How Can You Build a Wood Processor: A Step-by-Step Guide?
In a world increasingly driven by efficiency and sustainability, the art of wood processing has taken on new significance. Whether you’re a seasoned lumberjack, a DIY enthusiast, or simply someone looking to harness the power of nature, building your own wood processor can be a game-changer. This innovative machine not only streamlines the task of transforming logs into usable firewood or lumber but also empowers you to take control of your wood supply. Imagine the satisfaction of crafting your own equipment, tailored to your specific needs, while also reducing your reliance on commercial machinery. In this article, we will explore the essentials of constructing a wood processor, guiding you through the key considerations, materials, and techniques that will bring your vision to life.
Building a wood processor involves a blend of mechanical knowledge, woodworking skills, and an understanding of the materials you’ll be working with. From selecting the right engine to choosing the appropriate cutting mechanisms, each decision plays a crucial role in the overall functionality and efficiency of your machine. Additionally, safety considerations cannot be overlooked, as working with heavy machinery and sharp tools requires a thorough understanding of best practices to ensure a safe working environment.
As we delve deeper into the world of wood processing, you’ll discover the various designs and configurations available, each offering unique advantages depending
Materials Needed
To build a wood processor, a variety of materials are required to ensure durability and efficiency. The main components include:
- Frame and Structure: Steel or heavy-duty wood for the frame.
- Power Source: A gas or electric engine, typically in the range of 5 to 20 horsepower.
- Cutting Mechanism: A chainsaw or circular saw blade, appropriate for the size of logs being processed.
- Conveyor Belt: To transport cut wood pieces.
- Hydraulic System: For log clamping and splitting.
- Safety Equipment: Guards, shields, and emergency stop features.
Using high-quality materials will ensure that the wood processor lasts longer and operates safely.
Design Considerations
When designing a wood processor, several factors must be taken into account:
- Size of Logs: Determine the maximum diameter and length of logs that the machine will handle.
- Processing Speed: The efficiency of the cutting and splitting mechanisms should match your production goals.
- Mobility: Decide if the wood processor will be stationary or portable.
- Safety Features: Incorporate safety guards and emergency shut-off switches.
The design should facilitate easy access for maintenance and repairs, ensuring the longevity of the machine.
Building the Frame
The frame serves as the backbone of the wood processor. Start by constructing a robust base using steel or heavy-duty wood. Follow these steps:
- Measure: Determine the dimensions based on the size of logs you will process.
- Cut Materials: Use a cutting tool to create the necessary pieces for the frame.
- Assemble: Weld or bolt the frame together, ensuring all connections are secure.
Consider adding adjustable legs to accommodate uneven ground.
Installing the Cutting Mechanism
The cutting mechanism is crucial for processing wood efficiently. Here’s how to install it:
- Choose the Right Saw: Select a chainsaw or circular saw that fits the intended use.
- Mount the Saw: Securely attach the saw to the frame using brackets and bolts.
- Align: Ensure that the saw is properly aligned for optimal cutting performance.
Ensure all components are tightly fastened to prevent vibrations during operation.
Hydraulic System Setup
A hydraulic system is essential for log clamping and splitting. The setup involves:
- Hydraulic Pump: Install a hydraulic pump connected to the power source.
- Cylinders: Position hydraulic cylinders for log clamping and splitting.
- Hoses and Valves: Connect hoses to the cylinders and install valves for control.
The hydraulic system must be tested for leaks and functionality before use.
Electrical and Safety Features
Integrating electrical components and safety features is vital for safe operation:
- Wiring: Run electrical wires from the power source to the motor, ensuring compliance with local electrical codes.
- Emergency Stops: Install easily accessible emergency stop buttons.
- Safety Shields: Add guards around moving parts to protect operators.
Ensure that all electrical connections are insulated and secure.
Component | Material | Purpose |
---|---|---|
Frame | Steel/Wood | Support structure |
Engine | Gas/Electric | Power source |
Cutting Mechanism | Chainsaw/Circular Saw | Cut logs |
Hydraulic System | Hydraulic Components | Log handling |
Understanding the Components of a Wood Processor
A wood processor is a machine designed to cut, split, and stack wood efficiently. The primary components include:
- Engine: Powers the entire system; can be gas or electric.
- Feeding Mechanism: Guides logs into the processor; can be manual or automatic.
- Cutting System: Typically a chainsaw or circular saw for cutting logs to desired lengths.
- Splitting Mechanism: Hydraulic or mechanical system that splits the wood after cutting.
- Conveyor System: Moves the processed wood to a stacking area.
- Control System: Manages all operations and ensures safety.
Selecting Materials for Construction
Choosing the right materials is crucial for durability and performance. Key materials include:
Material | Purpose |
---|---|
Steel | Main frame and structural components |
Aluminum | Lightweight components, such as the conveyor |
Hydraulic Hoses | Connects the hydraulic system to the splitter |
Electrical Wiring | Powers the engine and control systems |
Bearings | Allows smooth movement of the conveyor and splitter |
Designing the Layout
The layout of a wood processor should optimize efficiency and ease of use. Consider the following design elements:
- Log Infeed Area: Space for logs to be fed into the machine.
- Cutting Area: Room for the cutting mechanism to operate safely.
- Splitting Area: Design for the splitter, allowing for debris clearance.
- Outfeed and Stacking Area: Ensure adequate space for processed wood to be stacked or moved.
Building the Frame
Constructing the frame is the first step in assembling your wood processor. Follow these guidelines:
- Cut Steel Beams: Use a cutting torch or saw to create beams according to your design.
- Weld Joints: Assemble the beams using a MIG or TIG welder for maximum strength.
- Install Supports: Ensure the frame has adequate cross-bracing to prevent bending or flexing.
