How Long Does It Really Take to Kiln Dry Wood?
Kiln drying wood is a crucial step in the woodworking and construction industries, ensuring that lumber is not only aesthetically pleasing but also structurally sound. As the demand for high-quality, durable wood continues to rise, understanding the intricacies of the kiln drying process becomes increasingly important for both hobbyists and professionals alike. But how long does it actually take to kiln dry wood? This question is not just a matter of time; it involves a myriad of factors including wood species, moisture content, and the specific drying methods employed.
In essence, kiln drying is a controlled process that removes moisture from freshly cut wood, enhancing its stability and preventing issues such as warping, cracking, and fungal growth. The duration of this process can vary significantly depending on several variables. For instance, denser species of wood typically require longer drying times compared to lighter varieties. Additionally, the initial moisture content of the wood plays a pivotal role; logs with higher moisture levels will naturally take longer to reach the desired dryness.
As we delve deeper into the specifics of kiln drying, we will explore the various factors that influence drying times, the different types of kilns used, and best practices for achieving optimal results. Whether you’re a seasoned woodworker or just starting out, understanding the nuances of kiln drying will empower
Factors Influencing Kiln Drying Time
The time required to kiln dry wood can vary significantly based on several factors. Understanding these variables is crucial for achieving optimal drying results. The primary factors include:
- Wood Species: Different species have varying densities and moisture content levels, which can affect drying time. For instance, hardwoods like oak may take longer to dry than softwoods like pine.
- Initial Moisture Content: The starting moisture level of the wood directly influences the drying duration. Higher moisture content requires more time to reach the desired equilibrium.
- Kiln Type and Efficiency: The design and efficiency of the kiln play an essential role. Modern, high-efficiency kilns can reduce drying times significantly compared to older models.
- Temperature and Humidity Levels: The temperature and humidity inside the kiln are critical parameters. Higher temperatures generally accelerate drying but may lead to defects if not managed properly.
- Airflow: Adequate airflow within the kiln ensures even drying and minimizes the risk of checking and warping.
Typical Drying Times for Common Wood Species
The following table summarizes the average kiln drying times for various wood species, assuming a standard initial moisture content of around 30%:
Wood Species | Average Drying Time (Days) |
---|---|
Pine | 5-7 |
Spruce | 5-8 |
Oak | 7-14 |
Maple | 7-12 |
Cherry | 8-12 |
Walnut | 10-14 |
Stages of Kiln Drying Process
The kiln drying process typically consists of several stages, each designed to gradually reduce the wood’s moisture content while minimizing defects. The stages include:
- Heating Phase: The kiln is heated to a specific temperature to increase the wood’s internal temperature, which facilitates moisture evaporation.
- Drying Phase: During this phase, the wood loses moisture to the surrounding air. The temperature and humidity levels are carefully monitored and adjusted to optimize the drying process.
- Equalization Phase: Once the wood reaches a certain moisture level, the kiln’s environment is adjusted to equalize the moisture content throughout the wood pieces. This helps to prevent internal stresses that could lead to warping or cracking.
- Conditioning Phase: In the final stage, the wood is conditioned to stabilize its moisture content before removal from the kiln. This may involve introducing humidity to prevent rapid drying out, which can lead to defects.
Understanding these stages and the factors affecting them can lead to more effective kiln drying practices, ensuring high-quality results.
Factors Influencing Kiln Drying Time
The duration required to kiln dry wood is contingent on several critical factors, including:
- Wood Species: Different species have varying moisture content and density, influencing the drying rate. For instance, hardwoods like oak may take longer to dry than softer woods such as pine.
- Initial Moisture Content: The starting moisture content of the wood significantly impacts drying time. Wood that has just been harvested will typically contain more moisture than seasoned wood.
- Kiln Temperature and Humidity: Higher temperatures can accelerate drying, while humidity levels in the kiln must be controlled to prevent surface checking or warping.
- Airflow and Circulation: Proper airflow is essential for effective drying. Insufficient circulation can lead to uneven drying and extended time frames.
Typical Drying Times by Wood Type
The following table outlines approximate kiln drying times based on wood species and initial moisture content:
Wood Species | Initial Moisture Content (%) | Approximate Drying Time (Days) |
---|---|---|
Pine | 30-60 | 5-10 |
Oak | 30-60 | 10-20 |
Maple | 30-60 | 10-15 |
Cherry | 30-60 | 8-12 |
Walnut | 30-60 | 12-18 |
Monitoring the Drying Process
To ensure effective kiln drying, continuous monitoring is essential. Key methods include:
- Moisture Meters: Utilize moisture meters to check the moisture content of the wood periodically throughout the drying process.
- Temperature Sensors: Implement temperature sensors to maintain optimal kiln conditions and ensure uniform drying.
