How Does Wood Gasification Work? Unraveling the Science Behind This Eco-Friendly Energy Source
In an era where sustainable energy solutions are more critical than ever, wood gasification emerges as a fascinating and innovative method of converting biomass into usable energy. This process not only offers a renewable alternative to fossil fuels but also showcases the remarkable ability of nature’s resources to power our modern lives. As we delve into the intricacies of wood gasification, we will uncover the science behind this transformative technology and its potential to revolutionize energy production while minimizing environmental impact.
Wood gasification is a thermochemical process that transforms organic materials, primarily wood, into a combustible gas known as syngas. This gas, composed mainly of hydrogen, carbon monoxide, and methane, can be harnessed for various applications, from generating electricity to powering vehicles. The process involves heating wood in a low-oxygen environment, which initiates a series of chemical reactions that break down the biomass into simpler compounds. Understanding how this conversion occurs is essential for appreciating the broader implications of wood gasification in the context of renewable energy.
As we explore the mechanics of wood gasification, we will also consider its advantages and challenges. This technology not only promotes energy independence by utilizing locally sourced materials but also contributes to waste reduction by repurposing wood residues and byproducts. However, the efficiency and economic viability
Wood Gasification Process
The wood gasification process involves the thermal decomposition of organic material in a low-oxygen environment, producing a mixture of gases known as syngas (synthetic gas). This process can be broken down into several distinct stages:
- Drying: The moisture content of the wood is reduced, which is crucial for efficient gasification. Typically, wood needs to be dried to below 20% moisture content.
- Pyrolysis: In this stage, the wood is heated to approximately 200-700°C in the absence of oxygen. This process breaks down the wood into solid charcoal, liquid tar, and gaseous byproducts.
- Gasification: The charcoal produced in the pyrolysis stage is further heated in the presence of a limited amount of oxygen or steam. This reaction converts the charcoal into syngas, which primarily consists of carbon monoxide (CO), hydrogen (H₂), and carbon dioxide (CO₂).
- Combustion: In some systems, the syngas can be combusted directly to generate heat or can be further processed to produce biofuels.
Key Components of a Wood Gasification System
A wood gasification system comprises several essential components that work together to facilitate the gasification process:
- Gasifier: The core unit where wood is converted into syngas. It includes a reactor chamber where pyrolysis and gasification occur.
- Feed System: This mechanism ensures a steady supply of wood chips or pellets into the gasifier.
- Cooling and Cleaning System: After gasification, the syngas must be cooled and cleaned to remove particulates and tar, which can damage engines or turbines.
- Power Generation Unit: This can be a gas engine or turbine that converts the syngas into usable energy.
Component | Function |
---|---|
Gasifier | Converts wood into syngas through pyrolysis and gasification. |
Feed System | Delivers wood chips or pellets into the gasifier. |
Cooling and Cleaning System | Removes tar and particulates from the syngas. |
Power Generation Unit | Converts syngas into electrical or mechanical energy. |
Applications of Wood Gasification
Wood gasification has a variety of applications across different sectors. Some notable uses include:
- Electricity Generation: Syngas can be burned in generators to produce electricity.
- Heat Production: The heat generated from burning syngas can be used for residential or industrial heating applications.
- Biofuel Production: Syngas can be further processed to create biofuels such as ethanol or biodiesel.
- Chemical Feedstock: The components of syngas can be used as feedstock for the synthesis of chemicals and materials.
These applications highlight the versatility of wood gasification in contributing to renewable energy solutions and reducing dependence on fossil fuels.
Principles of Wood Gasification
Wood gasification is a thermochemical process that converts organic materials, primarily wood, into a combustible gas known as wood gas or syngas. This process involves several stages, including drying, pyrolysis, combustion, and reduction.
- Drying: Moisture is removed from the wood, which is essential for effective gasification.
- Pyrolysis: At elevated temperatures, wood decomposes into volatile compounds and charcoal. This step produces gases, tars, and char.
- Combustion: A portion of the char is burned with limited oxygen to produce heat, which is crucial for the subsequent stages.
- Reduction: The remaining char reacts with the gases produced during pyrolysis, converting them into carbon monoxide (CO), hydrogen (H2), and methane (CH4).
Gas Composition
The composition of wood gas varies based on the feedstock and gasification conditions. Typically, wood gas consists of:
Component | Typical Volume Percentage |
---|---|
Carbon Dioxide (CO2) | 10-20% |
Carbon Monoxide (CO) | 20-30% |
Hydrogen (H2) | 15-20% |
Methane (CH4) | 5-15% |
Tars and other compounds | Varies |
This mixture can be used as a fuel for internal combustion engines, gas turbines, or for direct heating applications.
Types of Gasifiers
Wood gasifiers come in various designs, each suited for different applications. The main types include:
- Updraft Gasifier:
- Feedstock is loaded from the top.
- Gas flows upward through the fuel bed.
- Produces a relatively low-quality gas with higher tar content.
- Downdraft Gasifier:
- Feedstock is introduced from the top.
- Gas flows downward through the fuel bed.
- Produces cleaner gas with lower tar content, suitable for engines.
- Fluidized Bed Gasifier:
- Uses a bed of sand or other material fluidized by air.
- Provides uniform temperature and better conversion efficiency.
- Suitable for larger scale applications.
- Entrained Flow Gasifier:
- Uses fine particles of feedstock suspended in a gas stream.
- Operates at high temperatures and pressures.
- Produces high-quality gas and is used in industrial applications.
Applications of Wood Gas
Wood gas has a variety of applications, including:
- Electricity Generation:
- Can be used in gas engines or turbines for power production.
- Heat Production:
- Suitable for direct heating applications in industrial and residential settings.
