How Can You Make Wood Coasters Waterproof for Long-lasting Use?
Wood coasters are not only functional but also add a touch of warmth and style to any home decor. However, without proper treatment, they can quickly become damaged by moisture, leading to unsightly stains and warping. If you’ve invested time and effort into crafting or selecting beautiful wooden coasters, ensuring their longevity is essential. In this article, we will explore effective methods to make your wood coasters waterproof, preserving their beauty and functionality for years to come. Whether you’re a DIY enthusiast or simply looking to protect your favorite pieces, you’ll find valuable insights that will elevate your coaster care game.
To start, understanding the nature of wood and its interaction with liquids is crucial. Wood is a porous material, which means it can absorb moisture, leading to potential damage. By applying the right waterproofing techniques, you can create a barrier that prevents liquid penetration while maintaining the aesthetic appeal of the wood. Various products and methods are available, each with its own benefits and considerations, making it essential to choose the right approach for your specific coasters.
In this guide, we will delve into several popular waterproofing options, from sealants and finishes to natural oils and waxes. Each method has its unique characteristics, and we will discuss how to apply them effectively to achieve the
Choosing the Right Waterproofing Product
When selecting a waterproofing product for wood coasters, consider the following options:
- Polyurethane: This is a popular choice due to its durability and resistance to water. It forms a hard protective layer.
- Epoxy Resin: Known for its excellent waterproofing properties, epoxy resin creates a thick, glossy finish that is highly resistant to moisture.
- Varnish: Oil-based varnishes can provide good water resistance and enhance the natural beauty of the wood.
- Sealants: Specifically designed to penetrate wood, sealants provide a waterproof barrier while allowing the wood to breathe.
When choosing a product, ensure it is specifically labeled for wood applications to achieve optimal results.
Preparation of Wood Coasters
Before applying any waterproofing product, proper preparation of the wood is essential. Follow these steps:
- Sanding: Start with a medium-grit sandpaper (around 120 grit) and work your way to a fine-grit sandpaper (220 grit). This will smooth the surface and help the waterproofing agent adhere better.
- Cleaning: Remove dust and debris using a damp cloth or a vacuum. Ensure the surface is completely dry before application.
- Sealing Edges: If the wood is porous, consider sealing the edges to prevent water absorption. This can be done using a clear wood sealant.
Application Process
The application of the waterproofing product will vary depending on the type used. Here’s a general guide:
- Mixing: If using epoxy resin, thoroughly mix the components as per the manufacturer’s instructions.
- Application:
- Use a brush or foam applicator to apply the first coat evenly.
- Ensure all surfaces, including edges, are covered.
- Drying Time: Allow the first coat to dry completely. Refer to the product instructions for specific drying times.
- Sanding Between Coats: Lightly sand the surface with fine-grit sandpaper before applying additional coats to enhance adhesion.
- Number of Coats: Generally, 2-3 coats are recommended for optimal waterproofing.
Maintenance of Waterproofed Coasters
To ensure longevity and maintain the waterproof properties of your wood coasters, follow these maintenance tips:
- Regular Cleaning: Wipe coasters with a damp cloth; avoid soaking them in water.
- Reapplication: Depending on usage, reapply the waterproofing product every 1-2 years to maintain effectiveness.
- Storage: When not in use, store coasters in a cool, dry place to prevent moisture buildup.
Comparison of Waterproofing Options
Product Type | Durability | Ease of Application | Finish |
---|---|---|---|
Polyurethane | High | Moderate | Glossy |
Epoxy Resin | Very High | Challenging | Thick and Glossy |
Varnish | Moderate to High | Easy | Natural Look |
Sealants | Moderate | Easy | Clear |
By understanding the various waterproofing options and following the proper application and maintenance techniques, you can ensure that your wood coasters remain beautiful and functional for years to come.
Choosing the Right Waterproofing Product
Selecting an appropriate waterproofing product is crucial for protecting wood coasters. Various options are available, each with distinct properties suited to different types of wood and usage scenarios.
- Polyurethane Sealers: These provide a durable, clear finish that resists water and scratches.
- Epoxy Resins: Ideal for creating a thick, hard coating that offers excellent waterproofing and durability.
- Marine Varnish: Specifically designed for high-moisture environments, offering superior protection against water damage.
- Wood Oils: While not completely waterproof, certain oils can add a degree of water resistance and enhance the wood’s natural beauty.
Preparation of Wood Coasters
Before applying any waterproofing product, proper preparation of the wood surface is essential to ensure optimal adhesion and performance.
- Sanding: Use fine-grit sandpaper (220 grit) to smooth the surface and edges of the coasters. This promotes better product adhesion.
- Cleaning: Remove dust and debris with a damp cloth. Allow the coasters to dry completely before proceeding.
- Conditioning (Optional): For certain types of wood, applying a wood conditioner can help achieve a more uniform finish.
Application Techniques
Effective application techniques ensure even coverage and long-lasting protection of the wood coasters.
- Brush Application: Use a high-quality synthetic brush for water-based products or a natural bristle brush for oil-based products. Apply in long, even strokes.
- Spray Application: For epoxy or polyurethane, consider using a spray applicator for a smooth, even coat. Maintain a distance of 6-12 inches from the surface.
- Roller Application: A foam roller can be used for larger areas, ensuring minimal bubbles and a smooth finish.
Recommended Application Process
Follow these steps for applying waterproofing products to wood coasters:
Step | Description |
---|---|
First Coat | Apply the initial coat generously, covering all surfaces. Allow to dry according to the manufacturer’s instructions. |
Second Coat | Lightly sand the first coat once dry to promote adhesion. Apply the second coat, ensuring even distribution. |
Final Coat | Depending on the product, a third coat may be beneficial for enhanced protection. Repeat the drying and sanding process as needed. |
Drying and Curing Times
Understanding drying and curing times for the chosen product is critical for achieving optimal results.
