How Do You Make Wood Bats? A Step-by-Step Guide to Crafting Your Own
Introduction
Crafting your own wooden baseball bat is not just a rewarding project; it’s a celebration of tradition, craftsmanship, and personal expression. Whether you’re a seasoned player looking to create a custom bat that perfectly suits your swing or a woodworking enthusiast eager to try your hand at a new skill, making wood bats combines art and functionality in a way that few other projects can. As you delve into the world of bat making, you’ll discover the nuances of selecting the right wood, shaping the bat to your specifications, and finishing it to perfection. Join us as we explore the fascinating process of transforming raw timber into a finely crafted instrument that can enhance your game and showcase your unique style.
Overview
The art of making wooden bats has been passed down through generations, with each craftsman bringing their own techniques and preferences to the table. The choice of wood is crucial, as different types impart varying characteristics to the bat’s performance and feel. From the classic maple and ash to more exotic woods, understanding the properties of each material is the first step in creating a bat that meets your specific needs.
Once the right wood is selected, the shaping process begins. This involves careful measurements and precise cuts to achieve the ideal weight, balance, and barrel size. The final touches,
Choosing the Right Wood
Selecting the appropriate type of wood is crucial for creating high-quality bats. Different woods provide varying levels of durability, weight, and performance. The most common types of wood used for bats include:
- Maple: Known for its hardness and density, maple bats are popular among professional players for their ability to withstand impact and provide a solid feel.
- Ash: Offers a lighter option that provides excellent flexibility and a larger sweet spot, making it a favorite among many players.
- Birch: A hybrid between maple and ash, birch combines the best features of both, providing durability and a larger sweet spot while maintaining a lighter weight.
Preparing the Wood
Once the wood type is selected, preparation is essential. The wood should be dried to a specific moisture content to ensure durability and prevent warping. The ideal moisture content for bat wood is typically around 8-12%.
- Drying Process:
- Air Drying: Place the wood in a well-ventilated area, allowing it to dry naturally over a few months.
- Kiln Drying: Use a kiln to rapidly reduce moisture content, which can be more efficient and controlled.
Shaping the Bat
Shaping the bat involves cutting the wood to the desired length and diameter. This process can be done using a lathe, which allows for precise control over the bat’s shape and dimensions.
- Steps for Shaping:
- Cut the wood to the rough length (usually around 34 inches for a full-sized bat).
- Mount the wood on a lathe, securing it tightly.
- Gradually shape the bat by removing material from the barrel, handle, and knob area, ensuring a consistent taper and proper balance.
Finishing Touches
After shaping the bat, the finishing process enhances durability and aesthetics. This typically involves sanding, sealing, and applying a finish.
- Sanding: Use progressively finer sandpaper to smooth the surface, starting with a coarse grit and moving to a finer grit.
- Sealing: Apply a wood sealant to protect against moisture and damage.
- Finishing: A clear coat or lacquer can be applied for a polished look and added protection.
Wood Type | Durability | Weight | Flexibility |
---|---|---|---|
Maple | High | Heavy | Low |
Ash | Medium | Light | High |
Birch | Medium-High | Medium | Medium |
By carefully selecting the wood, preparing it properly, shaping it accurately, and applying the right finish, you can create a high-quality wooden bat that meets your specific needs and preferences.
Choosing the Right Wood
Selecting the appropriate wood is crucial for creating high-quality bats. The most commonly used woods include:
- Maple: Known for its hardness and durability, maple provides a dense grain structure.
- Ash: Offers flexibility and a lighter weight, making it easier to swing.
- Birch: A hybrid of maple and ash, birch combines hardness with a degree of flexibility.
Factors to consider include:
- Weight: Heavier woods may offer more power, while lighter woods enhance swing speed.
- Grain: The straightness and tightness of the grain affect performance and durability.
- Moisture Content: Ideally, wood should have a moisture content of around 6-8% for optimal performance.
Shaping the Bat
Once the wood is selected, the bat is shaped using a lathe. This process involves several steps:
- Cutting the Blank: Start with a wood blank that is larger than the desired dimensions of the finished bat.
- Mounting: Secure the blank on the lathe with appropriate chucks to ensure stability during shaping.
- Turning: Gradually shape the bat by removing excess material, following the desired taper and barrel dimensions.
The dimensions typically include:
- Length: Common lengths range from 32 to 34 inches.
- Barrel Diameter: Standard diameters are between 2.5 to 2.75 inches.
- Handle Diameter: Usually about 0.9 to 1 inch, depending on player preference.
Finishing the Bat
After shaping, the finishing process enhances aesthetics and protects the wood:
- Sanding: Smooth the surface with progressively finer sandpaper (from 80 to 220 grit).
- Sealing: Apply a wood sealer to prevent moisture absorption.
- Staining/Painting: Optional, but can improve the appearance and provide a personalized touch.
A final coat of clear finish or lacquer will provide added protection against wear and tear.
