How Can You Create Your Own Wood Burning Stencils?
Wood burning, or pyrography, is an ancient art form that transforms simple wooden surfaces into stunning works of art. One of the most effective ways to elevate your wood burning projects is by using stencils. Stencils not only simplify the design process but also allow artists of all skill levels to create intricate patterns and images with precision. If you’ve ever admired beautifully crafted wooden pieces adorned with detailed designs and wondered how to achieve similar results, you’re in the right place. In this guide, we will explore the fascinating world of wood burning stencils, equipping you with the knowledge and techniques to create your own stunning designs.
Creating wood burning stencils can be a rewarding endeavor, blending creativity with craftsmanship. The process begins with selecting the right materials and tools, which are essential for achieving clean and precise designs. Whether you’re looking to create simple shapes or elaborate patterns, understanding the basics of stencil-making will set the foundation for your wood burning journey. From choosing the appropriate type of wood to preparing your stencil for use, each step plays a crucial role in the final outcome.
Once you have your stencil ready, the real fun begins! The art of wood burning allows for endless possibilities, from personalizing gifts to enhancing home décor. Stencils can help you
Choosing the Right Materials
Selecting appropriate materials is crucial for creating effective wood-burning stencils. The primary materials needed include:
- Stencil Material: Choose a flexible yet durable material. Common options include:
- Mylar sheets: These are reusable and can withstand high temperatures.
- Cardstock: Ideal for one-time use, but can warp under heat.
- Plastic sheets: Lightweight and often available in various thicknesses.
- Adhesive: A repositionable spray adhesive can help secure the stencil to the wood surface without damaging it.
- Wood: Ensure the wood is clean and smooth. Softwoods like pine are easier to work with than hardwoods but may burn more quickly.
- Burning Tool: A wood-burning pen with interchangeable tips offers versatility for different designs.
Designing Your Stencil
The stencil design process involves creating a pattern that fits your artistic vision. Here are the steps to follow:
- Choose a Design:
- Consider using software like Adobe Illustrator or free alternatives such as Inkscape to create or modify designs.
- Simplicity is key; intricate designs may be challenging to transfer to wood.
- Resize the Design:
- Adjust the dimensions to fit the wood piece you are working on.
- Print the design on standard paper to use as a template.
- Transfer the Design:
- Place the printed design under the stencil material and trace it using a fine-tipped marker or pen.
- Ensure that all elements are clearly defined for accurate burning.
Cutting the Stencil
Once the design is transferred, the next step is to cut out the stencil. This requires precision and the right tools:
- Use a craft knife or stencil cutter for clean cuts.
- Ensure your cutting surface is protected to avoid damage to your workspace.
Cutting Tips:
- Start with larger areas before moving to finer details.
- Maintain steady pressure to create smooth edges.
Preparing the Wood Surface
Before applying the stencil, prepare the wood surface to ensure optimal results.
- Sanding: Use fine-grit sandpaper to smooth the wood. This helps the stencil adhere better and provides a cleaner burn.
- Cleaning: Wipe the wood with a damp cloth to remove dust and debris. Allow it to dry completely before proceeding.
Applying the Stencil
Securing the stencil on the wood is vital for accuracy during the burning process. Follow these steps:
- Position the Stencil: Place the stencil on the wood, ensuring it is straight and centered.
- Adhere the Stencil: Lightly spray the back with repositionable adhesive to prevent slipping.
- Check Alignment: Before burning, double-check that the design is correctly aligned.
Wood Burning Process
With the stencil in place, you can begin the wood-burning process.
- Settings: Adjust your wood-burning tool to the appropriate temperature based on the wood type. Softer woods may require less heat.
- Technique: Use a steady hand and follow the stencil outline carefully.
- Pressure Control: Vary the pressure on the tool to create different burn depths and effects.
Material Type | Durability | Best Use |
---|---|---|
Mylar Sheets | High | Reusable stencils |
Cardstock | Medium | One-time use |
Plastic Sheets | Medium to High | Versatile applications |
This process will result in a beautifully burned design, ready for finishing touches such as sealing and staining if desired.
Materials Needed for Wood Burning Stencils
To create effective wood burning stencils, gather the following materials:
- Stencil Material:
- Mylar sheets
- Cardstock
- Thin plastic sheets
- Cutting Tools:
- Craft knife or X-Acto knife
- Scissors
- Cutting mat
- Wood Burning Tools:
- Wood burning pen or tool
- Various tips for detailing
- Additional Supplies:
- Pencil and eraser
- Ruler
- Tape or adhesive spray
- Sandpaper (optional)
Designing Your Stencil
Begin by creating a design that suits your project. Follow these steps:
- Choose a Design:
- Use graphic design software or hand-draw your design.
- Ensure the design has clear lines and open areas for burning.
- Scale the Design:
- Adjust the size to fit your wood piece using a ruler or design software.
- Print or trace the design onto your chosen stencil material.
- Transfer the Design:
- If using cardstock, trace the design directly onto the sheet.
- For Mylar or plastic, use adhesive spray to secure the design paper.
Cutting the Stencil
Carefully cut out the design to create your stencil:
- Secure the Material:
- Use tape to hold the stencil in place on the cutting mat.
- Cut the Design:
- Follow the lines meticulously with a craft knife for precision.
- Take your time to avoid tearing or damaging the stencil material.
- Clean Edges:
- After cutting, use sandpaper to smooth any rough edges, ensuring a clean burn.
Using the Stencil for Wood Burning
Once your stencil is ready, prepare to use it on wood:
- Select the Wood:
- Choose a smooth, clean piece of wood that fits your project.
