How Is Wood Veneer Made? Exploring the Process Behind This Versatile Material
Wood veneer, a thin layer of wood sliced from a log, is a remarkable material that combines beauty and functionality in the world of design and craftsmanship. From luxurious furniture to intricate cabinetry, veneer offers the rich aesthetic of solid wood while maximizing resources and minimizing waste. As sustainability becomes increasingly important in our choices, understanding how wood veneer is made reveals not only the artistry behind this material but also the innovative techniques that allow us to enjoy the warmth and character of wood in a more eco-friendly way.
The process of creating wood veneer is a blend of traditional craftsmanship and modern technology. It begins with selecting the right species of wood, where the unique grain patterns and colors are carefully considered. Once the logs are harvested, they undergo a series of steps that involve cutting, steaming, and slicing to produce the thin sheets that will ultimately be transformed into stunning surfaces. This meticulous approach ensures that each veneer retains the natural beauty of the wood while being versatile enough for various applications.
As we delve deeper into the intricacies of veneer production, we will explore the different methods used to slice the wood, the importance of grain matching, and the finishing techniques that enhance both the appearance and durability of the final product. By understanding how wood veneer is made, we can appreciate not just its aesthetic appeal, but also
Types of Wood Veneer
Wood veneer can be categorized based on various factors, including the method of production, thickness, and the type of wood used. Understanding these types can help in selecting the right veneer for specific applications.
- Natural Veneer: Sliced from logs, preserving the wood’s natural grain and color. This type is often used for high-end furniture and cabinetry.
- Reconstituted Veneer: Made from reconstituted wood fibers, dyed, and glued together to mimic the appearance of natural wood. This is a more sustainable option and provides consistent patterns.
- Backed Veneer: A layer of support material (such as paper or fabric) is added to the back of the veneer. This enhances stability and makes the veneer easier to handle.
Production Process of Wood Veneer
The production of wood veneer involves several key steps, each designed to ensure the final product meets quality and aesthetic standards.
- Log Selection: High-quality logs are chosen based on species, grain pattern, and overall integrity. The selected logs should be free of defects and disease.
- Debarking: The outer bark of the log is removed to prepare it for slicing. This step is crucial to ensure a clean surface for veneer production.
- Soaking or Steaming: Logs may be soaked or steamed to increase flexibility, allowing for smoother slicing and reducing the risk of cracking.
- Slicing: The log is sliced into thin sheets using one of several methods:
- Rotary Cutting: The log is rotated against a knife, producing a continuous sheet of veneer.
- Flat Slicing: The log is sliced flatly, creating a veneer that shows the grain pattern prominently.
- Quarter Slicing: The log is cut into quarters, resulting in a straight grain appearance.
- Drying: The sliced veneers are then dried to the desired moisture content, which helps prevent warping and enhances durability.
- Trimming and Grading: Each sheet is trimmed to size and graded based on quality, color, and grain pattern, ensuring uniformity in the final product.
Applications of Wood Veneer
Wood veneer is versatile and used in various applications across different industries. Its aesthetic appeal, combined with a cost-effective profile, makes it a popular choice.
Application | Description |
---|---|
Furniture | Used in tabletops, cabinets, and decorative elements. |
Wall Panels | Provides an elegant finish for interior walls. |
Doors | Veneered doors offer a high-end look at a lower cost. |
Musical Instruments | Often used for pianos and guitars for aesthetic appeal. |
Crafts | Ideal for model making and artistic projects. |
the production and application of wood veneer showcase its significance in design and craftsmanship, providing both functionality and beauty in a range of products.
Wood Veneer Production Process
The manufacturing of wood veneer involves several systematic steps that transform logs into thin sheets of wood, suitable for various applications in furniture, cabinetry, and decorative surfaces. The primary methods for producing wood veneer include slicing, peeling, and sawing.
Log Preparation
Before the veneer can be produced, logs undergo rigorous preparation processes:
- Selection: High-quality logs are chosen based on species, grain pattern, and overall quality.
- Debarking: The outer bark is removed to expose the wood underneath.
- Soaking or Steaming: Logs may be soaked in hot water or steamed to make the wood more pliable, preventing splits during the slicing or peeling process.
Slicing Techniques
There are three main slicing techniques utilized in wood veneer production:
- Flat Slicing (Plain Slicing):
- The log is cut parallel to the growth rings.
- Produces a cathedral grain pattern.
- Quarter Slicing:
- The log is cut perpendicular to the growth rings.
- Results in a straight grain appearance, ideal for high-end applications.
- Rotary Peeling:
- The log is mounted on a lathe and rotated against a knife.
- This method produces a continuous sheet of veneer, typically used for plywood and lower-cost applications.
Slicing Method | Grain Pattern | Common Uses |
---|---|---|
Flat Slicing | Cathedral grain | Furniture, cabinetry |
Quarter Slicing | Straight grain | High-end veneers |
Rotary Peeling | Varied patterns | Plywood, low-cost uses |
Drying Process
After slicing, the veneer sheets must be dried to achieve the correct moisture content:
- Kiln Drying: Veneers are placed in a kiln to remove moisture rapidly and uniformly.
- Air Drying: Alternatively, veneers may be air-dried for a more gradual moisture reduction, though this method takes longer.
The drying process is crucial as it prevents warping, splitting, or mold growth.
Trimming and Grading
Once dried, the veneer sheets are trimmed and graded:
- Trimming: Edges are cut to ensure uniform size and eliminate defects.
- Grading: Veneers are classified based on aesthetic quality, grain pattern, color consistency, and the presence of imperfections.
