How Do You Make Wood Pellets? A Step-by-Step Guide to the Process
In recent years, wood pellets have emerged as a popular and sustainable energy source, captivating eco-conscious consumers and industries alike. These small, cylindrical pieces of compressed wood are not only an efficient fuel option but also a testament to the ingenuity of recycling and repurposing natural materials. As the world shifts towards greener alternatives, understanding how wood pellets are made becomes essential for anyone interested in renewable energy solutions. Whether you’re a homeowner looking to heat your space sustainably or a business seeking eco-friendly practices, the journey of wood pellets from raw material to finished product is both fascinating and informative.
Creating wood pellets involves a meticulous process that transforms sawdust and wood shavings into a compact form of energy. The journey begins with sourcing the right type of wood, often by utilizing byproducts from lumber mills or forestry operations. This not only reduces waste but also ensures that the production process is environmentally friendly. Once the raw materials are collected, they undergo a series of steps including drying, grinding, and compressing, all designed to maximize efficiency and energy output.
The final product, wood pellets, is not just a fuel source; it represents a commitment to sustainability and innovation. As you delve deeper into the intricacies of wood pellet production, you’ll discover the various techniques and technologies that enhance their
Raw Material Selection
The first step in making wood pellets is selecting the right raw materials. The quality of the pellets significantly depends on the type of wood used and its moisture content. Ideal raw materials include:
- Sawdust
- Wood shavings
- Wood chips
- Agricultural residues (such as straw or corn stover)
Hardwoods like oak and maple produce denser and more energy-efficient pellets compared to softwoods. Additionally, the moisture content of the raw material should be between 10% and 15% to ensure optimal pellet formation. If the moisture level is too high, it can lead to poor pellet quality and increased energy consumption during the pelleting process.
Drying Process
Once the raw materials are selected, they typically undergo a drying process to reduce moisture content. This can be accomplished using various methods:
- Air Drying: Exposing the material to ambient air for several days.
- Kiln Drying: Utilizing a controlled environment to expedite moisture removal.
- Flash Drying: Rapid drying using hot air in a specialized drying system.
The goal is to achieve uniform moisture content, which enhances the efficiency of the subsequent pelleting process.
Grinding and Milling
The dried raw materials are then ground into finer particles to ensure uniformity. This step is crucial as it increases the surface area, allowing for better compaction during pelleting. Grinding equipment may include:
- Hammer mills
- Roller mills
The material should be reduced to a size of approximately 3mm to 6mm for optimal pelleting results.
Pelleting Process
In the pelleting phase, the finely ground material is subjected to high pressure and temperature to form pellets. This is typically achieved using a pellet mill. The key parameters during this process include:
- Die Temperature: Should be maintained between 70°C to 90°C.
- Pressure: High pressure is applied to compress the material.
During pelleting, lignin within the wood acts as a natural binder, helping to hold the pellets together. The final size of the pellets is usually around 6mm to 8mm in diameter.
Cooling and Screening
After the pelleting process, the freshly made pellets are hot and may contain residual moisture. Cooling is necessary to harden the pellets and reduce breakage during handling. This is commonly achieved using a counter-flow cooler.
Screening is then performed to remove any fines or broken pellets, ensuring only high-quality pellets proceed to packaging.
Process | Description |
---|---|
Raw Material Selection | Choosing suitable wood types and ensuring proper moisture content. |
Drying Process | Reducing moisture through air, kiln, or flash drying. |
Grinding and Milling | Grinding materials to a fine consistency for better compaction. |
Pelleting Process | Forming pellets under high pressure and temperature. |
Cooling and Screening | Cooling pellets and removing fines to ensure quality. |
Packaging and Storage
The final step involves packaging the pellets for distribution and storage. Pellets are typically bagged or stored in bulk containers. Proper storage is crucial to prevent moisture absorption and degradation of quality. Ideal storage conditions include:
- A dry environment
- Elevated storage to avoid contact with moisture
- Protection from direct sunlight
These measures help maintain the integrity and energy efficiency of the wood pellets until they are ready for use.
Raw Material Selection
Choosing the right raw materials is crucial for making high-quality wood pellets. The most commonly used materials include:
- Wood Sawdust: A primary ingredient, ideally sourced from hardwoods or softwoods.
- Wood Shavings: Often a byproduct of woodworking processes, suitable for pellet production.
- Wood Chips: Larger than sawdust but can be processed into smaller pieces.
- Agricultural Residues: Such as straw or corn stalks, can be blended with wood materials.
Quality of the raw material impacts the density, durability, and burn efficiency of the final pellets.
Size Reduction
The raw materials must be processed to a uniform size to ensure efficient pelletization. This involves:
- Chipping: Larger wood pieces are chipped into smaller fragments.
- Grinding: The chipped material is ground down to a fine consistency, typically less than 1/4 inch in diameter.
Machinery used includes hammer mills and grinders, which help achieve the desired particle size.
Drying Process
Moisture content plays a significant role in pellet production. The ideal moisture level for wood pellets is between 10-15%. The drying process can be achieved using:
- Air Drying: Natural drying using ambient air over several days.
- Kiln Drying: Using heat to rapidly reduce moisture content.
Maintaining the correct moisture level is essential to ensure proper pellet formation and combustion efficiency.
Pelletizing
The pelletizing process compresses the dried and sized materials into pellets. This involves:
- Conditioning: Adding steam or moisture to the material to enhance pliability.
- Extrusion: Forcing the conditioned material through a die in a pellet mill, which shapes it into pellets.
