How Can You Master the Art of Wood Engraving?
Engraving in wood is an age-old craft that marries creativity with precision, allowing artisans and hobbyists alike to transform simple wooden surfaces into stunning works of art. Whether you’re looking to personalize a gift, create a unique home decor piece, or simply explore a new hobby, mastering the art of wood engraving can be a rewarding endeavor. With the right tools, techniques, and a touch of imagination, you can carve intricate designs that tell a story or convey a special message. In this article, we will delve into the essentials of wood engraving, guiding you through the process from concept to completion.
Engraving wood involves more than just a steady hand; it requires an understanding of the materials and methods that will yield the best results. From selecting the right type of wood to choosing the appropriate engraving tools, each step plays a crucial role in the overall outcome of your project. Whether you opt for traditional hand tools or modern laser engravers, knowing how to navigate the various options available will empower you to achieve your desired effect.
As you embark on your wood engraving journey, you’ll discover that the possibilities are virtually limitless. From simple patterns and monograms to elaborate scenes and intricate designs, the choice of what to engrave is entirely up to you. With practice
Choosing the Right Tools for Wood Engraving
Selecting appropriate tools is crucial for achieving high-quality engravings in wood. The type of engraving you want to accomplish will determine the tools you’ll need. Commonly used tools include:
- Hand Tools: Such as chisels, gouges, and carving knives.
- Power Tools: Like rotary tools (Dremel), laser engravers, and CNC machines.
- Engraving Pens: These are excellent for detailed work and fine lines.
When choosing tools, consider the following factors:
- Type of Wood: Softer woods (like pine) are easier to engrave than hardwoods (like oak or maple).
- Design Complexity: Intricate designs may require more precise tools.
- Finishing Needs: Some tools may leave a rough finish that requires sanding or additional finishing.
Preparing the Wood Surface
Before engraving, it’s essential to prepare the wood surface properly to ensure a clean and professional result. Follow these steps:
- Select Quality Wood: Use wood that is free from knots, cracks, and other imperfections.
- Sand the Surface: Begin with a coarse grit sandpaper (e.g., 80-grit) and gradually progress to a finer grit (e.g., 220-grit) to create a smooth surface.
- Clean the Wood: Remove any dust or debris by wiping the surface with a damp cloth or using a vacuum.
- Apply a Template (Optional): For complex designs, consider using a stencil or transferring the design onto the wood.
Techniques for Engraving in Wood
Various techniques can be employed depending on the tools available and the desired outcome. Here are some popular methods:
- Hand Carving: This traditional method involves using chisels and knives to manually carve the design into the wood. It allows for a high level of detail but requires skill and practice.
- Burning: Wood burning, or pyrography, uses a heated tool to burn designs into the wood. This technique is excellent for creating intricate patterns and shading.
- Laser Engraving: A modern and precise method where a laser engraver etches the design into the wood. This method is suitable for detailed, repeatable designs.
- CNC Engraving: CNC machines allow for automated engraving, making it easy to create consistent and intricate designs on wood.
Technique | Tool Required | Skill Level | Best For |
---|---|---|---|
Hand Carving | Chisels, Knives | Intermediate to Advanced | Detailed, Custom Designs |
Burning | Wood Burner | Beginner to Intermediate | Textured Designs |
Laser Engraving | Laser Engraver | Beginner | Precise, Reproducible Designs |
CNC Engraving | CNC Machine | Intermediate to Advanced | Complex Designs, Mass Production |
Finishing Touches
After the engraving is complete, it is important to finish the wood properly to enhance its appearance and durability. Consider these steps:
- Sanding: Lightly sand the engraved areas to remove any rough edges or burns.
- Sealing: Apply a wood sealer or finish to protect the engraving and enhance the wood’s natural beauty.
- Polishing: For a glossy finish, use a wood polish or wax after the sealer has dried.
By following these guidelines, you can achieve beautiful and lasting engravings on wood that showcase your craftsmanship and creativity.
Choosing the Right Tools for Wood Engraving
The choice of tools is crucial for achieving quality results in wood engraving. Various methods exist, each requiring specific tools suited to the project at hand.
- Hand Tools: Ideal for detailed work and small projects.
- Chisels: Different sizes for varied depths and widths of cuts.
- V-tools: Perfect for creating fine lines and intricate designs.
- Gouges: Used for removing larger sections of wood.
- Power Tools: Efficient for larger projects or when speed is essential.
- Dremel Rotary Tool: Versatile for engraving and carving with various attachments.
- Laser Engraver: Offers precision and the ability to replicate designs with ease.
- Engraving Machines: Automated options for consistency across multiple pieces.
- Software: For laser engravers, design software is necessary.
- CorelDRAW: Widely used for vector graphics.
- Adobe Illustrator: Excellent for creating detailed designs.
Preparing the Wood Surface
Before engraving, proper preparation of the wood surface enhances the final outcome.
- Selection of Wood: Choose a type of wood that is easy to engrave, such as basswood or cherry.
- Sanding: Smooth the surface using fine-grit sandpaper (220 grit) to remove any imperfections.
- Cleaning: Wipe the surface with a damp cloth to remove dust and debris, allowing for clearer engraving.
- Marking the Design: Lightly sketch the design using a pencil or transfer it using carbon paper.
Engraving Techniques
Different techniques can be applied depending on the desired effect and tools used.
- Relief Engraving: Involves carving away the background, leaving the design raised. This technique is best suited for hand tools.