Installing the Engine and Power System
Select an engine that can handle the workload. Installation steps include:
- Mount the Engine: Securely attach the engine to the frame using bolts.
- Connect the Fuel System: Ensure proper fuel lines are connected to prevent leaks.
- Set Up Electrical Wiring: Install wiring for controls and engine ignition, adhering to safety standards.
Integrating the Cutting and Splitting Mechanisms
The cutting and splitting mechanisms require precise installation for optimal functionality:
- Cutting Mechanism:
- Attach the saw blade to the engine output shaft.
- Ensure the alignment is correct to avoid binding during operation.
- Splitting Mechanism:
- Install the hydraulic splitter, ensuring it is securely mounted.
- Connect hydraulic hoses from the pump to the splitter, checking for leaks.
Testing and Safety Checks
Before using the wood processor, conduct thorough testing:
- Check All Connections: Ensure all bolts and fittings are tight.
- Run the Engine: Test the engine to ensure it operates smoothly.
- Test the Cutting and Splitting Functions: Operate each mechanism separately to identify any issues.
- Safety Features: Install emergency stop buttons and guards around moving parts.
Maintaining the Wood Processor
Regular maintenance is essential for longevity and performance:
- Daily Checks: Inspect hydraulic fluid levels and clean debris from the machine.
- Weekly Maintenance: Sharpen cutting blades and check for any wear on components.
- Annual Overhaul: Inspect the frame and replace any worn-out parts as necessary.
Expert Insights on Building a Wood Processor
James Whitaker (Mechanical Engineer, TimberTech Solutions). “When building a wood processor, it is crucial to focus on the efficiency of the cutting mechanism. Utilizing high-quality blades and ensuring proper alignment will significantly enhance performance and reduce downtime.”
Linda Chen (Sustainable Forestry Consultant, GreenWood Innovations). “Incorporating eco-friendly materials and energy-efficient motors into your wood processor design not only supports sustainability but also appeals to a growing market of environmentally conscious consumers.”
Mark Thompson (Industrial Equipment Designer, WoodTech Magazine). “Attention to safety features is paramount when constructing a wood processor. Implementing guards, emergency shut-off switches, and proper training for operators can prevent accidents and ensure a safer working environment.”
Frequently Asked Questions (FAQs)
What materials are necessary to build a wood processor?
To build a wood processor, you will need materials such as a robust frame (steel or heavy-duty wood), a powerful engine (gas or electric), hydraulic components for splitting, a conveyor belt for transporting logs, and various tools for assembly.
What are the essential components of a wood processor?
Essential components include a log cradle, a splitting wedge, a hydraulic system for operation, a cutting mechanism (such as a chainsaw), and a collection area for processed wood.
How much does it cost to build a wood processor?
The cost to build a wood processor can vary widely based on materials and components used, but a basic model may range from $1,500 to $5,000, while more advanced models can exceed $10,000.
Do I need any special skills to build a wood processor?
Yes, building a wood processor requires mechanical skills, knowledge of hydraulic systems, and familiarity with woodworking tools and safety practices to ensure proper assembly and operation.
What safety precautions should I take when building a wood processor?
Safety precautions include wearing appropriate personal protective equipment (PPE), ensuring proper ventilation during assembly, following manufacturer guidelines for machinery, and securing all moving parts to prevent accidents.
Can I modify an existing wood processor design?
Yes, modifying an existing wood processor design is common. Ensure modifications enhance functionality, maintain safety standards, and do not compromise the structural integrity of the machine.
Building a wood processor is a multifaceted project that requires careful planning, the right materials, and a solid understanding of mechanical principles. The process typically involves designing a machine that can efficiently cut, split, and transport wood. Key components include a powerful engine, cutting blades, and a splitting mechanism, all of which must be integrated into a cohesive unit. Proper safety measures and ergonomic considerations are crucial to ensure the machine is not only effective but also safe for the user.
Throughout the construction process, it is essential to prioritize quality materials to enhance durability and performance. Selecting the right engine and ensuring that the cutting and splitting mechanisms are robust will significantly impact the efficiency of the wood processor. Additionally, incorporating features such as adjustable height and mobility can improve usability and versatility, making the machine suitable for various wood processing tasks.
In summary, building a wood processor requires a blend of engineering knowledge, practical skills, and attention to detail. By following a structured approach and focusing on the integration of essential components, one can create a machine that meets specific wood processing needs. Ultimately, the investment of time and resources into this project can yield significant benefits, including increased productivity and efficiency in wood processing operations.
Author Profile
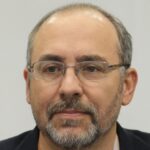
-
Darryl Norman is a seasoned entrepreneur and industry expert with a deep understanding of wood truss manufacturing and construction materials. As the President of Timberlake TrussWorks, LLC, Darryl played a pivotal role in shaping the company’s reputation for quality and precision. His leadership ensured that each truss met rigorous structural standards, providing builders with dependable components essential to their projects.
Beginning in 2025, Darryl Norman has shifted his focus to education and knowledge-sharing through an informative blog dedicated to wood truss manufacturing. Drawing from his extensive experience in the field, he provides in-depth insights into truss design, material selection, and construction techniques. This blog serves as a valuable resource for builders, contractors, and homeowners seeking practical guidance on truss systems and structural integrity.
Latest entries
- March 18, 2025General Wood TopicsWhat Color Is Ebony Wood? Unveiling the Rich Hues of This Luxurious Timber
- March 18, 2025Construction & FrameworkHow Can You Effectively Mount a Headboard to Your Wall?
- March 18, 2025General Wood TopicsCan Bees Really Eat Wood? Unraveling the Myths and Facts
- March 18, 2025General Wood TopicsDo Rabbits Really Chew on Wood? Exploring Their Eating Habits!