How Can You Build a Flute Out of Wood?
Crafting a wooden flute is not just an artistic endeavor; it’s a journey into the world of music, creativity, and craftsmanship. The soothing tones of a flute can transport listeners to serene landscapes, evoke deep emotions, and bring people together through the universal language of sound. Whether you’re a seasoned musician looking to experiment with your own instrument or a woodworking enthusiast eager to try your hand at something new, building a flute from wood offers a unique blend of challenge and reward. In this article, we’ll explore the essential techniques, tools, and materials needed to create your very own wooden flute, guiding you through each step of the process.
Creating a wooden flute involves understanding both the art of woodworking and the science of acoustics. The choice of wood, the design of the instrument, and the precision of your measurements all play crucial roles in determining the final sound quality. From selecting the right type of wood that resonates beautifully to mastering the intricate finger holes that allow for varied musical notes, each decision contributes to the overall character of your flute.
As you embark on this rewarding project, you’ll discover not only the technical skills required but also the joy of connecting with a tradition that spans cultures and centuries. With patience and practice, you’ll be able to craft a
Choosing the Right Wood
The selection of wood is crucial for crafting a quality flute. Different types of wood can impart unique tonal qualities and structural integrity. Here are some commonly used woods for flute making:
- Maple: Offers a bright, clear sound with a good projection.
- Cherry: Known for its warm tones and rich color, cherry can provide a more mellow sound.
- Hickory: Dense and durable, hickory produces a strong, focused tone.
- Bamboo: While technically a grass, bamboo is often used for its light weight and resonant qualities.
When selecting wood, consider the following factors:
- Moisture content: Ensure the wood is properly seasoned to prevent warping.
- Grain structure: Look for straight, tight grains for better sound quality.
Preparing the Wood
Once you have chosen the wood, the next step is to prepare it for shaping. This process involves cutting the wood to length and removing any imperfections. Follow these steps:
- Cut the wood to the desired length, typically between 24 to 30 inches for a flute.
- Remove bark and rough edges using a chisel or hand plane to create a smooth surface.
- Sand the surface using progressively finer grits of sandpaper until smooth.
Ensure that you maintain a uniform thickness throughout the body of the flute, as this will affect the sound quality.
Shaping the Flute Body
Shaping the body of the flute is an essential step that influences both aesthetics and acoustics. The basic outline of a flute typically features a cylindrical shape. You may consider the following methods for shaping:
- Hand-carving: This traditional method allows for detailed control but requires skill and patience.
- Drilling: Using a drill press, create a bore through the center of the wood for a consistent diameter.
Consider the following dimensions when shaping the flute:
Part of Flute | Recommended Dimension |
---|---|
Length | 24-30 inches |
Diameter | 0.75-1 inch |
Embouchure hole | 0.25-0.5 inch diameter |
Creating the Finger Holes
Finger holes are critical for producing different pitches. The placement and size of these holes directly affect the flute’s playability. Follow these guidelines:
- Determine hole placement: Use a tuner to establish the correct pitch for each note.
- Drill holes: Start with smaller holes (1/8 inch) and gradually widen them if necessary.
- Test playability: Make adjustments based on the ease of covering each hole and the resultant sound.
It is recommended to space the holes evenly to facilitate comfortable finger positioning.
Finishing Touches
After shaping and drilling, the flute requires finishing to enhance its durability and appearance. Follow these steps:
- Final sanding: Use fine-grit sandpaper to smooth all surfaces.
- Sealing: Apply a natural oil or lacquer to protect the wood from moisture and wear.
- Polishing: Buff the surface to achieve a smooth, glossy finish.
Ensure that any finish used is non-toxic, especially if the flute will be played frequently.
Materials Required for Crafting a Wooden Flute
To successfully build a wooden flute, it is essential to gather the appropriate materials. Each component contributes to the instrument’s sound quality and playability. Here is a list of necessary materials:
- Wood: Choose a dense, fine-grained wood like:
- Maple
- Cherry
- Walnut
- Drill: A hand drill or electric drill with various bits.
- Files and Sandpaper: For smoothing edges and achieving the desired shape.
- Measuring Tools: A ruler or caliper for precise measurements.
- Wood Glue: To secure joints, if needed.
- Finish: Oil or lacquer for protecting the wood and enhancing appearance.
Designing the Flute
Before starting the construction, it is crucial to design the flute. This involves determining the length, diameter, and hole placements, which significantly affect pitch and tone.
- Length: The typical length for a concert flute ranges from 18 to 26 inches. Longer flutes produce lower pitches.
- Diameter: A diameter of 0.75 to 1 inch is common, impacting the volume and tonal quality.
- Hole Placement: The positioning of finger holes affects the flute’s range. A standard design includes:
- Six finger holes
- One embouchure hole, located about a third of the way down from the top
Cutting the Wood
Once the design is finalized, the next step is to cut the wood to the desired length and shape.
- Measure and Mark: Use a ruler to mark the length of the flute on the wood.
- Cut: Employ a saw to cut the wood precisely.
- Drill: Create the embouchure hole first, followed by the finger holes. The hole sizes typically range from 5/16 inch to 3/8 inch in diameter, depending on the desired pitch.
Shaping the Flute
After cutting and drilling, shape the flute for comfort and aesthetics.
