How Can You Successfully Ingrave Wood: A Step-by-Step Guide?
How To Engrave Wood?
Engraving wood is a captivating art form that transforms simple pieces of timber into stunning works of art. Whether you’re looking to personalize a gift, create a unique piece of home decor, or simply explore a new hobby, mastering the techniques of wood engraving can open up a world of creativity. With the right tools and a bit of practice, you can turn your ideas into beautifully detailed designs that showcase your individuality and craftsmanship.
In this article, we will delve into the essentials of wood engraving, covering everything from the types of tools you’ll need to the various techniques that can bring your designs to life. We’ll explore the differences between hand engraving and using modern technology, such as laser engraving, to help you choose the best method for your project. Whether you’re a beginner eager to learn the basics or an experienced artisan looking to refine your skills, understanding the nuances of this craft will set you on the path to creating breathtaking engraved wood pieces.
Join us as we embark on a journey through the enchanting world of wood engraving, where imagination meets craftsmanship, and discover how you can transform ordinary wood into extraordinary art. Get ready to unleash your creativity and make your mark on this timeless medium!
Choosing the Right Tools for Wood Engraving
Selecting the appropriate tools for wood engraving is crucial to achieving precision and quality in your work. Various tools are available, each catering to different techniques and desired outcomes. Here are some common options:
- Wood Burning Tool: Ideal for creating intricate designs and shading, this tool uses heat to burn the wood surface, allowing for fine details.
- Dremel Rotary Tool: This versatile tool can be fitted with various bits for engraving, cutting, and sanding. It is suitable for both detailed work and larger designs.
- Chisels and Gouges: Hand tools that provide control and are excellent for traditional carving techniques. They come in different shapes and sizes for various effects.
- Laser Engraver: For precision and speed, a laser engraver can etch complex designs into wood with high accuracy. This method is ideal for mass production or detailed projects.
When selecting your tools, consider the type of wood you will be engraving, as harder woods may require more robust tools.
Preparing the Wood Surface
Before engraving, proper preparation of the wood surface is essential. This ensures that the design adheres well and that the finished product looks polished. Follow these steps for optimal preparation:
- Choose the Right Wood: Softwoods such as pine are easier to engrave, while hardwoods like oak provide a more durable finish.
- Sand the Surface: Use fine-grit sandpaper (220 grit or higher) to smooth the wood. This removes any imperfections that could affect the engraving.
- Clean the Surface: Wipe the wood with a damp cloth to remove dust and debris, allowing for a clearer engraving.
- Apply a Base Coat (Optional): For certain designs, applying a thin coat of paint or stain can enhance contrast in the engraving.
Engraving Techniques
Engraving wood can be achieved through several techniques, each yielding different results. Here are some common methods:
- V-Carving: This technique uses a V-shaped bit to create grooves in the wood, allowing for detailed lettering and graphics.
- Relief Engraving: This involves carving away the background wood, leaving the design raised. It can add depth and texture to the piece.
- Deep Engraving: This method requires more force and can create bold designs that stand out significantly from the wood surface.
Technique | Best For | Tool Required |
---|---|---|
V-Carving | Detailed lettering and intricate designs | V-Bit |
Relief Engraving | Textured designs | Chisels or Rotary Tool |
Deep Engraving | Bold designs and patterns | Rotary Tool or Laser Engraver |
Finishing Touches After Engraving
Once the engraving is complete, adding finishing touches can enhance the overall appearance and longevity of the piece. Consider the following steps:
- Sanding Again: Lightly sand the engraved areas to remove any rough edges or burn marks from the engraving process.
- Staining or Painting: Apply stain or paint to emphasize the engraved design. Ensure the stain is compatible with the wood type and desired effect.
- Sealing: Use a clear wood finish or sealant to protect the wood and engraving from moisture and wear. This step is crucial for maintaining the quality of the piece over time.
By following these steps, you can achieve professional results in your wood engraving projects, ensuring both beauty and durability.
Choosing the Right Tools for Wood Engraving
Selecting appropriate tools is crucial for achieving precise and aesthetically pleasing wood engravings. The following tools are commonly used in the wood engraving process:
- Engraving Tools:
- Burins: These are traditional tools with a sharp point for fine detail work.
- Rotary Tools: Devices like Dremel can be used with various bits for different engraving effects.
- Laser Engravers: Provide high precision and are suitable for complex designs.
- Cutting Mats: Protect your work surface and ensure the longevity of your tools.
- Clamps: Secure the wood piece firmly while you work.
- Rulers and Templates: Ensure accuracy in your designs and measurements.
Preparing the Wood Surface
Proper surface preparation enhances the quality of the engraving. Follow these steps for optimal results:
- Select the Right Wood: Softer woods like pine or basswood are easier to engrave compared to hardwoods like oak or maple.
- Sand the Surface: Use fine-grit sandpaper to create a smooth surface, removing any imperfections.
- Clean the Surface: Wipe the wood with a clean cloth to eliminate dust and debris.
Designing Your Engraving
Before engraving, it’s essential to have a clear design. Consider the following methods to create your design:
- Freehand Drawing: Sketch your design directly onto the wood using a pencil.
- Templates: Use stencils to trace your design, ensuring accuracy.
- Digital Designs: Create designs using graphic software and print them onto transfer paper.
Engraving Techniques
Engraving can be done using various techniques depending on the desired outcome. Here are some popular methods:
- V-Carving: Involves using a V-shaped bit to create deep grooves, perfect for lettering.
