How Can You Create Effective Wood Splitter Plans?
If you’re an avid woodworker, a homeowner with a fireplace, or someone who simply enjoys the warmth of a crackling fire, you know that splitting wood can be a labor-intensive task. While store-bought wood splitters can be costly, building your own wood splitter can be a rewarding project that saves you money and provides you with a sense of accomplishment. In this article, we’ll explore how to build a wood splitter from scratch, offering detailed plans and insights to help you create a tool that will make your wood-splitting tasks more efficient and enjoyable.
Creating your own wood splitter not only allows you to customize the design to fit your specific needs, but it also gives you the opportunity to learn valuable skills in woodworking and machinery. From selecting the right materials to understanding the mechanics of splitting wood, this project can be both educational and practical. Whether you’re looking to tackle larger logs or simply streamline your wood preparation process, having a reliable splitter at your disposal can make all the difference.
As we delve into the specifics of building a wood splitter, we’ll cover essential considerations such as the types of wood splitters available, the tools required for the job, and safety precautions to keep in mind. With a solid plan in hand, you’ll be well on your way to crafting
Choosing the Right Design
When developing wood splitter plans, the first step is selecting a design that suits your needs and skill level. There are several common designs, including:
- Horizontal Splitters: Ideal for splitting larger logs, these models are generally easier to load and operate.
- Vertical Splitters: These are perfect for handling heavy logs, as they allow the wood to be loaded from the ground level.
- Electric vs. Gas-Powered: Electric splitters are quieter and require less maintenance, while gas-powered models provide greater mobility and power.
Considerations for choosing a design include:
- The type and size of wood you typically split
- The available space for the splitter
- Your budget and power source preferences
Materials and Tools Required
Creating a wood splitter requires specific materials and tools. Below is a comprehensive list of what you will need:
Materials:
- Steel plates (for the frame and wedge)
- Hydraulic cylinder
- Hydraulic pump
- Wheels (for mobility)
- Axles
- Piping and fittings for hydraulic connections
- Electrical components (if using an electric model)
Tools:
- Welder
- Drill
- Angle grinder
- Measuring tape
- Safety gear (gloves, goggles)
Building the Frame
The frame serves as the foundation for your wood splitter. It should be sturdy enough to withstand the forces generated during operation. Key steps include:
- Cutting the Steel Plates: Cut the steel plates to the desired dimensions for the frame.
- Welding the Base: Weld the base section of the frame, ensuring it is level and square.
- Adding Support Beams: Incorporate additional beams for stability, especially if you are building a vertical model.
The frame should ultimately be designed to support the hydraulic components and withstand the pressure of splitting wood.
Hydraulic System Assembly
The hydraulic system is crucial for the operation of your wood splitter. Here’s how to assemble it:
- Install the Hydraulic Cylinder: Secure the cylinder to the frame, ensuring it is aligned correctly for optimal splitting force.
- Connect the Hydraulic Pump: Attach the hydraulic pump to the cylinder using piping and fittings. Ensure all connections are tight to prevent leaks.
- Fill the System with Hydraulic Fluid: Use the recommended hydraulic fluid to fill the system, following manufacturer specifications.
Safety Features and Testing
Incorporating safety features is essential when building a wood splitter. Consider the following:
- Emergency Shut-off Switch: Install a switch that can quickly cut power to the hydraulic system.
- Safety Guards: Add guards around moving parts to prevent accidental contact.
- Proper Signage: Clearly label controls and safety instructions on the machine.
Before using the splitter, conduct a thorough test to ensure all components function correctly. This includes:
- Checking for hydraulic leaks
- Testing the splitting action with small logs
- Ensuring stability during operation
Component | Description | Importance |
---|---|---|
Hydraulic Cylinder | Drives the splitting action | Essential for operation |
Frame | Supports the entire structure | Critical for stability |
Safety Features | Protects the operator | Vital for safe operation |
Essential Components of a Wood Splitter
Building a wood splitter requires understanding the essential components that contribute to its functionality and efficiency. Below are the primary components that should be included in your plans:
- Engine: The power source, typically a gas engine or electric motor, that drives the hydraulic pump.
- Hydraulic Pump: Converts mechanical energy from the engine into hydraulic energy to move the splitter.
- Hydraulic Cylinder: The component that uses hydraulic pressure to drive the splitting wedge forward.
- Wedge: The cutting tool that splits the wood; it can be designed in various shapes for different types of logs.
- Frame: The structural support that holds all components together, usually made from heavy-duty steel.
- Log Cradle: A support structure that holds the log in place while it is being split, enhancing safety and efficiency.
Materials Needed
When constructing a wood splitter, selecting the right materials is crucial for durability and performance. Here’s a list of essential materials:
- Steel Tubing: For the frame, choose a heavy-duty steel that can withstand stress.
- Hydraulic Components: Ensure you have a quality hydraulic pump, cylinder, and hoses.
- Engine: Select an engine with adequate horsepower for your splitting needs (typically between 5 to 20 HP).
- Wedge Material: Use hardened steel for the wedge to ensure it can withstand repeated impacts.
- Wheels and Axle: For mobility, use heavy-duty wheels and a strong axle.
Basic Design Overview
A simple wood splitter design consists of several key elements arranged in a logical manner. Below is a basic layout:
Component | Description |
---|---|
Engine | Positioned at the rear for balance and accessibility. |
Hydraulic Pump | Mounted next to the engine for direct power transfer. |
Hydraulic Cylinder | Positioned horizontally, extending towards the wedge. |
Wedge | Fixed at the front, attached to the end of the cylinder. |
Frame | Constructed from steel tubing, providing overall support. |
Log Cradle | Located in front of the wedge for optimal log placement. |
Construction Steps
Follow these steps to construct your wood splitter:
- Frame Assembly:
- Cut steel tubing to the required lengths.
