How Do You Engrave Wood: A Step-by-Step Guide for Beginners?
Engraving wood is a timeless craft that marries artistry with precision, allowing creators to transform simple wooden surfaces into extraordinary works of art. Whether you’re looking to personalize a gift, create unique home decor, or embark on a creative project, understanding the fundamentals of wood engraving can open up a world of possibilities. With the right tools, techniques, and a bit of practice, you can turn your visions into reality, making every piece a reflection of your individual style and creativity.
At its core, wood engraving involves carving designs into the surface of wood, a process that can be achieved through various methods ranging from traditional hand tools to modern laser technology. Each approach offers its own set of advantages, catering to different skill levels and project requirements. The choice of wood type, design complexity, and engraving technique all play crucial roles in the final outcome, making it essential for aspiring engravers to consider these factors carefully.
As you delve deeper into the art of wood engraving, you’ll discover a wealth of techniques and tips that can enhance your skills and elevate your projects. From selecting the right tools to mastering the intricacies of design transfer, this article will guide you through the essential steps to help you create stunning engraved pieces that are sure to impress. Whether you’re a beginner or an experienced artisan, the
Tools Required for Wood Engraving
To achieve precise and high-quality engravings on wood, several tools are essential. The choice of tools depends on the engraving method you plan to use.
- Hand Tools:
- Chisels: Useful for detailed work and creating designs by hand.
- V-Tools: Ideal for outlining and finer details.
- Gouges: Best for creating deeper cuts and textures.
- Power Tools:
- Rotary Tool: Versatile and can be fitted with various bits for engraving.
- Laser Engraver: Provides precision and can handle complex designs.
- Dremel Tool: A popular choice for detailed work with various attachments.
- Safety Equipment:
- Safety Glasses: Protects your eyes from wood chips and debris.
- Dust Mask: Prevents inhalation of wood dust.
- Gloves: Protects your hands from sharp tools.
Engraving Techniques
Various techniques can be employed for engraving wood, each yielding different results based on the desired outcome.
- Hand Engraving: Involves using chisels and other hand tools to carve designs directly into the wood. This method requires practice and skill but offers a personal touch.
- Power Engraving: Utilizes rotary tools or laser engravers for quicker and more uniform designs. This technique is suitable for both intricate and larger projects.
- Pyrography: Also known as wood burning, this technique uses a heated tool to burn designs into the wood, creating a unique texture and appearance.
Choosing the Right Wood
Selecting the appropriate type of wood is crucial for successful engraving. Different woods react differently to engraving techniques.
Wood Type | Characteristics | Best Uses |
---|---|---|
Softwoods | Easier to carve, less resistance | Fine details, beginners |
Hardwoods | More durable, can achieve finer detail | Long-lasting items, intricate designs |
Plywood | Consistent layers, versatile | Craft projects, signage |
Bamboo | Eco-friendly, unique appearance | Decorative items, art pieces |
When choosing wood, consider the grain, density, and finish. Fine-grained woods generally provide better results for intricate designs, while denser woods offer durability.
Preparing the Wood Surface
Proper preparation of the wood surface is essential for achieving the best engraving results.
- Sanding: Start with coarse sandpaper (e.g., 80-grit) and progress to finer grits (up to 220-grit) to create a smooth surface.
- Cleaning: Remove dust and debris using a damp cloth. Ensure the surface is completely dry before engraving.
- Marking the Design: Use a pencil or transfer paper to outline the design on the wood. This step serves as a guide during engraving.
By following these steps, you will ensure that the wood is adequately prepared for the engraving process, leading to cleaner and more precise results.
Understanding the Tools for Wood Engraving
Wood engraving requires specific tools to achieve the desired results. The choice of tool depends on the technique and detail level.
- Hand Tools:
- Chisels: Used for carving intricate designs. They come in various shapes and sizes.
- V-gouges: Perfect for creating sharp lines and details.
- Wood knives: Ideal for fine detailing and trimming.
- Power Tools:
- Dremel or rotary tools: Versatile for both engraving and polishing.
- Laser engravers: Provide precision and can handle complex designs.
- Other Tools:
- Sandpaper: For finishing touches and smoothing surfaces.
- Pencils or markers: For outlining designs before engraving.
Preparing the Wood Surface
Proper surface preparation is crucial for a successful engraving process. Follow these steps:
- Select the Right Wood: Choose a softwood like pine or a hardwood like oak, depending on the desired effect.
- Sand the Surface: Use fine-grit sandpaper (220 grit or higher) to smooth the wood.
- Clean the Surface: Wipe off dust and debris with a damp cloth to ensure a clean engraving area.
- Mark Your Design: Use a pencil or marker to sketch the design lightly on the wood.
Engraving Techniques
Different techniques yield varying results in wood engraving. Below are popular methods:
- Carving:
- Utilize hand tools to remove wood and create depth.
- Best for three-dimensional designs.
- Burning:
- Use a wood-burning tool to scorch the surface.
- Ideal for adding texture and shading.
- Laser Engraving:
- Employ a laser engraver for precision etching.
- Suitable for complex patterns and detailed images.