- Relief Engraving: This method removes material from around the design, creating a raised effect.
- Inlay Work: Combines engraving with inserting different materials into the engraved areas for contrast.
Finishing Your Engraving
Once the engraving is complete, finishing touches enhance the wood’s appearance and protect the design. Consider these steps:
- Cleaning: Remove any dust or debris from the engraving with a soft brush.
- Staining: Apply wood stain to enhance the contrast between the engraved areas and the wood.
- Sealing: Use a clear wood finish or sealant to protect the engraving and enhance durability.
Safety Precautions
Maintaining safety is paramount during the engraving process. Adhere to the following safety tips:
- Wear Protective Gear: Use safety goggles and a dust mask to protect your eyes and lungs.
- Work in a Well-Ventilated Area: Ensure proper airflow to avoid inhaling fumes from stains or finishes.
- Handle Tools Carefully: Always cut away from your body and keep tools out of reach of children.
Common Mistakes to Avoid
To ensure a successful engraving project, be mindful of these common pitfalls:
- Rushing the Process: Take your time to ensure precision and quality in your work.
- Ignoring Material Properties: Different woods have varying hardness; choose your tools accordingly.
- Neglecting Safety: Always prioritize safety by using protective equipment and maintaining a clean workspace.
Expert Insights on Wood Engraving Techniques
Dr. Emily Carter (Woodworking Specialist, Artisan’s Journal). “Engraving wood requires a careful selection of tools, such as rotary tools or laser engravers, depending on the desired intricacy and depth of the design. Understanding the type of wood is crucial, as softer woods engrave differently than hardwoods.”
James Thornton (Master Craftsman, The Woodworker’s Guild). “Preparation is key when engraving wood. Properly sanding the surface and applying a finish before engraving can significantly enhance the final appearance of the design and prevent splintering.”
Linda Nguyen (Artistic Designer, Creative Woodworks). “Incorporating different engraving techniques, such as relief engraving or deep carving, can add unique textures and dimensions to your project. Experimenting with various patterns and styles will help you find your distinct artistic voice.”
Frequently Asked Questions (FAQs)
What tools are needed to engrave wood?
To engrave wood, you will typically need a rotary tool or laser engraver, engraving bits or laser attachments, clamps to secure the wood, and safety equipment such as goggles and a dust mask.
What types of wood are best for engraving?
Softwoods like pine and cedar are easier to engrave and produce cleaner results. Hardwoods such as oak and maple can also be engraved but may require more advanced tools and techniques.
Can I engrave wood by hand?
Yes, wood can be engraved by hand using tools such as chisels, knives, or wood burning pens. This method requires skill and patience but allows for intricate designs.
How do I prepare wood for engraving?
Prepare the wood by sanding it to a smooth finish, removing dust and debris, and ensuring it is free of any finishes or coatings that could interfere with the engraving process.
What design techniques are effective for wood engraving?
Effective design techniques include using contrasting colors, incorporating textures, and selecting designs that complement the natural grain of the wood. Simple, bold designs often yield the best results.
Is it necessary to seal wood after engraving?
Sealing wood after engraving is recommended to protect the design and enhance the wood’s appearance. A clear finish, such as polyurethane or varnish, can help preserve the engraved details.
engraving wood is a versatile and rewarding craft that allows for the personalization of various wooden items. The process typically involves selecting the appropriate tools, such as rotary tools, laser engravers, or hand chisels, depending on the desired outcome and the intricacy of the design. Proper preparation of the wood surface is crucial, as it ensures better adherence of the engraving and enhances the final appearance of the work. Additionally, choosing the right type of wood can significantly impact the quality of the engraving, with softer woods often being easier to work with for detailed designs.
Moreover, understanding the techniques involved in engraving, such as controlling depth and speed, is essential for achieving precision. Practicing on scrap pieces of wood can help engravers refine their skills before working on final projects. Safety precautions, including protective eyewear and proper ventilation, should not be overlooked, especially when using power tools or chemicals in the finishing process.
Ultimately, engraving wood not only serves as a means of artistic expression but also allows for the creation of unique gifts and home decor. By mastering the techniques and tools involved, anyone can transform simple wooden items into cherished keepsakes. Embracing this craft can lead to a fulfilling hobby or even a potential business venture,
Author Profile
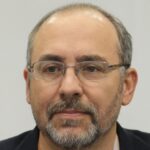
-
Darryl Norman is a seasoned entrepreneur and industry expert with a deep understanding of wood truss manufacturing and construction materials. As the President of Timberlake TrussWorks, LLC, Darryl played a pivotal role in shaping the company’s reputation for quality and precision. His leadership ensured that each truss met rigorous structural standards, providing builders with dependable components essential to their projects.
Beginning in 2025, Darryl Norman has shifted his focus to education and knowledge-sharing through an informative blog dedicated to wood truss manufacturing. Drawing from his extensive experience in the field, he provides in-depth insights into truss design, material selection, and construction techniques. This blog serves as a valuable resource for builders, contractors, and homeowners seeking practical guidance on truss systems and structural integrity.
Latest entries
- March 18, 2025General Wood TopicsWhat Color Is Ebony Wood? Unveiling the Rich Hues of This Luxurious Timber
- March 18, 2025Construction & FrameworkHow Can You Effectively Mount a Headboard to Your Wall?
- March 18, 2025General Wood TopicsCan Bees Really Eat Wood? Unraveling the Myths and Facts
- March 18, 2025General Wood TopicsDo Rabbits Really Chew on Wood? Exploring Their Eating Habits!