How Can You Create Your Own Branding Iron for Wood?
Creating a unique branding iron for wood is a fantastic way to add a personal touch to your woodworking projects, whether you’re a hobbyist or a professional craftsman. Imagine the satisfaction of marking your creations with a custom logo, initials, or a special design that reflects your style and craftsmanship. Not only does a branding iron elevate the aesthetic appeal of your work, but it also serves as a signature, ensuring that your pieces stand out in a sea of mass-produced items. In this article, we will explore the fascinating process of making your own branding iron, from the materials you’ll need to the techniques that will bring your vision to life.
To embark on this creative journey, it’s essential to understand the basic principles behind branding irons. These tools typically consist of a metal stamp heated to a high temperature, which leaves a lasting impression on wood surfaces. The process involves selecting the right materials, designing your branding stamp, and mastering the heating method that will ensure a crisp and clear imprint. Whether you opt for a simple design or something more intricate, the steps you take will be crucial in achieving the desired outcome.
As we delve deeper into the topic, we’ll cover the various options available for crafting your branding iron, including DIY methods and commercially available tools. You’ll learn about the importance of choosing the right
Choosing the Right Materials
Selecting appropriate materials is crucial for creating a durable branding iron. The main components you will need include:
- Metal Rod: A steel rod is commonly used for the handle and branding head due to its strength and heat retention.
- Brass or Copper: These metals are often used for the branding head because they can withstand high temperatures and hold detail well.
- Wood for Handle: A sturdy hardwood like oak or maple can provide a comfortable grip and absorb heat from the metal.
Consider the following characteristics when selecting your materials:
Material | Properties | Best Use |
---|---|---|
Steel | Durable, heat-resistant | Handle and core structure |
Brass | Good heat conductor, easy to engrave | Branding head |
Copper | Excellent heat retention | Detailed branding designs |
Hardwood | Comfortable grip, absorbs heat | Handle for branding iron |
Designing the Branding Iron
Before you start shaping the iron, sketch your design. This will serve as a reference throughout the process. Keep the following tips in mind:
- Simple Designs: Start with straightforward shapes or letters, as complex designs may be challenging to execute.
- Size: Ensure your branding head is proportionate to the items you will be branding.
- Mirror Image: Remember that your design will be reversed when stamped, so make adjustments as necessary.
Utilize design software or graph paper to draft your concept, allowing for precise measurements and scaling.
Shaping the Branding Head
Once you have your materials and design, you can begin shaping the branding head. This process typically involves the following steps:
- Cut the Metal: Using a metal saw, cut the brass or copper into the desired shape according to your design.
- File and Smooth: Employ a metal file to smooth the edges and refine the design. This is crucial for achieving clean lines.
- Welding (if necessary): If your design includes multiple elements, use a welding tool to secure them together.
Attaching the Handle
To attach the handle to the branding head securely, follow these steps:
- Drill Holes: Drill a hole into the branding head and the metal rod for the handle.
- Insert and Secure: Insert the metal rod into the branding head and use a pin or screw to hold them together. This ensures stability during use.
Testing the Branding Iron
Before using your branding iron on actual projects, conduct a test run. Follow these steps:
- Heat the Iron: Use a propane torch or place the iron in a forge until it reaches a red-hot temperature.
- Test on Scrap Wood: Press the branding head onto a piece of scrap wood to check for clarity and detail.
Adjust the temperature and pressure as necessary to achieve the best results.
Remember, crafting a branding iron is an art that requires patience and precision. Each step contributes to the final quality of your branding tool.
Materials Needed for a Branding Iron
Creating a branding iron involves selecting the right materials to ensure durability and effectiveness. The following components are essential:
- Metal Rod: A steel or iron rod, approximately 1/2 inch in diameter, serves as the handle.
- Metal Plate: A piece of brass or steel for the branding head, typically around 1/4 inch thick.
- Design Template: A sketch or digital design of the branding mark you wish to create.
- Heat Source: A propane torch, furnace, or electric heating element to heat the branding iron.
- Safety Gear: Gloves, goggles, and a heat-resistant surface to work on.
Designing Your Branding Iron
When designing the branding mark, consider the following steps:
- Select a Design: Choose a logo, initials, or a symbol that represents your brand.
- Size and Proportion: Determine the size of the branding iron; common dimensions range from 2 to 4 inches in width.
- Create a Template: Draw your design on paper or use graphic design software. Ensure it is in reverse for accurate branding.
- Transfer to Metal: Use carbon paper to transfer the design onto the metal plate.
Fabricating the Branding Iron
The fabrication process involves several steps:
- Cutting the Metal: Use a metal saw to cut the metal plate into the desired shape, based on your template.
- Shaping the Design: Employ a grinder or file to carve out the design into the metal plate. Ensure edges are smooth for even branding.
- Attaching the Handle: Weld or securely attach the metal rod to the branding head to create a sturdy handle.
Heating the Branding Iron
Heating the branding iron properly is crucial for effective branding. Follow these guidelines:
- Use a Suitable Heat Source: Depending on your chosen method:
- Propane Torch: Heat the branding head directly until it glows.
- Furnace: Place the iron in the furnace until it reaches the desired temperature.
- Test for Adequate Heat: Test the branding iron on a scrap piece of wood to ensure it leaves a clear mark.
