How Can You Create a Resin Mold Using Wood?
Creating unique and stunning resin art pieces has become a popular hobby for many DIY enthusiasts and crafters. One of the essential steps in this creative process is making a mold that can shape your resin into beautiful forms. While there are many commercial molds available, crafting your own resin mold out of wood can add a personal touch to your projects and allow for endless customization. Whether you’re looking to create coasters, jewelry, or decorative items, learning how to make a resin mold from wood can open up a world of possibilities for your artistic expression.
In this article, we will explore the fascinating process of transforming wood into a functional mold for resin casting. From selecting the right type of wood to understanding the necessary tools and techniques, we’ll guide you through the essentials of mold-making. You’ll discover how to create a sturdy and reliable mold that not only captures intricate details but also withstands the rigors of resin pouring.
As we delve deeper into the topic, you’ll gain insights into the best practices for ensuring your mold is both effective and durable. Whether you’re a seasoned crafter or a beginner eager to experiment, this guide will equip you with the knowledge to embark on your resin molding journey with confidence. Get ready to unleash your creativity and craft custom molds that reflect your unique
Gathering Materials
To create a resin mold out of wood, you will need to gather essential materials and tools. The quality of these materials greatly influences the outcome of your mold. Here’s a list of what you’ll need:
- Wood: Choose a type of wood that is smooth and has minimal grain, such as plywood or MDF.
- Sealant: To prevent the resin from sticking to the wood, a sealant like polyurethane or a wood varnish is necessary.
- Release Agent: Silicone spray or petroleum jelly can be used as a release agent to ensure the resin comes out easily.
- Clamps: For holding your mold together securely during the resin pouring process.
- Saw: A table saw or circular saw for cutting the wood to size.
- Drill: To create holes if needed for alignment or handles.
- Sandpaper: To smooth edges and surfaces.
Designing the Mold
Designing the mold is a critical step that requires careful consideration. The complexity of your design will determine the amount of time and resources needed. Follow these guidelines:
- Sketch the design: Create a detailed sketch of the mold you want to make, including dimensions and features.
- Consider the mold’s depth: Ensure that the depth accommodates the thickness of the resin layer you intend to pour.
- Account for draft angles: If your mold has vertical sides, include a slight angle to facilitate easy removal of the cured resin.
Building the Mold Frame
Constructing the mold frame involves cutting the wood and assembling it into the desired shape. Follow these steps:
- Cut the wood: Use your saw to cut the wood according to the dimensions from your sketch.
- Assemble the frame: Use clamps to hold the pieces together. Ensure the corners are square for a uniform mold.
- Secure the joints: Fasten the joints using wood screws or wood glue, depending on your design requirements.
- Check for leaks: Before sealing, pour water into the mold to check for leaks. If any are found, seal them with additional wood glue or caulk.
Sealing the Mold
Sealing the mold is essential to prevent the resin from adhering to the wood. Follow these steps:
- Apply a sealant: Use a brush or cloth to apply a generous coat of sealant on all surfaces of the mold. Allow it to dry completely.
- Sand the surface: Once dry, lightly sand the surface to ensure a smooth finish.
- Reapply sealant: For added protection, apply a second coat of sealant and let it dry thoroughly.
Applying Release Agent
Before pouring resin, it’s vital to apply a release agent to the mold. This step facilitates the removal of the cured resin from the mold without damage:
- Choose a release agent: Silicone spray or petroleum jelly works well.
- Apply evenly: Spray or coat the entire interior surface of the mold, ensuring complete coverage.
- Let it dry: Allow the release agent to set for a few minutes before pouring the resin.
Pouring the Resin
Now that your mold is prepared, you can proceed to pour the resin. Follow these instructions:
- Mix the resin: Follow the manufacturer’s instructions to mix the resin and hardener.
- Pour carefully: Slowly pour the resin into the mold, avoiding bubbles.
- Use a stir stick: If bubbles form, use a stir stick to gently pop them.
