How Can You Effectively Dry Green Wood?
Drying green wood is a crucial step in woodworking, carpentry, and various DIY projects. Whether you’re a seasoned craftsman or a weekend hobbyist, understanding how to properly dry green wood can significantly impact the quality and durability of your finished product. Freshly cut wood, known as green wood, contains a high moisture content that can lead to warping, cracking, and other structural issues if not handled correctly. In this article, we will explore effective methods for drying green wood, ensuring that your creations stand the test of time.
When it comes to drying green wood, the process is not as simple as leaving it out in the sun. Several factors, including wood species, thickness, and environmental conditions, play a vital role in determining the best drying method. From air drying to kiln drying, each approach has its advantages and challenges. Understanding these methods will help you choose the right technique for your specific project, ensuring that your wood is adequately prepared for use.
Moreover, the drying process requires patience and attention to detail. Rushing the drying can lead to undesirable results, while taking the time to do it right can yield beautiful, stable wood that enhances your craftsmanship. In the following sections, we will delve deeper into the various techniques, tips, and best practices for drying green
Methods of Drying Green Wood
Drying green wood can be accomplished using several methods, each with its own advantages and disadvantages. The choice of method often depends on the type of wood, the intended use, and available resources.
Air Drying
Air drying is one of the oldest and most traditional methods for drying green wood. This process involves stacking the wood outdoors in a manner that allows air to circulate freely around each piece.
- Advantages:
- Low cost and minimal equipment required.
- Suitable for large quantities of wood.
- Retains the natural appearance and properties of the wood.
- Disadvantages:
- Weather-dependent; drying may be slow in humid or rainy conditions.
- Risk of insect damage or fungal growth if not properly managed.
To effectively air dry wood, consider the following steps:
- Stacking: Stack the wood in a well-ventilated area, using spacers (stickers) between layers to allow airflow.
- Covering: Use a tarp or roof to protect the stack from rain while ensuring the sides remain open for air circulation.
- Monitoring: Regularly check the moisture content and condition of the wood.
Kiln Drying
Kiln drying accelerates the drying process by controlling temperature, humidity, and airflow within a closed environment. This method is often employed commercially for high-quality lumber.
- Advantages:
- Faster than air drying, typically taking days to weeks.
- Reduces the risk of defects such as warping or cracking.
- Can achieve lower moisture content suitable for various applications.
- Disadvantages:
- Higher initial investment due to equipment costs.
- Requires careful monitoring to prevent damage from overheating.
When using a kiln, follow these general steps:
- Loading: Load the wood into the kiln, ensuring proper spacing for airflow.
- Setting Conditions: Set the kiln to the appropriate temperature and humidity levels based on the wood species.
- Monitoring: Continuously monitor the moisture content and adjust conditions as necessary.
Dehumidification Drying
Dehumidification drying is a method that uses a dehumidifier to remove moisture from the air surrounding the wood. This technique is effective in controlled indoor environments.
- Advantages:
- Can be used year-round, regardless of outdoor weather conditions.
- Energy-efficient compared to traditional kilns.
- Disadvantages:
- Slower than kiln drying but faster than air drying.
- Initial setup costs may be higher.
Comparison Table of Drying Methods
Method | Time Required | Cost | Quality Control |
---|---|---|---|
Air Drying | Weeks to Months | Low | Variable |
Kiln Drying | Days to Weeks | High | High |
Dehumidification Drying | Weeks | Medium | Moderate |
Factors Affecting Drying Time
Several factors can influence the drying time of green wood, including:
- Wood Species: Different species have varying densities and moisture contents, affecting drying rates.
- Thickness: Thicker pieces of wood take longer to dry than thinner ones.
- Environmental Conditions: Temperature, humidity, and airflow in the drying area significantly impact the process.
- Initial Moisture Content: The higher the moisture content at the start, the longer it will take to dry.
By understanding these factors and selecting the appropriate drying method, one can effectively reduce the moisture content of green wood to suit their specific needs.
Understanding Moisture Content in Green Wood
The moisture content in green wood refers to the amount of water contained within the wood fibers. This content can significantly affect the drying process and the final quality of the lumber. Understanding this concept is crucial for effective drying methods.
- Freshly Cut Wood: Contains about 30-200% moisture content, depending on the species and conditions.
- Air-Dried Wood: Typically reaches a moisture content of 12-20%.
- Kiln-Dried Wood: Can achieve a moisture content as low as 6-8%.
Moisture content can be measured using a moisture meter, providing insight into the drying progress and the point at which the wood is ready for use.
Methods for Drying Green Wood
There are several methods to dry green wood, each with its advantages and considerations. The choice of method often depends on the desired end use of the wood and available resources.
Air Drying
Air drying is a natural process that involves exposing the wood to air in a shaded, well-ventilated area. Key steps include:
- Select the Right Location: Choose a dry, shady area with good airflow.
- Stacking: Stack the wood with spacers (stickers) between layers to allow air circulation.
- Covering: Protect the stack from rain and direct sunlight to minimize warping and checking.
Kiln Drying
Kiln drying accelerates the drying process using controlled heat and humidity. This method is more efficient but requires specialized equipment.
- Types of Kilns:
- Conventional Kilns: Use heat from gas or electricity to dry wood.
- Dehumidification Kilns: Employ dehumidifiers to control moisture levels.
- Process:
- Load the green wood into the kiln.
- Set the desired temperature and humidity levels.
- Monitor moisture content regularly until it reaches the target.
