How Can You Create Your Own Wooden Flute? A Step-by-Step Guide
The enchanting sound of a wooden flute has captivated musicians and listeners alike for centuries, evoking images of serene forests and tranquil streams. Crafting your own wooden flute not only allows you to create a unique musical instrument but also connects you to a rich tradition of craftsmanship and artistry. Whether you’re an experienced woodworker or a curious beginner, the journey of making a wooden flute is both rewarding and fulfilling. In this article, we will explore the essential steps and considerations involved in this timeless craft, guiding you through the process of transforming raw wood into a melodious masterpiece.
To embark on the adventure of making a wooden flute, one must first understand the fundamental principles of flute design and acoustics. The choice of wood plays a crucial role in determining the instrument’s tone and resonance, while the dimensions and shape influence its playability and sound quality. As you delve into the world of flute-making, you will discover the importance of precision and attention to detail, from selecting the right materials to crafting the finger holes that allow for a range of musical notes.
As you progress through the crafting process, you will also learn about the various techniques and tools that can enhance your woodworking skills. From shaping the body of the flute to finishing touches that bring out the natural beauty of the
Choosing the Right Wood
The selection of wood is a crucial factor in crafting a wooden flute, as different types of wood impart distinct tonal qualities and characteristics to the instrument. Common choices for flute-making include:
- Maple: Known for its bright, clear sound and good projection.
- Cedar: Offers a warm, mellow tone, ideal for softer music.
- Cherry: Balances brightness and warmth, suitable for versatile playing styles.
- Bamboo: Although technically a grass, bamboo provides a unique, rich sound and is lightweight.
When selecting wood, consider the following factors:
- Grain structure: A tight and straight grain is preferable for better acoustics.
- Moisture content: Ensure the wood is properly dried to prevent warping.
- Sustainability: Choose ethically sourced wood to minimize environmental impact.
Tools and Materials Needed
To create a wooden flute, gather the following tools and materials:
- Wood: A suitable piece of hardwood or bamboo.
- Drill: For creating finger holes and the airway.
- Ruler: To measure and mark dimensions accurately.
- Saw: For cutting the wood to length.
- Sandpaper: For smoothing the surfaces and edges.
- Wood glue: If constructing in sections or repairing.
- Finish: Oil or lacquer to protect and enhance the wood’s appearance.
Below is a table summarizing the tools and their purposes:
Tool | Purpose |
---|---|
Drill | To create finger holes and the airway |
Ruler | To ensure precise measurements |
Saw | To cut the wood to the desired length |
Sandpaper | For finishing and smoothing |
Wood glue | For joining pieces if necessary |
Finish | To protect and enhance the wood |
Shaping the Flute
Once you have your wood prepared and tools at hand, the next step is shaping the flute. Follow these steps:
- Cut the Wood: Start by cutting the wood to the desired length. The length will affect the pitch; longer flutes produce lower notes, while shorter flutes yield higher notes.
- Create the Bore: Drill a hole down the center of the wood to create the bore. The diameter of the bore influences the flute’s sound; a wider bore produces a louder sound while a narrower bore offers more control.
- Cut the Finger Holes: Mark the positions for the finger holes based on your design. Typically, these holes are spaced according to the scale you wish to achieve. Drill each hole carefully and ensure they are smooth.
- Shape the Ends: Carve the ends of the flute; one end will be a blow hole, which may need to be angled slightly for optimal sound production. The other end may be closed or left open, depending on the design.
- Sand the Flute: Use sandpaper to smooth all surfaces and edges to prevent splinters and enhance comfort.
Finishing Touches
After shaping, apply a finish to protect the wood and improve its appearance. Options include:
- Natural oils: Such as linseed or tung oil, which penetrate the wood and provide a protective barrier.
- Lacquer: Offers a glossy finish but may change the sound slightly.
- Wax: For a natural look and feel, though less protective than oils.
Allow the finish to cure as per the manufacturer’s instructions before playing the flute.
Materials Required
To craft a wooden flute, select high-quality materials that will enhance the instrument’s sound and durability. The following list outlines the essential materials:
- Wood: Common choices include:
- Bamboo
- Maple
- Cherry
- Walnut
- Drill: A hand drill or a power drill with appropriate bits.
- Ruler or Measuring Tape: For accurate measurements.
- Saw: A fine saw suitable for cutting wood.
- Sandpaper: Various grits for smoothing the wood surface.
- Wood Finish or Sealant: To protect the flute from moisture.
- Tuning Device: A tuner or an app to help with pitch accuracy.
Designing the Flute
Creating a design for your flute is an essential step. Consider the following aspects:
- Length: The overall length of the flute affects pitch. Longer flutes produce lower notes, while shorter flutes yield higher notes.
- Bore Diameter: The internal diameter affects airflow and sound quality. A standard bore diameter ranges from 1/2 inch to 3/4 inch.
- Finger Holes: The placement and size of finger holes influence the range and tuning. A common flute has six to eight holes.
Design Aspect | Recommended Specification |
---|---|
Length | 24 to 30 inches |
Bore Diameter | 0.5 to 0.75 inches |
Number of Finger Holes | 6 to 8 holes |
Cutting the Wood
After selecting the wood and finalizing the design, proceed with cutting. Follow these steps:
- Measure and Mark: Use the ruler to measure the desired length and mark it on the wood.
- Cut the Wood: Carefully saw along the marked line to achieve a straight edge.
- Drill the Bore: Using a drill bit, create a hole along the length of the wood. Ensure the hole is consistent in diameter.
- Create Finger Holes: Mark the positions for the finger holes based on your design. Drill the holes with a smaller bit, gradually increasing the size for tuning.
Shaping and Smoothing
Once the wood is cut and drilled, refine its shape and finish:
- Sand the Edges: Use sandpaper to smooth all edges and surfaces, avoiding any sharp points.
