How Can You Create Your Own Wooden Surfboard?
Introduction
Imagine gliding across the shimmering waves, the sun kissing your skin, and the thrill of riding a wave on a surfboard you crafted with your own hands. Making a wooden surfboard is not just a rewarding DIY project; it’s a journey that connects you with the ocean and the art of craftsmanship. Whether you’re an experienced surfer looking to deepen your relationship with the sport or a woodworking enthusiast eager to explore new horizons, this guide will walk you through the fascinating process of creating a wooden surfboard. Get ready to unleash your creativity and learn the skills that will transform raw materials into a beautiful, functional piece of art.
Creating a wooden surfboard is a blend of artistry and engineering, requiring both creativity and precision. The journey begins with selecting the right type of wood, as this choice significantly impacts the board’s performance and aesthetics. From the initial design to the final finishing touches, each step in the process offers an opportunity to personalize your board, making it a true reflection of your style and surfing philosophy.
As you delve into the world of wooden surfboards, you’ll discover the various techniques and tools involved, from shaping the blank to applying the fiberglass for durability. This hands-on experience not only enhances your understanding of surfboard dynamics but also fosters a
Choosing the Right Wood
Selecting the right type of wood is crucial for building a wooden surfboard that is both durable and functional. Common wood types used in surfboard construction include:
- Paulownia: Lightweight and resistant to warping, making it ideal for surfboards.
- Cedar: Known for its buoyancy and natural resistance to water, though it can be heavier.
- Bamboo: Strong and flexible, bamboo is an eco-friendly option that also provides a unique aesthetic.
When selecting wood, consider the following factors:
- Weight: A lighter board is easier to maneuver in the water.
- Flexibility: The right amount of flex enhances performance and comfort.
- Water Resistance: Essential to prevent damage and ensure longevity.
Creating the Blank
Once the wood type is selected, the next step is to create the surfboard blank. This involves shaping the wood into the desired surfboard outline. Tools typically required include:
- Jigsaw
- Planer
- Sanding tools
Begin by sketching the desired shape on the wood. Cut the rough outline with a jigsaw, then use the planer to refine the shape, ensuring a smooth finish. Sanding is critical to eliminate any rough edges and create a hydrodynamic surface.
Tool | Purpose | Recommended Use |
---|---|---|
Jigsaw | Initial cutting of the blank | To cut the rough outline |
Planer | Shaping and smoothing | To achieve the desired thickness |
Sander | Finishing | To prepare for lamination |
Laminating the Surfboard
Laminating the surfboard involves applying fiberglass and resin to strengthen the board and provide a waterproof surface. The process includes:
- Preparation: Ensure the surface of the blank is clean and sanded. Lay out fiberglass cloth on a flat surface.
- Resin Application: Mix the epoxy or polyester resin according to the manufacturer’s instructions. Use a brush or roller to apply the resin over the fiberglass cloth.
- Layering: Apply multiple layers of fiberglass for added strength. Typically, two to three layers are sufficient.
- Curing: Allow the resin to cure as per the instructions. This can take several hours to a day.
Be mindful of ventilation and safety when working with resin, as fumes can be harmful.
Finishing Touches
After the board has cured, it’s time to add the finishing touches. This includes shaping the fins, adding traction pads, and painting or varnishing the board.
For fins, you can either purchase ready-made fins or craft your own from wood or fiberglass. Attach them using resin and ensure they are aligned correctly for optimal performance.
To enhance aesthetics and durability, consider the following options:
- Paint: Use marine-grade paint for water resistance.
- Varnish: A clear coat adds shine and protection.
Regular maintenance is essential to prolong the life of your surfboard. After every use, rinse with fresh water and inspect for any damages.
Materials Needed for Building a Wooden Surfboard
Creating a wooden surfboard requires careful selection of materials to ensure durability, performance, and aesthetic appeal. Below is a list of essential materials:
- Wood Types:
- Paulownia
- Balsa
- Cedar
- Adhesives:
- Epoxy resin
- Wood glue
- Fin System:
- Fin boxes or glass-on fins
- Fiberglass Cloth:
- 4 oz or 6 oz fiberglass for strength
- Sandpaper:
- Various grits (80, 120, 220)
- Sealer and Finish:
- Marine varnish or oil finish
Designing Your Surfboard
Designing your surfboard involves determining its shape, dimensions, and overall aesthetics. Consider the following aspects:
- Dimensions:
- Length, width, and thickness will affect performance. A longer board generally provides stability, while a shorter board offers maneuverability.
- Shape:
- Outline shapes include fish, shortboard, longboard, and funboard. Each shape serves different surfing styles.
- Tail Design:
- Options include square, round, or swallow tails, influencing the board’s handling and speed.
- Color and Finish:
- Choose colors and patterns that reflect your style. The finish can enhance visual appeal and protect the wood.
Constructing the Board
The construction process requires precision and attention to detail. Follow these steps:
- Template Creation:
- Create a template of your design using plywood or cardboard.
- Wood Selection and Cutting:
- Select wood pieces according to your template. Use a jigsaw or bandsaw for accurate cuts.
- Lamination:
- For strength, laminate multiple layers of wood if necessary. Apply wood glue between layers and clamp them until dry.
- Shaping the Board:
- Use a planer and sanders to achieve the desired contour. Focus on achieving a smooth, aerodynamic shape.
Finishing Touches
The final touches are crucial for both performance and aesthetics:
- Sanding:
- Begin with coarse sandpaper and progress to finer grits, ensuring a smooth surface.