Graded veneers are then sorted for different markets, ensuring the right quality reaches the intended application.
Finishing Touches
The final stage involves applying finishes to the veneer:
- Sanding: Light sanding smooths the surface for a uniform finish.
- Coating: Various finishes, such as varnish, lacquer, or oil, can be applied to enhance appearance and durability.
This stage not only enhances the aesthetic appeal but also protects the veneer from environmental damage.
Applications of Wood Veneer
Wood veneer serves a multitude of purposes across different industries:
- Furniture: Used in tabletops, cabinets, and seating.
- Interior Design: Applied in wall panels, doors, and decorative elements.
- Musical Instruments: Often used in the construction of pianos and guitars for aesthetic and tonal qualities.
- Architectural Features: Incorporated in high-end commercial and residential spaces for elegant finishing touches.
By understanding the detailed process of wood veneer production, one can appreciate the craftsmanship and technology that go into creating these versatile materials.
Understanding the Process of Wood Veneer Production
Dr. Emily Carter (Wood Technology Specialist, Timber Innovations Institute). “The production of wood veneer involves a meticulous process where logs are carefully selected based on species and quality. The logs are then debarked and subjected to either rotary peeling or slicing, methods that significantly influence the veneer’s grain pattern and thickness.”
James Thompson (Senior Furniture Designer, Artisan Woodworks). “In my experience, the craftsmanship involved in veneer production is crucial. Each sheet of veneer must be dried to the appropriate moisture content to prevent warping, and the finishing process is equally important to enhance the natural beauty of the wood.”
Linda Martinez (Sustainable Forestry Consultant, EcoWood Alliance). “Sustainability plays a vital role in veneer production. Ethical sourcing of timber and the use of environmentally friendly adhesives are essential practices that not only preserve forests but also ensure that the veneer industry can thrive without compromising ecological integrity.”
Frequently Asked Questions (FAQs)
What is wood veneer?
Wood veneer is a thin layer or slice of wood, typically less than 3mm thick, that is adhered to core panels (like wood, particle board, or medium-density fiberboard) to produce flat panels such as doors, tops, and panels for cabinets, parquet floors, and parts of furniture.
How is wood veneer made?
Wood veneer is made by slicing or peeling logs into thin sheets. The process involves debarking the log, then using specialized machinery to cut the wood into sheets either through rotary peeling, slicing, or sawing techniques, depending on the desired grain pattern and thickness.
What types of wood are commonly used for veneers?
Common types of wood used for veneers include oak, maple, cherry, walnut, and mahogany. Exotic woods such as teak, rosewood, and bamboo are also popular for their unique appearances and characteristics.
What are the benefits of using wood veneer?
Wood veneer offers several benefits, including cost-effectiveness compared to solid wood, a wide variety of grain patterns and colors, and sustainability as it allows for the use of less wood while still achieving a high-quality appearance.
How is wood veneer applied to surfaces?
Wood veneer is typically applied using adhesives. The veneer is cut to size, coated with glue, and then pressed onto the substrate using a veneer press to ensure a strong bond. The process may involve heat and pressure to enhance adhesion.
Can wood veneer be refinished or repaired?
Yes, wood veneer can be refinished or repaired, although the process is more delicate than with solid wood. Minor scratches and dents can often be sanded out, while larger damages may require patching or replacing sections of veneer.
Wood veneer is a thin layer of wood that is sliced or peeled from a log, primarily used in furniture, cabinetry, and decorative applications. The production of wood veneer involves several key steps, starting with the selection of high-quality logs. These logs are then processed through methods such as rotary cutting, flat slicing, or quarter slicing, each yielding different grain patterns and appearances. After the initial cutting, the veneer sheets are dried to the appropriate moisture content, ensuring stability and preventing warping.
Once dried, the veneer can be further treated or finished according to the desired application. This may include sanding, staining, or applying protective coatings. The versatility of wood veneer allows it to mimic the appearance of solid wood while being more cost-effective and environmentally friendly. Additionally, the use of veneer can significantly reduce the amount of wood required, promoting sustainable practices in the woodworking industry.
In summary, the process of making wood veneer is a meticulous one that emphasizes quality and craftsmanship. By understanding the methods involved in its production, one can appreciate the aesthetic and functional benefits that wood veneer offers. It serves as an excellent alternative to solid wood, providing beauty and durability while supporting sustainable resource management.
Author Profile
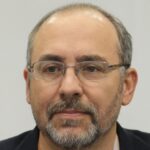
-
Darryl Norman is a seasoned entrepreneur and industry expert with a deep understanding of wood truss manufacturing and construction materials. As the President of Timberlake TrussWorks, LLC, Darryl played a pivotal role in shaping the company’s reputation for quality and precision. His leadership ensured that each truss met rigorous structural standards, providing builders with dependable components essential to their projects.
Beginning in 2025, Darryl Norman has shifted his focus to education and knowledge-sharing through an informative blog dedicated to wood truss manufacturing. Drawing from his extensive experience in the field, he provides in-depth insights into truss design, material selection, and construction techniques. This blog serves as a valuable resource for builders, contractors, and homeowners seeking practical guidance on truss systems and structural integrity.
Latest entries
- March 18, 2025General Wood TopicsWhat Color Is Ebony Wood? Unveiling the Rich Hues of This Luxurious Timber
- March 18, 2025Construction & FrameworkHow Can You Effectively Mount a Headboard to Your Wall?
- March 18, 2025General Wood TopicsCan Bees Really Eat Wood? Unraveling the Myths and Facts
- March 18, 2025General Wood TopicsDo Rabbits Really Chew on Wood? Exploring Their Eating Habits!