How Can You Master the Art of Carving Faces in Wood?
Carving faces in wood is a captivating blend of artistry and craftsmanship that allows woodworkers to breathe life into their creations. Whether you’re a seasoned artisan or a curious beginner, the allure of transforming a simple block of wood into a detailed, expressive face is undeniable. This ancient craft not only showcases your skills but also invites you to explore the depths of human emotion and character through the medium of wood. In this article, we will delve into the techniques, tools, and artistic considerations that will guide you on your journey to mastering the art of face carving.
The process of carving faces in wood involves a unique combination of observation, technique, and creativity. Understanding the structure of the human face is essential, as it provides the foundation for capturing likeness and expression. From the subtle curves of the cheekbones to the intricate details of the eyes, each feature requires careful attention and skillful execution. As you embark on this artistic endeavor, you’ll discover the importance of choosing the right type of wood, as well as the tools that will help you achieve precision and finesse in your work.
Moreover, face carving is not just about replicating what you see; it’s about infusing your personality and style into each piece. This craft encourages experimentation and innovation, allowing you to
Choosing the Right Tools
Selecting appropriate tools is crucial for carving faces in wood. The right tools not only improve the quality of your work but also ensure your safety and comfort during the carving process. Here are essential tools you should consider:
- Carving Knives: These are specialized knives designed for detailed work. Look for a knife with a comfortable handle and a sharp, narrow blade.
- Gouges: Various sizes and shapes of gouges can help create depth and texture in your carving. U-shaped and V-shaped gouges are particularly useful for detailing facial features.
- Chisels: Flat chisels are ideal for removing larger sections of wood and refining the overall shape of the face.
- V-tools: These are excellent for creating fine lines and details, such as wrinkles and hair texture.
- Saws: A small coping saw can be used to cut out rough shapes before fine detailing begins.
Understanding Wood Selection
Choosing the right type of wood is essential for successful face carving. Different woods have distinct characteristics that affect the carving process and final appearance. Here’s a comparison of common wood types:
Wood Type | Density | Workability | Finish |
---|---|---|---|
Basswood | Low | Excellent | Smooth |
Butternut | Medium | Good | Warm |
Cherry | Medium | Moderate | Rich |
Oak | High | Poor | Textured |
Basswood is highly recommended for beginners due to its softness, making it easier to carve and providing a smooth finish. Harder woods like oak require more effort and skill.
Techniques for Carving Faces
Carving faces involves various techniques that focus on capturing likeness and expression. Here are key techniques to master:
- Blocking Out: Start by roughly shaping the head and features with larger tools, like chisels. This step establishes proportions and overall form.
- Refining Shapes: Gradually move to smaller tools, refining the eyes, nose, and mouth. Pay attention to symmetry and proportions.
- Detailing: Use gouges and V-tools to add fine details. Focus on wrinkles, pores, and hair texture to bring the face to life.
- Texturing: Create different textures using various tools to differentiate between skin and hair. Experiment with techniques like stippling for skin texture.
- Smoothing: Once details are carved, use sandpaper or a fine knife to smooth out any rough edges and achieve a polished finish.
Finishing Touches
After the carving is complete, applying a finish is essential to protect the wood and enhance its appearance. Follow these steps:
- Sanding: Begin with medium-grit sandpaper and progress to finer grits for a smooth finish.
- Staining or Painting: Choose a wood stain or paint that complements your design. Apply evenly to avoid blotching.
- Sealing: Use a wood sealer or varnish to protect the surface from moisture and wear. Several coats may be necessary for durability.
By carefully selecting tools, wood, and techniques, you can achieve impressive results in face carving that showcase your artistic skills and attention to detail.
Choosing the Right Wood
Selecting the appropriate type of wood is crucial for carving faces. Different woods have varying densities, grain patterns, and workability, which can significantly affect the final outcome.
- Softwoods: Easier to carve and ideal for beginners.
- Pine: Readily available, lightweight, and affordable.
- Basswood: Smooth grain, minimal knots, and widely used for carving.
- Hardwoods: More durable and often used for detailed, high-quality work.
- Cherry: Beautiful grain, rich color, but harder to carve.
- Maple: Tough and dense, suitable for intricate designs.
Essential Tools for Face Carving
The right tools can make the difference between a frustrating experience and a satisfying result. Here’s a list of essential tools you should consider:
Tool | Purpose |
---|---|
Carving Knife | For detailed cuts and shaping facial features. |
Gouges | For hollowing and creating depth in the carving. |
Chisels | For removing larger sections of wood quickly. |
V-tools | For fine lines and detailing, especially around eyes and lips. |
Mallet | Used to strike chisels and gouges for more force. |
Sandpaper | For smoothing surfaces after carving. |
Basic Techniques for Face Carving
Understanding fundamental techniques will enhance your ability to carve realistic faces. Here are some key techniques to master:
- Blocking Out: Start with a rough outline of the face. Focus on the overall shape and proportions.
- Defining Features: Gradually refine the features such as eyes, nose, and mouth. Use a combination of your carving knife and gouges.
- Texturing: Add texture to the hair and skin using varied tools. This step can help create realism.
- Shading: Use deeper cuts and varied strokes to create shadows and highlights, enhancing the three-dimensional effect.
Carving Process Step-by-Step
Follow these steps to carve a face effectively:
- Sketch the Design: Use a pencil to draw the outline of the face directly onto the wood.
- Remove Excess Wood: Use a carving knife to remove large sections around the face outline.
