How Are Wood Pellets Made? Unveiling the Process Behind This Eco-Friendly Fuel
In an age where sustainable energy solutions are increasingly sought after, wood pellets have emerged as a popular choice for heating and energy production. These small, cylindrical pieces of compressed wood are not only efficient but also environmentally friendly, making them a staple in homes and industries alike. But have you ever wondered how these tiny powerhouses are made? Understanding the process behind wood pellet production not only highlights the ingenuity of modern manufacturing but also underscores the importance of renewable resources in our quest for a greener future. Join us as we delve into the fascinating journey of wood pellets, from raw materials to the final product.
The production of wood pellets begins with the careful selection of raw materials, primarily wood waste such as sawdust, wood shavings, and other biomass residues. This choice of feedstock is crucial, as it not only influences the quality of the pellets but also ensures that the process is sustainable and minimizes waste. Once the materials are gathered, they undergo a series of processes designed to prepare them for pelletization, including drying, grinding, and conditioning. Each step plays a vital role in transforming these raw materials into the high-energy fuel that wood pellets are known for.
After the preparation phase, the actual pelletization process takes center stage. This involves compressing the treated biomass under
Raw Material Selection
The process of making wood pellets begins with the careful selection of raw materials. Typically, the primary source is sawmill residuals, such as wood shavings, sawdust, and wood chips. These materials are preferred due to their consistency and low moisture content. Other sources can include:
- Agricultural residues (e.g., corn stover, straw)
- Recycled wood products
- Dedicated energy crops (e.g., switchgrass)
The choice of raw material can influence the quality and burning characteristics of the final pellet product.
Drying Process
Before the wood material can be processed into pellets, it must be dried to a specific moisture content, usually around 10-15%. Excess moisture can lead to poor pellet quality and efficiency during combustion. The drying process typically involves:
- Mechanical Dryers: These use heat and air to reduce moisture content.
- Air Drying: A more natural method, where wood is allowed to dry in the open air, although this method is slower.
Grinding
Once dried, the wood material is ground into finer particles. The goal is to achieve a uniform size to ensure consistent pellet production. The grinding process typically involves:
- Hammer mills or grinders, which reduce the material to a specific particle size (usually less than 6mm).
- Screening to remove oversized particles.
This step is crucial as the uniformity of the feedstock directly affects the efficiency of the pelletizing process.
Pelletizing Process
The core of wood pellet production is the pelletizing process, where the ground material is compressed into dense pellets. This involves several key steps:
- Conditioning: The ground material is mixed with steam or water to increase its temperature and soften the lignin, which acts as a natural binder.
- Pellet Mill: The conditioned material is fed into a pellet mill, where it is forced through a die. The pressure and heat cause the lignin to melt and bind the particles together, forming pellets.
- Cooling: After being extruded, the pellets are hot and need to be cooled. This is often achieved using a cooling conveyor that allows air to circulate around the pellets.
Quality Control
Ensuring the quality of wood pellets is critical for both performance and customer satisfaction. Several measures are taken during the production process to maintain high standards:
- Moisture Content: Regular checks to ensure pellets remain within the desired moisture range.
- Durability Tests: Pellets are subjected to mechanical tests to assess their strength and durability.
- Chemical Analysis: Testing for contaminants and ensuring compliance with industry standards.
Quality Parameter | Standard Range |
---|---|
Moisture Content | 10-15% |
Durability | 97% or higher |
Ash Content | 1-5% |
By adhering to these quality control measures, manufacturers can produce high-quality wood pellets that meet the needs of consumers and regulatory standards.
Raw Material Selection
The production of wood pellets begins with the selection of raw materials, which primarily consist of wood residues. These materials can come from various sources, including:
- Sawmill Residues: Sawdust, wood shavings, and wood chips generated during the lumber production process.
- Forest Residues: Leftover branches, tops, and other wood debris from logging operations.
- Recycled Wood: Clean, untreated wood from construction and demolition sites, or other wood waste products.
The quality and type of raw materials significantly influence the final properties of the wood pellets, such as their calorific value and ash content.
Grinding Process
Once the raw materials are sourced, they undergo a grinding process to achieve a uniform particle size. This step is crucial for ensuring consistent pellet quality. The grinding process involves:
- Hammer Mills: These machines crush the raw materials into smaller particles, typically ranging from 1 to 5 mm in diameter.
- Screening: After grinding, the material is screened to remove oversized particles and ensure uniformity.
Drying Stage
Wood fibers contain moisture, which must be reduced to an optimal level (generally between 10% and 15%) before pelletization. The drying stage can be achieved through several methods:
- Natural Drying: Utilizing sunlight and air to reduce moisture content, although this method is weather-dependent.
- Kiln Drying: Employing heated air circulation in a kiln to control moisture levels more efficiently.
- Direct Fired Dryers: Using combustion gases to heat and dry the wood material quickly.
Pulping and Conditioning
After drying, the wood particles undergo conditioning, where they are mixed with steam. This process enhances the pliability of the wood fibers, making them easier to compress. Key elements include:
- Temperature Control: The conditioning process usually requires maintaining specific temperatures to maximize fiber softness.
- Additives: Some manufacturers may incorporate natural binders, such as lignin, to enhance pellet durability.
Pelletizing Process
The conditioned wood material is then fed into a pellet mill, where it is compressed through a die to form pellets. The pelletizing process involves:
- Die and Roller Configuration: The die contains holes that shape the pellets, while rollers apply pressure to compress the material.