- Chemical Production:
- Raw material for producing chemicals like methanol or ethanol.
- Transportation Fuel:
- Can be processed into biofuels for vehicles.
Factors Affecting Gasification Efficiency
The efficiency of wood gasification is influenced by several factors:
- Feedstock Characteristics:
- Type, moisture content, and size of wood affect gas yield and quality.
- Operating Conditions:
- Temperature, pressure, and airflow must be optimized for efficient gasification.
- Gasifier Design:
- The design impacts the residence time of gases and solids, influencing conversion rates.
- Catalysts:
- Use of catalysts can enhance reaction rates and improve gas quality.
By understanding these principles and factors, users can effectively utilize wood gasification for energy production and other applications.
Understanding the Mechanisms of Wood Gasification
Dr. Emily Carter (Renewable Energy Specialist, GreenTech Innovations). “Wood gasification is a thermochemical process that converts organic materials into a combustible gas, known as syngas. This process involves heating wood in a low-oxygen environment, which allows for the breakdown of cellulose and lignin into simpler molecules, ultimately producing a gas that can be used for energy generation or as a fuel for engines.”
Mark Johnson (Environmental Engineer, EcoSolutions Inc.). “The efficiency of wood gasification largely depends on the design of the gasifier and the type of feedstock used. Advanced gasifiers can achieve high conversion efficiencies, making them a viable option for sustainable energy production. However, understanding the moisture content and chemical composition of the wood is crucial for optimizing the gasification process.”
Linda Chen (Bioenergy Researcher, National Renewable Energy Laboratory). “One of the significant advantages of wood gasification is its ability to utilize waste biomass, reducing landfill contributions while producing renewable energy. Furthermore, the syngas produced can be further processed into biofuels or chemicals, highlighting the versatility of this technology in the transition towards a circular economy.”
Frequently Asked Questions (FAQs)
What is wood gasification?
Wood gasification is a thermochemical process that converts organic materials, such as wood, into a combustible gas known as syngas. This process occurs in a controlled environment with limited oxygen, allowing for the breakdown of biomass into simpler molecules.
How does the wood gasification process work?
The wood gasification process involves several stages: drying, pyrolysis, combustion, and reduction. Initially, moisture is removed from the wood. During pyrolysis, the wood decomposes into volatile gases and charcoal. The combustion stage partially burns the charcoal, producing heat, which facilitates the reduction of remaining materials into syngas.
What are the main components of wood gas?
Wood gas primarily consists of carbon monoxide (CO), hydrogen (H2), carbon dioxide (CO2), and methane (CH4). The exact composition can vary based on the type of wood used and the gasification conditions.
What are the advantages of wood gasification?
Wood gasification offers several advantages, including the ability to utilize renewable biomass resources, reduced greenhouse gas emissions compared to fossil fuels, and the production of syngas that can be used for electricity generation, heating, or as a fuel for vehicles.
What types of equipment are used in wood gasification?
Common equipment for wood gasification includes gasifiers, which can be fixed-bed, fluidized-bed, or entrained-flow types. Additional components may include scrubbers for gas cleaning, condensers for moisture removal, and engines or turbines for energy conversion.
Is wood gasification a sustainable energy solution?
Wood gasification can be considered a sustainable energy solution when sourced from sustainably managed forests. It provides a renewable energy source while promoting waste reduction and carbon neutrality, as the carbon released during combustion is offset by the carbon absorbed during the growth of the biomass.
Wood gasification is a thermochemical process that converts organic materials, such as wood, into a combustible gas known as syngas. This process involves heating the biomass in a low-oxygen environment, which prevents complete combustion and allows for the breakdown of the material into simpler molecules. The resulting syngas primarily consists of carbon monoxide, hydrogen, and small amounts of methane and other hydrocarbons, making it a versatile fuel that can be utilized for various energy applications.
The gasification process typically involves several stages: drying, pyrolysis, oxidation, and reduction. Initially, the wood is dried to remove moisture, followed by pyrolysis, where it decomposes into solid charcoal, liquid tar, and gaseous products. The oxidation phase introduces a limited amount of air or oxygen, which partially combusts the charcoal to generate heat. Finally, in the reduction phase, the remaining gases react with the char and steam to produce syngas. This multi-step process not only maximizes energy extraction from biomass but also minimizes harmful emissions compared to traditional combustion methods.
One of the key advantages of wood gasification is its ability to produce renewable energy from biomass, contributing to a more sustainable energy future. The syngas generated can be used directly for
Author Profile
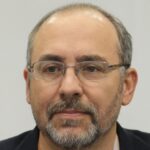
-
Darryl Norman is a seasoned entrepreneur and industry expert with a deep understanding of wood truss manufacturing and construction materials. As the President of Timberlake TrussWorks, LLC, Darryl played a pivotal role in shaping the company’s reputation for quality and precision. His leadership ensured that each truss met rigorous structural standards, providing builders with dependable components essential to their projects.
Beginning in 2025, Darryl Norman has shifted his focus to education and knowledge-sharing through an informative blog dedicated to wood truss manufacturing. Drawing from his extensive experience in the field, he provides in-depth insights into truss design, material selection, and construction techniques. This blog serves as a valuable resource for builders, contractors, and homeowners seeking practical guidance on truss systems and structural integrity.
Latest entries
- March 18, 2025General Wood TopicsWhat Color Is Ebony Wood? Unveiling the Rich Hues of This Luxurious Timber
- March 18, 2025Construction & FrameworkHow Can You Effectively Mount a Headboard to Your Wall?
- March 18, 2025General Wood TopicsCan Bees Really Eat Wood? Unraveling the Myths and Facts
- March 18, 2025General Wood TopicsDo Rabbits Really Chew on Wood? Exploring Their Eating Habits!