Quality Control and Testing
Quality control is essential to ensure that the bats meet performance and safety standards. The following tests are recommended:
- Weight Check: Ensure consistency in weight across batches.
- Balance Test: Verify that the bat is balanced according to specifications.
- Performance Testing: Test for durability and performance using impact tests, simulating game conditions.
Packaging and Distribution
Once the bats pass quality control, packaging and distribution involve:
- Labeling: Clearly mark each bat with the brand, model, and specifications.
- Protective Packaging: Use bubble wrap or custom inserts to prevent damage during transport.
- Distribution Channels: Establish relationships with retailers or direct-to-consumer sales via online platforms.
Ensure that all packaging complies with industry standards and regulations to maintain product integrity.
Expert Insights on Crafting Wood Bats
Emily Carter (Master Woodworker, Timber Craft Journal). “The selection of the right type of wood is crucial when making baseball bats. Ash and maple are popular choices due to their balance of weight and durability, but understanding the grain structure can significantly influence the bat’s performance.”
David Thompson (Sports Equipment Engineer, Bat Performance Review). “When crafting wood bats, precision in the turning process is essential. A well-turned bat can enhance swing speed and control, which are vital for performance. Utilizing CNC technology can improve consistency in bat production.”
Linda Martinez (Baseball Coach and Equipment Specialist, Youth Sports Magazine). “It’s important to consider the player’s style and preference when designing a wood bat. Customization options, such as grip size and weight distribution, can greatly affect a player’s comfort and effectiveness at the plate.”
Frequently Asked Questions (FAQs)
What materials are best for making wood bats?
The best materials for making wood bats include solid hardwoods such as maple, ash, and birch. Each wood type offers different characteristics in terms of weight, durability, and flexibility.
What tools are required to make wood bats?
Essential tools for making wood bats include a lathe, chisels, sanders, a drill press, and measuring tools. Safety equipment such as goggles and gloves is also necessary.
What is the process for shaping a wood bat?
The process involves selecting a wood blank, mounting it on a lathe, and then shaping it to the desired specifications using chisels and sanders. The bat is gradually refined to achieve the correct weight and balance.
How do I finish a wood bat after shaping?
After shaping, the bat should be sanded to a smooth finish, followed by the application of a protective finish such as lacquer or polyurethane. This enhances durability and provides a polished appearance.
What are the common mistakes to avoid when making wood bats?
Common mistakes include improper measurements, uneven shaping, and inadequate finishing. Ensuring precision at each step is crucial for producing a quality bat.
Can I customize the design of my wood bat?
Yes, customization is possible. You can alter the length, weight, and barrel shape, as well as add personal engravings or paint designs to create a unique bat tailored to your preferences.
In summary, making wood bats involves a detailed process that requires careful selection of materials, precise shaping, and thorough finishing techniques. The choice of wood is crucial, with popular options including ash and maple, each offering unique characteristics in terms of weight, durability, and performance. Once the wood is selected, the bat must be cut to the desired length and diameter, followed by shaping the handle and barrel to achieve the right balance and feel for the player.
Additionally, the finishing process is vital for enhancing the bat’s appearance and longevity. This includes sanding the surface to a smooth finish, applying protective coatings, and ensuring that the bat meets specific regulations for use in various leagues. Attention to detail at every stage of production can significantly impact the bat’s performance on the field.
Key takeaways from the discussion on making wood bats highlight the importance of craftsmanship and material science in bat production. Understanding the properties of different woods and the impact of design choices can lead to the creation of high-quality bats tailored to the preferences of individual players. As such, aspiring bat makers should invest time in learning about the materials and techniques involved to produce bats that not only meet performance standards but also resonate with the players’ needs.
Author Profile
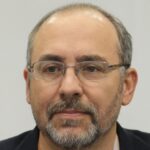
-
Darryl Norman is a seasoned entrepreneur and industry expert with a deep understanding of wood truss manufacturing and construction materials. As the President of Timberlake TrussWorks, LLC, Darryl played a pivotal role in shaping the company’s reputation for quality and precision. His leadership ensured that each truss met rigorous structural standards, providing builders with dependable components essential to their projects.
Beginning in 2025, Darryl Norman has shifted his focus to education and knowledge-sharing through an informative blog dedicated to wood truss manufacturing. Drawing from his extensive experience in the field, he provides in-depth insights into truss design, material selection, and construction techniques. This blog serves as a valuable resource for builders, contractors, and homeowners seeking practical guidance on truss systems and structural integrity.
Latest entries
- March 18, 2025General Wood TopicsWhat Color Is Ebony Wood? Unveiling the Rich Hues of This Luxurious Timber
- March 18, 2025Construction & FrameworkHow Can You Effectively Mount a Headboard to Your Wall?
- March 18, 2025General Wood TopicsCan Bees Really Eat Wood? Unraveling the Myths and Facts
- March 18, 2025General Wood TopicsDo Rabbits Really Chew on Wood? Exploring Their Eating Habits!