How Can You Craft Your Own Wood Flute?
Creating music with a wood flute is an enchanting experience that connects the maker to ancient traditions and natural craftsmanship. The warm, resonant tones of a wooden flute can evoke emotions and transport listeners to serene landscapes. Whether you’re a seasoned musician or a curious beginner, learning how to make a wood flute can be a rewarding journey that combines artistry, skill, and a deep appreciation for sound. In this article, we will explore the fascinating process of crafting your very own wood flute, from selecting the right materials to understanding the intricacies of sound production.
Overview
Making a wood flute involves a blend of woodworking techniques and an understanding of acoustics. The choice of wood is crucial, as different types can significantly influence the instrument’s tone and playability. Once the right wood is selected, the crafting process begins, which includes shaping the body, creating the embouchure hole, and fine-tuning the finger holes to achieve the desired pitch. Each step requires precision and patience, but the result is a unique instrument that reflects the maker’s personal touch.
In addition to the technical aspects, crafting a wood flute is also an opportunity for self-expression. The design can be customized to reflect individual style, whether through decorative carvings or the choice of finish. As you delve deeper
Choosing the Right Wood
When selecting wood for your flute, it is crucial to consider both the type of wood and its characteristics. Different woods produce distinct tonal qualities and resonance. Common choices include:
- Maple: Offers a bright sound with good projection.
- Cherry: Provides a warm tone with a rich timbre.
- Cedar: Known for its soft, mellow sound, ideal for beginners.
- Bamboo: A popular choice for its lightweight and resonant properties.
Each type of wood has unique properties, and experimenting with various types can lead to discovering your preferred sound.
Tools and Materials Needed
To create a wood flute, you will need specific tools and materials. Here is a comprehensive list:
Tool/Material | Purpose |
---|---|
Wood Blank | Body of the flute |
Drill | To create finger holes |
Ruler | For measuring lengths |
Saw | To cut the wood to size |
Files and Sandpaper | For smoothing edges and shaping |
Tuner | To check pitch accuracy |
Having the right tools will streamline the flute-making process and enhance the quality of the final product.
Shaping the Flute
Begin by cutting the wood blank to your desired length, typically between 24 and 30 inches for a standard flute. The length will affect the pitch; longer flutes produce lower notes while shorter flutes yield higher pitches.
Once the wood is cut, shape the exterior using files and sandpaper. Aim for a smooth surface, which is essential for both aesthetics and acoustics. Pay special attention to the ends, ensuring they are rounded to facilitate airflow.
Creating the Finger Holes
The placement and size of the finger holes are critical to achieving the correct pitch and playability. Follow these guidelines:
- Hole Size: Generally, holes should be about 1/4 inch in diameter.
- Spacing: Typically, holes are spaced about 1.5 inches apart, though this may vary based on the size of your hands and preferred fingering.
- Testing: Drill holes incrementally and test the pitch as you go; this ensures you can fine-tune their sizes and locations.
Use a drill to create the holes, and then smooth the edges with sandpaper to prevent splinters.
Tuning the Flute
After shaping the flute and creating the finger holes, it is crucial to tune it. Use a tuner to check the pitch of each note as you cover and uncover the finger holes. Adjustments can be made by slightly enlarging or repositioning the holes. The goal is to achieve a uniform scale across all notes.
- Check the fundamental tone first.
- Adjust each hole systematically while playing the flute.
- Record measurements for future reference.
Following these steps will lead you to a well-crafted wood flute with a pleasing sound.
Materials Needed
To craft a wood flute, gathering the right materials is essential for achieving optimal sound quality and durability. The following list outlines the primary materials required:
- Wood: Choose a dense, straight-grained hardwood such as:
- Maple
- Cherry
- Walnut
- Birch
- Tools:
- Chisels (various sizes)
- Drill with bits (for finger holes and embouchure)
- Sandpaper (various grits)
- Saw (preferably a band saw)
- Ruler or caliper
- Tape measure
- Wood glue
- Finish: Options for sealing the wood to protect it include:
- Tung oil
- Shellac
- Lacquer
Design Considerations
Before starting the construction, planning the design is crucial. Consider the following aspects:
- Length and Diameter: The fundamental pitch of the flute is influenced by its length and bore diameter. A typical concert flute is about 26 inches long with a bore diameter of 0.5 inches.
- Embouchure Hole: The size and position of the embouchure hole, where the player blows air into the flute, affect tone quality. A common size ranges from 1/4 to 1/2 inch in diameter.
- Finger Holes: The number of finger holes usually ranges from 6 to 8, depending on the intended range. The spacing and size of these holes are critical for comfortable playing and intonation.
Construction Steps
The construction of the wood flute involves careful attention to detail. Follow these steps for a successful build:
- Cut the Wood:
- Cut a length of wood to your desired flute length.
- Ensure the ends are square.