Solar Drying
Solar drying leverages sunlight to dry wood, using a solar kiln or simply stacking wood in sunlight with adequate airflow. Important considerations include:
- Design: Solar kilns should be designed to maximize sunlight exposure while minimizing heat loss.
- Monitoring: Regularly check moisture levels to ensure even drying.
Factors Influencing Drying Time
Several factors can affect the time it takes to dry green wood, including:
Factor | Impact on Drying Time |
---|---|
Wood Species | Different species have varying densities and moisture content. |
Thickness of Wood | Thicker pieces take longer to dry than thinner ones. |
Environmental Conditions | Humidity, temperature, and airflow play critical roles. |
Stack Arrangement | Proper stacking improves airflow and reduces drying time. |
Potential Issues During Drying
While drying wood, several issues may arise that can affect the quality of the final product:
- Warping: Uneven drying can cause wood to twist or bend.
- Cracking: Rapid moisture loss can lead to surface cracks or checks.
- Fungal Growth: High moisture levels can encourage mold and decay.
To mitigate these issues, maintaining consistent drying conditions and monitoring moisture levels is essential.
Expert Strategies for Drying Green Wood
Dr. Emily Carter (Wood Science Researcher, Timber Innovations Institute). “The most effective method for drying green wood is to utilize a controlled environment, such as a solar kiln, which allows for gradual moisture removal while minimizing the risk of warping and cracking.”
James O’Reilly (Master Carpenter, Heritage Woodworks). “Air drying is a traditional approach that can be very effective; however, it is crucial to stack the wood properly with spacers to promote airflow and prevent mold growth during the drying process.”
Linda Tran (Sustainable Forestry Consultant, EcoWood Solutions). “For those looking to expedite the drying process, using a dehumidifier in a well-ventilated space can significantly reduce drying time while maintaining the integrity of the wood.”
Frequently Asked Questions (FAQs)
What is the best method to dry green wood?
The best method to dry green wood is air drying, which involves stacking the wood in a well-ventilated area, allowing moisture to evaporate naturally over time. This method minimizes the risk of warping and cracking.
How long does it take to dry green wood?
The drying time for green wood varies depending on the type of wood, thickness, and environmental conditions. Generally, it can take anywhere from several months to over a year for the wood to reach a suitable moisture content.
What is the ideal moisture content for dried wood?
The ideal moisture content for dried wood is typically between 6% and 12%. This range ensures the wood is stable for use in construction or woodworking projects.
Can I speed up the drying process of green wood?
Yes, you can speed up the drying process by using a kiln or a dehumidifier. These methods control temperature and humidity, allowing for faster moisture removal while reducing the risk of defects.
What are the signs that green wood is drying properly?
Signs that green wood is drying properly include a gradual decrease in weight, the appearance of small cracks on the ends (checking), and a change in color. Additionally, the wood should feel noticeably lighter and sound more hollow when tapped.
Is it necessary to seal the ends of green wood during drying?
Yes, sealing the ends of green wood with a wax or sealant can help prevent rapid moisture loss, which reduces the risk of checking and splitting. This practice is especially beneficial for thicker pieces of wood.
Drying green wood is a critical process for anyone involved in woodworking, carpentry, or construction. The primary goal of drying green wood is to reduce its moisture content to a level that minimizes warping, cracking, and other forms of damage. Various methods can be employed, including air drying, kiln drying, and using a solar kiln, each with its advantages and drawbacks. Selecting the appropriate method depends on factors such as the type of wood, desired end use, and available resources.
Air drying is often the most accessible method, requiring minimal equipment and allowing the wood to acclimate naturally to the environment. However, it can be time-consuming and may not achieve the desired moisture content in humid climates. On the other hand, kiln drying offers a faster and more controlled approach, effectively reducing moisture content while also killing pests and fungi. Nevertheless, it requires specialized equipment and can be costly.
Key takeaways from the discussion on drying green wood include the importance of monitoring moisture levels throughout the drying process. Using a moisture meter can provide valuable insights into the wood’s condition and help determine when it has reached the appropriate dryness for its intended use. Additionally, understanding the specific characteristics of different wood species can aid in selecting the best drying method and
Author Profile
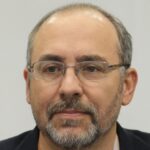
-
Darryl Norman is a seasoned entrepreneur and industry expert with a deep understanding of wood truss manufacturing and construction materials. As the President of Timberlake TrussWorks, LLC, Darryl played a pivotal role in shaping the company’s reputation for quality and precision. His leadership ensured that each truss met rigorous structural standards, providing builders with dependable components essential to their projects.
Beginning in 2025, Darryl Norman has shifted his focus to education and knowledge-sharing through an informative blog dedicated to wood truss manufacturing. Drawing from his extensive experience in the field, he provides in-depth insights into truss design, material selection, and construction techniques. This blog serves as a valuable resource for builders, contractors, and homeowners seeking practical guidance on truss systems and structural integrity.
Latest entries
- March 18, 2025General Wood TopicsWhat Color Is Ebony Wood? Unveiling the Rich Hues of This Luxurious Timber
- March 18, 2025Construction & FrameworkHow Can You Effectively Mount a Headboard to Your Wall?
- March 18, 2025General Wood TopicsCan Bees Really Eat Wood? Unraveling the Myths and Facts
- March 18, 2025General Wood TopicsDo Rabbits Really Chew on Wood? Exploring Their Eating Habits!