How Can You Accurately Calculate Wood for Framing Your Next Project?
When embarking on a construction or renovation project, one of the most crucial steps is understanding how to calculate the amount of wood needed for framing. Whether you’re building a new home, adding an extension, or simply tackling a DIY project, accurate calculations can save you time, money, and unnecessary frustration. Framing is the backbone of any structure, providing the essential support and shape that holds everything together. But how do you determine the right quantities and types of wood required to bring your vision to life?
Calculating wood for framing involves more than just a simple measurement of walls and beams. It requires an understanding of various factors, including the dimensions of your project, the type of framing you plan to use, and the specific materials that will best suit your needs. From the height and length of walls to the spacing of studs and headers, each element plays a vital role in ensuring your structure is both sturdy and efficient.
Additionally, knowing how to properly account for waste and potential mistakes is essential. Even seasoned builders can miscalculate, leading to excess costs or project delays. By mastering the art of wood calculation, you can confidently approach your framing project, equipped with the knowledge to make informed decisions and achieve a successful outcome. In the following sections, we will delve deeper into the methods
Calculating the Amount of Lumber Required
To accurately calculate the amount of lumber needed for framing, it is essential to consider various factors such as the dimensions of the structure, the spacing of the studs, and the type of wood used. Begin by determining the total square footage of the walls, floors, and ceilings that will be framed.
- Calculate Square Footage: Measure the length and height of each wall. Multiply these dimensions to find the square footage. For example, a wall that is 10 feet high and 20 feet long would have a square footage of 200 square feet.
- Account for Openings: Subtract the square footage of doors and windows from the total square footage. If a door measures 3 feet by 7 feet, its area is 21 square feet.
- Determine Framing Requirements: Standard stud spacing is typically 16 inches on center. This means that for every 16 inches of wall length, you will need one stud. Use the following formula to calculate the number of studs required:
\[
\text{Number of studs} = \frac{\text{Total wall length (in inches)}}{16} + 1
\]
- Calculate Additional Lumber: Include other framing components such as top and bottom plates, headers, and blocking. A typical calculation for plates is two lengths of the wall per wall, and headers will vary based on the number and size of openings.
Component | Calculation | Quantity |
---|---|---|
Studs | Length of wall (in ft) / 1.33 | Calculated total |
Top Plates | 2 x Length of wall (in ft) | Calculated total |
Bottom Plates | 2 x Length of wall (in ft) | Calculated total |
Headers | Based on openings | Calculated total |
Estimating Lumber Types and Sizes
Different types of wood have varying strengths and uses. The most common lumber for framing includes:
- Dimensional Lumber: Typically used for studs (2×4, 2×6), joists, and rafters.
- Engineered Wood: Such as laminated veneer lumber (LVL) for headers and beams due to its strength.
- Pressure-Treated Wood: Used for any framing that comes in contact with the ground.
When selecting lumber, consider:
- Load-Bearing Requirements: Ensure that the lumber can support the weight of the structure.
- Moisture Resistance: Use pressure-treated wood for areas prone to moisture exposure.
- Local Building Codes: Check local regulations for specific requirements on lumber types and sizes.
By accurately calculating the total square footage, accounting for openings, and selecting the appropriate lumber types, you can ensure that your framing project is both efficient and structurally sound.
Determining Framing Needs
Calculating the amount of wood required for framing involves several steps. First, establish the dimensions of the area you plan to frame. This typically includes walls, floors, and ceilings. You will need to consider both the vertical and horizontal elements of your structure.
- Measure the Area:
- Length of the walls
- Height of the walls
- Any openings such as doors and windows
- Calculate Linear Feet:
To determine the linear feet of wood needed, follow these steps:
- For walls: Multiply the total length of all walls by the height.
- For floors and ceilings: Multiply the length and width of the area.
Calculating Specific Framing Components
Different components of framing require specific calculations. Below are the key materials involved:
- Studs:
Standard framing uses 2×4 lumber for wall studs, spaced typically 16 inches on center.
- Formula: Total length of walls (in inches) ÷ 16
- Adjust for openings (subtract studs that would be cut for doors/windows).
- Top and Bottom Plates:
Each wall will require a top and bottom plate.
- Formula: Total length of walls x 2 (for both plates).
- Headers:
For door and window openings, headers provide structural support.
- Typically, use 2×6 or 2×8 lumber.
- Size and number will depend on the size and number of openings.
- Blocking and Bracing:
Additional wood is needed for blocking between studs and bracing for stability.
- Estimate 1 piece of blocking for every 4 feet of wall length.
Using a Framing Calculator
A framing calculator can streamline the process by providing quick estimates based on input dimensions. Many online tools allow you to input wall lengths, heights, and openings to receive material lists.
