How Do I Make Wood Pellets? A Step-by-Step Guide for Beginners
In recent years, the demand for sustainable and renewable energy sources has surged, leading many to explore the world of wood pellets. These compact, cylindrical pieces of biomass not only serve as an eco-friendly alternative to traditional fossil fuels but also provide an efficient way to heat homes and power various appliances. If you’ve ever wondered, “How do I make wood pellets?” you’re not alone. This article will guide you through the fascinating process of transforming raw wood materials into high-quality pellets, empowering you to tap into this green energy solution.
Creating wood pellets is an intricate yet rewarding process that begins with selecting the right raw materials. Typically made from sawdust, wood shavings, or other wood byproducts, the journey to pellet production involves several key steps. From drying and grinding the wood to the critical phase of pelletizing, each stage plays a vital role in ensuring the final product is both durable and efficient.
Moreover, understanding the importance of moisture content, binding agents, and the right machinery can significantly influence the quality of the pellets produced. As we delve deeper into the specifics, you’ll learn not only the technical aspects of wood pellet production but also the benefits of incorporating this sustainable practice into your energy routine. Get ready to uncover the secrets behind making your own wood pellets and
Raw Material Selection
The first step in making wood pellets is selecting the appropriate raw materials. The primary ingredient is wood, which can come from various sources, including sawmill residues, wood chips, or even recycled wood products. The quality of the wood directly influences the quality of the pellets produced.
Factors to consider when selecting raw materials include:
- Wood Type: Hardwoods like oak and maple produce denser and higher-quality pellets compared to softwoods such as pine and spruce.
- Moisture Content: Ideal moisture content for pellet production is between 10% and 15%. Higher moisture levels can lead to poor pellet formation and increased energy consumption during drying.
- Contaminants: Ensure the raw materials are free from contaminants such as dirt, metal, or plastic, as these can affect the pellet quality and the operation of the pellet mill.
Grinding the Raw Materials
After selecting the raw materials, the next step is grinding them into smaller pieces. This process increases the surface area of the wood, making it easier to compress into pellets.
- Equipment Used: A hammer mill is commonly used for this purpose. It breaks down the wood into smaller particles, typically less than 1/4 inch in size.
- Particle Size: Consistent particle size is crucial for uniform pellet production. Larger particles can cause inconsistencies in the final product and may lead to issues in the pelletizing process.
Drying Process
Drying the ground wood is essential to achieve the optimal moisture content. If the moisture content is too high, the pellets will not hold together properly, leading to a weaker product.
Methods of drying include:
- Air Drying: Leaving the ground wood in a controlled environment to allow moisture to evaporate naturally.
- Kiln Drying: Using a kiln to efficiently remove moisture from the wood. This method is faster and can achieve desired moisture levels more reliably.
Pelletizing
Once the wood is properly prepared, it is time to pelletize. This process compresses the ground wood into small, cylindrical shapes using a pellet mill.
- Pellet Mill Operation: The ground wood is fed into the pellet mill, where it is subjected to high pressure and heat. This causes the lignin in the wood to soften, binding the particles together.
- Die and Rollers: The pellet mill consists of a die and rollers that shape the wood into pellets. The size of the die holes can be adjusted to produce pellets of different diameters.
Cooling and Packaging
After pelletizing, the hot pellets need to be cooled to harden and reduce moisture content. This is typically achieved using a cooler.
- Cooling Methods:
- Air Cooling: Uses ambient air to cool the pellets gradually.
- Water Cooling: Involves spraying water on the pellets, although this can add moisture, requiring subsequent drying.
Once cooled, the pellets can be packaged for storage or distribution. Proper packaging is crucial to maintain pellet quality and prevent moisture absorption.
Step | Description | Considerations |
---|---|---|
Raw Material Selection | Choosing wood with the right properties | Type, moisture content, contaminants |
Grinding | Reducing wood to small particles | Uniform particle size |
Drying | Reducing moisture content | Method and efficiency |
Pelletizing | Compressing wood into pellets | Die size, pressure |
Cooling | Hardening the pellets | Cooling method |
Materials Needed for Wood Pellet Production
To create wood pellets, specific materials and tools are essential for efficient processing. The primary ingredient is biomass, typically wood, but other organic materials can also be utilized.
Primary Materials:
- Wood: Use sawdust, wood shavings, or wood chips. Hardwoods like oak and maple yield higher-quality pellets.
- Binder: While not always necessary, a natural binder such as lignin can enhance pellet integrity.
Equipment Required:
- Wood Chipper: For breaking down larger wood pieces into smaller chips.
- Hammer Mill: To grind wood chips or shavings into fine sawdust.
- Pellet Mill: The core machine that compresses the sawdust into pellets.
- Cooling System: To cool down the pellets post-production.
- Storage Containers: For storing the finished pellets.
Preparation of Raw Materials
The preparation stage is crucial for ensuring high-quality pellets. Properly processed raw materials lead to better pellet formation and combustion efficiency.
Steps for Preparation:
- Size Reduction: Use a wood chipper to reduce larger wood pieces to manageable sizes. Follow this with a hammer mill to produce fine sawdust.
- Moisture Content Adjustment: Optimal moisture content should be between 10% and 15%. If the sawdust is too dry, add water; if too wet, allow it to air dry.
- Sifting: Screen the sawdust to remove any oversized particles or contaminants.
Pelletization Process
The pelletization process involves compressing the prepared sawdust into cylindrical pellets.
Key Steps:
- Feeding: Introduce the prepared sawdust into the pellet mill.
- Compression: The mill uses high pressure and heat to compress the sawdust, causing lignin to soften and act as a natural binder.
- Forming Pellets: The mixture is forced through a die, creating pellets of uniform size.
- Cutting: Pellets are cut to a desired length as they exit the mill.
