How Can You Master the Art of Engraving Into Wood?
Engraving into wood is a timeless craft that marries creativity with precision, allowing artisans and hobbyists alike to transform simple wooden surfaces into stunning works of art. Whether you’re looking to personalize a gift, create a unique home decor piece, or simply explore a new hobby, understanding the techniques and tools involved in wood engraving can open up a world of possibilities. From intricate designs to bold lettering, the beauty of engraved wood lies in its ability to capture both detail and emotion, making every piece a reflection of the creator’s vision.
In this article, we will delve into the various methods of engraving wood, exploring both traditional and modern techniques. We’ll discuss the essential tools you’ll need, from handheld chisels to advanced laser engravers, and how each can impact the final outcome of your project. Additionally, we’ll touch on the types of wood best suited for engraving, as well as tips for preparing your surface to ensure crisp, clean lines that bring your designs to life.
Whether you’re a beginner eager to learn the basics or an experienced craftsman seeking to refine your skills, this guide will equip you with the knowledge needed to embark on your engraving journey. Get ready to unleash your creativity and discover the joy of turning wood into a canvas for your imagination!
Choosing the Right Tools for Wood Engraving
Selecting the appropriate tools is crucial for achieving precise and aesthetically pleasing engravings on wood. The choice of tools will largely depend on the engraving method you choose—hand engraving or machine engraving.
For hand engraving, consider the following tools:
- V-gouges: Ideal for creating sharp lines and details.
- U-gouges: Useful for wider grooves and softer edges.
- Chisels: Essential for removing larger sections of wood.
- Wood carving knives: Provide versatility for various designs.
For machine engraving, options include:
- Laser engravers: Offer high precision and can handle complex designs.
- Rotary tools: Equipped with various bits for different engraving effects.
- CNC machines: Suitable for larger projects and repetitive designs.
Preparing Your Wood Surface
Properly preparing the wood surface is essential to ensure the best results from your engraving. Follow these steps:
- Select the wood type: Softer woods like pine or basswood are easier to engrave than hardwoods like oak or maple.
- Sand the surface: Use fine-grit sandpaper (220 grit or higher) to smooth the wood and remove any rough spots.
- Clean the wood: Wipe the surface with a damp cloth to remove dust and debris. Allow it to dry completely before engraving.
- Apply a design: Transfer your design onto the wood using carbon paper or a transfer pencil.
Engraving Techniques
Engraving techniques can vary based on the tools used and the desired outcome. Here are some common methods:
Technique | Description |
---|---|
Hand Engraving | Using manual tools to carve designs directly into the wood. This method allows for a high degree of control and personalization. |
Laser Engraving | A precise method that uses a focused laser beam to burn the design into the wood. This technique is ideal for intricate patterns. |
CNC Engraving | Utilizes computer numerical control machines to automate the engraving process, ensuring uniformity and accuracy. |
Finishing Your Engraved Wood
Once the engraving is complete, it’s vital to finish the piece to enhance its appearance and protect the design. Recommended finishing steps include:
- Sanding the engraved area: Lightly sand the engraved lines to remove any splinters.
- Applying a finish: Choose between varnish, oil, or wax to seal the wood and enhance the color of the engraving.
- Buffing: Use a soft cloth to buff the surface for a smooth, polished look.
- Final inspection: Check for any imperfections or areas that need touch-ups before your project is considered complete.
By carefully selecting tools, preparing the wood surface, utilizing appropriate engraving techniques, and finishing properly, you can create beautifully engraved wooden pieces that showcase your craftsmanship.
Tools Needed for Wood Engraving
To achieve precise and detailed engravings, it’s essential to have the right tools at your disposal. Here is a list of commonly used tools:
- Dremel Rotary Tool: Versatile and suitable for various engraving tasks.
- Engraving Pen: Ideal for detailed work and fine lines.
- Laser Engraver: Offers high precision for intricate designs.
- Chisels and Gouges: Traditional tools for hand-carving and engraving.
- Sandpaper: For smoothing the surface before and after engraving.
- Clamps: To secure the wood while working.
Choosing the Right Wood
Selecting the appropriate type of wood is crucial for successful engraving. Consider the following options:
Wood Type | Characteristics | Best Uses |
---|---|---|
Basswood | Soft, easy to carve | Intricate designs |
Birch | Fine grain, holds detail well | General engraving |
Maple | Harder, smooth surface | Durable items |
Pine | Soft, affordable | Beginners’ projects |
Cedar | Pleasant aroma, easy to work with | Decorative pieces |
Preparing the Wood Surface
Before you begin engraving, proper preparation of the wood surface is essential:
- Clean the Surface: Remove dust and debris using a cloth.
- Sand the Wood: Use sandpaper to smooth the surface. Start with coarse grit and progress to fine grit.
- Mark the Design: Use a pencil or a transfer method to outline your design lightly on the wood.
Engraving Techniques
There are several techniques to consider when engraving wood, each offering different effects:
- Freehand Engraving: Involves drawing directly on the wood using an engraving tool.
- Stenciling: Use pre-made stencils to guide your engraving, ensuring consistency.
- Pyrography: A method that uses heat to burn designs into the wood.
- Laser Engraving: Utilizing a laser engraver for precise and intricate designs.
Safety Precautions
Engraving can pose certain risks; therefore, adhering to safety precautions is imperative:
- Wear Safety Goggles: Protect your eyes from flying debris.
