How Can You Build an Effective Kiln for Drying Wood?
For woodworking enthusiasts and craftsmen alike, the importance of properly dried wood cannot be overstated. Wood that retains too much moisture can warp, crack, or become susceptible to mold and decay, ultimately compromising the integrity of your projects. While commercial drying methods can be expensive and time-consuming, building your own kiln can be a rewarding and cost-effective solution. In this article, we’ll explore the ins and outs of constructing a homemade kiln specifically designed for drying wood, allowing you to take control of your lumber preparation process and ensure that every piece is perfectly seasoned for your next creation.
Overview
Creating a kiln for drying wood involves understanding the principles of heat, airflow, and humidity control. A well-designed kiln not only accelerates the drying process but also minimizes the risk of defects in the wood, making it an invaluable tool for anyone serious about woodworking. Whether you’re a hobbyist looking to improve your craft or a professional seeking efficiency, a homemade kiln can be tailored to your specific needs and available resources.
In this guide, we will delve into various kiln designs, materials, and techniques that can help you achieve optimal drying conditions. From simple setups using readily available materials to more complex systems that incorporate temperature and humidity controls, you’ll discover how to create a kiln that meets
Materials Needed for Building a Kiln
To construct a kiln for drying wood, a variety of materials are essential to ensure effective operation and durability.
- Wood: Select heat-resistant materials, such as plywood or solid wood, for the structure.
- Insulation: Use ceramic fiber insulation or fiberglass to maintain internal temperatures.
- Heating Source: Options include electric heating elements, propane burners, or wood stoves.
- Ventilation: Install fans or vents to facilitate air circulation and moisture removal.
- Thermometers: Accurate temperature gauges are crucial for monitoring internal conditions.
- Humidity Control: Utilize hygrometers to track moisture levels within the kiln.
Design Considerations for the Kiln
An effective kiln design is integral to achieving optimal drying results. Consider the following design elements:
- Size: Determine the kiln dimensions based on the volume of wood to be dried. A larger kiln allows for more wood but may require additional heating resources.
- Shape: Rectangular designs are common, but circular configurations can also be effective.
- Access: Ensure that the kiln has a door for easy loading and unloading of wood.
- Foundation: Construct a sturdy base to support the weight of the kiln and maintain stability.
Feature | Considerations |
---|---|
Heating Method | Electric, propane, or wood |
Insulation Type | Ceramic fiber or fiberglass |
Size | Based on wood volume |
Ventilation | Fans or natural airflow |
Building the Kiln
Once materials and design considerations are finalized, follow these steps to construct the kiln:
- Construct the Frame: Begin by creating a rectangular frame using plywood or solid wood. Ensure the frame is square and level.
- Insulate the Walls: Line the interior walls with insulation material, ensuring there are no gaps that could lead to heat loss.
- Install the Heating Source: Position your chosen heating method within the kiln, ensuring it is securely fixed and safe to operate.
- Set Up Ventilation: Incorporate vents or fans to promote airflow. Position them to allow moisture-laden air to escape while drawing in drier air.
- Add Thermometers and Hygrometers: Place monitoring devices at various points within the kiln for accurate temperature and humidity readings.
- Seal the Structure: Ensure all joints and seams are sealed to prevent moisture escape and heat loss.
Operational Guidelines for the Kiln
To achieve the best drying results, adhere to the following operational guidelines:
- Loading the Kiln: Stack wood in a manner that allows for air circulation between pieces.
- Temperature Management: Maintain a consistent temperature, typically between 120°F to 160°F (49°C to 71°C), depending on the wood type.
- Monitoring Moisture Levels: Regularly check humidity levels to prevent over-drying or warping.
- Duration: The drying process can take several days to weeks, depending on wood thickness and environmental conditions.
By following these steps and guidelines, you can successfully build and operate a kiln suitable for drying wood efficiently.
Materials Needed for Building a Wood Drying Kiln
To construct an effective kiln for drying wood, you will require specific materials that will ensure optimal heating and moisture control. Below is a list of essential components:
- Wood: For the frame and structure, select durable woods like cedar or treated lumber.
- Insulation: Use foam board or fiberglass insulation to retain heat.
- Heating Source: Options include electric heaters, propane burners, or wood stoves.
- Humidity Control: A hygrometer to monitor moisture levels, and possibly a dehumidifier.
- Ventilation Components: Fans for air circulation and vents for moisture release.
- Sealant: Weather stripping or caulk to prevent air leaks.
Designing the Kiln Structure
The design of the kiln plays a crucial role in its efficiency and effectiveness. Here are key considerations:
- Size: Determine the volume of wood you intend to dry and size the kiln accordingly. A typical small-scale kiln might measure 4′ x 8′ x 8′.
- Frame: Construct a sturdy frame using your chosen wood. Ensure it can support the weight and maintain structural integrity over time.
- Insulation: Line the interior with insulation to minimize heat loss. The walls should be at least 2-4 inches thick.
- Flooring: A slatted floor allows for airflow under the wood. Consider using pressure-treated wood or metal grating.
- Roof: Include a weatherproof roof that can withstand various elements. An angled design can help with water runoff.
Heating and Ventilation Setup
The heating and ventilation system is critical for effective wood drying. Follow these guidelines:
- Heating Source Installation: Position the heater at one end of the kiln to allow for uniform heat distribution. Ensure it is safely installed with appropriate clearances.
- Ventilation: Install adjustable vents at both the top and bottom of the kiln. This setup allows hot, moist air to escape while drawing in cooler air.
- Fans: Place fans strategically within the kiln to promote air circulation. Ideally, use one or two fans to maintain even temperatures throughout the space.