Cooling and Storage of Pellets
After pelletization, cooling and proper storage are vital to maintain pellet quality and prevent spoilage.
Cooling Process:
- Cooling System: Use a cooling conveyor or air cooling system to lower the temperature of the pellets. This step reduces moisture and prevents breakage.
Storage Guidelines:
- Dry Environment: Store pellets in a dry, well-ventilated area to prevent moisture absorption.
- Containers: Use airtight containers or bags to protect from pests and humidity.
- Temperature Control: Maintain a stable temperature to prolong shelf life.
Testing and Quality Control
Quality control ensures that the pellets produced meet the necessary standards for combustion efficiency and emission levels.
Testing Parameters:
- Moisture Content: Regularly check moisture levels using a moisture meter.
- Durability: Perform a durability test by dropping pellets to assess their strength.
- Calorific Value: Measure the energy content using a calorimeter to ensure optimal combustion performance.
Utilizing these processes and guidelines will facilitate the efficient production of high-quality wood pellets suitable for various applications, including heating and energy generation.
Expert Insights on How to Make Wood Pellets
Dr. Emily Carter (Renewable Energy Specialist, GreenTech Innovations). “To successfully make wood pellets, it is essential to start with high-quality raw materials, such as sawdust or wood shavings, which should be free from contaminants. The moisture content of the wood should be around 10-15% for optimal pellet formation and combustion efficiency.”
Mark Thompson (Wood Pellet Manufacturing Consultant, EcoPellet Solutions). “The process of making wood pellets involves drying, grinding, and compressing the biomass. Utilizing a pellet mill is crucial, as it applies the necessary pressure and heat to form dense pellets. Ensuring the right die specifications can significantly enhance pellet quality.”
Linda Martinez (Sustainable Forestry Expert, ForestWise Institute). “Sourcing sustainable wood materials is key to producing environmentally friendly wood pellets. It is important to adhere to sustainable forestry practices to ensure that the production of pellets does not contribute to deforestation or habitat loss.”
Frequently Asked Questions (FAQs)
How do I make wood pellets at home?
To make wood pellets at home, you need to start with raw materials such as sawdust or wood shavings. Dry the material to a moisture content of around 10-15%, then use a pellet mill to compress the material into small cylindrical pellets. Finally, allow the pellets to cool and store them in a dry place.
What equipment is required for making wood pellets?
The primary equipment needed includes a wood pellet mill, a hammer mill for grinding the raw material, a dryer for reducing moisture content, and a cooling system for the finished pellets. Additional tools may include a sieve for sorting and a storage container.
What types of wood are best for making pellets?
Hardwoods such as oak, maple, and hickory are ideal for making pellets due to their density and high energy content. Softwoods like pine and fir can also be used, but they may produce more ash and have a lower energy density.
How do I ensure the quality of my wood pellets?
To ensure high-quality wood pellets, control the moisture content of the raw materials, maintain consistent pellet size, and monitor the compression process. Conduct regular testing for durability, ash content, and energy output to meet industry standards.
Can I add additives to my wood pellets?
Yes, additives such as binders or lubricants can be used to improve pellet durability and reduce wear on the equipment. However, it is essential to ensure that any additives used are safe and do not compromise the burning efficiency of the pellets.
How should I store wood pellets after making them?
Store wood pellets in a cool, dry place away from moisture to prevent spoilage. Use airtight containers or bags to protect them from humidity and pests. Proper storage will help maintain the pellets’ quality and energy efficiency.
the process of making wood pellets involves several critical steps that ensure the production of high-quality fuel. Initially, the selection of appropriate raw materials, such as sawdust or wood shavings, is essential. These materials must be dry and free from contaminants to achieve optimal pelletization. The next step involves grinding the raw materials to a fine consistency, which facilitates the pelletizing process.
Following the grinding, the material is subjected to a pellet mill, where it is compressed under high pressure and temperature. This process not only shapes the wood into pellets but also activates the natural lignin within the wood, which acts as a binding agent. After pelletizing, the pellets should be cooled and dried to achieve the desired moisture content, ensuring they are suitable for storage and use.
Key takeaways from the discussion on making wood pellets include the importance of material selection, the necessity of proper grinding, and the role of the pellet mill in shaping and binding the pellets. Additionally, understanding the significance of cooling and drying processes cannot be understated, as they directly impact the durability and efficiency of the final product. Overall, mastering these steps can lead to successful wood pellet production, providing an efficient and renewable energy source.
Author Profile
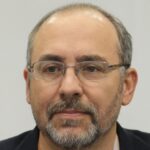
-
Darryl Norman is a seasoned entrepreneur and industry expert with a deep understanding of wood truss manufacturing and construction materials. As the President of Timberlake TrussWorks, LLC, Darryl played a pivotal role in shaping the company’s reputation for quality and precision. His leadership ensured that each truss met rigorous structural standards, providing builders with dependable components essential to their projects.
Beginning in 2025, Darryl Norman has shifted his focus to education and knowledge-sharing through an informative blog dedicated to wood truss manufacturing. Drawing from his extensive experience in the field, he provides in-depth insights into truss design, material selection, and construction techniques. This blog serves as a valuable resource for builders, contractors, and homeowners seeking practical guidance on truss systems and structural integrity.
Latest entries
- March 18, 2025General Wood TopicsWhat Color Is Ebony Wood? Unveiling the Rich Hues of This Luxurious Timber
- March 18, 2025Construction & FrameworkHow Can You Effectively Mount a Headboard to Your Wall?
- March 18, 2025General Wood TopicsCan Bees Really Eat Wood? Unraveling the Myths and Facts
- March 18, 2025General Wood TopicsDo Rabbits Really Chew on Wood? Exploring Their Eating Habits!