How Do You Engrave on Wood? A Step-by-Step Guide for Beginners
Engraving on wood is a captivating art form that marries creativity with craftsmanship, allowing individuals to transform simple wooden surfaces into personalized masterpieces. Whether you’re looking to add a unique touch to a gift, create custom signage, or explore a new hobby, the process of engraving offers endless possibilities. With the right tools and techniques, you can bring your visions to life, making each piece a reflection of your personality and style. In this article, we will delve into the essentials of wood engraving, guiding you through the methods, tools, and tips that will help you master this timeless craft.
At its core, engraving on wood involves etching or carving designs into the surface of the material, creating depth and texture that can be both visually striking and tactile. There are various techniques to achieve this, ranging from traditional hand-carving methods to modern laser engraving, each offering unique advantages and challenges. Understanding the different approaches will empower you to choose the one that best aligns with your project goals and skill level.
In addition to the techniques, selecting the right type of wood is crucial for achieving the desired results. Different woods possess varying grain patterns, hardness, and colors, all of which can influence the final appearance of your engraving. As you embark on your engraving journey, this article will provide insights
Choosing the Right Tools
Selecting the appropriate tools is crucial for successful wood engraving. The tools you choose will depend on the complexity of your design and the type of wood you are working with. Here are some common tools used for wood engraving:
- Hand Tools: These include chisels, knives, and gouges. They allow for precise control but require a steady hand and skill.
- Rotary Tools: Dremel tools and similar devices can help you achieve intricate designs quickly. They are versatile and suitable for both detailed and larger engravings.
- Laser Engravers: For more advanced projects, laser engravers can produce highly detailed and precise designs. They are ideal for intricate patterns and can work on various materials.
- Engraving Pens: These are electric tools designed specifically for engraving on wood, providing ease of use for beginners.
Preparing the Wood Surface
Proper preparation of the wood surface is essential for achieving clean and precise engravings. Follow these steps to prepare your wood:
- Select the Right Wood: Softer woods like pine or cedar are easier to engrave than hardwoods like oak or maple.
- Sand the Surface: Use fine-grit sandpaper to smooth out the surface. This helps the engraving tool glide smoothly and prevents splintering.
- Clean the Surface: Remove any dust or debris from sanding using a clean cloth or compressed air.
- Transfer Your Design: You can sketch your design directly onto the wood or use transfer paper for more complex designs.
Engraving Techniques
Different engraving techniques can yield varying results. Here are some common methods:
- V-Carving: This method uses a V-shaped bit to create deep, narrow grooves. It’s ideal for text and detailed designs.
- Flat-Bottom Carving: Using flat bits, this technique is suitable for creating wider lines and areas with more depth.
- Texturing: This involves creating patterns on the wood surface without cutting deeply into the material. It can enhance the visual appeal of the engraving.
Technique | Best For | Tools Needed |
---|---|---|
V-Carving | Text and intricate designs | V-shaped bit, rotary tool |
Flat-Bottom Carving | Wider lines and deep cuts | Flat bits, rotary tool |
Texturing | Surface patterns | Various bits, rotary tool |
Finishing Touches
After completing the engraving, it’s important to finish the wood properly to enhance its appearance and durability. Consider the following steps:
- Clean the Engraved Area: Remove any debris or dust from the engraving using a soft brush.
- Apply Wood Finish: Use a wood stain or sealant to protect the engraving and enhance the wood grain. This step can significantly improve the visual appeal of your work.
- Polish the Surface: For a smooth finish, use a fine cloth to buff the surface after applying the finish.
By following these guidelines, you can achieve professional-quality engravings on wood, regardless of your skill level.
Materials Needed for Wood Engraving
To successfully engrave on wood, gather the following materials:
- Wood Surface: Choose softwoods like pine or hardwoods like oak depending on the desired finish.
- Engraving Tool: Options include:
- Handheld rotary tools (e.g., Dremel)
- Laser engravers
- Wood burning tools
- Design Template: Use paper or digital designs.
- Clamps: To secure the wood while engraving.
- Safety Gear: Goggles, mask, and gloves for protection.
Preparing the Wood Surface
Proper preparation ensures a smooth engraving process. Follow these steps:
- Select the Wood: Choose a piece that is free of knots and imperfections.
- Sand the Surface: Use fine-grit sandpaper to create a smooth, even surface.
- Clean the Surface: Remove dust and debris with a damp cloth and let it dry completely.
- Apply a Base Coat (optional): For a better finish, apply a wood sealer or a coat of paint, allowing it to dry.
Engraving Techniques
Different techniques can be used for engraving on wood, depending on the tools available:
- Hand Engraving:
- Use a chisel or gouge to carve designs manually.
- Control depth and angle for varied effects.
- Rotary Tool Engraving:
- Attach a suitable engraving bit.
- Follow the design template carefully.
- Adjust speed settings based on the wood type to prevent burning.
- Laser Engraving:
- Set the laser cutter to the appropriate power and speed.
- Upload the design and ensure it fits the wood dimensions.
- Monitor the process to avoid excessive burning or cutting through the material.
Engraving Tips and Best Practices
Implement the following tips for optimal results:
- Test on Scrap Wood: Always practice on a similar wood type before working on the final piece.
- Maintain Consistent Pressure: Apply even pressure to ensure uniform depth and design clarity.
- Work Slowly: Take your time to avoid mistakes and ensure precision.
- Clean the Engraved Area: Remove debris with a brush or cloth to reveal the design clearly.
