How Can You Successfully Epoxy Live Edge Wood for a Stunning Finish?
Epoxy resin has transformed the world of woodworking, offering artisans and DIY enthusiasts alike the ability to create stunning, one-of-a-kind pieces. Among the most popular applications is the use of epoxy with live edge wood, where the natural contours and beauty of the wood are preserved and enhanced. Whether you’re crafting a unique tabletop, a striking river table, or decorative art pieces, learning how to epoxy live edge wood can elevate your projects to new heights. In this article, we will explore the essential techniques, materials, and tips to help you master this captivating craft.
When it comes to working with live edge wood, the combination of natural beauty and epoxy resin creates a striking visual effect that captures the essence of nature. The process involves selecting the right type of wood, preparing the surface, and carefully mixing and pouring the epoxy to fill voids and cracks. Understanding the properties of epoxy, including curing times and color options, is crucial for achieving the desired results. This overview will guide you through the foundational steps while igniting your creativity to experiment with different styles and finishes.
As you embark on your journey into the world of epoxy and live edge wood, you’ll discover the joy of transforming raw materials into functional art. From the initial preparation to the final finishing touches, each step
Preparing the Wood
To successfully epoxy live edge wood, the first step involves meticulous preparation of the wood surface. This ensures that the epoxy adheres properly and results in a smooth, aesthetically pleasing finish. The key steps in preparation include:
- Cleaning: Remove any dust, dirt, or debris from the wood surface. This can be done using a vacuum or a damp cloth.
- Sanding: Sand the surface with progressively finer grits of sandpaper, typically starting with 80-grit and moving up to 220-grit. This creates a smooth surface for the epoxy to bond.
- Sealing: If the wood is particularly porous or has cracks, consider sealing it with a thin layer of epoxy or a wood sealer. This prevents air bubbles from forming in the epoxy.
Choosing the Right Epoxy
The selection of the appropriate epoxy resin is critical for achieving the desired finish. Epoxy resins come in various formulations, and understanding these can aid in making the right choice. Consider the following factors:
- Viscosity: Choose a low-viscosity epoxy for deep pours, as it will flow better into cracks and voids.
- Curing Time: Depending on your project timeline, select an epoxy with a suitable curing time, ranging from fast to slow curing.
- UV Resistance: For projects exposed to sunlight, opt for a UV-resistant epoxy to prevent yellowing over time.
Type of Epoxy | Viscosity | Curing Time | UV Resistance |
---|---|---|---|
General Purpose | Medium | 24 hours | No |
Low Viscosity | Low | 48 hours | Yes |
Fast Cure | Medium | 4-6 hours | No |
Mixing the Epoxy
Proper mixing of the epoxy resin and hardener is essential for achieving optimal results. Follow these guidelines:
- Follow Instructions: Always adhere to the manufacturer’s instructions regarding the mixing ratio, which is typically 1:1 or 2:1.
- Use a Clean Container: Mix the components in a clean, dry container to avoid contamination.
- Mix Thoroughly: Stir the mixture for at least 3-5 minutes, scraping the sides and bottom of the container to ensure complete integration.
Pouring the Epoxy
Once the epoxy is mixed, it’s time to pour it onto the prepared live edge wood. The following tips will help ensure an even application:
- Create a Dam: If the wood has significant voids, create a dam using painter’s tape or plastic sheeting around the edges to contain the epoxy.
- Pour Slowly: Start pouring the epoxy at one end and allow it to flow over the surface. This minimizes air bubble formation.
- Use a Heat Gun: To help eliminate any surface bubbles, gently wave a heat gun over the epoxy after pouring.
Finishing Touches
After the epoxy has cured, finishing touches are necessary to achieve a polished look. This involves:
- Sanding: Once fully cured, sand the surface with fine-grit sandpaper (400-grit) for a smooth finish.
- Polishing: Apply a polishing compound to enhance the shine.
