How Can You Create Your Own Unique Wooden Mask?
Creating a wooden mask is not just an artistic endeavor; it’s a journey into the rich tapestry of culture, tradition, and self-expression. Whether you’re inspired by indigenous art forms, theatrical traditions, or simply the allure of working with your hands, crafting a wooden mask allows you to explore your creativity while connecting with the age-old practices of artisans from around the world. As you embark on this project, you’ll discover the joy of transforming a simple piece of wood into a captivating work of art that can tell stories, evoke emotions, and even serve as a unique decorative piece in your home.
Overview
The process of making a wooden mask involves several key steps that blend artistry with craftsmanship. From selecting the right type of wood to sketching your design, each stage is crucial in bringing your vision to life. Understanding the tools and techniques required for carving, shaping, and finishing your mask will enhance your skills and ensure a successful outcome. Moreover, the cultural significance behind various mask designs can inspire your creativity, allowing you to infuse personal meaning into your work.
As you delve deeper into the world of wooden mask-making, you’ll learn about the various styles and traditions that influence this art form. Whether you are drawn to the bold expressions of African tribal masks or
Choosing the Right Wood
Selecting the appropriate type of wood is crucial for crafting a wooden mask. Each type of wood offers different characteristics, affecting the mask’s durability, appearance, and ease of carving. Here are some commonly used woods for mask-making:
- Basswood: Known for its softness and fine grain, making it easy to carve.
- Cedar: Lightweight and aromatic, cedar also has natural resistance to decay.
- Pine: Readily available and budget-friendly, though it may have knots that complicate carving.
- Mahogany: A more expensive option, mahogany is dense and offers a rich color.
Consider the following factors when selecting wood:
Wood Type | Characteristics | Recommended Use |
---|---|---|
Basswood | Soft, easy to carve | Beginners, intricate designs |
Cedar | Lightweight, aromatic | Outdoor masks, rustic designs |
Pine | Affordable, may have knots | Simple projects, practice |
Mahogany | Dense, rich color | Professional work, high-end masks |
Designing the Mask
Before you start carving, it is essential to have a clear design. Begin by sketching your mask on paper, considering dimensions and features. Focus on the following elements:
- Face shape: Decide whether you want a human, animal, or abstract design.
- Facial features: Plan where the eyes, nose, and mouth will be positioned.
- Decorative elements: Think about additional features like patterns, textures, or paint.
Creating a template can help maintain proportions. You can transfer the design directly onto the wood using carbon paper or by tracing.
Carving the Mask
Once you have your design, it’s time to start the carving process. Follow these steps for effective mask carving:
- Prepare the workspace: Ensure your work area is well-lit and organized.
- Secure the wood: Use clamps to hold the wood in place.
- Start with rough cuts: Use a saw to cut out the general shape of the mask.
- Carve details: Gradually use chisels and knives to refine the features.
- Sand the surface: Begin with coarse sandpaper and progress to finer grits to achieve a smooth finish.
Safety is paramount; always wear protective gear, such as gloves and goggles, while using sharp tools.
Finishing Touches
After carving, the mask requires finishing touches to enhance its appearance and durability. Consider these options:
- Sealing: Apply a wood sealer to protect against moisture.
- Painting: Use acrylic or oil-based paints for vibrant colors. Consider using a primer before painting for better adhesion.
- Varnishing: To add a glossy finish, apply a clear varnish after the paint has dried.
Ensure all materials used are suitable for the intended use of the mask, especially if it will be worn. This is essential for both aesthetic and safety reasons.
Materials Required for Crafting a Wooden Mask
To create a wooden mask, it is essential to gather the appropriate materials that will ensure durability and ease of work. Here is a list of recommended materials:
- Wood: Choose a softwood like pine or basswood for ease of carving, or hardwood like oak for durability.
- Carving Tools: A set of chisels, a carving knife, and a gouge for shaping the wood.
- Sandpaper: Various grits (80 to 220) for smoothing the surface.
- Wood Glue: For assembling different parts if necessary.
- Paints and Finishes: Acrylic or oil paints, wood stain, and a clear sealant for protection.
- Safety Equipment: Gloves, goggles, and a dust mask for protection during the carving process.
Designing the Mask
The design phase is crucial, as it dictates the overall aesthetic and functionality of the mask. Follow these steps to create a compelling design:
- Sketch Ideas: Begin with freehand sketches, exploring different shapes and features.
- Consider Dimensions: Determine the size of the mask in relation to the wearer’s face.
- Facial Features: Decide on exaggerated features or abstract shapes to convey the intended expression or theme.
- Template Creation: Once a design is finalized, create a detailed template to transfer onto the wood.
Carving the Wooden Mask
Carving is the most intricate part of the process, requiring patience and precision. Follow these steps to carve your mask effectively:
- Transfer the Design: Use carbon paper to trace your template onto the wood surface.
- Initial Cuts: Begin with larger tools to remove excess wood and outline the basic shape.
- Refining Details: Gradually switch to finer tools for intricate details, such as eyes, nose, and mouth.
- Depth and Texture: Vary the depth of cuts to add dimension and texture to the mask.
Finishing Touches
Once the carving is complete, it is time to refine and finish the mask. This enhances appearance and longevity.
- Sanding: Smooth the entire surface using progressively finer sandpaper, ensuring all rough edges are eliminated.
- Painting: Apply acrylic or oil paints according to the desired color scheme, allowing each layer to dry completely.
