How Can You Effectively Fix Cupped Wood Floors?
Wood floors are a timeless choice for homeowners, exuding warmth and elegance that can enhance any living space. However, even the most beautiful hardwood can fall victim to environmental factors, leading to a common issue known as cupping. This phenomenon occurs when the edges of the floorboards rise higher than the center, creating a wavy appearance that can detract from the overall aesthetic of your home. Understanding how to fix wood floor cupping is essential not only for restoring the beauty of your floors but also for preserving their longevity.
Cupping is often a result of excessive moisture, whether from humidity in the air, spills, or water leaks. When wood absorbs too much moisture, it expands unevenly, leading to the characteristic cupped shape. While it can be disheartening to see your once-flawless floors in such a state, the good news is that there are effective strategies to address this issue. From identifying the underlying causes to implementing corrective measures, homeowners can take proactive steps to restore their wood floors to their former glory.
In this article, we will explore the various methods to fix wood floor cupping, including preventive measures to avoid future occurrences. By understanding the root causes and applying the right solutions, you can ensure that your hardwood floors remain a stunning centerpiece in your
Understanding the Causes of Cupping
Cupping in wood floors occurs when the edges of the boards are higher than the center, resulting in a concave shape. This issue can arise from various factors, primarily related to moisture levels. Understanding these causes is essential for addressing the problem effectively.
- Excessive Moisture: High humidity or water leaks can cause wood to absorb moisture, leading to cupping.
- Temperature Fluctuations: Rapid changes in temperature can also impact moisture levels in wood.
- Improper Installation: Inadequate acclimatization of flooring before installation can result in uneven moisture levels.
- Subfloor Issues: Moisture from below the flooring, such as from a damp subfloor, can contribute to the issue.
Steps to Fix Wood Floor Cupping
Addressing cupping requires a systematic approach to minimize moisture levels and restore the wood’s original shape. Follow these steps:
- Identify and Eliminate Moisture Sources:
- Inspect for leaks in plumbing or roofs.
- Ensure proper ventilation in areas like basements or crawl spaces.
- Use dehumidifiers to manage humidity levels.
- Drying the Wood:
- Allow the wood to dry naturally by removing any excess moisture. This may take several days to weeks, depending on the severity of the cupping and humidity levels.
- Consider using fans or a combination of heating and dehumidification to accelerate the drying process.
- Sanding the Surface:
- Once the wood is adequately dried, sanding may be necessary to level the surface. Use a floor sander and start with coarse-grit sandpaper, progressively moving to finer grits.
- Always follow with a thorough vacuuming to remove dust particles.
- Reapplication of Finish:
- After sanding, reapply the wood finish to protect the surface. This may involve staining followed by several coats of polyurethane or other sealants.
- Regular Maintenance:
- Maintain consistent humidity levels in your home between 30-50% to prevent future cupping.
Prevention Strategies
Taking preventive measures can reduce the risk of cupping in wood floors. Consider the following strategies:
- Acclimate New Flooring: Allow new wood to acclimate to the home’s environment before installation.
- Control Indoor Humidity: Use humidifiers or dehumidifiers as needed to maintain stable humidity levels.
- Seal and Finish: Regularly apply sealants and finishes to protect the wood from moisture.
- Monitor Subfloor Conditions: Ensure that the subfloor is dry and well-ventilated, especially in basements.
Moisture Source | Mitigation Technique |
---|---|
Leaks | Repair plumbing and roofing issues |
High Humidity | Use dehumidifiers and ensure proper ventilation |
Improper Installation | Ensure proper acclimatization and installation techniques |
Damp Subfloor | Improve subfloor drainage and moisture barriers |
By following these steps and strategies, homeowners can effectively address and prevent wood floor cupping, ensuring the longevity and aesthetic appeal of their flooring.
Understanding Wood Floor Cupping
Wood floor cupping occurs when the edges of the boards are higher than the center, leading to a concave appearance. This issue often arises from moisture imbalance, commonly due to excessive humidity or water exposure. Recognizing the causes is crucial in addressing and preventing further damage.
Identifying the Causes
To effectively fix cupping, it’s important to determine the underlying causes. Common reasons include:
- High Humidity: Excessive moisture in the air can lead to absorption by the wood.
- Water Damage: Spills, leaks, or flooding can introduce water, causing swelling.
- Poor Installation: Inadequate acclimation or improper installation techniques can lead to uneven moisture absorption.
- Subfloor Issues: Moisture from the subfloor can migrate to the hardwood, leading to cupping.
Immediate Steps to Address Cupping
Taking immediate action can help mitigate further damage. Follow these steps:
- Identify Moisture Sources: Check for leaks, spills, or high humidity levels.
- Reduce Humidity: Use dehumidifiers or air conditioners to lower indoor humidity.
- Improve Ventilation: Increase airflow in the area to facilitate moisture evaporation.
- Dry the Floor: Use fans to help dry out the wood, especially after water exposure.
Long-term Solutions
Implementing long-term strategies can prevent recurrence of cupping. Consider the following methods:
- Control Indoor Climate: Maintain a stable humidity level between 30% and 50%.
- Proper Sealing: Apply sealants or finishes to the wood to protect against moisture.
- Regular Maintenance: Periodically check for leaks and address them immediately.
