How Can You Build Your Own Wooden Surfboard?
Surfing is more than just a sport; it’s a lifestyle, a culture, and for many, a form of art. Crafting your own wooden surfboard can elevate this experience to new heights, allowing you to connect with the ocean in a uniquely personal way. Imagine gliding over the waves on a board that you meticulously shaped and designed with your own hands. Not only does building a wooden surfboard offer a rewarding challenge, but it also provides an opportunity to create a sustainable piece of equipment that reflects your individuality. In this article, we will explore the essential steps and considerations for embarking on this exciting journey of craftsmanship.
Building a wooden surfboard is a blend of traditional techniques and modern innovation. It requires an understanding of the materials, tools, and processes involved in shaping wood into a functional and aesthetically pleasing surfboard. From selecting the right type of wood to understanding the hydrodynamics of the board’s design, each decision plays a crucial role in the final product. Whether you’re a seasoned woodworker or a complete novice, the process can be both educational and fulfilling.
As you delve into the world of wooden surfboard construction, you’ll discover the importance of patience and precision. Each phase, from crafting the blank to applying the final finish, demands attention to detail
Choosing the Right Wood
When building a wooden surfboard, selecting the appropriate type of wood is crucial for performance and durability. Common choices include:
- Paulownia: Lightweight and buoyant, ideal for performance boards.
- Cedar: Offers a good balance of weight and flexibility, suitable for various board shapes.
- Plywood: Cost-effective and readily available, but may require additional finishing for a smooth surface.
Consider the following factors when choosing wood:
- Weight: Lighter woods enhance maneuverability.
- Durability: Hardwoods resist dings and damage.
- Flexibility: Certain woods provide the right amount of flex for your surfing style.
Cutting and Shaping the Blank
Once you have selected your wood, the next step involves cutting and shaping the blank. This process requires precision and attention to detail.
- Use a band saw or jigsaw to cut the blank to your desired dimensions.
- Shape the blank using hand planes, rasps, and sandpaper to achieve the desired contours.
Tool | Purpose |
---|---|
Band Saw | Cutting the blank to rough shape |
Hand Plane | Shaping the bottom and rails |
Sander | Smoothing surfaces and edges |
Ensure that the board’s rocker, width, and thickness are suitable for your intended use. Regularly check your progress against the desired dimensions to maintain symmetry.
Applying the Fiberglass and Resin
After shaping, the next critical step is to protect your wooden surfboard with fiberglass and resin. This process enhances durability and provides a waterproof barrier.
- Prepare the surface by sanding it smooth.
- Cut fiberglass cloth to size, allowing for overlap on the edges.
- Mix the epoxy resin as per the manufacturer’s instructions.
To apply the fiberglass:
- Lay the fiberglass cloth over the board.
- Pour the mixed resin onto the cloth and spread it evenly using a squeegee.
- Ensure all areas are saturated, avoiding bubbles and dry spots.
Allow the resin to cure completely, following the recommended drying time before proceeding to the next step.
Finishing Touches
Once the fiberglass has cured, it’s essential to finish the board properly for aesthetics and performance.
- Sanding: Start with coarse sandpaper and gradually move to finer grits for a smooth finish.
- Polishing: Use a polishing compound to achieve a glossy surface.
- Sealing: Apply a sealant to protect against moisture and UV damage.
Consider adding artwork or decals at this stage, ensuring they are also sealed under a final layer of resin for longevity.
These finishing touches not only improve the look of your surfboard but also enhance its performance and lifespan on the waves.
Materials Needed
To build a wooden surfboard, gathering the right materials is crucial for both performance and durability. Here’s a comprehensive list of what you will need:
- Wood: Choose suitable types like Paulownia, Cedar, or Balsa, which are lightweight and buoyant.
- Fiberglass: For strength and waterproofing.
- Epoxy Resin: Preferred over polyester for its superior bonding and environmental resistance.
- Foam Blank: A pre-shaped foam core can simplify the process.
- Sandpaper: Various grits for smoothing surfaces.
- Clamps: To hold pieces together while the adhesive sets.
- Saw: A jigsaw or circular saw for cutting wood and shaping the board.
- Planer: For achieving a smooth finish on the wood surface.
- Router: To create the edges and any desired contours.
- Measuring Tape and Ruler: For precise measurements.
Designing the Surfboard
Before construction, it’s essential to design the surfboard. The design will affect the board’s performance, including speed, stability, and maneuverability. Consider these factors:
- Length: Generally ranges from 5 to 9 feet, depending on skill level and wave conditions.
- Width: Affects stability; wider boards are easier for beginners.
- Thickness: Influences buoyancy; thicker boards float better.
- Rocker: The curve of the board; more rocker aids maneuverability, while less rocker increases speed.
- Tail Shape: Different shapes (square, round, swallow) impact performance in various surf conditions.
Shaping the Surfboard
Shaping is one of the most critical steps in building a wooden surfboard. Follow these guidelines:
- Cut the Foam Blank: Start by cutting the foam to your desired dimensions using a saw.
- Outline the Shape: Use a pencil to mark the outline of the surfboard on the foam.
- Shaping with a Planer: Gradually shave down the foam to achieve the desired thickness and contours.
- Refining Edges: Use a router to refine the rails and add any necessary contours.
- Sanding: Smooth all surfaces with sandpaper, starting with coarse grits and moving to finer grits for a polished finish.
Applying Fiberglass and Resin
This step adds strength and waterproofing to your surfboard. Follow these instructions:
- Prepare the Area: Ensure a clean, dust-free workspace.
