How Did Wooden Ships Manage to Stay Leak-Free Throughout History?
For centuries, wooden ships have been the vessels of choice for explorers, traders, and adventurers navigating the vast oceans. These majestic crafts, crafted from timber and designed with remarkable ingenuity, have carried countless stories across the waves. Yet, one question often arises: how did these wooden ships manage to stay afloat without succumbing to the relentless forces of water? The answer lies in a combination of skilled craftsmanship, innovative design, and the natural properties of wood itself. In this article, we will delve into the fascinating techniques and materials that kept these ships seaworthy, revealing the secrets behind their remarkable resilience against leaks and water damage.
Overview
The construction of wooden ships was an art form that combined both science and tradition. Shipbuilders utilized specific types of wood known for their durability and resistance to rot, ensuring that the vessels could withstand the harsh marine environment. Additionally, the design of the hull played a crucial role in minimizing leaks. Techniques such as caulking, which involved sealing gaps with natural fibers and tar, were employed to create a watertight barrier.
Moreover, the natural swelling of wood when exposed to water contributed to the integrity of the ship’s structure. As the wood absorbed moisture, it expanded, effectively sealing any small openings that might otherwise allow
Construction Techniques
Wooden ships were meticulously constructed using various techniques that enhanced their durability and water resistance. The choice of wood, the design of the hull, and the method of assembly were crucial factors.
- Types of Wood:
- Certain types of wood, such as oak, teak, and cedar, were favored for shipbuilding due to their natural oils and density, which provided better resistance to water.
- Joinery Methods:
- The use of mortise and tenon joints helped create tight connections between wooden planks, minimizing gaps where water could enter.
- Caulking:
- Caulking, made from materials like oakum (a fiber from old ropes), was used to seal seams. This process involved packing caulking material into the joints and then compressing it with a caulking iron.
Design Features
The design of wooden ships also played a pivotal role in preventing leaks. The hull shape, the arrangement of planks, and other features contributed to their seaworthiness.
- Hull Shape:
- A well-designed hull minimized resistance and allowed water to flow around the ship rather than into it.
- Sheathing:
- Many ships were sheathed with copper or other metals to provide an additional barrier against water and marine growth, thus reducing the risk of leaks.
- Scantlings:
- The term ‘scantlings’ refers to the dimensions and arrangement of the wooden frames and planks. Properly calculated scantlings ensured that the structure could withstand the forces exerted by water.
Maintenance Practices
Regular maintenance was essential to ensure that wooden ships remained leak-free throughout their operational lives.
- Inspection:
- Shipwrights conducted regular inspections to identify and repair worn or damaged areas.
- Re-caulking:
- Over time, caulking would degrade, so re-caulking was a routine maintenance task to maintain water tightness.
- Dry Docking:
- Ships were periodically taken into dry dock for thorough inspections and repairs. This practice allowed for the inspection of the hull below the waterline.
Maintenance Task | Frequency | Purpose |
---|---|---|
Inspection | Bi-annually | Identify leaks and wear |
Caulking | Annually | Seal seams |
Dry Docking | Every 2-3 years | Comprehensive repairs |
Through these construction techniques, design features, and diligent maintenance practices, wooden ships effectively minimized the risk of leaks, allowing them to navigate the seas safely for extended periods.
Construction Techniques of Wooden Ships
Wooden ships utilized several advanced construction techniques that contributed to their ability to minimize leaks. Key methods included:
- Caulking: This process involved sealing the seams between the planks with materials such as oakum (hemp fibers soaked in tar) or lead. Caulking created a watertight barrier that prevented water ingress.
- Laying Planks: Planks were typically laid in a manner that allowed for expansion and contraction. The overlapping seams, often in a diagonal pattern, helped to further secure the structure against leaks.
- Fastening Methods: Wooden ships used various fastening techniques, including wooden pegs, iron nails, or copper rivets. These fasteners secured the planks tightly together, reducing the gaps that could allow water to seep in.
Wood Treatments and Preservation
The longevity and water resistance of wooden ships were enhanced through specific treatments and preservation techniques:
- Tar and Pitch: These substances were applied to the hull to create an additional waterproof barrier. Tar and pitch not only protected the wood from water but also from marine organisms.
- Seasoning Wood: The wood used for shipbuilding was often seasoned, meaning it was dried and cured to minimize moisture content. This practice reduced swelling when the wood was submerged in water.
- Use of Durable Woods: Certain types of wood, such as oak, teak, and mahogany, were favored for their natural resistance to rot and water damage. Their inherent properties contributed to the overall watertightness of the ship.
Design Features
Several design elements in wooden ships played a crucial role in preventing leaks:
- Hull Shape: The streamlined shape of the hull reduced water resistance and facilitated easier passage through water, minimizing the chances of leaks due to pressure.
- Decking and Overlaps: The deck was constructed with a slight camber, allowing water to run off rather than pool. Additionally, overlapping deck planks helped to seal the structure against leaks.
- Double Hulls: Some ships utilized a double hull design, where an inner and outer layer of planking created an additional barrier against water ingress.
Maintenance Practices
Regular maintenance was essential in ensuring the integrity of wooden ships:
- Routine Inspections: Crew members conducted regular checks for signs of wear, damage, or leaks, allowing for prompt repairs.
- Re-caulking: As ships aged, caulking would wear away or degrade. Regular re-caulking was necessary to maintain a watertight seal.
