How Does a Wood Chipper Work? Unraveling the Mechanics Behind This Essential Tool
Have you ever gazed at a pile of fallen branches and leaves in your yard and wondered how to turn that mess into mulch? Enter the wood chipper, a powerful tool that transforms bulky yard waste into manageable chips, making landscaping and gardening tasks easier than ever. Whether you’re a homeowner looking to tidy up your garden or a professional landscaper seeking efficiency, understanding how a wood chipper works can unlock a world of possibilities for waste reduction and resourceful gardening. In this article, we’ll delve into the mechanics behind this essential outdoor equipment, revealing the fascinating process that converts raw wood into useful material.
Wood chippers are ingeniously designed machines that utilize sharp blades and a robust engine to break down larger pieces of wood into smaller, more manageable chips. At their core, these machines operate on a straightforward principle: feed the wood into the chipper, and watch as it is shredded into fine pieces. The process not only helps in reducing the volume of yard waste but also creates a valuable byproduct that can be used for mulch, compost, or even fuel.
Understanding the inner workings of a wood chipper can enhance your appreciation for this remarkable tool. From the feeding mechanism that guides the branches into the chipper to the rotating blades that perform the heavy lifting,
Components of a Wood Chipper
A wood chipper consists of several key components that work together to convert branches and other wood materials into small chips. Understanding these components is essential for grasping how the machine operates effectively. The main parts include:
- Feeding Chute: This is where the wood is inserted into the chipper. It is designed to guide the material into the cutting mechanism safely.
- Blades or Cutting Mechanism: The heart of the chipper, these sharp blades rotate at high speeds to slice through the wood. They can be made of hardened steel or other durable materials to withstand wear.
- Engine: The engine powers the chipper, typically available in gas, electric, or diesel options, depending on the size and intended use of the machine.
- Discharge Chute: After the wood is chipped, the small pieces are expelled through this chute, which can often be directed to a specific area.
- Frame and Wheels: The frame supports all components, while wheels provide mobility for easy transport across different terrains.
Operating Mechanism
When the wood chipper is operational, the process begins with the user feeding branches or wood debris into the feeding chute. The following sequence outlines the working mechanism:
- Feeding: The operator places the wood into the feeding chute. Some models feature automatic feeding mechanisms that pull the wood into the chipper.
- Cutting: Once inside, the wood encounters the rotating blades. These blades spin rapidly, cutting the wood into smaller pieces.
- Chipping: The cut pieces are further processed by additional blades or knives, reducing them to chips of uniform size.
- Discharge: Finally, the wood chips exit through the discharge chute, where they can be directed into a collection bag or onto the ground.
This systematic process allows wood chippers to efficiently handle large volumes of material while producing consistent chip sizes.
Types of Wood Chippers
There are various types of wood chippers available, each suited for different applications and user needs. The main types include:
Type | Description | Ideal Use |
---|---|---|
Towable Chippers | Large units that can be towed behind vehicles. | Commercial landscaping and tree services. |
Self-Contained | Portable units with built-in engines. | Homeowners for yard maintenance. |
Electric Chippers | Smaller, quieter units powered by electricity. | Residential use for small branches. |
Industrial Chippers | Heavy-duty machines for large-scale wood processing. | Timber mills and large construction sites. |
Each type has its specific advantages and is designed for different scales of operation, making it crucial for users to choose one that meets their requirements.
Safety Considerations
Operating a wood chipper involves inherent risks, and following safety protocols is paramount to prevent accidents. Key safety considerations include:
- Protective Gear: Always wear safety goggles, gloves, and hearing protection.
- Clear Area: Ensure the working area is free from bystanders and obstacles.
- Proper Feeding: Never place hands or fingers near the feeding chute while the machine is running.
- Regular Maintenance: Keep blades sharp and check for any mechanical issues before use.
By adhering to these guidelines, operators can significantly reduce the risk of injury while effectively utilizing the wood chipper.