Monitoring and Controlling Conditions
Maintaining the right conditions inside the kiln is essential for effective drying. Implement the following:
- Temperature Control: Use a thermostat to maintain temperatures between 130°F and 180°F, depending on the wood species.
- Moisture Monitoring: Regularly check the humidity levels with a hygrometer. Adjust ventilation as needed to control moisture content.
- Data Logging: Consider using a data logger for temperature and humidity to track conditions over time, providing insights for adjustments.
Operational Considerations
Once the kiln is built, operational procedures must be established:
- Loading the Kiln: Stack wood in a way that allows for maximum airflow around each piece. Use spacers if necessary.
- Initial Drying Phase: Begin with a lower temperature and gradually increase to prevent cracking.
- Regular Checks: Monitor conditions daily, adjusting ventilation and heating as needed to maintain optimal drying rates.
By adhering to these guidelines, you will create an efficient kiln for drying wood that maximizes quality and minimizes waste.
Expert Recommendations for Building a Wood Drying Kiln
Dr. Emily Carter (Wood Technology Specialist, Timber Innovations). “When constructing a kiln for drying wood, it is crucial to ensure proper airflow and temperature control. Utilizing a combination of insulation materials and a reliable heating source can significantly enhance the efficiency of the drying process.”
Mark Thompson (Sustainable Forestry Consultant, Green Timber Solutions). “A well-designed kiln should incorporate moisture monitoring systems to prevent over-drying, which can lead to warping and cracking. Additionally, consider using renewable energy sources to minimize environmental impact.”
Linda Rodriguez (Architectural Woodworker, Artisan Woodworks). “The size and design of your kiln should be tailored to the specific types of wood you plan to dry. A modular approach allows for scalability and adaptability to different wood species and moisture content levels.”
Frequently Asked Questions (FAQs)
What materials do I need to make a kiln for drying wood?
To construct a kiln for drying wood, you will need materials such as plywood or OSB for the structure, insulation (like fiberglass or foam board), a heat source (electric heater or propane burner), a fan for air circulation, and a humidity control system.
What is the ideal temperature for drying wood in a kiln?
The ideal temperature for drying wood in a kiln typically ranges from 120°F to 160°F (49°C to 71°C). This temperature range helps to effectively remove moisture while minimizing the risk of warping or cracking.
How long does it take to dry wood in a kiln?
The drying time for wood in a kiln can vary depending on the type of wood, its initial moisture content, and the kiln’s conditions. Generally, it takes between 1 to 3 weeks to achieve optimal dryness.
Can I use a regular oven instead of a kiln for drying wood?
Using a regular oven is not recommended for drying wood due to its limited capacity and the risk of combustion. A kiln provides controlled conditions that are essential for effective drying without damaging the wood.
How do I control humidity levels in a wood drying kiln?
Humidity levels in a wood drying kiln can be controlled using a dehumidifier or by adjusting the ventilation. Monitoring with a hygrometer ensures that moisture levels are kept within the desired range for effective drying.
What safety precautions should I take when building a wood drying kiln?
When building a wood drying kiln, ensure proper ventilation to prevent the buildup of flammable gases. Use heat-resistant materials, avoid electrical hazards, and maintain a safe distance from combustible materials to minimize fire risks.
constructing a kiln for drying wood involves understanding the fundamental principles of moisture removal and heat application. The process typically requires careful planning and selection of materials to ensure efficient drying while minimizing the risk of damaging the wood. Various designs, including solar kilns, conventional electric kilns, and homemade alternatives, can be utilized depending on the resources available and the scale of the wood drying operation.
Key considerations include the kiln’s insulation, ventilation, and heating methods, which directly influence the drying rate and quality of the wood. Proper monitoring of temperature and humidity is essential to achieve optimal results, as excessive heat or moisture can lead to warping or cracking. Additionally, incorporating a moisture meter can enhance the precision of the drying process, ensuring that the wood reaches the desired moisture content without compromising its integrity.
Ultimately, building a kiln for drying wood is a valuable investment for woodworkers and craftsmen seeking to improve the quality of their materials. By following best practices and utilizing appropriate techniques, one can create a functional and efficient kiln that meets their specific needs. This not only enhances the durability and usability of the wood but also contributes to sustainable practices in woodworking and construction.
Author Profile
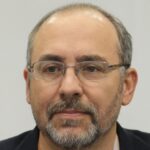
-
Darryl Norman is a seasoned entrepreneur and industry expert with a deep understanding of wood truss manufacturing and construction materials. As the President of Timberlake TrussWorks, LLC, Darryl played a pivotal role in shaping the company’s reputation for quality and precision. His leadership ensured that each truss met rigorous structural standards, providing builders with dependable components essential to their projects.
Beginning in 2025, Darryl Norman has shifted his focus to education and knowledge-sharing through an informative blog dedicated to wood truss manufacturing. Drawing from his extensive experience in the field, he provides in-depth insights into truss design, material selection, and construction techniques. This blog serves as a valuable resource for builders, contractors, and homeowners seeking practical guidance on truss systems and structural integrity.
Latest entries
- March 18, 2025General Wood TopicsWhat Color Is Ebony Wood? Unveiling the Rich Hues of This Luxurious Timber
- March 18, 2025Construction & FrameworkHow Can You Effectively Mount a Headboard to Your Wall?
- March 18, 2025General Wood TopicsCan Bees Really Eat Wood? Unraveling the Myths and Facts
- March 18, 2025General Wood TopicsDo Rabbits Really Chew on Wood? Exploring Their Eating Habits!