How Can You Craft Your Own Wooden Flute?
Crafting a wooden flute is a timeless endeavor that marries artistry with the joy of music-making. Whether you’re a seasoned woodworker or a curious beginner, the allure of creating your own instrument is both enchanting and rewarding. The rich, warm tones of a wooden flute resonate with a unique character, offering a personal touch that mass-produced instruments simply cannot replicate. In this article, we will guide you through the fascinating process of making a flute from wood, exploring the techniques, tools, and materials required to bring your musical vision to life.
Creating a wooden flute involves more than just selecting the right piece of wood; it requires an understanding of acoustics, design, and craftsmanship. From choosing the ideal type of wood to shaping the body and crafting the mouthpiece, each step plays a crucial role in determining the final sound quality. The journey of making your own flute is not only about producing music but also about connecting with the rich traditions of flute-making that span cultures and centuries.
As you delve into this creative project, you’ll discover the joy of experimentation and the satisfaction of honing your skills. Whether you aim to play soothing melodies or vibrant tunes, the process of crafting a wooden flute will deepen your appreciation for music and the art of instrument-making. Prepare to embark on
Choosing the Right Wood
Selecting the appropriate type of wood is crucial for crafting a quality flute. The wood you choose will impact the tone, durability, and overall playability of the instrument. Common types of wood used for flute making include:
- Maple: Known for its bright tone and durability.
- Cedar: Offers a warm, rich sound, often preferred for its acoustic properties.
- Walnut: Provides a darker tone, suitable for a more mellow sound.
- Birch: A good all-around choice that offers a balanced tone.
When selecting wood, consider factors such as grain structure, density, and moisture content. Ideally, the wood should be air-dried and free from knots or other defects that can affect sound quality.
Tools and Materials Required
To make a wooden flute, you will need specific tools and materials. Here is a comprehensive list:
Tool/Material | Purpose |
---|---|
Wood | The main material for the flute body. |
Chisels | For shaping the wood and creating the embouchure hole. |
Drill | To create finger holes. |
Saw | For cutting the wood to the desired length. |
Sandpaper | To smooth the surface of the flute. |
Tuner | To ensure the flute is in tune after finishing. |
Finish (oil or lacquer) | To protect the wood and enhance appearance. |
Ensure that all tools are sharp and in good condition to achieve the best results.
Shaping the Flute Body
The shaping of the flute body involves several steps. Start by cutting the wood to the desired length, which typically ranges from 20 to 26 inches for a standard flute. The length affects the pitch, with longer flutes producing lower notes.
- Mark the Embouchure Hole: This is where the player blows into the flute. Typically, the hole is located about one-third of the way from the end of the flute.
- Drill the Hole: Using a drill, create the embouchure hole, ensuring it is clean and smooth.
- Create Finger Holes: Mark where the finger holes will be placed, usually spaced evenly along the body. Drill these holes carefully, as their size and placement will affect tuning and playability.
Tuning the Flute
Once the flute is shaped and assembled, tuning is essential. This process can be meticulous, but it is vital for producing a pleasing sound.
To tune your flute:
- Begin by playing it in its current state to identify any discrepancies in pitch.
- Adjust the size of the finger holes or embouchure hole as necessary. Enlarging holes can raise the pitch, while reducing them can lower it.
- Use a tuner to ensure each note produced is accurate.
Finishing Touches
After achieving the desired tuning, apply a finish to protect the wood and enhance its appearance. Common finishes include:
- Natural oils: Such as linseed or tung oil, which penetrate the wood and provide a subtle sheen.
- Lacquer: For a more polished look, though it may alter the sound slightly due to its thickness.
Allow the finish to cure properly before playing the flute to ensure the best acoustic performance.
Choosing the Right Wood
Selecting the appropriate type of wood is crucial for crafting a flute that not only sounds good but is also durable. The wood must be dense yet lightweight, allowing for proper sound production and ease of handling. Here are some commonly used woods for flute making:
- African Blackwood: Known for its rich, warm tone and durability. It is a preferred choice for many professional flutists.
- Maple: Offers a bright, clear sound and is widely available, making it a great option for beginners.
- Bamboo: While not traditional hardwood, bamboo is an excellent choice for making flutes due to its natural acoustics and lightweight properties.
- Cherry: Known for its beautiful grain and warm sound, cherry wood is a good alternative for those seeking aesthetic appeal.
Tools and Materials Required
To construct a wooden flute, the following tools and materials are essential:
Tool/Material | Purpose |
---|---|
Wood (chosen type) | Base material for the flute |
Saw | Cutting the wood to size |
Drill | Creating finger holes and embouchure hole |
Sandpaper | Smoothing surfaces for better playability |
Chisel | Carving details and shaping the flute |
Ruler | Measuring dimensions accurately |
Tuner | Ensuring pitch accuracy |
Designing the Flute
Before beginning construction, it is important to design the flute. Consider the following aspects:
- Length: The length of the flute determines the pitch. A longer flute produces lower notes, while a shorter one produces higher notes.
- Diameter: A wider bore allows for a louder sound but may sacrifice some tonal quality. Experiment with different diameters to find the desired balance.
- Embouchure Hole: The size and shape of the embouchure hole affect sound production. A typical shape is oval or rectangular, and placement on the flute is also critical.
Constructing the Flute
Follow these steps to construct your wooden flute:
- Cut the Wood: Use a saw to cut the wood to the desired length based on your design.
- Drill the Bore: Drill a straight hole through the length of the wood. A uniform bore will ensure consistent sound quality.