- Let it cure: Allow the resin to cure fully according to the product specifications.
Table of Materials and Their Uses
Material | Use |
---|---|
Wood | Forms the mold structure |
Sealant | Prevents resin adhesion |
Release Agent | Facilitates resin removal |
Clamps | Holds mold together during curing |
Saw | Cuts wood to required dimensions |
Drill | Creates holes for alignment |
Sandpaper | Smooths edges and surfaces |
Choosing the Right Wood
Selecting the appropriate type of wood is crucial for creating a successful resin mold. Consider the following types:
- Plywood: Durable and cost-effective, suitable for larger molds.
- MDF (Medium-Density Fiberboard): Smooth surface ideal for detailed designs.
- Softwoods (e.g., pine, cedar): Easier to work with but may require sealing.
- Hardwoods (e.g., oak, maple): Provide strength and durability but are more expensive.
Preparing the Wood
Before crafting the mold, preparation is essential to ensure a smooth casting process.
- Cut the Wood: Use a saw to cut the wood into the desired dimensions for the mold. Ensure that the pieces fit snugly together.
- Sand the Edges: Smooth all edges and surfaces with sandpaper to prevent the resin from sticking and to avoid imperfections.
- Seal the Wood: Apply a sealant or wood finish to the wood to prevent resin absorption. This step is vital for achieving clean edges and maintaining the mold’s shape.
Assembling the Mold
Once the wood is prepared, the next step is assembling the mold.
- Use Wood Glue: Apply a strong wood glue to the edges of the pieces and fit them together.
- Clamping: Clamp the pieces together until the glue dries completely. This process ensures a tight seal.
- Create a Base: If necessary, attach a base to the mold to hold the sides in place and provide stability during the casting process.
Applying Release Agent
To ensure easy removal of the resin from the mold, apply a release agent.
- Types of Release Agents:
- Commercial Mold Release: Specifically designed for resin applications.
- Petroleum Jelly: A budget-friendly alternative that can work effectively.
- Cooking Spray: Readily available and can be used as a last resort.
- Application: Generously coat all surfaces of the mold with the release agent, ensuring complete coverage.
Pouring the Resin
With the mold prepared, you can now pour the resin.
- Mix the Resin: Follow the manufacturer’s instructions for mixing the resin and hardener. Ensure thorough mixing to avoid soft spots.
- Pouring Technique: Slowly pour the resin into the mold, starting from one corner and allowing it to flow gently. This technique minimizes bubbles.
- Curing Time: Allow the resin to cure according to the product instructions. This period can vary based on the type of resin used.
Demolding and Finishing
After the resin has cured, it’s time to demold and finish the piece.
- Removing the Mold: Carefully separate the wood pieces from the cured resin. If the release agent was applied correctly, this should be a straightforward process.
- Sanding and Polishing: Use sandpaper to smooth any rough edges or surfaces. Consider polishing the resin for a glossy finish.
Step | Action |
---|---|
Cut Wood | Create mold dimensions |
Assemble Mold | Glue and clamp pieces |
Apply Release | Coat mold surfaces |
Pour Resin | Mix and carefully pour |
Cure | Wait as per instructions |
Demold | Remove mold and clean edges |
Finish | Sand and polish as needed |
This structured approach will yield a reliable and effective resin mold crafted from wood, facilitating various creative projects.
Expert Insights on Creating Wooden Resin Molds
Jessica Harmon (Master Woodworker, Artisan Crafts Journal). “When constructing a resin mold from wood, it is crucial to select a non-porous wood type to prevent the resin from leaking. Additionally, applying a release agent before pouring the resin will ensure a smooth extraction process.”
Michael Tran (Industrial Designer, Design Innovations). “Precision is key in mold-making. Using a CNC machine for cutting the wooden mold can significantly enhance accuracy and reduce the risk of imperfections, which is essential for achieving a flawless final product.”