Branding Technique
When ready to brand, follow these steps for optimal results:
- Prepare the Wood: Ensure the surface of the wood is clean and smooth.
- Position the Branding Iron: Align the branding iron firmly against the wood surface.
- Apply Pressure: Press down evenly and hold for 5 to 10 seconds, depending on the wood type and thickness.
- Remove and Inspect: Carefully lift the branding iron to check the quality of the imprint. Repeat if necessary.
Maintenance and Storage
Proper maintenance ensures longevity and performance of your branding iron:
- Clean After Use: Wipe off any residue with a damp cloth after each branding session.
- Storage: Store the iron in a dry place to prevent rusting.
- Inspect Regularly: Check for any damage or wear before each use to ensure optimal branding quality.
Expert Insights on Crafting a Branding Iron for Wood
Emily Carter (Master Woodworker and Author of “The Art of Wood Branding”). “Creating a branding iron for wood requires precision in design and execution. I recommend starting with a clear sketch of your logo or initials, ensuring that the dimensions fit well with the size of the wood pieces you plan to brand. Using high-quality metal for the branding tip will ensure durability and effectiveness.”
James Thompson (Metal Fabrication Specialist, Crafting Today Magazine). “When making a branding iron, the choice of metal is crucial. I suggest using brass or steel for the branding head, as they can withstand high temperatures without warping. Additionally, ensure that the handle is made of heat-resistant material to prevent burns during use.”
Linda Martinez (DIY Enthusiast and Host of ‘Craft It Yourself’). “I believe that safety should be a top priority when crafting a branding iron. Always wear appropriate protective gear, such as gloves and goggles, when working with hot metal. Moreover, consider using a propane torch for heating the branding iron, as it provides a consistent and controllable heat source.”
Frequently Asked Questions (FAQs)
What materials are needed to make a branding iron for wood?
To create a branding iron for wood, you will need a metal rod (preferably steel), a heat source (like a propane torch or forge), a design template, and tools for shaping and finishing, such as a grinder or welding equipment.
How do I design the branding iron?
Design the branding iron by sketching your desired logo or text on paper. Transfer the design onto the metal rod using a marker or engraving tool, ensuring the design is reversed for proper branding on wood.
What is the best method to heat the branding iron?
The best method to heat the branding iron is to use a propane torch or forge. Ensure the iron reaches a glowing red heat, which is optimal for branding wood without burning it.
How do I apply the branding iron to wood?
Position the heated branding iron firmly against the wood surface for a few seconds, applying even pressure. Ensure the iron is level to achieve a consistent imprint.
How do I maintain my branding iron?
To maintain your branding iron, clean it after each use to remove any residue. Store it in a dry place to prevent rusting, and periodically check for any wear or damage that may require repairs.
Can I use a branding iron on other materials besides wood?
Yes, a branding iron can be used on other materials such as leather, cork, and certain plastics. However, the heating method and duration may vary depending on the material’s properties.
creating a branding iron for wood involves a series of well-defined steps that require careful planning and execution. The process typically begins with designing the desired brand, which can be done using graphic design software or by sketching it out by hand. Once the design is finalized, selecting the appropriate materials, such as metal for the branding head and a sturdy handle for ease of use, is crucial. The branding iron can then be fabricated using methods such as welding or casting, ensuring that the brand is durable and capable of withstanding high temperatures.
Additionally, it is important to consider the heating method for the branding iron. Options include using a propane torch, electric heating elements, or even a forge, depending on the resources available and the scale of production. Proper heating ensures that the branding iron reaches the necessary temperature to create a clear and lasting impression on wood surfaces. Safety precautions should also be prioritized during the entire process to prevent accidents and injuries.
Key takeaways from the discussion emphasize the importance of precision in both design and fabrication. A well-crafted branding iron not only enhances the aesthetic appeal of wood products but also serves as a means of identification and brand recognition. By following the outlined steps and considering the insights provided, individuals can successfully
Author Profile
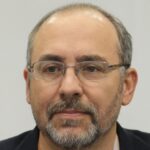
-
Darryl Norman is a seasoned entrepreneur and industry expert with a deep understanding of wood truss manufacturing and construction materials. As the President of Timberlake TrussWorks, LLC, Darryl played a pivotal role in shaping the company’s reputation for quality and precision. His leadership ensured that each truss met rigorous structural standards, providing builders with dependable components essential to their projects.
Beginning in 2025, Darryl Norman has shifted his focus to education and knowledge-sharing through an informative blog dedicated to wood truss manufacturing. Drawing from his extensive experience in the field, he provides in-depth insights into truss design, material selection, and construction techniques. This blog serves as a valuable resource for builders, contractors, and homeowners seeking practical guidance on truss systems and structural integrity.
Latest entries
- March 18, 2025General Wood TopicsWhat Color Is Ebony Wood? Unveiling the Rich Hues of This Luxurious Timber
- March 18, 2025Construction & FrameworkHow Can You Effectively Mount a Headboard to Your Wall?
- March 18, 2025General Wood TopicsCan Bees Really Eat Wood? Unraveling the Myths and Facts
- March 18, 2025General Wood TopicsDo Rabbits Really Chew on Wood? Exploring Their Eating Habits!