Understanding the Components of a Wood Chipper
A wood chipper comprises several essential components that work together to process wood efficiently. The main parts include:
- Feeding Chute: This is where you insert branches and wood into the chipper. It is designed to guide the material into the cutting mechanism.
- Blades: The cutting blades are typically made of hardened steel and are responsible for shredding the wood. They can be fixed or rotating, depending on the design of the chipper.
- Rotor: The rotor is a cylindrical component that spins at high speeds, facilitating the cutting process. It houses the blades and helps in the chipping action.
- Discharge Chute: After the wood is processed, the chips are expelled through the discharge chute. The angle and direction can usually be adjusted for convenience.
- Engine: Most wood chippers are powered by either a gas engine or an electric motor, providing the necessary force for operation.
How the Chipping Process Works
The operation of a wood chipper can be broken down into several sequential steps:
- Feeding: The user inserts branches or wood into the feeding chute. The design often includes a safety mechanism to prevent accidental injury.
- Cutting: As the material enters the chipper, it comes into contact with the rotating blades on the rotor. The blades slice through the wood fibers, reducing them to smaller pieces.
- Chipping: The continuous rotation of the rotor ensures that the wood is not only cut but also shredded into chips. The size of the chips can vary based on the chipper design and the sharpness of the blades.
- Discharge: Once the wood is chipped, the material is expelled through the discharge chute. This can be directed into a collection bag, trailer, or simply onto the ground.
Types of Wood Chippers
Wood chippers come in various types, each suited for different applications:
Type | Description | Best Suited For |
---|---|---|
Electric Chippers | Lightweight and quieter, powered by electricity. | Small yard debris and light branches. |
Gas-Powered Chippers | More powerful and portable, using gasoline engines. | Larger jobs and thicker branches. |
Tow-Behind Chippers | Designed to be towed by vehicles, ideal for extensive work. | Commercial use and large-scale operations. |
Commercial Chippers | Heavy-duty machines built for high volume. | Landscaping, forestry, and tree care. |
Maintenance Tips for Wood Chippers
Regular maintenance is crucial to ensure optimal performance and longevity of a wood chipper. Key maintenance practices include:
- Blade Sharpening: Keep blades sharp for efficient chipping. Dull blades increase strain on the engine and reduce performance.
- Engine Checks: Regularly inspect oil levels, air filters, and spark plugs to maintain engine health.
- Cleaning: Remove debris and build-up from the machine after each use to prevent corrosion and mechanical issues.
- Lubrication: Apply lubricant to moving parts as specified by the manufacturer to reduce wear and tear.
- Safety Inspections: Regularly check safety features and emergency stops to ensure they are functional.
Safety Precautions When Using a Wood Chipper
Using a wood chipper involves certain risks; thus, adherence to safety precautions is vital:
- Personal Protective Equipment (PPE): Always wear gloves, goggles, and ear protection.
- Keep Hands Clear: Never reach into the feeding chute while the chipper is running.
- Feed Wood Properly: Insert wood in the correct orientation to avoid kickback or jams.
- Avoid Loose Clothing: Ensure that clothing is fitted to prevent entanglement in moving parts.
- Follow Manufacturer Guidelines: Adhere to the operational guidelines provided in the user manual.
Understanding the Mechanics of Wood Chippers
Dr. Emily Carter (Mechanical Engineer, TimberTech Innovations). “A wood chipper operates by using sharp blades to shred branches and other wood materials into smaller pieces. The design typically includes a feed chute where the material is inserted, and as the wood is fed into the machine, it is pulled into the cutting chamber where it encounters rotating blades that efficiently reduce it to chips.”
James Thompson (Landscape Management Specialist, GreenScape Solutions). “The effectiveness of a wood chipper is largely dependent on its power source and blade design. Electric chippers are quieter and suitable for smaller jobs, while gas-powered models offer higher throughput and can handle larger branches. Understanding the specific needs of your landscaping project is crucial in selecting the right type of wood chipper.”