Material Specifications and Quantities
Below is a sample table showing estimated quantities based on a hypothetical framing project for a 200 sq. ft. wall area:
Component | Quantity Required | Notes |
---|---|---|
2×4 Studs | 45 | Based on 16″ spacing |
Top Plates | 2 | For two walls |
Bottom Plates | 2 | For two walls |
Headers | 2 | Size will depend on door/window size |
Blocking | 10 | 1 piece every 4 ft |
Final Adjustments and Considerations
When ordering materials, always account for waste and mistakes. A general rule is to add 10% to your total material needs. Additionally, consider the type of wood, as different species and grades may have varying costs and structural properties.
Expert Insights on Calculating Wood for Framing
Emily Carter (Construction Project Manager, BuildSmart Solutions). “Accurate calculations for wood framing begin with a comprehensive understanding of the project’s design and dimensions. It is essential to account for both the structural elements and the aesthetic features to ensure that the right amount of lumber is ordered without excess waste.”
James Thompson (Architectural Engineer, TimberTech Innovations). “When calculating wood for framing, one must consider the type of wood being used, as different species have varying strengths and weight. Additionally, it is vital to include allowances for cuts and waste, typically estimating around 10% extra to accommodate for errors during construction.”
Linda Garcia (Building Materials Specialist, EcoBuild Resources). “Utilizing software tools designed for framing calculations can significantly enhance accuracy. These tools can help in determining the precise quantities of lumber needed based on the framing layout, which is particularly useful for larger projects where manual calculations may lead to errors.”
Frequently Asked Questions (FAQs)
How do I determine the amount of wood needed for framing a wall?
To calculate the amount of wood needed for framing a wall, measure the total length and height of the walls. Multiply the length by the height to find the square footage, then divide by the coverage area of the lumber you plan to use, accounting for studs, top and bottom plates, and any windows or doors.
What types of wood are commonly used for framing?
Common types of wood used for framing include dimensional lumber such as pine, fir, and spruce. Pressure-treated lumber is often used for areas exposed to moisture, while engineered wood products like LVL (Laminated Veneer Lumber) provide added strength and stability.
What is the standard spacing for framing studs?
The standard spacing for framing studs is typically 16 inches on center (OC) for residential construction. However, 24 inches OC may be used in certain applications, depending on local building codes and structural requirements.
How do I calculate the number of studs needed for a wall?
To calculate the number of studs needed, first determine the total length of the wall in inches. Divide this number by the stud spacing (usually 16 or 24 inches) and add one additional stud for the end of the wall. Round up to the nearest whole number to ensure sufficient coverage.
What factors should I consider when calculating wood for framing?
Consider factors such as the type of structure, local building codes, the presence of windows and doors, and the overall design of the project. Additionally, account for waste and mistakes by adding about 10% to your total material estimate.
How do I calculate the amount of plywood needed for sheathing?
To calculate the amount of plywood needed for sheathing, measure the total square footage of the walls to be covered. Divide this number by the square footage of a standard plywood sheet (typically 32 square feet for a 4×8 sheet) to determine the total number of sheets required, rounding up as necessary.
Calculating wood for framing is an essential skill for anyone involved in construction or DIY projects. The process involves determining the amount of lumber needed based on the dimensions of the structure, including walls, floors, and roofs. Accurate calculations help in budgeting and ensure that the right quantity of materials is purchased, minimizing waste and project delays.
Key factors to consider when calculating wood for framing include the type of framing method being used, the dimensions of the space, and the specific requirements for structural support. It is crucial to account for various elements such as studs, plates, headers, and any additional framing needed for windows and doors. Utilizing standard lumber sizes and understanding local building codes can further streamline the calculation process.
mastering the calculation of wood for framing not only enhances efficiency in construction projects but also contributes to better resource management. By following systematic steps and employing accurate measurements, individuals can ensure that their framing projects are completed successfully and within budget. This foundational knowledge is invaluable for both professional builders and enthusiastic DIYers alike.
Author Profile
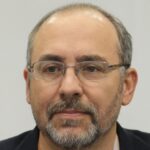
-
Darryl Norman is a seasoned entrepreneur and industry expert with a deep understanding of wood truss manufacturing and construction materials. As the President of Timberlake TrussWorks, LLC, Darryl played a pivotal role in shaping the company’s reputation for quality and precision. His leadership ensured that each truss met rigorous structural standards, providing builders with dependable components essential to their projects.
Beginning in 2025, Darryl Norman has shifted his focus to education and knowledge-sharing through an informative blog dedicated to wood truss manufacturing. Drawing from his extensive experience in the field, he provides in-depth insights into truss design, material selection, and construction techniques. This blog serves as a valuable resource for builders, contractors, and homeowners seeking practical guidance on truss systems and structural integrity.
Latest entries
- March 18, 2025General Wood TopicsWhat Color Is Ebony Wood? Unveiling the Rich Hues of This Luxurious Timber
- March 18, 2025Construction & FrameworkHow Can You Effectively Mount a Headboard to Your Wall?
- March 18, 2025General Wood TopicsCan Bees Really Eat Wood? Unraveling the Myths and Facts
- March 18, 2025General Wood TopicsDo Rabbits Really Chew on Wood? Exploring Their Eating Habits!