- Use a Dust Mask: Prevent inhalation of wood dust.
- Work in a Well-Ventilated Area: Minimize exposure to fumes, especially when using power tools.
- Keep Tools Sharp: Dull tools can slip and cause injuries.
Finishing Touches
After engraving, finishing the piece enhances its appearance and durability:
- Clean the Engraved Area: Use a brush or cloth to remove dust.
- Apply Wood Finish: Consider using varnish, oil, or lacquer to protect the wood and bring out the grain.
- Polish the Surface: Buff the wood with a soft cloth for a smooth finish.
Common Mistakes to Avoid
Being aware of common pitfalls can help improve your engraving results:
- Skipping Surface Preparation: Neglecting to sand can lead to uneven engravings.
- Rushing the Process: Take your time to ensure precision and quality.
- Ignoring Tool Maintenance: Dull or dirty tools can affect the engraving quality.
Expert Insights on Engraving Techniques for Wood
Emily Carter (Master Woodworker, Artisan Crafts Journal). “When engraving into wood, it is crucial to select the right type of wood for your project. Hardwoods such as maple or oak provide a smooth surface that holds detail well, while softer woods like pine can be more forgiving but may not capture intricate designs as effectively.”
James Thompson (Laser Engraving Specialist, TechCraft Innovations). “Utilizing laser engraving technology allows for precision and versatility in designs. It is essential to adjust the settings based on the wood type to prevent charring or burning, ensuring a clean and professional finish.”
Linda Morales (DIY Enthusiast and Author, Creative Woodworking). “For those new to wood engraving, starting with hand tools like chisels and gouges can be immensely rewarding. Mastering these tools enhances your understanding of the material and improves your skills over time, making it easier to transition to more advanced techniques.”
Frequently Asked Questions (FAQs)
What tools are needed to engrave into wood?
To engrave into wood, you typically need a wood engraving tool, such as a rotary tool or a laser engraver. Additional supplies may include clamps to secure the wood, safety goggles, and a dust mask for protection.
What types of wood are best for engraving?
Softwoods like pine, cedar, and basswood are ideal for engraving due to their ease of carving. However, hardwoods such as maple and cherry can also be used, providing a more durable finish but requiring more effort.
Can I engrave on treated or painted wood?
Engraving on treated or painted wood is possible, but it may require additional preparation. Sanding the surface to remove the finish can help achieve a cleaner engraving, ensuring better adhesion and visibility.
How deep should I engrave into the wood?
The depth of the engraving depends on the desired effect. Generally, a depth of 1/16 inch to 1/8 inch is sufficient for most designs, providing a noticeable contrast without compromising the structural integrity of the wood.
Is it necessary to use a stencil for engraving?
Using a stencil is not mandatory but can greatly enhance precision and consistency in your engraving. Stencils help guide the engraving tool, especially for intricate designs or lettering.
What safety precautions should I take while engraving wood?
When engraving wood, always wear safety goggles to protect your eyes from flying debris. A dust mask is also recommended to avoid inhaling wood dust. Additionally, ensure your workspace is well-ventilated and free from flammable materials.
Engraving into wood is a rewarding craft that allows individuals to create personalized and decorative items. The process typically involves selecting the right tools, such as rotary engravers, laser engravers, or hand tools, depending on the desired effect and intricacy of the design. Understanding the type of wood being used is crucial, as different woods have varying densities and grain patterns that can affect the engraving outcome. Proper preparation of the wood surface, including sanding and cleaning, ensures a smooth finish and enhances the quality of the engraving.
Additionally, planning the design is a significant step in the engraving process. Utilizing templates or stencils can help achieve precision, especially for intricate designs. For those using laser engravers, software programs can assist in creating and modifying designs before transferring them onto the wood. It is also essential to consider safety precautions, such as wearing protective gear and ensuring proper ventilation when using power tools or chemicals.
engraving into wood combines artistry with technical skill. By selecting appropriate tools, preparing the wood properly, and carefully planning the design, anyone can create beautiful engraved pieces. This craft not only allows for creativity but also provides an opportunity to produce unique gifts or home decor items that carry personal significance.
Author Profile
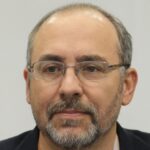
-
Darryl Norman is a seasoned entrepreneur and industry expert with a deep understanding of wood truss manufacturing and construction materials. As the President of Timberlake TrussWorks, LLC, Darryl played a pivotal role in shaping the company’s reputation for quality and precision. His leadership ensured that each truss met rigorous structural standards, providing builders with dependable components essential to their projects.
Beginning in 2025, Darryl Norman has shifted his focus to education and knowledge-sharing through an informative blog dedicated to wood truss manufacturing. Drawing from his extensive experience in the field, he provides in-depth insights into truss design, material selection, and construction techniques. This blog serves as a valuable resource for builders, contractors, and homeowners seeking practical guidance on truss systems and structural integrity.
Latest entries
- March 18, 2025General Wood TopicsWhat Color Is Ebony Wood? Unveiling the Rich Hues of This Luxurious Timber
- March 18, 2025Construction & FrameworkHow Can You Effectively Mount a Headboard to Your Wall?
- March 18, 2025General Wood TopicsCan Bees Really Eat Wood? Unraveling the Myths and Facts
- March 18, 2025General Wood TopicsDo Rabbits Really Chew on Wood? Exploring Their Eating Habits!