- Bottom Cleaning: The hull was routinely cleaned to remove barnacles and other marine growth that could compromise the integrity of the ship and lead to leaks.
Maintenance Practice | Description |
---|---|
Routine Inspections | Regular checks for damage or leaks. |
Re-caulking | Replacement of worn-out caulking materials. |
Bottom Cleaning | Removal of marine growth to protect the hull. |
Environmental Adaptations
Wooden ships were often adapted to their operating environments, which aided in preventing leaks:
- Local Materials: Builders often used locally available woods that were more resistant to local water conditions, ensuring better performance.
- Climate Considerations: The design and construction were adjusted according to the climate, with additional treatments applied in humid or saline environments to enhance water resistance.
- Regional Techniques: Different cultures developed unique shipbuilding techniques that were particularly effective in their respective waters, leading to innovations that improved leak prevention.
Understanding the Craftsmanship Behind Wooden Ship Sealing
Dr. Emily Carter (Marine Archaeologist, Nautical History Journal). “The construction of wooden ships involved meticulous techniques such as caulking, where fibers from natural materials like oakum were used to fill gaps between planks. This process, combined with the natural swelling of wood when wet, created a watertight seal essential for seaworthiness.”
Captain James Thornton (Naval Historian and Author). “Skilled shipwrights employed a combination of overlapping planks and strategic fastening methods to minimize leaks. The careful selection of wood types and the application of pitch or tar further enhanced the ship’s ability to resist water intrusion.”
Dr. Sarah Lin (Materials Scientist, Journal of Marine Engineering). “The use of specific tree species, such as oak and cedar, was crucial in shipbuilding. These woods not only provided strength but also had natural oils that helped repel water, contributing to the overall integrity of the vessel against leaks.”
Frequently Asked Questions (FAQs)
How did wooden ships prevent leaks?
Wooden ships utilized a combination of tight-fitting joints, caulking materials, and the natural swelling of wood when wet to create a watertight seal. The planks were often joined using techniques like lapstrake or carvel construction, which minimized gaps.
What materials were used for caulking wooden ships?
Traditional caulking materials included oakum, made from hemp or jute fibers, which was soaked in tar or pitch to enhance water resistance. This was packed into the seams between planks to prevent water ingress.
How did shipbuilders ensure the wood was durable?
Shipbuilders selected specific types of wood, such as oak or teak, known for their density and resistance to rot. They also treated the wood with preservatives and used techniques like steaming to bend it, enhancing its durability.
Did wooden ships require regular maintenance to prevent leaks?
Yes, regular maintenance was essential. Ship crews routinely inspected and repaired caulking, replaced damaged planks, and applied protective coatings to maintain the integrity of the hull and prevent leaks.
What role did the design of the hull play in preventing leaks?
The design of the hull, including its shape and the arrangement of planks, contributed significantly to water resistance. A well-designed hull minimized water pressure against the seams and allowed for better water flow, reducing the risk of leaks.
How did the construction techniques evolve to improve leak prevention?
Construction techniques evolved through innovations such as the of iron fastenings, improved caulking methods, and the use of more advanced joinery techniques. These advancements enhanced the structural integrity and watertightness of wooden ships.
Wooden ships historically managed to minimize leaks through a combination of skilled craftsmanship, innovative design, and the natural properties of wood. Shipbuilders employed various techniques such as caulking, which involved filling the seams between planks with materials like oakum and pitch, to create a watertight seal. This meticulous attention to detail ensured that even the smallest gaps were addressed, significantly reducing the risk of water ingress.
Additionally, the use of specific types of wood, such as oak and teak, contributed to the durability and water resistance of these vessels. The natural oils and density of these woods helped repel water, further enhancing the ship’s ability to remain buoyant and leak-free. Furthermore, the design of wooden ships often included a double hull or additional reinforcements in key areas, providing an extra layer of protection against leaks.
In summary, the successful construction of wooden ships that did not leak was a result of advanced shipbuilding techniques, the selection of appropriate materials, and thoughtful design considerations. These elements combined allowed wooden ships to navigate vast oceans with minimal water intrusion, showcasing the ingenuity of maritime engineering in historical contexts.
Author Profile
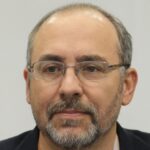
-
Darryl Norman is a seasoned entrepreneur and industry expert with a deep understanding of wood truss manufacturing and construction materials. As the President of Timberlake TrussWorks, LLC, Darryl played a pivotal role in shaping the company’s reputation for quality and precision. His leadership ensured that each truss met rigorous structural standards, providing builders with dependable components essential to their projects.
Beginning in 2025, Darryl Norman has shifted his focus to education and knowledge-sharing through an informative blog dedicated to wood truss manufacturing. Drawing from his extensive experience in the field, he provides in-depth insights into truss design, material selection, and construction techniques. This blog serves as a valuable resource for builders, contractors, and homeowners seeking practical guidance on truss systems and structural integrity.
Latest entries
- March 18, 2025General Wood TopicsWhat Color Is Ebony Wood? Unveiling the Rich Hues of This Luxurious Timber
- March 18, 2025Construction & FrameworkHow Can You Effectively Mount a Headboard to Your Wall?
- March 18, 2025General Wood TopicsCan Bees Really Eat Wood? Unraveling the Myths and Facts
- March 18, 2025General Wood TopicsDo Rabbits Really Chew on Wood? Exploring Their Eating Habits!