Linda Martinez (Environmental Engineer, EcoWaste Management). “Wood chippers not only help in waste management by reducing the volume of organic materials but also contribute to sustainable practices. The chips produced can be used as mulch, which helps retain soil moisture and suppress weeds, thus promoting a healthier ecosystem.”
Frequently Asked Questions (FAQs)
How does a wood chipper work?
A wood chipper operates by using sharp blades to shred branches and other wood materials into smaller pieces. The wood is fed into the machine, where it is cut and processed, resulting in wood chips that can be used for mulch or compost.
What types of wood chippers are available?
There are several types of wood chippers, including electric chippers, gas-powered chippers, and tow-behind chippers. Each type varies in power, capacity, and intended use, catering to different needs from residential to commercial applications.
What materials can be processed by a wood chipper?
Wood chippers are designed to handle a variety of materials, including branches, leaves, and small trees. However, they should not be used for processing materials like metal, plastic, or large logs that exceed the machine’s capacity.
Is it safe to operate a wood chipper?
Operating a wood chipper can be safe when following proper safety precautions. Users should wear protective gear, keep hands and loose clothing away from the feed area, and ensure the machine is in good working condition before use.
How do I maintain a wood chipper?
Regular maintenance of a wood chipper includes cleaning the blades, checking for wear and tear, lubricating moving parts, and inspecting the engine or motor. Following the manufacturer’s guidelines will help ensure optimal performance and longevity.
Can a wood chipper handle wet wood?
While wood chippers can process wet wood, it may lead to clogging and reduced efficiency. It is generally recommended to chip dry wood for better performance and to avoid potential damage to the machine.
In summary, a wood chipper is a powerful machine designed to reduce large volumes of wood and organic material into manageable chips. The operation of a wood chipper involves a series of mechanical processes that utilize sharp blades or knives to cut, shred, and chip the material fed into it. Understanding the components of a wood chipper, including the feed mechanism, cutting system, and discharge chute, is essential for effective operation and maintenance.
Additionally, safety is a critical aspect of using a wood chipper. Operators must adhere to safety guidelines to prevent accidents and injuries. Proper personal protective equipment (PPE), such as gloves, goggles, and ear protection, should always be worn. Furthermore, it is important to familiarize oneself with the machine’s features and operating instructions to ensure safe and efficient use.
Lastly, wood chippers come in various sizes and types, catering to different needs, from small residential models to large commercial machines. This versatility allows users to select a wood chipper that best suits their specific requirements, whether for landscaping, yard cleanup, or larger-scale wood processing. By understanding the functionality and safety measures associated with wood chippers, users can maximize their effectiveness and ensure a safer working environment.
Author Profile
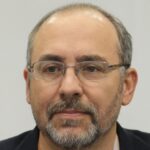
-
Darryl Norman is a seasoned entrepreneur and industry expert with a deep understanding of wood truss manufacturing and construction materials. As the President of Timberlake TrussWorks, LLC, Darryl played a pivotal role in shaping the company’s reputation for quality and precision. His leadership ensured that each truss met rigorous structural standards, providing builders with dependable components essential to their projects.
Beginning in 2025, Darryl Norman has shifted his focus to education and knowledge-sharing through an informative blog dedicated to wood truss manufacturing. Drawing from his extensive experience in the field, he provides in-depth insights into truss design, material selection, and construction techniques. This blog serves as a valuable resource for builders, contractors, and homeowners seeking practical guidance on truss systems and structural integrity.
Latest entries
- March 18, 2025General Wood TopicsWhat Color Is Ebony Wood? Unveiling the Rich Hues of This Luxurious Timber
- March 18, 2025Construction & FrameworkHow Can You Effectively Mount a Headboard to Your Wall?
- March 18, 2025General Wood TopicsCan Bees Really Eat Wood? Unraveling the Myths and Facts
- March 18, 2025General Wood TopicsDo Rabbits Really Chew on Wood? Exploring Their Eating Habits!