How Can You Build Your Own CNC Wood Router?
In the realm of woodworking, the advent of CNC (Computer Numerical Control) technology has revolutionized the way artisans approach their craft. Imagine transforming your creative visions into tangible masterpieces with precision and ease. Building a CNC wood router not only empowers you with the ability to create intricate designs and patterns but also enhances your woodworking capabilities, allowing for greater efficiency and accuracy. Whether you’re a hobbyist looking to elevate your projects or a seasoned woodworker aiming to streamline your workflow, constructing your own CNC wood router can be a rewarding and fulfilling endeavor.
Creating a CNC wood router involves a blend of mechanical engineering, electronics, and software programming. At its core, a CNC router is a machine that uses computer-controlled movements to carve, cut, and shape wood into desired forms. The journey to build one begins with understanding the essential components, such as the frame, motors, and control systems, which work in harmony to bring your designs to life. With the right materials and a bit of know-how, you can craft a machine tailored to your specific needs, whether for intricate carvings or large-scale projects.
As you embark on this exciting project, you’ll discover the importance of planning and precision in every step of the construction process. From selecting the right tools to configuring the software
Choosing the Right Components
Selecting the appropriate components is crucial for building a CNC wood router that meets your needs. The primary components include the frame, motors, control system, and cutting tools.
- Frame: Typically constructed from aluminum extrusions or steel, the frame must be sturdy to handle the vibrations during operation.
- Motors: Stepper motors are commonly used due to their precision and reliability. Consider NEMA 17 or NEMA 23 sizes depending on your desired torque and speed.
- Control System: Options include Arduino-based systems or dedicated CNC controllers like GRBL or Mach3. Each has its pros and cons in terms of complexity and functionality.
- Cutting Tools: Choose a router or spindle suitable for wood. A 1/4″ or 1/2″ router bit is often effective for various projects.
Building the Frame
The frame serves as the foundation for your CNC router. Follow these steps to construct it effectively:
- Measure and Cut Materials: Use a saw to cut your aluminum extrusions or steel to the desired lengths based on your design.
- Assemble the Base: Create a rectangular base, ensuring it is square and stable. Use corner brackets and screws for reinforcement.
- Add Vertical Supports: Attach vertical supports to the corners of the base. This will hold the gantry and other moving parts.
- Install the Gantry: The gantry must be able to move smoothly along the X-axis. Use linear rails for better precision.
Installing the Motors and Electronics
Once the frame is complete, the next step involves the installation of motors and electronics.
- Mount Motors: Secure the stepper motors to the frame using brackets. Ensure they are aligned correctly to avoid misalignment during operation.
- Wiring: Connect the motors to the control board. Ensure that the connections are secure and that the wiring is neatly organized to prevent interference.
- Power Supply: Choose a power supply that can provide adequate voltage and current for your motors, typically between 12V and 36V depending on your setup.
Component | Specifications | Notes |
---|---|---|
Frame Material | Aluminum Extrusion / Steel | Choose based on weight and stability |
Stepper Motor | NEMA 17 / NEMA 23 | Torque requirements may vary |
Control System | Arduino / GRBL / Mach3 | Complexity vs. functionality |
Power Supply | 12V – 36V | Ensure it meets motor requirements |
Setting Up the Software
Software is essential for controlling your CNC wood router. Choose a suitable software solution for both design and operation.
- CAD Software: Programs like Fusion 360 or SketchUp are great for creating designs.
- CAM Software: Use software like Easel or VCarve to generate the G-code necessary for your CNC router.
- Control Software: Upload the G-code to your control system. Test the movements in air (without cutting material) to confirm accuracy.
Testing and Calibration
Calibration ensures that your CNC wood router operates correctly. Follow these steps:
- Initial Test: Run the machine without any load. Check for smooth movement across all axes.
- Check Dimensions: Use calipers to measure the output dimensions of a simple cut. Adjust steps per mm in your firmware settings if necessary.