- Water-Based Polyurethane: Typically dries to the touch in 1-2 hours, but requires 24 hours for full curing.
- Oil-Based Polyurethane: Usually takes 4-6 hours to dry to the touch, with a full cure time of 48 hours.
- Epoxy Resins: Generally, these will set in about 4-6 hours but may require 72 hours for complete curing.
Maintenance and Care
Proper maintenance extends the life of your waterproofed wood coasters. Implement the following care practices:
- Cleaning: Use a damp cloth for regular cleaning, avoiding harsh chemicals that could damage the finish.
- Reapplication: Depending on usage, consider reapplying the waterproofing product every 1-2 years to maintain effectiveness.
- Storage: When not in use, store coasters in a dry, cool place to minimize exposure to moisture.
Testing Waterproofing Effectiveness
After completing the waterproofing process, it’s essential to test the effectiveness of the coating.
- Water Drop Test: Place a few drops of water on the coaster. If the water beads up and does not soak in, the waterproofing is effective.
- Stain Test: Leave a damp glass on the coaster for a few hours. Check for any discoloration or water marks afterward.
Following these guidelines will ensure that your wood coasters are not only aesthetically pleasing but also well-protected against moisture damage.
Expert Strategies for Waterproofing Wood Coasters
Dr. Emily Carter (Wood Finishing Specialist, TimberTech Solutions). “To effectively waterproof wood coasters, I recommend using a high-quality marine varnish. This type of finish not only provides a durable barrier against moisture but also enhances the natural beauty of the wood. Ensure you apply at least three coats, allowing adequate drying time between each application for optimal results.”
Mark Thompson (DIY Home Improvement Expert, Craft & Build Magazine). “For a more natural approach, consider using a mixture of beeswax and mineral oil. This combination not only protects the wood from water damage but also nourishes the fibers, prolonging the life of your coasters. Apply the mixture liberally, let it soak in, and then buff off the excess for a beautiful finish.”
Linda Chen (Interior Design Consultant, Eco-Friendly Living). “If you are looking for an eco-conscious option, I suggest using a water-based polyurethane. This product is less toxic compared to traditional oil-based finishes and provides excellent waterproofing capabilities. Make sure to choose a product labeled as food-safe if you plan to use the coasters for beverages.”
Frequently Asked Questions (FAQs)
How can I make wood coasters waterproof?
To make wood coasters waterproof, apply a sealant such as polyurethane or epoxy resin. These products create a durable barrier against moisture.
What type of sealant is best for wood coasters?
Polyurethane is often recommended for its durability and resistance to water. Epoxy resin provides a thicker, more robust coating, ideal for high-use coasters.
How many coats of sealant should I apply?
Typically, two to three coats of sealant are recommended. Allow each coat to dry completely before applying the next for optimal protection.
Can I use regular paint as a waterproofing method?
Regular paint is not advisable for waterproofing wood coasters. It may not provide the necessary durability and moisture resistance required for effective protection.
How long does the waterproofing process take?
The waterproofing process can take several hours to a few days, depending on the type of sealant used and the drying times specified by the manufacturer.
Is it necessary to sand the wood before applying sealant?
Yes, sanding the wood surface is essential. It helps the sealant adhere better and provides a smoother finish, enhancing the overall appearance and effectiveness.
making wood coasters waterproof is an essential step in ensuring their longevity and functionality. The process typically involves selecting the right type of wood, preparing the surface properly, and applying a suitable waterproofing finish. Common methods include using sealants such as polyurethane, epoxy resin, or specialized wood finishes that offer water resistance. Each of these options has its own application techniques and drying times, which should be carefully followed to achieve the best results.
It is important to note that surface preparation plays a crucial role in the effectiveness of the waterproofing process. Sanding the wood to a smooth finish not only enhances the appearance but also allows the waterproofing agents to adhere better. Additionally, applying multiple coats of the chosen finish can significantly improve the durability of the coasters against moisture and spills.
Lastly, regular maintenance is vital for preserving the waterproof qualities of the coasters over time. Periodically reapplying the waterproof finish, especially after heavy use, can help maintain their protective barrier. By following these steps, wood coasters can remain functional and aesthetically pleasing for years to come, making them a worthwhile investment for any home or gathering.
Author Profile
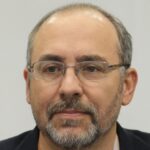
-
Darryl Norman is a seasoned entrepreneur and industry expert with a deep understanding of wood truss manufacturing and construction materials. As the President of Timberlake TrussWorks, LLC, Darryl played a pivotal role in shaping the company’s reputation for quality and precision. His leadership ensured that each truss met rigorous structural standards, providing builders with dependable components essential to their projects.
Beginning in 2025, Darryl Norman has shifted his focus to education and knowledge-sharing through an informative blog dedicated to wood truss manufacturing. Drawing from his extensive experience in the field, he provides in-depth insights into truss design, material selection, and construction techniques. This blog serves as a valuable resource for builders, contractors, and homeowners seeking practical guidance on truss systems and structural integrity.
Latest entries
- March 18, 2025General Wood TopicsWhat Color Is Ebony Wood? Unveiling the Rich Hues of This Luxurious Timber
- March 18, 2025Construction & FrameworkHow Can You Effectively Mount a Headboard to Your Wall?
- March 18, 2025General Wood TopicsCan Bees Really Eat Wood? Unraveling the Myths and Facts
- March 18, 2025General Wood TopicsDo Rabbits Really Chew on Wood? Exploring Their Eating Habits!