Pellet mills vary in design, including flat die and ring die types, each offering different capacities and efficiencies.
Cooling and Packaging
After pelletization, the pellets are hot and require cooling. This is typically done using:
- Coolers: Air-cooling systems that bring down the temperature and moisture content.
Once cooled, the pellets are packaged for storage or transport. Packaging methods include:
- Bulk Bags: Large bags for transport to retailers or wholesalers.
- Small Bags: Retail-sized bags for consumer sales.
Quality Control Measures
Quality control is essential throughout the wood pellet production process. Key measures include:
- Moisture Testing: Ensuring pellets maintain the optimal moisture content.
- Durability Testing: Assessing the strength and resistance of pellets to breakage.
- Calorific Value Testing: Measuring the energy output of the pellets.
Regular testing ensures the final product meets industry standards and customer expectations.
Environmental Considerations
Sustainable practices in wood pellet production are vital. Considerations include:
- Sourcing Materials: Using sustainably harvested wood and waste materials.
- Energy Use: Implementing energy-efficient machinery and processes.
- Waste Management: Minimizing waste and recycling byproducts.
Adhering to environmental standards contributes to a more sustainable industry overall.
Expert Insights on the Wood Pellet Manufacturing Process
Dr. Emily Carter (Renewable Energy Specialist, GreenTech Innovations). “The process of making wood pellets begins with sourcing high-quality raw materials, typically sawdust or wood shavings. These materials must be dried to a specific moisture content to ensure efficient pelletization and combustion.”
Mark Thompson (Wood Processing Engineer, TimberTech Solutions). “Once the raw materials are prepared, they undergo a grinding process to achieve a uniform particle size. This is crucial, as it affects the density and durability of the final pellets. Following grinding, the material is subjected to high pressure and temperature in a pellet mill, which binds the particles together.”
Linda Garcia (Sustainability Consultant, EcoFuel Advisors). “After pelletization, the wood pellets must be cooled and screened to remove any fines. Proper storage is essential to maintain quality, as pellets can absorb moisture from the environment. Understanding these steps is vital for anyone looking to enter the wood pellet market.”
Frequently Asked Questions (FAQs)
How do you make wood pellets?
Wood pellets are made by grinding wood into sawdust, drying it to reduce moisture content, and then compressing it under high pressure through a pellet mill, which forms small cylindrical pellets.
What types of wood are best for making pellets?
Hardwoods such as oak, maple, and hickory are preferred for their density and energy content, while softwoods like pine and spruce can also be used, providing a different burn quality and ash content.
What equipment is needed to produce wood pellets?
Essential equipment includes a wood chipper or grinder for reducing wood to sawdust, a dryer for moisture control, a pellet mill for shaping the pellets, and a cooler for reducing the temperature of the pellets post-production.
What is the ideal moisture content for wood pellets?
The ideal moisture content for wood pellets is typically between 8% and 10%. This range ensures optimal combustion efficiency and minimizes the risk of mold growth during storage.
Can you make wood pellets at home?
Yes, it is possible to make wood pellets at home using a small-scale pellet mill, provided you have access to appropriate raw materials and equipment for drying and grinding the wood.
How should wood pellets be stored?
Wood pellets should be stored in a cool, dry place, ideally in a sealed container or bag to protect them from moisture and pests, which can degrade their quality and performance.
the process of making wood pellets involves several critical steps that ensure the production of high-quality fuel. It begins with the selection of raw materials, typically wood shavings, sawdust, or other biomass sources, which must be dried to an appropriate moisture content. This is essential as excessive moisture can hinder the pelletization process and affect the energy density of the final product.
The next phase involves grinding the dried materials into a fine powder, which facilitates the pellet formation. This powder is then subjected to high pressure and temperature within a pellet mill, where it is compressed into small, cylindrical shapes. The heat generated during this process helps to bind the particles together, primarily due to the natural lignin present in the wood, which acts as a binding agent.
Finally, the newly formed pellets are cooled and can be screened to remove any fines. Proper storage is crucial to maintain their quality, as wood pellets are susceptible to moisture absorption. Overall, understanding these steps is vital for anyone interested in producing wood pellets, whether for personal use or commercial purposes.
Key takeaways from this discussion include the importance of moisture control, the role of grinding in pellet production, and the necessity of cooling and proper storage to ensure the longevity
Author Profile
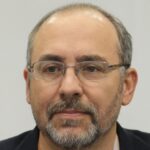
-
Darryl Norman is a seasoned entrepreneur and industry expert with a deep understanding of wood truss manufacturing and construction materials. As the President of Timberlake TrussWorks, LLC, Darryl played a pivotal role in shaping the company’s reputation for quality and precision. His leadership ensured that each truss met rigorous structural standards, providing builders with dependable components essential to their projects.
Beginning in 2025, Darryl Norman has shifted his focus to education and knowledge-sharing through an informative blog dedicated to wood truss manufacturing. Drawing from his extensive experience in the field, he provides in-depth insights into truss design, material selection, and construction techniques. This blog serves as a valuable resource for builders, contractors, and homeowners seeking practical guidance on truss systems and structural integrity.
Latest entries
- March 18, 2025General Wood TopicsWhat Color Is Ebony Wood? Unveiling the Rich Hues of This Luxurious Timber
- March 18, 2025Construction & FrameworkHow Can You Effectively Mount a Headboard to Your Wall?
- March 18, 2025General Wood TopicsCan Bees Really Eat Wood? Unraveling the Myths and Facts
- March 18, 2025General Wood TopicsDo Rabbits Really Chew on Wood? Exploring Their Eating Habits!