How Long Does It Really Take to Dry Wood in a Kiln?
When it comes to woodworking, the quality of the final product often hinges on one crucial factor: moisture content. For artisans, builders, and hobbyists alike, understanding how long to dry wood in a kiln is essential for achieving optimal results. Kiln drying not only enhances the wood’s durability and stability but also minimizes the risk of warping, cracking, and other issues that can arise from improper moisture levels. As the demand for high-quality lumber continues to rise, mastering the kiln drying process has become more important than ever.
Kiln drying is a controlled process that accelerates the natural drying of wood, allowing it to reach the desired moisture content efficiently. The duration of this process can vary significantly based on several factors, including the type of wood, its initial moisture content, and the specific drying conditions employed in the kiln. Understanding these variables is crucial for anyone looking to optimize their drying time and produce top-notch lumber.
In this article, we will explore the intricacies of kiln drying, including the science behind moisture removal and the best practices for achieving consistent results. Whether you are a seasoned woodworker or just starting your journey, knowing how long to dry wood in a kiln will empower you to make informed decisions that enhance your craftsmanship and the longevity of your projects. Get ready to
Factors Affecting Drying Time
The time required to dry wood in a kiln can vary significantly based on several factors. Understanding these factors can help ensure optimal drying conditions and product quality.
- Type of Wood: Different species of wood have varying densities and moisture contents, which influence drying times. For instance, hardwoods like oak generally take longer to dry than softwoods like pine.
- Initial Moisture Content: The starting moisture content of the wood will directly affect drying duration. Wood with a high moisture content will require more time to reach the desired equilibrium moisture content (EMC).
- Kiln Temperature and Humidity: The temperature and humidity levels inside the kiln play critical roles in the drying process. Higher temperatures can accelerate drying but may also lead to defects if not managed properly.
- Airflow: Adequate airflow within the kiln is essential for effective moisture removal. Insufficient airflow can lead to uneven drying and increased drying times.
- Thickness of the Wood: Thicker pieces of wood will take longer to dry than thinner pieces. It is essential to consider the dimensions when estimating drying times.
Typical Drying Times
The following table provides a general overview of drying times for various wood species based on their moisture content and thickness.
Wood Species | Moisture Content (%) | Thickness (inches) | Approx. Drying Time (days) |
---|---|---|---|
Pine | 30-60 | 1 | 5-7 |
Oak | 30-60 | 1 | 10-14 |
Maple | 30-60 | 1 | 7-10 |
Cedar | 30-60 | 1 | 5-8 |
This table serves as a guideline, and actual drying times may vary based on the kiln’s specific conditions and the wood’s characteristics.
Monitoring the Drying Process
Monitoring the drying process is crucial to achieving the desired moisture content without damaging the wood. Key practices include:
- Using Moisture Meters: These devices can help track the moisture level in the wood throughout the drying process, ensuring optimal moisture removal.
- Regular Inspections: Frequent checks of the kiln environment and wood condition can help identify any issues early, allowing for adjustments in temperature, humidity, or airflow.
- Adjusting Drying Schedule: Based on ongoing assessments, it may be necessary to modify the drying schedule to prevent defects such as checking, warping, or splitting.
By understanding the various factors that influence drying times and implementing effective monitoring practices, one can optimize the kiln drying process for improved results.
Factors Influencing Drying Time
The duration required to dry wood in a kiln can vary significantly based on several key factors. Understanding these variables is essential for optimizing the drying process.
- Wood Species: Different species of wood have varying moisture content and density, affecting drying times. For example:
- Hardwoods (e.g., oak, maple) typically take longer to dry than softwoods (e.g., pine, fir).
- Initial Moisture Content: The starting moisture content of the wood plays a crucial role. Higher moisture content results in longer drying times:
- Freshly cut green wood (over 50% moisture) can take several weeks to dry.
- Kiln-dried wood (around 8-12% moisture) may require less time.
- Kiln Temperature and Humidity: The operating conditions of the kiln are critical. Higher temperatures generally speed up drying, but excessive heat can cause defects like cracking:
- Typical kiln temperatures range from 120°F to 180°F (49°C to 82°C).
- Humidity levels should be controlled to avoid condensation, which can lead to uneven drying.
- Airflow: Adequate airflow within the kiln facilitates moisture removal, impacting drying efficiency:
- Air circulation should be uniform to ensure consistent drying across all pieces of wood.
Typical Drying Times
While the exact drying time can vary based on the factors mentioned, general guidelines can provide a framework for expectations. Below is a table outlining approximate drying times for various wood types under optimal kiln conditions.
Wood Type | Initial Moisture Content | Approximate Drying Time |
---|---|---|
Softwoods (e.g., Pine, Cedar) | 50%+ | 1-2 weeks |
Hardwoods (e.g., Oak, Maple) | 50%+ | 2-4 weeks |
Exotic Hardwoods (e.g., Teak, Mahogany) | 50%+ | 3-6 weeks |
Reclaimed Wood | Varies | 4-8 weeks |
Monitoring the Drying Process
To ensure optimal results during the drying process, monitoring is essential. Here are some techniques:
- Moisture Meters: Utilize moisture meters to track the moisture content of the wood throughout the drying process. This allows for adjustments in kiln conditions if necessary.
