets for optimal freshness?
To maintain optimal freshness, wood pellets should be stored in a cool, dry place, away from moisture and direct sunlight. Keeping them in a sealed container or bag helps prevent absorption of humidity, which can affect their burning quality.
Can I use any type of wood pellet in my smoker?
While many smokers can use various types of wood pellets, it is essential to check the manufacturer’s recommendations. Some smokers may perform better with specific pellet types, and certain woods may produce undesirable flavors if not compatible with the food being smoked.
How long do wood pellets last once opened?
Once opened, wood pellets can last for several months if stored properly. However, exposure to air and moisture can lead to degradation. It is advisable to use them within six months for the best flavor and performance.
Wood pellets are a popular choice for smokers due to their ability to produce consistent heat and flavorful smoke. The process of making wood pellets involves several key steps, starting with the selection of high-quality raw materials, typically hardwoods or fruitwoods. These materials are then chipped into small pieces, dried to reduce moisture content, and ground into a fine powder. This powder is subsequently compressed under high pressure to form pellets, which are then cooled and packaged for distribution.
The manufacturing process emphasizes the importance of maintaining low moisture levels and high density to ensure optimal burning characteristics. The use of additives is generally avoided, as pure wood pellets provide a cleaner burn and better flavor. Additionally, the choice of wood species significantly influences the flavor profile, with different types of wood imparting unique tastes to the food being smoked.
understanding how wood pellets are made is essential for smokers seeking to enhance their cooking experience. By selecting the right type of wood pellets, users can achieve superior flavor and performance in their smoking endeavors. This knowledge not only aids in making informed purchasing decisions but also contributes to a more enjoyable and flavorful barbecue experience.
Author Profile
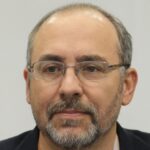
-
Darryl Norman is a seasoned entrepreneur and industry expert with a deep understanding of wood truss manufacturing and construction materials. As the President of Timberlake TrussWorks, LLC, Darryl played a pivotal role in shaping the company’s reputation for quality and precision. His leadership ensured that each truss met rigorous structural standards, providing builders with dependable components essential to their projects.
Beginning in 2025, Darryl Norman has shifted his focus to education and knowledge-sharing through an informative blog dedicated to wood truss manufacturing. Drawing from his extensive experience in the field, he provides in-depth insights into truss design, material selection, and construction techniques. This blog serves as a valuable resource for builders, contractors, and homeowners seeking practical guidance on truss systems and structural integrity.
Latest entries
- March 18, 2025General Wood TopicsWhat Color Is Ebony Wood? Unveiling the Rich Hues of This Luxurious Timber
- March 18, 2025Construction & FrameworkHow Can You Effectively Mount a Headboard to Your Wall?
- March 18, 2025General Wood TopicsCan Bees Really Eat Wood? Unraveling the Myths and Facts
- March 18, 2025General Wood TopicsDo Rabbits Really Chew on Wood? Exploring Their Eating Habits!