- Cut Fiberglass Cloth: Cut the cloth to size, allowing for overlap on the edges.
- Mix Epoxy Resin: Follow the manufacturer’s instructions for mixing resin and hardener.
- Lay Fiberglass: Place the fiberglass cloth over the shaped foam.
- Apply Resin: Using a brush or roller, apply a generous amount of resin over the fiberglass, ensuring full saturation.
- Curing: Allow the board to cure as per the resin’s specifications, typically 24 hours.
Final Touches
After the board has cured, perform the finishing touches to ensure it’s ready for the waves.
- Sand the Surface: Lightly sand to remove imperfections and achieve a smooth finish.
- Add Additional Layers: Depending on desired durability, consider adding more layers of fiberglass and resin.
- Attach Fins: Install fin boxes and fins according to your design preferences.
- Polish: Use a polishing compound for a glossy finish.
Testing the Surfboard
Before hitting the waves, conduct a test:
- Dry Test: Check balance and weight distribution on land.
- Water Test: Take it into calm water first to assess performance and make adjustments as necessary.
Building a wooden surfboard involves careful planning, precise shaping, and meticulous finishing. By following these guidelines, you can create a unique board tailored to your surfing style.
Expert Insights on Building a Wooden Surfboard
“Building a wooden surfboard requires a deep understanding of both the materials and the design. I recommend using high-quality marine plywood for durability and flexibility. Additionally, consider the board’s shape and rocker, as these factors significantly influence performance on the water.”
“As a surfboard shaper with over 15 years of experience, I emphasize the importance of precision in measurements. Each cut and curve should be meticulously planned to ensure the board not only looks good but also rides well. Experimenting with different wood types can also yield unique characteristics in the surfboard’s performance.”
“Sustainability is a key consideration in modern surfboard construction. Using reclaimed wood not only adds character to your board but also minimizes environmental impact. I advise builders to explore eco-friendly finishes that protect the wood without harmful chemicals.”
Frequently Asked Questions (FAQs)
What materials are needed to build a wooden surfboard?
To build a wooden surfboard, you will need marine-grade plywood, epoxy resin, fiberglass cloth, wood glue, clamps, sandpaper, and a surfboard template. Additionally, tools such as a jigsaw, planer, and sanding block are essential.
How long does it take to build a wooden surfboard?
The time required to build a wooden surfboard varies based on skill level and design complexity, but typically ranges from 20 to 40 hours. This includes cutting, shaping, laminating, and finishing the board.
Can beginners build a wooden surfboard?
Yes, beginners can build a wooden surfboard, but it is advisable to start with a simple design and follow detailed instructions or a guide. Gaining some woodworking skills beforehand will enhance the building experience.
What is the best type of wood for a surfboard?
The best types of wood for a surfboard include Paulownia, cedar, and balsa. These woods are lightweight, buoyant, and have good water resistance, making them ideal for surfboard construction.
How do I finish a wooden surfboard?
To finish a wooden surfboard, sand the surface smooth, apply a sealant or primer, and then coat it with epoxy resin. Allow adequate curing time between coats, and finish with a final sanding for a glossy appearance.
Is it necessary to use fiberglass on a wooden surfboard?
While not strictly necessary, using fiberglass on a wooden surfboard enhances durability and water resistance. It provides additional strength and helps prevent damage from impacts and water absorption.
Building a wooden surfboard is a rewarding endeavor that combines craftsmanship with a deep appreciation for the surf culture. The process involves selecting the right type of wood, typically marine-grade plywood or solid timber, and carefully shaping the board to achieve the desired dimensions and performance characteristics. Proper planning and execution are essential, as each step—from cutting and shaping to sealing and finishing—contributes to the overall quality and durability of the surfboard.
Throughout the construction process, attention to detail is paramount. Techniques such as laminating, sanding, and applying a waterproof finish not only enhance the aesthetics of the board but also ensure its longevity in the water. Additionally, understanding the hydrodynamics of surfboards can help builders tailor their designs to suit specific surfing styles and conditions, making the finished product more enjoyable to ride.
Ultimately, the journey of building a wooden surfboard is as significant as the final product itself. It fosters a connection to the craft and the ocean, allowing surfers to create a unique piece that reflects their personal style and preferences. By embracing the challenges and joys of this process, individuals can develop a deeper appreciation for both the art of surfboard making and the sport of surfing itself.
Author Profile
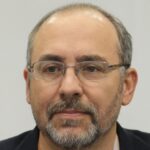
-
Darryl Norman is a seasoned entrepreneur and industry expert with a deep understanding of wood truss manufacturing and construction materials. As the President of Timberlake TrussWorks, LLC, Darryl played a pivotal role in shaping the company’s reputation for quality and precision. His leadership ensured that each truss met rigorous structural standards, providing builders with dependable components essential to their projects.
Beginning in 2025, Darryl Norman has shifted his focus to education and knowledge-sharing through an informative blog dedicated to wood truss manufacturing. Drawing from his extensive experience in the field, he provides in-depth insights into truss design, material selection, and construction techniques. This blog serves as a valuable resource for builders, contractors, and homeowners seeking practical guidance on truss systems and structural integrity.
Latest entries
- March 18, 2025General Wood TopicsWhat Color Is Ebony Wood? Unveiling the Rich Hues of This Luxurious Timber
- March 18, 2025Construction & FrameworkHow Can You Effectively Mount a Headboard to Your Wall?
- March 18, 2025General Wood TopicsCan Bees Really Eat Wood? Unraveling the Myths and Facts
- March 18, 2025General Wood TopicsDo Rabbits Really Chew on Wood? Exploring Their Eating Habits!