How Do I Engrave Wood? A Step-by-Step Guide to Mastering the Art!
Engraving wood is a timeless craft that combines artistry and precision, allowing creators to transform simple wooden surfaces into stunning works of art. Whether you’re looking to personalize a gift, create a unique piece of home decor, or simply explore a new hobby, wood engraving offers endless possibilities for expression. With the right techniques and tools, you can carve intricate designs, meaningful messages, or even elaborate patterns that breathe life into the natural beauty of wood. This article will guide you through the essential steps and considerations to embark on your engraving journey, ensuring your projects are both rewarding and successful.
To begin with, understanding the basics of wood engraving is crucial. This craft can be approached in various ways, from traditional hand tools to modern laser engraving machines, each offering distinct advantages and challenges. The choice of wood also plays a significant role in the outcome of your project, as different types of wood exhibit varying textures and grain patterns that can enhance or detract from your design.
Furthermore, mastering the techniques of engraving involves more than just the physical act of carving. It requires an appreciation for design principles, tool selection, and safety measures to ensure a smooth and enjoyable experience. As you delve deeper into the world of wood engraving, you’ll discover the joy of creating personalized items that not only showcase
Choosing the Right Tools
Selecting the appropriate tools is crucial for effective wood engraving. The choice primarily depends on the complexity of the design and the type of wood being used. Here are some common tools:
- Rotary Tools: Versatile and ideal for intricate designs. They come with various bits for different engraving styles.
- Laser Engravers: Offer precision and the ability to handle detailed images. Best for larger projects or commercial use.
- Hand Tools: Such as chisels and gouges, suitable for traditional engraving methods.
When choosing a tool, consider the following factors:
Tool Type | Pros | Cons |
---|---|---|
Rotary Tools | Versatile, affordable | Can be challenging for fine details |
Laser Engravers | High precision, complex designs | Expensive, requires power source |
Hand Tools | Traditional feel, tactile control | Time-consuming, requires skill |
Preparing the Wood Surface
Before engraving, it’s essential to prepare the wood surface properly to ensure the best results. Follow these steps:
- Select the Right Wood: Choose wood that is smooth and free from knots. Popular choices include pine, maple, and cherry.
- Sand the Surface: Use fine-grit sandpaper to create a smooth finish. This helps the engraving tool glide easily and prevents splintering.
- Clean the Surface: Wipe the wood with a damp cloth to remove dust and debris. Allow it to dry completely before starting.
Engraving Techniques
There are several engraving techniques you can use, depending on your desired effect and tools:
- V-Carving: This technique uses a V-shaped bit to create clean, sharp lines. Ideal for lettering and intricate designs.
- Deep Relief Carving: Involves removing a significant amount of material to create depth. This technique is more labor-intensive but results in a striking effect.
- Surface Etching: Utilizes a laser or rotary tool to create shallow designs that add texture without removing much wood.
Finishing Touches
After engraving, applying a finish can enhance the appearance and longevity of the wood piece. Consider the following options:
- Stains: To enhance the color and grain of the wood while providing contrast to the engraving.
- Sealants: Protect the engraving from moisture and wear, especially if the piece will be used outdoors.
- Polish: For a glossy finish, apply a wood polish or wax after the stain and sealant have dried.
By following these guidelines, you can achieve professional-quality wood engravings suitable for various projects.
Choosing the Right Tools for Wood Engraving
Selecting the appropriate tools is crucial for achieving precise and aesthetically pleasing engravings. The main options include:
- Hand Tools:
- Chisels: Ideal for detailed work; available in various shapes and sizes.
- Knives: Useful for fine lines and intricate designs.
- Gouges: Perfect for creating textures or deeper cuts.
- Power Tools:
- Dremel or Rotary Tools: Versatile and effective for both detailed and large-scale projects.
- Laser Engravers: Provide high precision and can handle complex designs efficiently.
- CNC Machines: Best for automated, consistent engravings on larger projects.
Preparing the Wood Surface
Proper preparation of the wood surface is essential for achieving optimal results. Follow these steps:
- Choose the Right Type of Wood:
- Softwoods (like pine) are easier to engrave but may not hold fine details as well as hardwoods (like oak or maple).
- Sanding:
- Sand the wood surface with fine-grit sandpaper (220 grit or higher) to ensure it is smooth and free of splinters.
- Wipe the surface with a damp cloth to remove dust particles.
- Sealing (Optional):
- Apply a wood sealer or finish to create a uniform surface, especially if using a laser engraver, as it can enhance contrast.
Engraving Techniques
Different engraving techniques can yield varied effects. Consider the following methods:
- V-Carving:
- Uses a V-shaped bit to create sharp, defined edges and depth. Ideal for lettering and intricate designs.
- Relief Carving:
- Involves carving away parts of the wood to create a raised design. This method adds dimension to the artwork.
- Burning:
- Utilizes a wood burner to create designs through heat. It produces a darker contrast and can achieve detailed textures.
Safety Precautions
When engraving wood, safety should be a priority. Follow these guidelines:
- Wear Protective Gear:
- Safety glasses to protect eyes from debris.
- Dust mask to prevent inhalation of fine particles.
- Gloves to protect hands from cuts and burns.
- Work in a Ventilated Area:
- Ensure proper airflow, especially when using power tools or burning techniques, to minimize exposure to fumes.