- Sealing: Once painted, apply a clear sealant to protect the mask from moisture and wear.
Adding Straps and Accessories
To ensure the mask can be worn comfortably, adding straps and any additional decorative elements is essential.
- Attachment: Use leather or elastic straps, securing them to the sides of the mask with screws or glue.
- Decoration: Enhance the mask with feathers, beads, or fabric, adhering them with strong glue.
- Final Inspection: Check for any rough spots or loose elements before the mask is complete.
Safety Precautions During the Process
Safety should always be a priority when working with tools and materials. Adhere to the following guidelines:
Safety Measure | Description |
---|---|
Wear Protective Gear | Use goggles, gloves, and a dust mask. |
Work in a Ventilated Area | Ensure proper airflow when using paints and finishes. |
Keep Tools Sharp | Dull tools can slip and cause accidents. |
Clean Work Area | Maintain a tidy workspace to prevent injuries. |
By following these detailed steps and guidelines, crafting a wooden mask becomes a structured and rewarding endeavor.
Expert Insights on Crafting Wooden Masks
Emily Carter (Master Woodworker, Artisan Crafts Journal). “Creating a wooden mask requires a deep understanding of both the material and the techniques involved. Start with selecting the right type of wood, such as basswood or pine, which are both lightweight and easy to carve. Always sketch your design beforehand to guide your carving process.”
James Liu (Cultural Anthropologist, Folklore Studies Quarterly). “Wooden masks have significant cultural meanings across various societies. When making a mask, it is essential to research the cultural context and symbolism behind the design. This not only enriches the crafting process but also honors the traditions from which these masks originate.”
Sarah Thompson (Art Instructor, Creative Arts Academy). “Safety should always be a priority when working with wood. Use proper tools and techniques to avoid injuries. Additionally, consider finishing your mask with non-toxic paints or sealants to protect the wood and enhance its visual appeal.”
Frequently Asked Questions (FAQs)
What materials do I need to make a wooden mask?
You will need a piece of wood (such as basswood or pine), carving tools (like chisels and knives), sandpaper, wood glue, paint or wood stain, and a protective finish such as varnish or sealant.
How do I choose the right type of wood for a mask?
Select a lightweight wood that is easy to carve, such as basswood or cedar. These types of wood provide a good balance between workability and durability, making them ideal for mask-making.
What are the basic steps to carve a wooden mask?
Start by sketching the mask design on paper. Transfer the design onto the wood, then use carving tools to shape the mask. After carving, sand the surface smooth, apply paint or stain, and finish with a protective coat.
Can I use power tools for making a wooden mask?
Yes, power tools such as rotary tools or band saws can expedite the carving process. However, ensure you have the necessary skills and safety equipment to use them effectively.
How do I ensure my wooden mask is safe to wear?
Make sure to sand all edges and surfaces thoroughly to prevent splinters. Additionally, use non-toxic paints and finishes, and consider adding padding or straps for comfort when wearing the mask.
What techniques can I use to add detail to my wooden mask?
You can use various carving techniques such as relief carving, chip carving, or wood burning to add intricate details. Additionally, layering paint or using different finishes can enhance the visual appeal of the mask.
In summary, creating a wooden mask involves a series of methodical steps that require both creativity and craftsmanship. The process begins with selecting the right type of wood, which is crucial for ensuring durability and ease of carving. Popular choices include basswood and pine due to their softness and workability. Once the wood is chosen, the design phase follows, where one sketches the intended mask shape and features, allowing for a clear vision before the actual crafting begins.
The next steps involve cutting the wood to shape, which can be done using various tools such as saws and chisels. Carving the details is a critical phase, as it brings the mask to life and adds character. Attention to detail during this stage is paramount, as it determines the final aesthetic of the mask. After carving, sanding the surface smooths out any rough edges, preparing the mask for finishing touches like painting or staining, which can enhance its visual appeal and protect the wood.
Finally, securing any additional elements, such as straps or decorative features, completes the mask. This entire process not only results in a unique piece of art but also offers a fulfilling experience that combines technical skill with artistic expression. Overall, making a wooden mask is an engaging project that can yield impressive
Author Profile
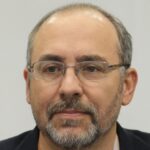
-
Darryl Norman is a seasoned entrepreneur and industry expert with a deep understanding of wood truss manufacturing and construction materials. As the President of Timberlake TrussWorks, LLC, Darryl played a pivotal role in shaping the company’s reputation for quality and precision. His leadership ensured that each truss met rigorous structural standards, providing builders with dependable components essential to their projects.
Beginning in 2025, Darryl Norman has shifted his focus to education and knowledge-sharing through an informative blog dedicated to wood truss manufacturing. Drawing from his extensive experience in the field, he provides in-depth insights into truss design, material selection, and construction techniques. This blog serves as a valuable resource for builders, contractors, and homeowners seeking practical guidance on truss systems and structural integrity.
Latest entries
- March 18, 2025General Wood TopicsWhat Color Is Ebony Wood? Unveiling the Rich Hues of This Luxurious Timber
- March 18, 2025Construction & FrameworkHow Can You Effectively Mount a Headboard to Your Wall?
- March 18, 2025General Wood TopicsCan Bees Really Eat Wood? Unraveling the Myths and Facts
- March 18, 2025General Wood TopicsDo Rabbits Really Chew on Wood? Exploring Their Eating Habits!