- Carve the Features: Focus on one feature at a time. Start with the eyes, then the nose, and finally the mouth.
- Refine Details: Switch to smaller tools for intricate details, ensuring to observe references for accuracy.
- Sand and Finish: Once the carving is complete, sand the surface to smooth out any rough patches. Consider applying a finish such as oil or varnish to protect the wood.
Common Mistakes to Avoid
Being aware of common pitfalls can save time and frustration. Here are mistakes to watch out for:
- Ignoring Wood Grain: Always carve with the grain to prevent splintering.
- Over-Detailing Early: Focus on the overall shape before adding details to avoid excessive removal of material.
- Neglecting Safety: Always use cut-resistant gloves and keep tools sharp to reduce the risk of injury.
Practicing and Improving Your Skills
Continuous practice is essential for honing your carving skills. Consider the following tips:
- Start Small: Begin with smaller projects before tackling larger, more complex carvings.
- Study Faces: Use photographs and real-life models to understand proportions and features better.
- Join a Community: Engage with local carving groups or online forums to exchange tips and get feedback on your work.
Expert Techniques for Carving Faces in Wood
Emily Carter (Master Woodcarver, Artisan Woodworks). “When carving faces in wood, it is essential to start with a well-defined plan. I recommend sketching the face on the wood before you begin carving, as this will help you visualize the final product and ensure that proportions are accurate.”
James Holloway (Woodworking Instructor, Craftsmanship School). “One of the most critical aspects of face carving is understanding the anatomy of the face. I advise students to study facial features and practice on smaller pieces before attempting larger projects. This foundational knowledge will greatly enhance the realism of your carvings.”
Linda Tran (Sculptor and Author, The Art of Wood Carving). “Using the right tools cannot be overstated. For detailed facial features, I prefer using a combination of chisels and knives. Each tool serves a unique purpose, and mastering their use will allow you to create intricate details that bring your carved faces to life.”
Frequently Asked Questions (FAQs)
What tools are necessary for carving faces in wood?
To carve faces in wood, essential tools include a set of carving knives, gouges, chisels, a mallet, and a whittling knife. Additionally, a carving glove and a sturdy workbench are recommended for safety and stability.
What type of wood is best for carving faces?
Basswood is often preferred for face carving due to its fine grain and softness, making it easy to work with. Other suitable options include butternut and pine, which also provide good results for intricate details.
How do I start carving a face in wood?
Begin by sketching the face design on the wood surface. Use a roughing knife to outline the basic shape, then gradually refine the features with smaller tools. Focus on one section at a time to maintain control and precision.
What techniques are used for detailing facial features?
Detailing techniques include using V-gouges for creating fine lines, carving small curves for eyes and lips, and employing stop cuts to define edges. Layering cuts gradually helps achieve depth and realism in facial features.
How can I finish a carved face to enhance its appearance?
After carving, sand the surface to smooth out rough areas, then apply wood finish such as oil, wax, or varnish. This not only enhances the appearance but also protects the wood from moisture and wear.
Are there any safety precautions to take while carving?
Yes, always wear a carving glove on your non-dominant hand to protect against accidental cuts. Ensure your workspace is well-lit and organized to prevent accidents. Additionally, maintain sharp tools, as dull tools can slip and cause injury.
Carving faces in wood is a rewarding and intricate craft that combines artistic expression with technical skill. To successfully carve faces, one must begin with a solid understanding of the tools and materials required, including chisels, knives, and the appropriate type of wood. Selecting the right wood, such as basswood or butternut, can significantly influence the ease of carving and the final appearance of the piece. Additionally, having a clear design or reference image can guide the carver through the process, ensuring that proportions and features are accurately represented.
The carving process typically involves several stages, starting with rough shaping and progressing to finer details. Techniques such as relief carving and in-the-round carving each offer unique challenges and outcomes. It is essential to practice patience and precision, as facial features require careful attention to detail to achieve realistic expressions. Furthermore, understanding the anatomy of the face can greatly enhance the quality of the carving, allowing for more lifelike representations.
Finally, finishing touches such as sanding, staining, or painting can elevate the carved face, adding depth and character to the work. Overall, mastering the art of carving faces in wood demands dedication and practice, but the satisfaction of creating a lifelike representation makes the effort worthwhile. Aspiring woodcar
Author Profile
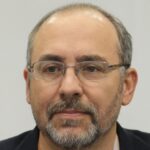
-
Darryl Norman is a seasoned entrepreneur and industry expert with a deep understanding of wood truss manufacturing and construction materials. As the President of Timberlake TrussWorks, LLC, Darryl played a pivotal role in shaping the company’s reputation for quality and precision. His leadership ensured that each truss met rigorous structural standards, providing builders with dependable components essential to their projects.
Beginning in 2025, Darryl Norman has shifted his focus to education and knowledge-sharing through an informative blog dedicated to wood truss manufacturing. Drawing from his extensive experience in the field, he provides in-depth insights into truss design, material selection, and construction techniques. This blog serves as a valuable resource for builders, contractors, and homeowners seeking practical guidance on truss systems and structural integrity.
Latest entries
- March 18, 2025General Wood TopicsWhat Color Is Ebony Wood? Unveiling the Rich Hues of This Luxurious Timber
- March 18, 2025Construction & FrameworkHow Can You Effectively Mount a Headboard to Your Wall?
- March 18, 2025General Wood TopicsCan Bees Really Eat Wood? Unraveling the Myths and Facts
- March 18, 2025General Wood TopicsDo Rabbits Really Chew on Wood? Exploring Their Eating Habits!