Repairing Cupped Floors
If cupping persists despite preventive measures, repairs may be necessary. Options include:
Repair Method | Description |
---|---|
Sanding | Sand down the edges of the boards to create a level surface. |
Refinishing | After sanding, apply a new finish to restore the wood’s appearance and provide additional protection. |
Replacement | In severe cases, replacing damaged boards may be necessary to ensure structural integrity and aesthetics. |
Preventive Measures
To prevent future cupping issues, consider these strategies:
- Acclimate Wood: Allow new wood to adjust to the environment before installation.
- Use Vapor Barriers: Install moisture barriers in areas prone to high humidity or moisture.
- Regular Inspections: Conduct routine checks for moisture levels and wood condition to catch issues early.
Consulting Professionals
If cupping persists despite your efforts, consulting a flooring professional may be necessary. Experts can provide tailored solutions based on specific conditions and materials involved. They can also recommend further assessments for underlying issues, such as subfloor moisture levels.
Expert Strategies for Addressing Wood Floor Cupping
Dr. Emily Carter (Wood Flooring Specialist, Timber Solutions Inc.). “To effectively address wood floor cupping, it is crucial to first identify the underlying moisture issue. This may involve checking for leaks or high humidity levels in the environment. Once the source is resolved, allowing the wood to acclimate to the proper humidity levels can help restore its original shape.”
James Thompson (Certified Flooring Installer, FloorCraft Experts). “In cases of severe cupping, sanding down the affected areas may be necessary to achieve a level surface. However, this should be done with caution, as over-sanding can damage the wood. It is advisable to consult with a professional to determine the best course of action for your specific flooring type.”
Linda Martinez (Home Improvement Consultant, Renovate Right). “Preventive measures are key to avoiding wood floor cupping. Regularly monitoring indoor humidity levels and using dehumidifiers in damp areas can significantly reduce the risk. Additionally, ensuring proper installation techniques, such as leaving adequate expansion gaps, can help maintain the integrity of the flooring over time.”
Frequently Asked Questions (FAQs)
What causes wood floor cupping?
Cupping occurs when the edges of the wood planks rise higher than the center, typically due to moisture imbalance. This can result from excessive humidity, water leaks, or improper installation.
How can I prevent wood floor cupping?
To prevent cupping, maintain consistent humidity levels in your home, use dehumidifiers if necessary, and ensure proper ventilation. Additionally, avoid water exposure and promptly address any leaks.
What are the steps to fix cupped wood floors?
To fix cupped wood floors, first reduce the humidity in the environment. Allow the wood to acclimate to the correct moisture levels. If necessary, sanding may be required to level the surface once the wood has dried.
Can I fix cupped floors myself, or should I hire a professional?
Minor cupping can often be addressed by homeowners through humidity control and acclimation. However, significant cupping or extensive damage may require professional assessment and repair.
Is cupping reversible?
Yes, cupping can be reversible if the underlying moisture issue is resolved and the wood is allowed to dry properly. In some cases, sanding may be needed to restore the floor’s appearance.
How long does it take for cupped wood floors to return to normal?
The time it takes for cupped wood floors to return to normal varies based on humidity levels and the extent of the cupping. It can take anywhere from a few days to several weeks for the wood to acclimate and flatten out.
In summary, addressing wood floor cupping requires a thorough understanding of its causes and effective remediation strategies. Cupping typically occurs due to moisture imbalance, where the edges of the planks absorb more moisture than the center, leading to a raised appearance. Identifying the source of excess moisture is crucial, as it may stem from high humidity, water leaks, or improper installation. Once the source is addressed, the next step involves drying out the affected area to restore the wood to its original shape.
Key takeaways include the importance of maintaining consistent humidity levels in your home, ideally between 30% and 50%. Utilizing dehumidifiers or humidifiers can help regulate moisture levels effectively. Additionally, ensuring proper ventilation in areas prone to moisture, such as basements or bathrooms, is vital in preventing future occurrences of cupping. Regular maintenance and monitoring of your wood floors will also aid in early detection of potential issues.
Ultimately, while wood floor cupping can be a concerning issue, it is manageable with the right approach. Engaging professional help may be necessary for severe cases, especially when structural damage is involved. By taking proactive measures and implementing effective solutions, homeowners can preserve the beauty and integrity of their wood floors for years to come
Author Profile
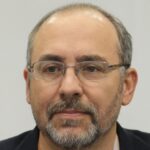
-
Darryl Norman is a seasoned entrepreneur and industry expert with a deep understanding of wood truss manufacturing and construction materials. As the President of Timberlake TrussWorks, LLC, Darryl played a pivotal role in shaping the company’s reputation for quality and precision. His leadership ensured that each truss met rigorous structural standards, providing builders with dependable components essential to their projects.
Beginning in 2025, Darryl Norman has shifted his focus to education and knowledge-sharing through an informative blog dedicated to wood truss manufacturing. Drawing from his extensive experience in the field, he provides in-depth insights into truss design, material selection, and construction techniques. This blog serves as a valuable resource for builders, contractors, and homeowners seeking practical guidance on truss systems and structural integrity.
Latest entries
- March 18, 2025General Wood TopicsWhat Color Is Ebony Wood? Unveiling the Rich Hues of This Luxurious Timber
- March 18, 2025Construction & FrameworkHow Can You Effectively Mount a Headboard to Your Wall?
- March 18, 2025General Wood TopicsCan Bees Really Eat Wood? Unraveling the Myths and Facts
- March 18, 2025General Wood TopicsDo Rabbits Really Chew on Wood? Exploring Their Eating Habits!