- Visual Inspections: Regularly inspect the wood for signs of over-drying or defects, such as checking for cracks or warping.
- Record Keeping: Maintain detailed records of temperature, humidity, and moisture content changes. This data can help refine future drying processes.
Post-Drying Considerations
After the drying process, certain steps should be taken to ensure the quality of the wood:
- Conditioning: Gradually acclimate the wood to room temperature and humidity levels to minimize stress and prevent cracking.
- Storage: Store the dried wood in a controlled environment to maintain its moisture content and prevent reabsorption of moisture from the air.
- Quality Testing: Conduct quality tests on the dried wood to ensure it meets the required specifications for strength and usability.
Understanding Kiln Drying Times from Industry Professionals
Dr. Emily Carter (Wood Science Researcher, Timber Innovations Institute). “The drying time for wood in a kiln can vary significantly based on the species of wood, initial moisture content, and the specific drying schedule employed. Generally, it takes anywhere from 24 hours to several days to achieve optimal moisture levels, with hardwoods typically requiring longer than softwoods.”
Mark Thompson (Kiln Operations Manager, GreenWood Lumber Co.). “In our operations, we find that a standard drying cycle for most species of lumber is about 5 to 7 days. However, factors such as the thickness of the wood and the desired final moisture content can extend this period. Monitoring humidity and temperature is crucial for efficient drying.”
Lisa Chen (Woodworking Expert and Author, Fine Woodworking Magazine). “For those new to kiln drying, it is essential to understand that while the process can be expedited, rushing it may lead to defects like warping or cracking. A well-managed kiln drying process should ideally take between 1 to 2 weeks, depending on the wood type and thickness.”
Frequently Asked Questions (FAQs)
How long does it typically take to dry wood in a kiln?
The drying time for wood in a kiln generally ranges from a few days to several weeks, depending on the type of wood, its initial moisture content, and the specific drying schedule employed.
What factors affect the drying time of wood in a kiln?
Several factors influence drying time, including wood species, thickness, initial moisture content, kiln temperature, humidity levels, and airflow within the kiln.
Can all types of wood be dried in a kiln?
Most types of wood can be dried in a kiln; however, some species may require specific drying protocols to prevent defects such as warping or cracking.
What is the ideal temperature for drying wood in a kiln?
The ideal temperature for drying wood in a kiln typically ranges from 120°F to 180°F (49°C to 82°C), depending on the wood species and desired moisture content.
How can I tell when the wood is properly dried?
Properly dried wood should have a moisture content of around 6% to 8% for most applications. A moisture meter can be used to accurately measure the moisture content.
What are the advantages of kiln drying wood compared to air drying?
Kiln drying offers several advantages, including faster drying times, reduced risk of insect infestation and mold growth, and improved dimensional stability and strength of the wood.
In summary, the duration required to dry wood in a kiln can vary significantly based on several factors, including the type of wood, its initial moisture content, the desired final moisture level, and the specific kiln technology being utilized. Generally, the drying process can take anywhere from a few days to several weeks. Hardwoods typically require longer drying times compared to softwoods due to their denser structure. Additionally, thicker pieces of wood will also take longer to dry than thinner ones.
It is essential to monitor the drying process closely to avoid issues such as warping, cracking, or checking, which can occur if the wood dries too quickly. Effective kiln drying involves balancing temperature, humidity, and air circulation to achieve optimal results. Understanding the specific requirements of the wood species being dried can lead to more efficient drying times and better quality end products.
Key takeaways include the importance of selecting the right drying schedule based on wood species and thickness, as well as the need for careful management of kiln conditions. By adhering to best practices in kiln drying, woodworkers and manufacturers can ensure that their wood is properly dried, leading to improved performance and longevity in various applications.
Author Profile
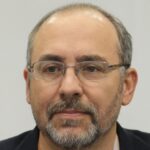
-
Darryl Norman is a seasoned entrepreneur and industry expert with a deep understanding of wood truss manufacturing and construction materials. As the President of Timberlake TrussWorks, LLC, Darryl played a pivotal role in shaping the company’s reputation for quality and precision. His leadership ensured that each truss met rigorous structural standards, providing builders with dependable components essential to their projects.
Beginning in 2025, Darryl Norman has shifted his focus to education and knowledge-sharing through an informative blog dedicated to wood truss manufacturing. Drawing from his extensive experience in the field, he provides in-depth insights into truss design, material selection, and construction techniques. This blog serves as a valuable resource for builders, contractors, and homeowners seeking practical guidance on truss systems and structural integrity.
Latest entries
- March 18, 2025General Wood TopicsWhat Color Is Ebony Wood? Unveiling the Rich Hues of This Luxurious Timber
- March 18, 2025Construction & FrameworkHow Can You Effectively Mount a Headboard to Your Wall?
- March 18, 2025General Wood TopicsCan Bees Really Eat Wood? Unraveling the Myths and Facts
- March 18, 2025General Wood TopicsDo Rabbits Really Chew on Wood? Exploring Their Eating Habits!