- Applying a Topcoat: If desired, a clear topcoat can be applied for additional protection and luster.
Preparing the Wood Surface
Proper preparation of the wood surface is crucial for achieving a successful epoxy finish. Follow these steps:
- Clean the Surface: Remove any dirt, dust, or debris. Use a vacuum and a damp cloth to ensure the surface is clean.
- Sand the Wood: Sand the live edge wood with progressively finer grits (starting from 80-grit to 220-grit) to create a smooth surface.
- Remove Dust: After sanding, remove dust using a tack cloth or compressed air to avoid imperfections in the epoxy.
Selecting the Right Epoxy Resin
Choosing the appropriate epoxy resin is essential for durability and aesthetics. Consider the following factors:
- Type of Epoxy: Use a clear casting epoxy for a glass-like finish.
- Cure Time: Select a resin based on your project timeline; fast-curing epoxies set quickly but may generate heat.
- UV Resistance: Opt for UV-resistant formulas to prevent yellowing over time.
Property | Fast-Curing Epoxy | Slow-Curing Epoxy | UV Resistant |
---|---|---|---|
Cure Time | 1-4 hours | 24-72 hours | Yes |
Heat Generation | High | Low | Variable |
Clarity | Clear | Clear | Yes |
Mixing the Epoxy
Accurate mixing of the epoxy is vital for optimal results. Follow these guidelines:
- Use a Clean Mixing Container: Avoid contamination by using a clean, dry container.
- Follow Ratio Instructions: Adhere to the manufacturer’s mix ratio (usually 1:1 or 2:1).
- Mix Thoroughly: Stir the mixture slowly and thoroughly for at least 3-5 minutes, scraping the sides and bottom of the container to ensure a uniform mixture.
Pouring the Epoxy
Pouring the epoxy requires precision to avoid bubbles and ensure even coverage. Follow these steps:
- Apply a Seal Coat: Pour a thin seal coat first to fill any pores in the wood. This prevents air bubbles from escaping.
- Use a Heat Gun: After pouring, gently wave a heat gun over the surface to eliminate bubbles that may rise.
- Layering: If applying multiple layers, allow each layer to cure as per the manufacturer’s instructions before applying the next.
Finishing Touches
Once the epoxy has cured, finishing touches can enhance the final appearance:
- Sand the Surface: Lightly sand the cured epoxy with fine-grit sandpaper (400-grit or higher) to smooth any imperfections.
- Polish: Use a polishing compound and a soft cloth to bring out a high-gloss finish.
- Seal the Edges: Consider applying a wood finish or sealant to the edges of the wood to protect against moisture.
Maintaining Epoxy Coated Wood
To maintain the appearance and longevity of your epoxy-coated wood, follow these maintenance tips:
- Clean Regularly: Use a soft, damp cloth to clean the surface, avoiding harsh chemicals.
- Avoid Direct Sunlight: Position the piece away from direct sunlight to minimize UV damage.
- Repair Scratches Promptly: For minor scratches, sand lightly and reapply a small amount of epoxy to restore the finish.
Expert Insights on Epoxy Techniques for Live Edge Wood
Emily Carter (Woodworking Specialist, Artisan’s Journal). “When working with live edge wood, it’s essential to choose a high-quality epoxy that not only enhances the natural beauty of the wood but also provides durability. I recommend using a clear epoxy resin to maintain the organic look while ensuring a strong bond.”
Michael Thompson (Furniture Designer, EcoWood Designs). “Preparation is key when epoxy filling live edge wood. Make sure the wood is completely dry and free from dust. I often suggest sealing the edges with painter’s tape to prevent any overflow of epoxy, which can ruin the aesthetic.”
Sarah Jenkins (Restoration Expert, Vintage Woodworks). “Applying epoxy in layers can significantly improve the finish. For deep cracks or voids, pour in thin layers, allowing each to cure before adding the next. This technique not only ensures a smooth surface but also minimizes the risk of bubbles forming.”