- Fiberglassing:
- Cut fiberglass cloth to size and lay it over the board. Apply epoxy resin, ensuring complete coverage. Use a squeegee to eliminate bubbles.
- Curing:
- Allow the resin to cure fully, following manufacturer instructions. This process may take several hours to days.
- Final Sanding and Sealing:
- Once cured, sand the board again to achieve a smooth finish. Apply marine varnish or oil as a protective sealant.
Installing the Fin System
The fin system is essential for stability and maneuverability. Here’s how to install it:
- Mark Fin Placement:
- Based on your design, mark where the fins will be placed on the board.
- Cut Fin Boxes:
- If using fin boxes, cut out the necessary slots. Ensure they fit snugly.
- Install Fins:
- For glass-on fins, attach them using epoxy. For fin boxes, insert and secure them according to manufacturer guidelines.
Testing and Adjustments
After completing your surfboard, testing is essential for performance validation:
- Test Ride:
- Take the board out on the water. Pay attention to its buoyancy, speed, and maneuverability.
- Adjustments:
- Make any necessary adjustments to the fin placement or shape based on performance feedback.
Expert Insights on Crafting Wooden Surfboards
Emily Carter (Master Craftsman, Surfboard Innovations). “Creating a wooden surfboard requires a deep understanding of both the wood’s properties and the hydrodynamics of surfboards. Selecting the right type of wood, such as paulownia or cedar, can significantly affect the board’s performance and durability.”
James O’Reilly (Surfboard Designer, WaveCraft Studios). “The shaping process is crucial. I recommend using a planer for the initial shaping and then refining with hand tools. This ensures that the contours are smooth and optimized for wave riding.”
Linda Tran (Environmental Sustainability Consultant, EcoSurf Boards). “Sustainability is key when making wooden surfboards. Sourcing wood from sustainable forests and using eco-friendly resins not only benefits the environment but also appeals to eco-conscious surfers.”
Frequently Asked Questions (FAQs)
What materials do I need to make a wooden surfboard?
You will need marine-grade plywood, epoxy resin, fiberglass cloth, a saw, sandpaper, clamps, and a surfboard template. Optional materials include a heat gun for shaping and a vacuum bag for laminating.
How long does it take to make a wooden surfboard?
The process typically takes between 20 to 40 hours, depending on your skill level and the complexity of the design. This includes time for shaping, laminating, and curing the resin.
What tools are essential for shaping a wooden surfboard?
Essential tools include a jigsaw or bandsaw for cutting the board, a planer for smoothing the surface, and various grades of sandpaper for finishing. A router can also be useful for adding details.
Can I use any type of wood for a surfboard?
Not all woods are suitable for surfboards. Choose lightweight, durable woods such as cedar, balsa, or marine plywood, which provide the necessary strength and buoyancy.
Is it difficult to make a wooden surfboard as a beginner?
While it can be challenging, beginners can successfully create a wooden surfboard with patience and practice. Following detailed plans and tutorials can significantly ease the learning curve.
What are the advantages of a wooden surfboard compared to foam boards?
Wooden surfboards offer enhanced durability, a unique aesthetic appeal, and a more traditional riding experience. They also provide better buoyancy and can be more environmentally friendly when sourced sustainably.
making a wooden surfboard is a rewarding and intricate process that combines craftsmanship with a deep appreciation for surfing culture. The journey begins with selecting the right type of wood, which not only affects the board’s performance but also its aesthetic appeal. Common choices include cedar, mahogany, and plywood, each offering unique characteristics in terms of weight, durability, and flexibility.
Once the wood is chosen, the shaping process is crucial. This involves cutting and sanding the wood to achieve the desired shape and dimensions. Attention to detail during this phase is essential, as it directly influences the board’s hydrodynamics and overall performance in the water. After shaping, the board must be sealed and finished properly to protect it from water damage and enhance its longevity.
Finally, the assembly and finishing touches, such as applying resin and fiberglass, are vital for ensuring the board is both functional and visually appealing. This step not only provides strength but also allows for creative expression through design. Overall, making a wooden surfboard requires patience, skill, and a passion for the craft, resulting in a unique and personalized piece of equipment that reflects the surfer’s individuality.
Key takeaways from this process include the importance of material selection, precision
Author Profile
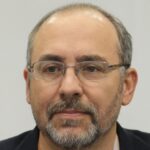
-
Mahlon Boehs is a seasoned entrepreneur and industry expert with a deep understanding of wood truss manufacturing and construction materials. As the President of Timberlake TrussWorks, LLC, Mahlon played a pivotal role in shaping the company’s reputation for quality and precision. His leadership ensured that each truss met rigorous structural standards, providing builders with dependable components essential to their projects.
Beginning in 2025, Mahlon Boehs has shifted his focus to education and knowledge-sharing through an informative blog dedicated to wood truss manufacturing. Drawing from his extensive experience in the field, he provides in-depth insights into truss design, material selection, and construction techniques. This blog serves as a valuable resource for builders, contractors, and homeowners seeking practical guidance on truss systems and structural integrity.
Latest entries
- March 18, 2025General Wood TopicsWhat Color Is Ebony Wood? Unveiling the Rich Hues of This Luxurious Timber
- March 18, 2025Construction & FrameworkHow Can You Effectively Mount a Headboard to Your Wall?
- March 18, 2025General Wood TopicsCan Bees Really Eat Wood? Unraveling the Myths and Facts
- March 18, 2025General Wood TopicsDo Rabbits Really Chew on Wood? Exploring Their Eating Habits!