- Weld the pieces together to form a sturdy rectangular base.
- Reinforce with cross beams for added stability.
- Engine and Hydraulic Pump Installation:
- Secure the engine at the rear of the frame using bolts.
- Connect the hydraulic pump directly to the engine using a drive belt.
- Hydraulic Cylinder and Wedge Attachment:
- Mount the hydraulic cylinder horizontally to the frame.
- Attach the splitting wedge to the front end of the cylinder.
- Log Cradle Construction:
- Create a cradle from wood or additional steel tubing.
- Ensure it is stable and positioned to hold logs securely while splitting.
- Final Assembly:
- Connect hydraulic hoses from the pump to the cylinder.
- Install wheels and axles for mobility.
- Test all components for proper functioning.
Safety Considerations
When building and operating a wood splitter, safety should be a top priority. Keep the following safety measures in mind:
- Protective Gear: Always wear gloves, goggles, and sturdy footwear.
- Emergency Stop: Include an easily accessible emergency stop switch.
- Stable Surface: Ensure the splitter operates on a flat, stable ground.
- Proper Training: Familiarize yourself and any users with the operation manual and safety guidelines before use.
Expert Insights on Building Wood Splitter Plans
John Matthews (Mechanical Engineer, TimberTech Solutions). “When designing wood splitter plans, it is crucial to consider the hydraulic system’s efficiency. A well-calibrated hydraulic pump can significantly enhance the splitting force, making the machine more effective and reducing wear on components.”
Linda Garcia (Woodworking Specialist, DIY Home Magazine). “Incorporating adjustable features in your wood splitter plans allows for versatility in handling different wood types. A splitter with adjustable height and splitting angles can accommodate a wider range of logs, improving overall usability.”
Michael Tran (Sustainable Forestry Consultant, GreenWood Initiative). “Sustainability should be a key consideration in your wood splitter design. Using recycled materials for the frame and ensuring energy efficiency in the hydraulic system not only reduces costs but also minimizes environmental impact.”
Frequently Asked Questions (FAQs)
What materials are needed to build a wood splitter?
To build a wood splitter, you will need a sturdy frame (typically made from steel or heavy-duty wood), a hydraulic cylinder, a pump, hoses, a power source (electric motor or gas engine), and various fasteners. Additionally, safety equipment and tools such as a welder, saw, and drill are essential.
Are there specific plans available for building a wood splitter?
Yes, there are numerous plans available online and in woodworking books. These plans often include detailed diagrams, material lists, and step-by-step instructions to guide you through the building process.
What are the key features to consider when designing a wood splitter?
Key features to consider include the splitting force, size of the logs it can handle, the type of power source, mobility (wheeled or stationary), and safety features such as guards and emergency shut-off switches.
Can I build a wood splitter using recycled materials?
Yes, building a wood splitter from recycled materials is possible, provided the materials are sturdy and safe. Ensure that any recycled components, especially the hydraulic system, are in good condition and suitable for the intended load.
How much does it cost to build a wood splitter?
The cost to build a wood splitter varies significantly based on materials and components used. On average, a DIY wood splitter can range from $300 to $1,000, depending on the quality of parts and whether you opt for new or used items.
What safety precautions should I take when building and using a wood splitter?
Safety precautions include wearing protective gear (gloves, goggles, and ear protection), ensuring all components are securely fastened, keeping bystanders at a safe distance, and familiarizing yourself with the operation of the hydraulic system to prevent accidents.
building a wood splitter can be a rewarding project that enhances your efficiency in preparing firewood or managing lumber. The plans for constructing a wood splitter typically involve selecting the right materials, understanding the mechanics of hydraulic systems, and ensuring safety measures are in place. By following detailed blueprints and instructions, you can create a functional and durable tool that meets your specific needs.
Key takeaways from the discussion include the importance of proper planning and design. Before embarking on the construction, it is crucial to assess the types of wood you will be splitting and the volume of work you expect to handle. This assessment will guide your choice of a hydraulic or manual splitter, as well as the dimensions and power requirements of your build.
Additionally, safety should be a paramount consideration throughout the building process and during operation. Utilizing protective gear, ensuring stable footing, and following operational guidelines will help prevent accidents. Ultimately, a well-constructed wood splitter not only saves time and effort but also enhances your overall wood processing experience.
Author Profile
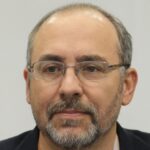
-
Darryl Norman is a seasoned entrepreneur and industry expert with a deep understanding of wood truss manufacturing and construction materials. As the President of Timberlake TrussWorks, LLC, Darryl played a pivotal role in shaping the company’s reputation for quality and precision. His leadership ensured that each truss met rigorous structural standards, providing builders with dependable components essential to their projects.
Beginning in 2025, Darryl Norman has shifted his focus to education and knowledge-sharing through an informative blog dedicated to wood truss manufacturing. Drawing from his extensive experience in the field, he provides in-depth insights into truss design, material selection, and construction techniques. This blog serves as a valuable resource for builders, contractors, and homeowners seeking practical guidance on truss systems and structural integrity.
Latest entries
- March 18, 2025General Wood TopicsWhat Color Is Ebony Wood? Unveiling the Rich Hues of This Luxurious Timber
- March 18, 2025Construction & FrameworkHow Can You Effectively Mount a Headboard to Your Wall?
- March 18, 2025General Wood TopicsCan Bees Really Eat Wood? Unraveling the Myths and Facts
- March 18, 2025General Wood TopicsDo Rabbits Really Chew on Wood? Exploring Their Eating Habits!