- Final Adjustments: Make any necessary adjustments to the motor settings or bed alignment to ensure precision in your cuts.
Understanding CNC Wood Router Components
To build an effective CNC wood router, it is crucial to understand its primary components. Each part plays a significant role in the overall functionality and precision of the machine.
- Frame: The structure that supports all components, typically made from aluminum or steel for rigidity.
- Linear Motion System: Includes rails and bearings that allow smooth movement of the router along the designated axes.
- Stepper Motors: Provide the necessary torque to drive the axes, enabling precise positioning and movement.
- Router Spindle: The cutting tool that removes material from the wood; typically high-speed and variable for different materials.
- Control System: The brain of the CNC router, often a combination of software and hardware that interprets design files and directs the motors accordingly.
- Power Supply: Supplies the necessary power to the motors and spindle, usually requiring careful selection based on the motor specifications.
Designing the CNC Router
A well-planned design is essential for a successful CNC wood router build. Consider the following design elements:
- Size and Workspace: Determine the dimensions based on the projects you intend to undertake. Common sizes vary from 24” x 24” to larger formats.
- Axis Configuration: Most routers operate in three axes (X, Y, Z). You can opt for a Cartesian design or a more complex arrangement like a delta configuration.
- Material Selection: Choose materials that balance weight and strength; options include plywood for the frame and aluminum for structural parts.
Component | Material Options | Notes |
---|---|---|
Frame | Aluminum, Steel, Plywood | Aluminum offers strength; plywood is cost-effective. |
Rails and Bearings | Steel, Linear Rail Systems | Linear rail systems provide smoother movement. |
Spindle | High-Speed Router | Choose based on desired cutting capabilities. |
Assembling the CNC Router
The assembly process requires precision and attention to detail. Follow these steps:
- Build the Frame: Assemble the base using your chosen materials, ensuring all joints are secure and stable.
- Install the Linear Motion System: Attach the rails to the frame, aligning them perfectly to facilitate smooth movement.
- Mount the Stepper Motors: Secure the motors to their designated locations on the frame, ensuring they are properly aligned with the linear rails.
- Attach the Router Spindle: Install the spindle on the Z-axis, confirming that it is level and secure.
- Set Up the Control System: Connect the control board to the stepper motors and spindle. Install the necessary software on your computer.
Wiring and Electronics
Proper wiring is essential for the functionality of your CNC wood router. Ensure the following:
- Power Connections: Connect the power supply to the control board and spindle, ensuring all connections are insulated and secure.
- Motor Connections: Wire the stepper motors to the control board, following the manufacturer’s specifications for color coding.
- Limit Switches: Install limit switches on each axis to prevent over-travel and potential damage.
Calibration and Testing
Calibration is critical for achieving accuracy in your CNC router.
- Home the Axes: Use the limit switches to establish the home position for each axis.
- Test Movement: Command each axis to move a predetermined distance, verifying that the movement corresponds accurately.
- Cutting Test: Perform a test cut on a scrap piece of wood to check the router’s performance and adjust settings as necessary.
By following these steps and understanding the core components involved, you will be well on your way to successfully building a CNC wood router tailored to your specific needs.
Expert Insights on Building a CNC Wood Router
John Mitchell (Mechanical Engineer, Precision Woodworking Solutions). “When building a CNC wood router, the choice of materials is crucial. Opt for high-quality aluminum extrusions for the frame to ensure rigidity and stability during operation. Additionally, consider using a solid MDF or plywood base to absorb vibrations and enhance precision.”
Linda Chen (CNC Programming Specialist, TechCraft Innovations). “Programming your CNC wood router effectively is just as important as the hardware itself. I recommend using software like Fusion 360 or VCarve for designing and generating toolpaths. Familiarize yourself with G-code, as it will allow you to optimize the performance of your machine.”