- Position the Stencil:
- Secure the stencil to the wood using tape or adhesive to prevent movement.
- Heat the Wood Burning Tool:
- Plug in your wood burning pen and allow it to reach the desired temperature.
- Burn the Design:
- Carefully trace the stencil with the burning tool, applying consistent pressure.
- Move at a steady pace to achieve uniform depth in the burn.
Finishing Touches
After completing the wood burning, finalize your project:
- Remove the Stencil:
- Carefully peel away the stencil material.
- Clean Up:
- Use a soft cloth to remove any debris from the wood surface.
- Optional Sealing:
- Apply a wood finish or sealant to protect the design and enhance its appearance.
- Display or Use:
- Your wood burning project is now ready for display or functional use.
Tips for Success
Consider these tips for optimal results:
- Practice on scrap wood before working on your final piece.
- Experiment with different wood types to find your preferred results.
- Utilize various wood burning tips for different effects, such as shading or detailing.
- Always work in a well-ventilated area to avoid fumes from the wood burning process.
Expert Insights on Crafting Wood Burning Stencils
Emily Carter (Woodworking Instructor, Artisan Craft School). “Creating wood burning stencils requires precision and creativity. Start by selecting a design that complements the wood grain, and ensure your stencil material is sturdy enough to withstand the heat. My students often find that using a laser cutter for intricate designs yields the best results.”
Michael Tran (Professional Wood Artist, Timber & Flame). “For effective wood burning stencils, I recommend using a combination of cardstock and clear adhesive spray. This approach allows for easy application and removal, ensuring that the wood surface remains intact after burning. Always test your stencil on scrap wood first to adjust for any inconsistencies.”
Linda Foster (DIY Craft Blogger, Crafting Chronicles). “When making wood burning stencils, consider the thickness of your stencil material. Thinner materials can warp under heat, leading to uneven burns. I advise using a thicker plastic or metal for durability, and always secure your stencil with painter’s tape to prevent movement during the burning process.”
Frequently Asked Questions (FAQs)
What materials do I need to make wood burning stencils?
To create wood burning stencils, you will need stencil paper or mylar sheets, a craft knife or scissors, a cutting mat, a wood burning tool, and a piece of wood for burning.
How do I design a stencil for wood burning?
Design your stencil by sketching your desired pattern on paper or using graphic design software. Ensure the design has clear lines and shapes, then transfer it onto stencil paper or mylar sheets for cutting.
What is the best method for cutting stencils?
The best method for cutting stencils is to use a sharp craft knife on a cutting mat. This allows for precision and control, ensuring clean edges and accurate shapes.
Can I use store-bought stencils for wood burning?
Yes, store-bought stencils can be used for wood burning. Ensure they are made from a heat-resistant material and are suitable for the size of your wood piece.
How do I transfer a stencil design onto wood?
To transfer a stencil design onto wood, place the stencil on the wood surface and trace around the edges with a pencil. Alternatively, you can use carbon paper between the stencil and wood for a more precise transfer.
What safety precautions should I take while wood burning?
When wood burning, always work in a well-ventilated area, use protective eyewear, and ensure your workspace is free from flammable materials. Additionally, allow the wood burning tool to cool down before handling.
creating wood burning stencils is a rewarding process that combines creativity with craftsmanship. The fundamental steps involve selecting a suitable design, preparing the stencil material, and ensuring proper alignment on the wood surface. By utilizing materials such as cardstock or mylar, artisans can achieve precise and clean designs that enhance the final piece. Additionally, the use of a wood burner with adjustable temperature settings allows for greater control over the burning process, ensuring that the design is executed flawlessly.
Key takeaways from the discussion include the importance of careful planning and preparation before starting the wood burning project. This includes choosing the right type of wood, as different woods react differently to burning. Furthermore, understanding the tools and techniques, such as the use of different tips on the wood burner, can significantly impact the quality of the final artwork. Practicing on scrap wood before applying the stencil to the final piece can also help in refining skills and achieving the desired outcome.
Ultimately, wood burning stencils not only serve as a means to create intricate designs but also allow for personal expression and creativity. By following the outlined steps and tips, individuals can successfully produce stunning wood-burned art that showcases their unique style and craftsmanship. With patience and practice, anyone can master the
Author Profile
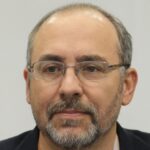
-
Darryl Norman is a seasoned entrepreneur and industry expert with a deep understanding of wood truss manufacturing and construction materials. As the President of Timberlake TrussWorks, LLC, Darryl played a pivotal role in shaping the company’s reputation for quality and precision. His leadership ensured that each truss met rigorous structural standards, providing builders with dependable components essential to their projects.
Beginning in 2025, Darryl Norman has shifted his focus to education and knowledge-sharing through an informative blog dedicated to wood truss manufacturing. Drawing from his extensive experience in the field, he provides in-depth insights into truss design, material selection, and construction techniques. This blog serves as a valuable resource for builders, contractors, and homeowners seeking practical guidance on truss systems and structural integrity.
Latest entries
- March 18, 2025General Wood TopicsWhat Color Is Ebony Wood? Unveiling the Rich Hues of This Luxurious Timber
- March 18, 2025Construction & FrameworkHow Can You Effectively Mount a Headboard to Your Wall?
- March 18, 2025General Wood TopicsCan Bees Really Eat Wood? Unraveling the Myths and Facts
- March 18, 2025General Wood TopicsDo Rabbits Really Chew on Wood? Exploring Their Eating Habits!