- Heat Generation: Friction from the compression process generates heat, which softens the lignin in the wood, helping to bind the pellets together.
Cooling and Packaging
Once the pellets are formed, they are hot and need to be cooled before packaging. This stage includes:
- Cooling Systems: Using air or water to reduce pellet temperature and stabilize their structure.
- Screening for Quality Control: Pellets are screened to remove fines and ensure uniform size before packaging.
- Bagging or Bulk Loading: Depending on market requirements, pellets are either bagged for retail or loaded in bulk for shipment.
Quality Control Measures
Throughout the production process, quality control measures are essential to ensure that the wood pellets meet industry standards. Key factors monitored include:
- Moisture Content: Critical for combustion efficiency and storage stability.
- Durability Testing: Ensuring that pellets can withstand handling and transportation without significant breakage.
- Calorific Value: Testing for energy output to comply with energy market requirements.
By meticulously following these steps, manufacturers can produce high-quality wood pellets suitable for various applications, including residential heating and industrial energy generation.
Understanding the Wood Pellet Manufacturing Process
Dr. Emily Carter (Biomass Energy Researcher, Green Energy Institute). “The production of wood pellets begins with the selection of raw materials, primarily wood waste such as sawdust and wood shavings. These materials are then dried to reduce moisture content, which is crucial for ensuring the efficiency of the pelletizing process.”
Mark Thompson (Senior Engineer, EcoPellet Technologies). “Once the wood is dried, it is ground into a fine powder. This powder is then subjected to high pressure and heat in a pellet mill, which causes the lignin in the wood to melt and bind the particles together, forming dense pellets.”
Lisa Chen (Sustainability Consultant, Renewable Resources Group). “After pelletizing, the pellets are cooled and screened to ensure uniform size. This final step is essential for quality control, as it affects the burning efficiency and storage of the pellets.”
Frequently Asked Questions (FAQs)
How are wood pellets produced?
Wood pellets are produced through a process that includes grinding wood into sawdust, drying the sawdust to reduce moisture content, and then compressing it under high pressure using a pellet mill. This process forms the sawdust into small cylindrical pellets.
What types of wood are used to make pellets?
Wood pellets can be made from various types of wood, including hardwoods like oak and maple, and softwoods like pine and spruce. The choice of wood affects the pellet’s density, heat output, and ash content.
What is the moisture content of wood pellets?
The ideal moisture content for wood pellets is typically between 4% and 8%. This range ensures optimal combustion efficiency and minimizes the production of smoke and creosote during burning.
Are additives used in the production of wood pellets?
Generally, no additives are required in the production of high-quality wood pellets. The natural lignin present in the wood acts as a binding agent, allowing the pellets to hold their shape without additional chemicals.
How are wood pellets packaged for sale?
Wood pellets are usually packaged in 40-pound bags or bulk containers. They are stored in dry conditions to prevent moisture absorption, which can lead to degradation in quality and performance.
What are the benefits of using wood pellets for heating?
Wood pellets offer several benefits for heating, including high energy efficiency, lower emissions compared to fossil fuels, and the use of renewable resources. They also provide a convenient and consistent fuel source for pellet stoves and boilers.
In summary, the process of making wood pellets involves several key steps that transform raw wood materials into a compact and efficient fuel source. Initially, wood is sourced from various types of biomass, including sawdust, wood shavings, and wood chips. This material undergoes size reduction through grinding, which is essential for achieving the appropriate particle size for pellet production. Following this, the wood is dried to reduce moisture content, as optimal moisture levels are crucial for ensuring proper pellet formation and combustion efficiency.
After drying, the wood particles are subjected to a process called pelleting, where they are compressed under high pressure and heat. This step not only shapes the wood into pellets but also causes the lignin within the wood to melt, acting as a natural binder that holds the pellets together. Once formed, the pellets are cooled and screened to remove any fines, ensuring a uniform product that is ready for packaging and distribution.
Key takeaways from the wood pellet production process include the importance of raw material selection, moisture control, and the role of heat and pressure in pellet formation. Understanding these factors is essential for manufacturers aiming to produce high-quality wood pellets that meet industry standards. Additionally, the environmental benefits of using wood pellets as a renewable energy source highlight
Author Profile
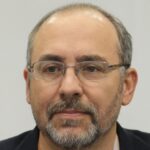
-
Darryl Norman is a seasoned entrepreneur and industry expert with a deep understanding of wood truss manufacturing and construction materials. As the President of Timberlake TrussWorks, LLC, Darryl played a pivotal role in shaping the company’s reputation for quality and precision. His leadership ensured that each truss met rigorous structural standards, providing builders with dependable components essential to their projects.
Beginning in 2025, Darryl Norman has shifted his focus to education and knowledge-sharing through an informative blog dedicated to wood truss manufacturing. Drawing from his extensive experience in the field, he provides in-depth insights into truss design, material selection, and construction techniques. This blog serves as a valuable resource for builders, contractors, and homeowners seeking practical guidance on truss systems and structural integrity.
Latest entries
- March 18, 2025General Wood TopicsWhat Color Is Ebony Wood? Unveiling the Rich Hues of This Luxurious Timber
- March 18, 2025Construction & FrameworkHow Can You Effectively Mount a Headboard to Your Wall?
- March 18, 2025General Wood TopicsCan Bees Really Eat Wood? Unraveling the Myths and Facts
- March 18, 2025General Wood TopicsDo Rabbits Really Chew on Wood? Exploring Their Eating Habits!