Step-by-Step Engraving Process
Follow these steps for effective wood engraving, regardless of technique:
Step | Description |
---|---|
1 | Prepare the wood surface by sanding and cleaning. |
2 | Sketch your design lightly on the wood. |
3 | Choose your engraving tool based on the selected technique. |
4 | Begin engraving by following the marked design, applying even pressure. |
5 | Regularly check the progress to ensure accuracy. |
6 | Finish by sanding edges for a smooth look and applying a finish if desired. |
Finishing Touches
After engraving, it’s essential to enhance the wood’s appearance and durability:
- Sanding: Lightly sand around the engraved area to remove any rough edges.
- Staining: Apply wood stain to enhance color contrast and highlight the engraving.
- Sealing: Use polyurethane or varnish to protect the wood and engraving from moisture and wear.
- Polishing: Buff the surface for a smooth, finished look.
Maintaining the engraved wood piece involves regular dusting and applying a suitable polish to preserve its beauty.
Expert Techniques for Engraving Wood
Emily Carter (Master Woodworker, Artisan’s Guild). “When engraving wood, it is crucial to select the right type of wood for your project. Softwoods like pine are easier to engrave but may not hold fine details as well as hardwoods like oak or maple. Always test your engraving technique on a scrap piece of wood to ensure the desired outcome.”
James Liu (Laser Engraving Specialist, TechCraft Innovations). “Utilizing a laser engraver can significantly enhance the precision of your wood engraving. It allows for intricate designs and can be adjusted for depth and speed, which is essential for achieving clean lines and detailed patterns.”
Maria Gonzalez (DIY Craft Instructor, Creative Hands Workshop). “For those new to wood engraving, I recommend starting with hand tools such as chisels or rotary tools. This hands-on approach helps develop a feel for the material and the engraving process, making it easier to transition to more advanced techniques later.”
Frequently Asked Questions (FAQs)
How do you engrave wood using a laser engraver?
Laser engraving involves using a focused beam of light to remove material from the wood surface. First, design your artwork using graphic design software. Then, set the appropriate power and speed settings on the laser engraver based on the wood type. Finally, place the wood on the engraving bed and start the machine to create the design.
What tools are needed for manual wood engraving?
Manual wood engraving requires specific tools such as engraving knives, chisels, or gouges, depending on the desired effect. Additionally, a bench hook or engraving board, safety goggles, and a steady hand are essential for precision and safety during the engraving process.
Can you engrave wood with a Dremel tool?
Yes, a Dremel tool can effectively engrave wood. By using a suitable engraving bit, you can create detailed designs. Ensure to set the Dremel to a low speed to maintain control and prevent the wood from burning.
What types of wood are best for engraving?
Softwoods like pine and cedar are ideal for engraving due to their ease of carving. Hardwoods such as maple and cherry can also be engraved but may require sharper tools and more effort. Ultimately, the choice depends on the desired finish and detail level.
Is it necessary to sand the wood before engraving?
Sanding the wood before engraving is recommended to create a smooth surface. This preparation helps achieve cleaner lines and better detail in the final engraving. Use fine-grit sandpaper to ensure an even finish.
How do you finish engraved wood to enhance its appearance?
To enhance the appearance of engraved wood, apply a finish such as wood oil, varnish, or polyurethane. These finishes protect the wood and accentuate the engraved details. Ensure the engraving is clean and free of dust before applying the finish for optimal results.
Engraving wood is a meticulous process that combines artistry with technical skill. The primary methods for wood engraving include hand tools, such as chisels and gouges, as well as modern techniques like laser engraving. Each method offers unique advantages, with hand tools allowing for a traditional, tactile experience, while laser engraving provides precision and efficiency. Understanding the type of wood and its grain is crucial, as different woods react differently to engraving techniques, influencing the final appearance of the design.
Preparation is essential for successful wood engraving. This includes selecting the appropriate tools and ensuring the wood surface is clean and smooth. Proper design planning, including sketching or using digital software, can greatly enhance the engraving process. Additionally, safety measures should be prioritized, especially when using power tools or lasers, to prevent accidents and ensure a safe working environment.
engraving wood is an art form that requires careful consideration of techniques, tools, and materials. Whether opting for traditional hand engraving or modern laser methods, understanding the nuances of wood and preparation can significantly impact the quality of the finished product. Engraving not only allows for the creation of beautiful designs but also enables personalization and craftsmanship that can be cherished for years to come.
Author Profile
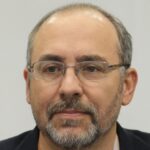
-
Darryl Norman is a seasoned entrepreneur and industry expert with a deep understanding of wood truss manufacturing and construction materials. As the President of Timberlake TrussWorks, LLC, Darryl played a pivotal role in shaping the company’s reputation for quality and precision. His leadership ensured that each truss met rigorous structural standards, providing builders with dependable components essential to their projects.
Beginning in 2025, Darryl Norman has shifted his focus to education and knowledge-sharing through an informative blog dedicated to wood truss manufacturing. Drawing from his extensive experience in the field, he provides in-depth insights into truss design, material selection, and construction techniques. This blog serves as a valuable resource for builders, contractors, and homeowners seeking practical guidance on truss systems and structural integrity.
Latest entries
- March 18, 2025General Wood TopicsWhat Color Is Ebony Wood? Unveiling the Rich Hues of This Luxurious Timber
- March 18, 2025Construction & FrameworkHow Can You Effectively Mount a Headboard to Your Wall?
- March 18, 2025General Wood TopicsCan Bees Really Eat Wood? Unraveling the Myths and Facts
- March 18, 2025General Wood TopicsDo Rabbits Really Chew on Wood? Exploring Their Eating Habits!