- Sand: Use sandpaper to smooth all edges and surfaces.
- Create a Taper: If desired, taper the ends of the flute slightly to enhance tonal qualities.
Finishing Touches
The final steps involve applying a protective finish and ensuring the flute is ready for play.
- Apply Finish: Use oil or lacquer to protect the wood and improve its appearance. Allow ample drying time.
- Tune the Flute: Play the flute and adjust the size of the finger holes if necessary to achieve the desired pitch.
Maintenance and Care
To ensure longevity and optimal sound quality, proper maintenance is essential.
- Cleaning: Wipe the flute after each use to remove moisture.
- Storage: Keep the flute in a protective case to avoid physical damage.
- Regular Checks: Inspect for cracks or wear and treat any issues promptly.
Expert Insights on Crafting Wooden Flutes
Dr. Emily Carter (Woodwind Instrument Specialist, The Musical Craft Journal). “When building a flute out of wood, selecting the right type of wood is crucial. Hardwoods like maple or cherry are preferred due to their density and tonal qualities, which significantly influence the sound production.”
James O’Connor (Master Woodworker and Luthier, Artisan Flutes Co.). “Precision in measurements and hole placements is vital for achieving the desired pitch and intonation. Utilizing tools like calipers and a drill press ensures accuracy, which is essential for a well-functioning wooden flute.”
Linda Tran (Acoustic Engineer, Sound Design Innovations). “Understanding the acoustics of a wooden flute is fundamental. The internal dimensions and the finish of the wood can alter the resonance and projection. Experimenting with different bore shapes can lead to unique sound characteristics.”
Frequently Asked Questions (FAQs)
What materials are needed to build a flute out of wood?
To build a wooden flute, you will need a suitable type of wood such as bamboo, maple, or cherry, a saw for cutting, a drill for creating finger holes, sandpaper for smoothing surfaces, and wood finish for sealing the flute.
What is the best type of wood for making a flute?
The best types of wood for flute making include hardwoods like maple, cherry, or boxwood due to their density and tonal qualities. Bamboo is also popular for its lightweight and resonant properties.
How do I determine the length of the flute?
The length of the flute is typically determined by the desired pitch. A general rule is that longer flutes produce lower pitches, while shorter flutes yield higher pitches. Standard concert flutes are usually around 26 inches long.
What is the process for creating finger holes?
Creating finger holes involves measuring and marking their positions based on the desired scale. Use a drill to create holes and then refine their sizes with sandpaper to achieve the correct pitch and tone.
How do I finish and seal the wooden flute?
After shaping and sanding the flute, apply a wood finish such as oil or lacquer to protect the wood from moisture and enhance its appearance. Allow adequate drying time as per the manufacturer’s instructions.
Can I customize the sound of my wooden flute?
Yes, the sound can be customized by adjusting the size and placement of the finger holes, the overall length of the flute, and the type of wood finish used. Experimentation will help achieve the desired tonal quality.
Building a flute out of wood is a rewarding endeavor that combines craftsmanship with musical artistry. The process begins with selecting the appropriate type of wood, as the choice of material significantly influences the flute’s tone and playability. Common woods used for flute-making include maple, cherry, and bamboo, each offering unique acoustic properties. Once the wood is selected, careful measurements and precise cutting are essential to create the body of the flute, ensuring that the internal bore is correctly shaped to produce the desired sound.
After shaping the flute, the next critical step involves creating the embouchure hole and finger holes. The placement and size of these holes are vital for achieving proper intonation and ease of playing. It is advisable to take a systematic approach, testing the flute at various stages to make adjustments as needed. Finishing touches, such as sanding and applying a protective sealant, enhance the flute’s aesthetic appeal and durability, ensuring it can withstand regular use.
building a wooden flute requires a combination of skill, patience, and an understanding of acoustics. Each step, from selecting the wood to final finishing, plays a crucial role in the overall quality of the instrument. Aspiring flute makers should be prepared to experiment and refine their techniques
Author Profile
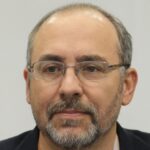
-
Darryl Norman is a seasoned entrepreneur and industry expert with a deep understanding of wood truss manufacturing and construction materials. As the President of Timberlake TrussWorks, LLC, Darryl played a pivotal role in shaping the company’s reputation for quality and precision. His leadership ensured that each truss met rigorous structural standards, providing builders with dependable components essential to their projects.
Beginning in 2025, Darryl Norman has shifted his focus to education and knowledge-sharing through an informative blog dedicated to wood truss manufacturing. Drawing from his extensive experience in the field, he provides in-depth insights into truss design, material selection, and construction techniques. This blog serves as a valuable resource for builders, contractors, and homeowners seeking practical guidance on truss systems and structural integrity.
Latest entries
- March 18, 2025General Wood TopicsWhat Color Is Ebony Wood? Unveiling the Rich Hues of This Luxurious Timber
- March 18, 2025Construction & FrameworkHow Can You Effectively Mount a Headboard to Your Wall?
- March 18, 2025General Wood TopicsCan Bees Really Eat Wood? Unraveling the Myths and Facts
- March 18, 2025General Wood TopicsDo Rabbits Really Chew on Wood? Exploring Their Eating Habits!