- Finish the Wood: Consider sealing the engraving with varnish or wood oil for protection and enhanced appearance.
Common Mistakes to Avoid
To enhance your engraving experience, be mindful of these common pitfalls:
Mistake | Description |
---|---|
Skipping Surface Preparation | Not sanding or cleaning can lead to poor engraving quality. |
Using Incorrect Tool Speed | Too high speeds may burn the wood; too low may not engrave effectively. |
Ignoring Safety Precautions | Failing to wear protective gear can result in injuries. |
Rushing the Process | Hurrying can lead to mistakes and uneven designs. |
Post-Engraving Care
After completing the engraving, follow these care steps to ensure longevity:
- Remove Dust: Gently brush off any remaining dust or debris.
- Apply Finish: Use wood oil, wax, or a sealant to protect the engraving and enhance its visibility.
- Store Properly: Keep the engraved item in a dry, safe place to prevent damage or wear.
By following these guidelines, you can achieve high-quality engravings on wood, whether for personal projects or professional use.
Expert Insights on Engraving Techniques for Wood
Emily Carter (Master Woodworker, Artisan Crafts Journal). “Engraving on wood requires a clear understanding of the type of wood being used. Softer woods like pine are easier to engrave, while harder woods such as oak may require more powerful tools and precise techniques to achieve clean results.”
David Chen (Laser Engraving Specialist, TechWood Innovations). “Using a laser engraver can significantly enhance the precision and detail of your designs. It is essential to adjust the speed and power settings according to the wood type to prevent burning or charring the surface.”
Rachel Torres (Artistic Designer, Creative Woodworks). “Incorporating different engraving techniques, such as rotary engraving or hand carving, can add unique textures and depth to your projects. Experimenting with various tools will help you discover the best method for your artistic vision.”
Frequently Asked Questions (FAQs)
How do you prepare wood for engraving?
To prepare wood for engraving, start by sanding the surface to remove any rough spots or imperfections. Clean the surface to eliminate dust and debris, ensuring a smooth and even engraving process.
What tools are needed for engraving on wood?
Common tools for wood engraving include rotary tools with engraving bits, laser engravers, and hand-held engraving tools. The choice of tool depends on the complexity of the design and the desired finish.
Can any type of wood be engraved?
Most types of wood can be engraved, but softer woods like pine and basswood are easier to work with and yield cleaner results. Hardwoods like oak or maple may require more advanced tools and techniques.
How deep should the engraving be on wood?
The depth of the engraving typically ranges from 1/32 inch to 1/8 inch, depending on the design and the intended use. Shallower engravings are suitable for decorative purposes, while deeper engravings may be necessary for durability.
Is it necessary to apply a finish after engraving?
Applying a finish after engraving is recommended to protect the wood and enhance the appearance of the design. Finishes such as varnish, lacquer, or oil can provide a protective layer and bring out the wood’s natural beauty.
What design considerations should be taken into account when engraving on wood?
When designing for wood engraving, consider the grain direction, type of wood, and size of the engraving. Simple designs with clear lines work best, as intricate details may become less defined due to the wood’s texture.
Engraving on wood is a versatile and rewarding craft that allows for the personalization of items, creation of art, and enhancement of woodworking projects. The process can be achieved through various methods, including hand engraving, laser engraving, and rotary tools, each offering distinct advantages and suitable applications. Understanding the properties of different types of wood is crucial, as it affects the engraving outcome, tool selection, and technique used.
Preparation is a key step in the engraving process. Properly selecting and preparing the wood surface ensures that the engraving is clean and precise. Techniques such as sanding and applying a suitable finish can enhance the final appearance of the engraved design. Additionally, planning the design layout and choosing the right tools will significantly impact the quality of the work.
Safety precautions should not be overlooked when engraving on wood. Using appropriate protective gear, such as goggles and masks, is essential to prevent injury and inhalation of dust particles. Moreover, maintaining a clean workspace and proper tool handling can prevent accidents and ensure a smooth engraving process.
In summary, engraving on wood is an accessible craft that combines creativity with technical skill. By understanding the various methods, preparing the wood properly, and adhering to safety measures, individuals can achieve beautiful and lasting
Author Profile
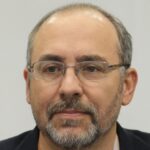
-
Darryl Norman is a seasoned entrepreneur and industry expert with a deep understanding of wood truss manufacturing and construction materials. As the President of Timberlake TrussWorks, LLC, Darryl played a pivotal role in shaping the company’s reputation for quality and precision. His leadership ensured that each truss met rigorous structural standards, providing builders with dependable components essential to their projects.
Beginning in 2025, Darryl Norman has shifted his focus to education and knowledge-sharing through an informative blog dedicated to wood truss manufacturing. Drawing from his extensive experience in the field, he provides in-depth insights into truss design, material selection, and construction techniques. This blog serves as a valuable resource for builders, contractors, and homeowners seeking practical guidance on truss systems and structural integrity.
Latest entries
- March 18, 2025General Wood TopicsWhat Color Is Ebony Wood? Unveiling the Rich Hues of This Luxurious Timber
- March 18, 2025Construction & FrameworkHow Can You Effectively Mount a Headboard to Your Wall?
- March 18, 2025General Wood TopicsCan Bees Really Eat Wood? Unraveling the Myths and Facts
- March 18, 2025General Wood TopicsDo Rabbits Really Chew on Wood? Exploring Their Eating Habits!