- Create Finger Holes: Mark and drill the finger holes according to your design. Commonly, six to eight holes are sufficient for diatonic scales.
- Shape the Embouchure Hole: Carefully carve the embouchure hole at one end of the flute. Ensure it is positioned correctly for optimal airflow.
- Sand the Surface: Use sandpaper to smooth all edges and surfaces. This step is vital for comfort during play and for achieving a good sound.
Tuning the Flute
After constructing the flute, tuning is essential:
- Use a tuner: Play each note and adjust the size of the finger holes as necessary to achieve the correct pitch.
- Check intonation: Ensure that all notes are in tune with each other. This may require minor adjustments to hole sizes.
- Test playability: Play the flute to assess its sound quality and make additional refinements if needed.
Finishing Touches
Once the flute is tuned, consider applying a finish to enhance the wood’s appearance and protect it:
- Natural oils: Apply linseed or tung oil for a natural finish that highlights the wood grain.
- Varnish: For a more durable surface, consider using a non-toxic varnish.
- Wax: A light coat of wax can offer protection while preserving the natural feel of the wood.
With these instructions, you can create a wooden flute tailored to your specifications and preferences. Proper attention to detail at each step will yield a beautiful instrument ready for performance.
Expert Insights on Crafting a Wooden Flute
Dr. Emily Carter (Woodwind Instrument Maker, Artisan Flutes Co.). “When crafting a wooden flute, it is essential to select the right type of wood, as different woods produce varying tonal qualities. Hardwoods like grenadilla or rosewood are often preferred for their density and durability, which contribute to a richer sound.”
Mark Thompson (Master Luthier, Thompson Instruments). “The precision in the bore and embouchure hole is crucial for achieving optimal sound quality. I recommend using a lathe for creating a consistent bore, as this will significantly influence the flute’s intonation and overall playability.”
Linda Chen (Music Educator and Flute Specialist, Harmony Music School). “For beginners interested in making their own flute, I suggest starting with a simple design and focusing on the finishing touches. Sanding and sealing the wood properly can enhance the instrument’s aesthetics and longevity, making it a joy to play.”
Frequently Asked Questions (FAQs)
What type of wood is best for making a flute?
The best types of wood for making a flute include hardwoods such as grenadilla, rosewood, and maple. These woods provide excellent acoustic properties and durability.
What tools are needed to make a wooden flute?
Essential tools include a saw, chisels, a drill, sandpaper, and a tuning device. Additionally, a lathe may be used for shaping the wood more precisely.
How do I determine the dimensions for the flute?
Dimensions depend on the desired key and sound quality. Generally, the length and diameter of the flute should be calculated based on standard flute measurements or specific design plans.
What is the process for drilling the finger holes?
Drill the finger holes at specific intervals along the body of the flute. The size and placement of each hole affect pitch and tone, requiring careful measurement and testing.
How do I finish the wooden flute after crafting?
After shaping and drilling, sand the surface smoothly and apply a finish such as oil or lacquer. This enhances the wood’s appearance and protects it from moisture.
Can I make a flute without prior woodworking experience?
While prior experience is beneficial, beginners can successfully make a flute by following detailed plans and tutorials. Patience and practice are key to achieving good results.
crafting a flute out of wood involves a series of precise steps that require both skill and patience. The process begins with selecting the appropriate type of wood, as different woods can affect the sound quality and tone of the flute. Common choices include hardwoods such as maple, cherry, or walnut, which provide durability and resonance. Once the wood is selected, proper measurements and designs must be made to ensure the flute’s dimensions align with traditional specifications or personal preferences.
After shaping the wood into the desired form, attention must be given to the flute’s embouchure hole and finger holes. These features significantly influence the instrument’s playability and sound production. Sanding and finishing the wood are crucial steps that enhance the flute’s aesthetic appeal and protect it from environmental factors. Finally, tuning the flute is essential to achieve the correct pitch, which may involve adjusting the size and placement of the finger holes.
Key takeaways from the discussion include the importance of material selection, precision in measurements, and the impact of design choices on sound quality. Additionally, aspiring flute makers should be prepared for a trial-and-error process, as achieving a well-tuned and playable instrument may require multiple adjustments. With dedication and practice, creating a wooden flute
Author Profile
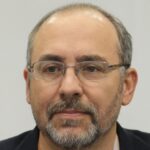
-
Darryl Norman is a seasoned entrepreneur and industry expert with a deep understanding of wood truss manufacturing and construction materials. As the President of Timberlake TrussWorks, LLC, Darryl played a pivotal role in shaping the company’s reputation for quality and precision. His leadership ensured that each truss met rigorous structural standards, providing builders with dependable components essential to their projects.
Beginning in 2025, Darryl Norman has shifted his focus to education and knowledge-sharing through an informative blog dedicated to wood truss manufacturing. Drawing from his extensive experience in the field, he provides in-depth insights into truss design, material selection, and construction techniques. This blog serves as a valuable resource for builders, contractors, and homeowners seeking practical guidance on truss systems and structural integrity.
Latest entries
- March 18, 2025General Wood TopicsWhat Color Is Ebony Wood? Unveiling the Rich Hues of This Luxurious Timber
- March 18, 2025Construction & FrameworkHow Can You Effectively Mount a Headboard to Your Wall?
- March 18, 2025General Wood TopicsCan Bees Really Eat Wood? Unraveling the Myths and Facts
- March 18, 2025General Wood TopicsDo Rabbits Really Chew on Wood? Exploring Their Eating Habits!