David Thompson (Woodworking Instructor, Artisan Academy). “Safety should always be a top priority when building and operating a CNC wood router. Implement emergency stop buttons and ensure that all moving parts are properly shielded. Regular maintenance checks will also help prevent accidents and prolong the life of your router.”
Frequently Asked Questions (FAQs)
What materials are needed to build a CNC wood router?
To build a CNC wood router, you will need materials such as aluminum extrusions or steel for the frame, stepper motors, a control board, lead screws or belts for movement, a router or spindle, and various electronic components like limit switches and wiring.
How much does it cost to build a CNC wood router?
The cost of building a CNC wood router can vary widely depending on the size and specifications. A basic setup can range from $500 to $2,000, while more advanced configurations may exceed $5,000.
What software is required for operating a CNC wood router?
You will need CAD (Computer-Aided Design) software to create designs and CAM (Computer-Aided Manufacturing) software to generate G-code for the CNC machine. Popular options include Fusion 360, Inkscape, and Mach3.
What are the key components of a CNC wood router?
The key components include the frame, motion system (stepper motors and lead screws), control electronics (controller and power supply), the cutting tool (router or spindle), and the software for design and operation.
How do I calibrate my CNC wood router?
Calibration involves setting the steps per millimeter for the motors, ensuring the machine moves accurately according to the design specifications. This can be done using test cuts and adjusting the settings in the control software accordingly.
Can I build a CNC wood router at home?
Yes, you can build a CNC wood router at home. Many hobbyists and professionals create their own machines using readily available materials and components, following detailed plans and guides available online.
Building a CNC wood router involves a series of methodical steps that require careful planning and execution. The process typically begins with selecting the right materials and components, including the frame, motors, and control systems. Understanding the specifications and capabilities of each component is crucial for ensuring that the final machine meets your intended woodworking needs. Additionally, proper assembly techniques and adherence to safety protocols are essential for creating a reliable and efficient CNC router.
Once the physical structure is established, attention must shift to the software aspect, which includes selecting appropriate CAD/CAM software for designing and executing projects. Familiarity with the software is vital for maximizing the router’s potential and achieving precise cuts. Calibration and testing of the machine are also critical steps, as they ensure accuracy and functionality before embarking on actual woodworking tasks.
In summary, building a CNC wood router is a rewarding project that combines mechanical engineering with digital design. It requires a comprehensive understanding of both hardware and software, as well as a commitment to precision and safety. By following a structured approach and leveraging available resources, enthusiasts can create a powerful tool that enhances their woodworking capabilities.
Key takeaways include the importance of selecting high-quality components, mastering the necessary software, and prioritizing safety throughout the building
Author Profile
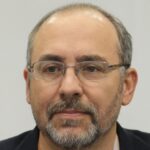
-
Darryl Norman is a seasoned entrepreneur and industry expert with a deep understanding of wood truss manufacturing and construction materials. As the President of Timberlake TrussWorks, LLC, Darryl played a pivotal role in shaping the company’s reputation for quality and precision. His leadership ensured that each truss met rigorous structural standards, providing builders with dependable components essential to their projects.
Beginning in 2025, Darryl Norman has shifted his focus to education and knowledge-sharing through an informative blog dedicated to wood truss manufacturing. Drawing from his extensive experience in the field, he provides in-depth insights into truss design, material selection, and construction techniques. This blog serves as a valuable resource for builders, contractors, and homeowners seeking practical guidance on truss systems and structural integrity.
Latest entries
- March 18, 2025General Wood TopicsWhat Color Is Ebony Wood? Unveiling the Rich Hues of This Luxurious Timber
- March 18, 2025Construction & FrameworkHow Can You Effectively Mount a Headboard to Your Wall?
- March 18, 2025General Wood TopicsCan Bees Really Eat Wood? Unraveling the Myths and Facts
- March 18, 2025General Wood TopicsDo Rabbits Really Chew on Wood? Exploring Their Eating Habits!