Finishing Your Engraving
Once the engraving is complete, finishing touches can enhance the final product:
- Cleaning:
- Remove any dust or debris from the engraving using a soft brush or cloth.
- Staining or Painting:
- Apply wood stain or paint to highlight the engraving. Test on a scrap piece first to ensure desired results.
- Sealing:
- Use a clear wood finish (such as polyurethane) to protect the engraving and enhance its longevity.
Common Mistakes to Avoid
To ensure successful wood engraving, be aware of these common pitfalls:
- Inadequate Surface Preparation:
- Skipping sanding can lead to uneven engraving and splintering.
- Using the Wrong Tool for the Job:
- Each tool has its specific application; using the incorrect one can result in poor quality.
- Neglecting Safety Protocols:
- Overlooking safety can lead to accidents or injuries during the engraving process.
By focusing on these aspects, you can improve your engraving skills and achieve professional-quality results.
Expert Insights on Wood Engraving Techniques
Emily Carter (Master Woodworker, Artisan’s Guild). “When engraving wood, it is crucial to select the right type of wood. Softwoods like pine are easier to engrave but may not hold intricate details as well as hardwoods like maple or cherry. Always test your design on a scrap piece to ensure the best results.”
David Lin (Laser Engraving Specialist, Precision Engraving Co.). “Using a laser engraver can significantly enhance the precision of your designs. Make sure to adjust the power and speed settings according to the wood type to prevent burning or charring, which can ruin the final product.”
Sarah Thompson (DIY Craft Instructor, Creative Workshop). “For hand engraving, tools like chisels and rotary engravers are essential. Practice your technique on less expensive materials before moving to your final piece to build confidence and skill in controlling the depth and angle of your cuts.”
Frequently Asked Questions (FAQs)
How do I choose the right tool for engraving wood?
Select tools based on the desired depth and detail of the engraving. Common options include rotary tools, laser engravers, and wood-burning pens. Each tool offers different capabilities, so consider your project requirements.
What type of wood is best for engraving?
Softwoods like pine and cedar are easier to engrave and yield cleaner results. Hardwoods such as oak and maple can also be engraved but may require more advanced tools and techniques.
Can I engrave painted or stained wood?
Yes, you can engrave painted or stained wood. However, ensure the paint or stain is fully cured to prevent smudging. The engraving will reveal the wood beneath the finish, creating a contrasting effect.
What safety precautions should I take when engraving wood?
Always wear safety goggles and a dust mask to protect against debris and dust. Ensure your workspace is well-ventilated, and follow the manufacturer’s safety instructions for your engraving tools.
How do I prepare wood for engraving?
Start by sanding the wood surface to a smooth finish. Clean off any dust or debris, and consider applying a wood conditioner to enhance the engraving quality. Ensure the wood is dry and free of knots for best results.
Can I engrave designs or text on wood?
Yes, you can engrave both designs and text on wood. Use templates or stencils for precise lettering, or create custom designs using software for laser engraving. Ensure the design is suitable for the wood type and tool used.
Engraving wood is a rewarding craft that allows individuals to create personalized items, gifts, or artistic pieces. The process can be approached using various techniques, including hand engraving, rotary tools, laser engraving, and wood burning. Each method has its own set of tools, materials, and skill requirements, making it essential for beginners to choose the approach that best fits their comfort level and project goals.
Preparation is crucial for successful wood engraving. Selecting the right type of wood is vital, as different woods respond uniquely to engraving techniques. Softwoods like pine are easier to engrave but may not hold intricate details as well as hardwoods like oak or cherry. Additionally, ensuring that the wood surface is clean and smooth will significantly enhance the quality of the engraving.
Safety precautions should not be overlooked during the engraving process. Proper protective gear, such as goggles and masks, is essential to prevent injury from dust and debris. Furthermore, understanding the specific safety measures associated with each engraving tool will help mitigate risks and ensure a safe working environment.
engraving wood is an accessible yet intricate craft that can yield beautiful and personalized results. By selecting the appropriate technique, preparing the wood properly, and adhering to safety guidelines, anyone can
Author Profile
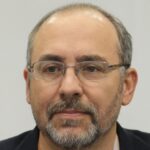
-
Darryl Norman is a seasoned entrepreneur and industry expert with a deep understanding of wood truss manufacturing and construction materials. As the President of Timberlake TrussWorks, LLC, Darryl played a pivotal role in shaping the company’s reputation for quality and precision. His leadership ensured that each truss met rigorous structural standards, providing builders with dependable components essential to their projects.
Beginning in 2025, Darryl Norman has shifted his focus to education and knowledge-sharing through an informative blog dedicated to wood truss manufacturing. Drawing from his extensive experience in the field, he provides in-depth insights into truss design, material selection, and construction techniques. This blog serves as a valuable resource for builders, contractors, and homeowners seeking practical guidance on truss systems and structural integrity.
Latest entries
- March 18, 2025General Wood TopicsWhat Color Is Ebony Wood? Unveiling the Rich Hues of This Luxurious Timber
- March 18, 2025Construction & FrameworkHow Can You Effectively Mount a Headboard to Your Wall?
- March 18, 2025General Wood TopicsCan Bees Really Eat Wood? Unraveling the Myths and Facts
- March 18, 2025General Wood TopicsDo Rabbits Really Chew on Wood? Exploring Their Eating Habits!