Linda Carter (Materials Scientist, Composite Solutions). “Understanding the chemical interactions between the wood and resin is vital. Proper sealing of the wood surface can prevent unwanted reactions, ensuring the durability and integrity of the mold.”
Frequently Asked Questions (FAQs)
What materials do I need to make a resin mold out of wood?
To create a resin mold from wood, you will need a piece of wood (such as plywood or MDF), wood glue, a saw, sandpaper, a release agent (like petroleum jelly or mold release spray), and epoxy resin.
How do I prepare the wood for making a resin mold?
Begin by cutting the wood to the desired shape and size. Sand the edges and surfaces to ensure they are smooth, as this will help achieve a clean mold finish. Apply a release agent to prevent the resin from sticking to the wood.
Can I use any type of wood for making a resin mold?
While most types of wood can be used, it is recommended to use dense, non-porous woods such as plywood or MDF. These materials provide a smoother surface and reduce the risk of resin leakage.
How do I ensure that the resin does not stick to the wooden mold?
Applying a generous coat of a suitable release agent is crucial. Ensure that all surfaces of the mold are covered to facilitate easy demolding once the resin has cured.
What is the curing time for resin in a wooden mold?
Curing time can vary based on the type of resin used and environmental conditions. Typically, epoxy resin can take anywhere from 24 to 72 hours to fully cure, but always refer to the manufacturer’s instructions for specific guidance.
Can I reuse a wooden mold for resin casting?
Yes, a wooden mold can be reused multiple times if it is properly maintained. Ensure that the release agent is applied before each use and inspect the mold for any damage after each casting to maintain its integrity.
Creating a resin mold out of wood is a rewarding process that allows for the customization of various projects, from art pieces to functional items. The first step involves selecting the appropriate type of wood, ensuring it is smooth and free of imperfections to achieve a high-quality finish. Proper preparation of the wood surface is crucial; sanding and sealing the wood can prevent resin from sticking and ensure a clean release once the mold is complete.
Once the wood is prepared, constructing the mold involves designing a frame that will hold the resin in place. This can be achieved by cutting the wood into the desired shape and securely fastening it together. It is essential to use a non-porous sealant on the interior surfaces to prevent the resin from leaking and to facilitate easier removal once the resin has cured. Additionally, incorporating release agents can further enhance the ease of demolding.
After the mold is constructed and sealed, the next step is mixing and pouring the resin. Attention to detail during this phase is vital, as proper mixing ratios and techniques will ensure a successful outcome. Allowing the resin to cure fully before attempting to remove it from the mold will yield the best results. Following these steps will enable anyone to create durable and intricate resin molds from wood, unlocking
Author Profile
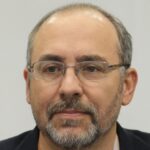
-
Darryl Norman is a seasoned entrepreneur and industry expert with a deep understanding of wood truss manufacturing and construction materials. As the President of Timberlake TrussWorks, LLC, Darryl played a pivotal role in shaping the company’s reputation for quality and precision. His leadership ensured that each truss met rigorous structural standards, providing builders with dependable components essential to their projects.
Beginning in 2025, Darryl Norman has shifted his focus to education and knowledge-sharing through an informative blog dedicated to wood truss manufacturing. Drawing from his extensive experience in the field, he provides in-depth insights into truss design, material selection, and construction techniques. This blog serves as a valuable resource for builders, contractors, and homeowners seeking practical guidance on truss systems and structural integrity.
Latest entries
- March 18, 2025General Wood TopicsWhat Color Is Ebony Wood? Unveiling the Rich Hues of This Luxurious Timber
- March 18, 2025Construction & FrameworkHow Can You Effectively Mount a Headboard to Your Wall?
- March 18, 2025General Wood TopicsCan Bees Really Eat Wood? Unraveling the Myths and Facts
- March 18, 2025General Wood TopicsDo Rabbits Really Chew on Wood? Exploring Their Eating Habits!