- Shape the Mouthpiece: Carve the mouthpiece to create a comfortable area for playing. This can be done using a knife or chisel.
- Finish the Surface: Apply a wood finish or sealant to protect the flute from moisture and enhance its appearance.
Tuning the Flute
Tuning is a critical step in ensuring the flute produces the correct pitch. Follow these guidelines:
- Initial Tuning: Play the flute and check the pitch with a tuner.
- Adjust Finger Holes: If the pitch is sharp, enlarge the finger holes slightly. If flat, consider shortening the flute or closing the holes.
- Fine-Tuning: Repeat the process until the desired pitch is achieved.
Final Assembly and Testing
After tuning, perform the final assembly:
- Check for Leaks: Ensure there are no air leaks around the finger holes.
- Test Playability: Play a scale to assess the instrument’s sound quality and note accuracy.
- Make Adjustments: If necessary, return to the finger holes or mouthpiece for further refinement.
This process results in a handcrafted wooden flute that showcases both artistry and functionality.
Expert Insights on Crafting a Wooden Flute
Dr. Emily Hartman (Luthier and Ethnomusicologist, The Woodwind Journal). “Creating a wooden flute requires not only an understanding of acoustics but also a deep appreciation for the materials involved. The choice of wood can significantly affect the tonal quality, so one must consider both the density and grain of the wood to achieve the desired sound.”
Michael Chen (Master Flute Maker, Artisan Flutes Co.). “The process of crafting a wooden flute begins with precise measurements and careful shaping. It is essential to maintain the correct bore size and taper to ensure optimal sound production. Patience and attention to detail during the sanding and finishing stages can make a substantial difference in the final product.”
Sarah Patel (Music Educator and Flute Specialist, Harmony Music Academy). “When teaching others how to make a wooden flute, I emphasize the importance of understanding the instrument’s anatomy. Each component, from the embouchure hole to the finger holes, plays a critical role in sound quality and playability. Encouraging students to experiment with different designs can lead to unique and personal instruments.”
Frequently Asked Questions (FAQs)
What materials are needed to make a wooden flute?
To make a wooden flute, you will need a suitable piece of wood (such as bamboo or hardwood), a saw, a drill, sandpaper, wood glue, and a finish like oil or varnish. Additionally, you may require a ruler, a pencil, and a file for shaping.
What is the best type of wood for crafting a flute?
The best types of wood for crafting a flute include hardwoods like maple, cherry, and walnut, as well as bamboo. These materials provide good tonal quality and durability, which are essential for producing a pleasing sound.
How do I determine the length of the flute?
The length of the flute is determined by the desired pitch. Generally, longer flutes produce lower pitches, while shorter flutes yield higher pitches. A common starting point is to use a length of around 24 inches for a standard concert flute.
What are the steps to create the finger holes?
To create finger holes, measure and mark their positions based on standard flute dimensions or your desired tuning. Use a drill to create the holes, then gradually enlarge them with a file to fine-tune the pitch and ensure comfortable finger placement.
How can I finish the wooden flute for durability?
To finish the wooden flute, sand the entire surface to a smooth texture, then apply a wood finish such as oil or varnish. Allow the finish to dry completely before using the flute to enhance its durability and protect it from moisture.
Is it necessary to tune the flute after making it?
Yes, tuning the flute is essential after construction. Adjust the size of the finger holes and the overall length of the flute to achieve the desired pitch. Regular tuning checks are also recommended to maintain sound quality over time.
making a wooden flute is a rewarding endeavor that combines craftsmanship with musicality. The process involves selecting the right type of wood, understanding the dimensions and design of the flute, and employing proper techniques for shaping and finishing the instrument. Each step, from cutting the wood to drilling the finger holes, requires careful attention to detail to ensure that the flute produces a pleasing sound and is comfortable to play.
Key takeaways from the discussion include the importance of choosing high-quality wood, as it significantly affects the flute’s tonal quality. Additionally, precise measurements are crucial for achieving the desired pitch and sound. Understanding the acoustics involved and experimenting with different designs can lead to a unique instrument that reflects the maker’s personal style. Finally, patience and practice are essential, as mastering the art of flute-making can take time and dedication.
Overall, the journey of creating a wooden flute not only enhances one’s woodworking skills but also deepens an appreciation for the intricacies of musical instrument design. Whether for personal use or as a gift, a handmade wooden flute can be a cherished item that embodies both artistry and functionality.
Author Profile
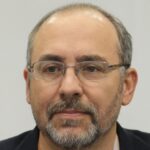
-
Darryl Norman is a seasoned entrepreneur and industry expert with a deep understanding of wood truss manufacturing and construction materials. As the President of Timberlake TrussWorks, LLC, Darryl played a pivotal role in shaping the company’s reputation for quality and precision. His leadership ensured that each truss met rigorous structural standards, providing builders with dependable components essential to their projects.
Beginning in 2025, Darryl Norman has shifted his focus to education and knowledge-sharing through an informative blog dedicated to wood truss manufacturing. Drawing from his extensive experience in the field, he provides in-depth insights into truss design, material selection, and construction techniques. This blog serves as a valuable resource for builders, contractors, and homeowners seeking practical guidance on truss systems and structural integrity.
Latest entries
- March 18, 2025General Wood TopicsWhat Color Is Ebony Wood? Unveiling the Rich Hues of This Luxurious Timber
- March 18, 2025Construction & FrameworkHow Can You Effectively Mount a Headboard to Your Wall?
- March 18, 2025General Wood TopicsCan Bees Really Eat Wood? Unraveling the Myths and Facts
- March 18, 2025General Wood TopicsDo Rabbits Really Chew on Wood? Exploring Their Eating Habits!