Frequently Asked Questions (FAQs)
What materials do I need to epoxy live edge wood?
To epoxy live edge wood, you will need epoxy resin, hardener, mixing cups, stir sticks, gloves, a heat gun or torch, clamps, and sandpaper. Optionally, you may also want a vacuum chamber to eliminate air bubbles.
How do I prepare the wood before applying epoxy?
Preparation involves cleaning the wood surface thoroughly to remove dust and debris, ensuring it is dry, and possibly sealing the edges with a thin layer of epoxy to prevent seepage. Sanding the surface can also help the epoxy adhere better.
What is the best type of epoxy to use for live edge wood projects?
A clear, two-part epoxy resin specifically designed for woodworking is ideal. Look for products that offer UV resistance and low viscosity to ensure proper flow and clarity.
How long does it take for epoxy to cure on live edge wood?
Curing time varies based on the epoxy brand and environmental conditions, but typically, it takes 24 to 72 hours to cure fully. Always refer to the manufacturer’s instructions for specific curing times.
Can I color the epoxy for my live edge wood project?
Yes, you can add color to epoxy using pigments or dyes designed for resin. Ensure that the color additives are compatible with the epoxy to maintain clarity and adhesion.
What are common mistakes to avoid when epoxying live edge wood?
Common mistakes include not properly sealing the wood, mixing the epoxy incorrectly, applying too thick a layer, and failing to eliminate air bubbles. Additionally, working in a humid or cold environment can affect curing.
epoxy resin is a popular choice for enhancing the beauty and durability of live edge wood projects. The process begins with selecting high-quality wood that showcases natural features, followed by preparing the wood surface to ensure proper adhesion of the epoxy. It is essential to clean and sand the wood thoroughly, as this will help achieve a smooth finish and prevent imperfections in the final product.
Once the wood is prepared, the next step involves mixing the epoxy resin according to the manufacturer’s instructions. Careful measurement and mixing are crucial to avoid issues such as bubbles or improper curing. Pouring the epoxy into the desired areas, especially where there are cracks or voids, requires patience and precision to ensure an even distribution and a flawless appearance.
After pouring, allowing the epoxy to cure fully is vital before any further finishing work is done. This may include sanding, polishing, and applying a protective topcoat to enhance the wood’s aesthetic and durability. By following these steps, one can create stunning live edge wood pieces that are not only visually appealing but also functional and long-lasting.
Key takeaways from the discussion include the importance of proper preparation and mixing techniques, as well as the need for patience during the curing process. Understanding these elements
Author Profile
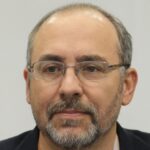
-
Darryl Norman is a seasoned entrepreneur and industry expert with a deep understanding of wood truss manufacturing and construction materials. As the President of Timberlake TrussWorks, LLC, Darryl played a pivotal role in shaping the company’s reputation for quality and precision. His leadership ensured that each truss met rigorous structural standards, providing builders with dependable components essential to their projects.
Beginning in 2025, Darryl Norman has shifted his focus to education and knowledge-sharing through an informative blog dedicated to wood truss manufacturing. Drawing from his extensive experience in the field, he provides in-depth insights into truss design, material selection, and construction techniques. This blog serves as a valuable resource for builders, contractors, and homeowners seeking practical guidance on truss systems and structural integrity.
Latest entries
- March 18, 2025General Wood TopicsWhat Color Is Ebony Wood? Unveiling the Rich Hues of This Luxurious Timber
- March 18, 2025Construction & FrameworkHow Can You Effectively Mount a Headboard to Your Wall?
- March 18, 2025General Wood TopicsCan Bees Really Eat Wood? Unraveling the Myths and Facts
- March 18, 2025General Wood TopicsDo Rabbits Really Chew on Wood? Exploring Their Eating Habits!