- Visual Inspections: Regularly inspect the wood for signs of checking, warping, or discoloration, which may indicate issues with the drying process.
Best Practices for Kiln Drying
Employing best practices can enhance the efficiency of kiln drying:
- Pre-Conditioning: Pre-condition wood before placing it in the kiln to reduce stress and minimize drying defects.
- Stacking: Properly stack wood to allow for maximum airflow and uniform exposure to heat and humidity.
- Gradual Drying: Gradually increase the kiln temperature during the drying cycle to prevent thermal shock.
- Adjusting Humidity: Maintain appropriate humidity levels throughout the drying process to avoid surface defects.
By considering these factors, one can achieve effective and efficient kiln drying, ensuring the quality and integrity of the wood.
Expert Insights on Kiln Drying Wood Duration
Dr. Emily Carter (Wood Science Specialist, Timber Research Institute). The duration for kiln drying wood typically ranges from 24 to 72 hours, depending on the species and initial moisture content. Factors such as the thickness of the lumber and the specific kiln technology used can significantly influence this timeframe.
Mark Thompson (Master Carpenter, Fine Woodworking Magazine). In my experience, achieving optimal dryness can take anywhere from a few days to a week. It is crucial to monitor the moisture levels throughout the process to prevent defects like warping or cracking.
Linda Garcia (Kiln Operations Manager, National Lumber Association). The average kiln drying cycle for hardwoods is approximately 5 to 10 days, while softwoods may require less time. However, the key is to ensure that the wood reaches the desired moisture content of around 6-8% for effective use in construction and furniture making.
Frequently Asked Questions (FAQs)
How long does it typically take to kiln dry wood?
The duration for kiln drying wood generally ranges from a few days to several weeks, depending on the wood species, initial moisture content, and the specific drying schedule employed.
What factors influence the kiln drying time of wood?
Key factors include the type of wood, thickness of the lumber, initial moisture content, kiln temperature, humidity levels, and airflow within the kiln.
Can all types of wood be kiln dried?
Most types of wood can be kiln dried; however, certain species may require specialized drying processes to avoid issues such as warping or cracking.
Is there a difference in drying time between hardwood and softwood?
Yes, hardwoods typically take longer to dry than softwoods due to their denser structure and higher moisture content.
How can I tell if wood is properly kiln dried?
Properly kiln dried wood should have a moisture content between 6% and 8%. A moisture meter can be used to accurately measure this.
What are the consequences of over-drying wood in a kiln?
Over-drying wood can lead to significant issues such as increased brittleness, warping, and the potential for surface checking, which can compromise the wood’s structural integrity.
Kiln drying wood is a critical process that significantly influences the quality and usability of lumber. The duration required for kiln drying wood can vary based on several factors, including the type of wood, the initial moisture content, the desired final moisture content, and the specific kiln drying method employed. Generally, the process can take anywhere from a few hours to several days, with softwoods typically drying faster than hardwoods due to their lower density and moisture content.
Understanding the moisture content is essential for effective kiln drying. Wood is usually dried to a moisture content between 6% to 8% for most applications, particularly in furniture making and construction. The initial moisture content of the wood, which can range from 20% to over 100% in freshly cut logs, plays a significant role in determining the overall drying time. Additionally, the efficiency of the kiln and the drying schedule also influence how quickly the wood reaches the desired moisture level.
It is also important to consider the potential effects of improper drying. Over-drying can lead to warping and cracking, while under-drying can result in mold growth and reduced strength. Therefore, monitoring the drying process closely and adjusting conditions as needed is vital for achieving optimal results. Ultimately, the
Author Profile
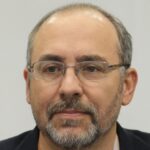
-
Darryl Norman is a seasoned entrepreneur and industry expert with a deep understanding of wood truss manufacturing and construction materials. As the President of Timberlake TrussWorks, LLC, Darryl played a pivotal role in shaping the company’s reputation for quality and precision. His leadership ensured that each truss met rigorous structural standards, providing builders with dependable components essential to their projects.
Beginning in 2025, Darryl Norman has shifted his focus to education and knowledge-sharing through an informative blog dedicated to wood truss manufacturing. Drawing from his extensive experience in the field, he provides in-depth insights into truss design, material selection, and construction techniques. This blog serves as a valuable resource for builders, contractors, and homeowners seeking practical guidance on truss systems and structural integrity.
Latest entries
- March 18, 2025General Wood TopicsWhat Color Is Ebony Wood? Unveiling the Rich Hues of This Luxurious Timber
- March 18, 2025Construction & FrameworkHow Can You Effectively Mount a Headboard to Your Wall?
- March 18, 2025General Wood TopicsCan Bees Really Eat Wood? Unraveling the Myths and Facts
- March 18, 2025General Wood TopicsDo Rabbits Really Chew on Wood? Exploring Their Eating Habits!