- Incised Engraving: Creates a sunken design into the wood, often used with power tools for precision.
- Pyrography: A technique that uses a heated pen to burn designs into the wood, offering a unique texture and depth.
- Laser Engraving: Utilizes a focused laser beam to etch designs, allowing for intricate details and repeatability.
Safety Precautions
When engaging in wood engraving, safety should always be prioritized.
- Protective Gear:
- Safety goggles to protect eyes from wood chips.
- Dust mask to prevent inhalation of wood dust.
- Ear protection when using power tools.
- Work Environment:
- Ensure good ventilation, especially when using power tools or lasers.
- Use a sturdy, flat work surface to stabilize the wood while engraving.
- Tool Maintenance: Regularly check and maintain tools to ensure they operate safely and effectively.
Finishing Touches
Once the engraving is complete, finishing touches can enhance the appearance and longevity of the wood piece.
- Sanding: Lightly sand the engraved areas to smooth out any rough edges.
- Staining or Painting: Apply wood stain or paint to enhance contrast and protect the wood.
- Sealing: Use a clear wood finish or sealant to protect the engraved design and the wood surface from moisture and wear.
By following these guidelines, the process of engraving in wood can be executed with both artistry and precision, resulting in beautiful and durable designs.
Expert Insights on Wood Engraving Techniques
Dr. Emily Carter (Woodworking Specialist, Artisan Crafts Journal). “Engraving in wood requires a precise understanding of the material’s grain and density. Choosing the right tool, whether it be a laser engraver or traditional carving tools, is crucial for achieving clean and detailed results.”
Mark Thompson (Master Woodworker, Timber Trends). “Preparation is key when engraving wood. Sanding the surface to a smooth finish before starting the engraving process not only enhances the final appearance but also reduces the risk of splintering during engraving.”
Linda Chen (DIY Home Improvement Expert, Crafting Today). “Experimenting with different types of wood can yield varied results in engraving. Softwoods like pine are easier to engrave but may not hold detail as well as hardwoods like maple or cherry, which provide a more durable finish.”
Frequently Asked Questions (FAQs)
What tools are needed to engrave in wood?
To engrave in wood, you typically need a wood engraving tool such as a rotary tool, laser engraver, or a chisel and mallet. Additionally, safety gear like goggles and a dust mask is recommended.
What types of wood are best for engraving?
Softwoods like pine, cedar, and basswood are ideal for engraving due to their ease of carving. Hardwoods such as oak and maple can also be used but may require more effort and sharper tools.
Can I engrave on finished wood surfaces?
Yes, you can engrave on finished wood surfaces, but it is advisable to sand the area lightly to ensure better adhesion of the engraving tool and a cleaner finish.
How deep should I engrave into the wood?
The depth of engraving typically ranges from 1/32 to 1/8 inch, depending on the design and the type of wood. It is essential to maintain a consistent depth for a professional appearance.
Is it possible to engrave intricate designs in wood?
Yes, intricate designs can be engraved in wood, especially using laser engravers or precision rotary tools. Careful planning and practice are necessary to achieve detailed results.
What safety precautions should I take while engraving wood?
Always wear safety goggles and a dust mask to protect against wood dust and debris. Ensure your workspace is well-ventilated and keep tools in good condition to prevent accidents.
Engraving in wood is a rewarding craft that combines creativity with technical skill. The process typically involves selecting the right tools, such as rotary engravers, laser engravers, or hand tools, depending on the desired outcome and intricacy of the design. Preparation of the wood surface is crucial, as it ensures a clean and precise engraving. Techniques vary from simple designs to intricate patterns, and understanding the properties of different wood types can significantly impact the final result.
Safety precautions should not be overlooked during the engraving process. Proper eye protection and ventilation are essential, especially when using power tools or lasers. Additionally, taking the time to practice on scrap wood can help refine techniques and boost confidence before tackling a final project. Maintaining the tools in good condition will also enhance performance and ensure high-quality engravings.
Ultimately, engraving in wood allows for a unique expression of artistry and personalization. Whether for creating gifts, home decor, or professional signage, mastering this skill opens up a world of possibilities. With patience and practice, anyone can learn to engrave wood effectively, producing beautiful and lasting pieces that showcase their creativity.
Author Profile
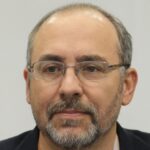
-
Mahlon Boehs is a seasoned entrepreneur and industry expert with a deep understanding of wood truss manufacturing and construction materials. As the President of Timberlake TrussWorks, LLC, Mahlon played a pivotal role in shaping the company’s reputation for quality and precision. His leadership ensured that each truss met rigorous structural standards, providing builders with dependable components essential to their projects.
Beginning in 2025, Mahlon Boehs has shifted his focus to education and knowledge-sharing through an informative blog dedicated to wood truss manufacturing. Drawing from his extensive experience in the field, he provides in-depth insights into truss design, material selection, and construction techniques. This blog serves as a valuable resource for builders, contractors, and homeowners seeking practical guidance on truss systems and structural integrity.
Latest entries
- March 18, 2025General Wood TopicsWhat Color Is Ebony Wood? Unveiling the Rich Hues of This Luxurious Timber
- March 18, 2025Construction & FrameworkHow Can You Effectively Mount a Headboard to Your Wall?
- March 18, 2025General Wood TopicsCan Bees Really Eat Wood? Unraveling the Myths and Facts
- March 18, 2025General Wood TopicsDo Rabbits Really Chew on Wood? Exploring Their Eating Habits!