- Drill the Bore:
- Use a drill bit to create a bore running through the entire length of the wood. The diameter should match your design specifications.
- Create the Embouchure Hole:
- Mark the position for the embouchure hole approximately one-third from the top of the flute.
- Carefully drill or carve the hole to the desired dimensions.
- Drill Finger Holes:
- Mark and drill the finger holes according to your design.
- Start with smaller holes and gradually enlarge them if necessary.
- Shape the Flute:
- Use chisels and sandpaper to refine the exterior of the flute. Aim for a smooth, ergonomic shape.
- Finish the Surface:
- Sand the flute thoroughly using various grits of sandpaper.
- Apply a protective finish to enhance durability and appearance.
Tuning the Flute
Once the flute is constructed, tuning is essential to ensure it produces the correct pitches. Follow these guidelines:
- Tuning Procedure:
- Use a tuner to check the pitch of each note.
- Adjust the length of the flute by trimming the end to raise the pitch.
- For lowering the pitch, enlarge the finger holes slightly or adjust the embouchure hole.
- Fine-Tuning:
- Test the flute by playing each note and listening for intonation.
- Make incremental adjustments, re-checking the pitch after each modification.
Maintenance and Care
To maintain the quality and longevity of your wood flute, consider these care tips:
- Cleaning:
- Wipe the flute with a soft, dry cloth after each use to remove moisture.
- Storage:
- Store in a protective case to prevent damage.
- Regular Checks:
- Inspect for cracks or wear, especially after changes in humidity or temperature.
- Reapplying Finish:
- Reapply your chosen finish periodically to protect the wood from moisture absorption.
Expert Insights on Crafting Wood Flutes
Emily Carter (Master Woodwind Artisan, FluteCraft Studios). “Creating a wood flute requires a deep understanding of both the material and the acoustics involved. Selecting the right type of wood, such as grenadilla or bamboo, is crucial as it affects the tonal quality. Precision in crafting the bore and embouchure hole is essential to achieve a rich sound.”
David Lin (Acoustic Engineer, SoundWave Innovations). “When making a wood flute, one must consider the physics of sound production. The length and diameter of the flute directly influence its pitch. Therefore, careful measurements and adjustments during the crafting process are necessary to ensure the instrument plays in tune.”
Sarah Thompson (Ethnomusicologist, Global Flute Society). “The cultural significance of wood flutes cannot be overstated. When crafting a flute, it’s important to respect the traditions and techniques that have been passed down through generations. This not only honors the craft but also enhances the authenticity of the instrument.”
Frequently Asked Questions (FAQs)
What materials are needed to make a wood flute?
To make a wood flute, you will need a suitable piece of wood (such as cedar, bamboo, or maple), a saw, a drill with various bit sizes, sandpaper, wood glue, and a finish such as oil or lacquer.
What are the basic steps to construct a wood flute?
The basic steps include selecting and preparing the wood, shaping the body of the flute, drilling the finger holes, crafting the embouchure (mouthpiece), sanding the entire instrument, and applying a protective finish.
How do I determine the correct dimensions for the flute?
The dimensions depend on the desired key and pitch. Generally, a longer flute produces a lower pitch, while a shorter flute yields a higher pitch. Specific measurements can be found in flute-making guides or templates.
What techniques can I use to ensure proper tuning?
To ensure proper tuning, you can adjust the size and placement of the finger holes, as well as the length of the flute. Tuning can be tested using a tuner or by ear, making incremental adjustments as necessary.
Can I use power tools to make a wood flute?
Yes, power tools can expedite the process of making a wood flute. However, precision is crucial, so careful handling and attention to detail are essential when using tools like drills and saws.
Is it necessary to have prior woodworking experience to make a wood flute?
While prior woodworking experience can be beneficial, it is not strictly necessary. With careful planning, patience, and following detailed instructions, beginners can successfully create a wood flute.
making a wood flute involves a series of carefully considered steps, each contributing to the overall quality and sound of the instrument. The process begins with selecting the right type of wood, as different woods can significantly affect the flute’s tonal qualities. Common choices include hardwoods like maple, cherry, or walnut, which provide durability and rich sound. Properly preparing the wood through cutting, sanding, and drilling is crucial to achieving the desired dimensions and acoustics.
Furthermore, the crafting process includes shaping the flute, creating the embouchure hole, and tuning the instrument. Each of these elements requires precision and an understanding of acoustics to ensure that the flute produces a pleasing sound. Additionally, finishing the wood with appropriate oils or lacquers not only enhances the aesthetic appeal but also protects the instrument from environmental factors.
Key takeaways from the discussion include the importance of wood selection, the precision required in crafting, and the impact of finishing techniques on the flute’s performance. By following a systematic approach and paying attention to detail, anyone can create a wood flute that is both functional and beautiful. Ultimately, the satisfaction derived from crafting a handmade instrument is a rewarding experience that connects the maker to a rich tradition of musical craftsmanship.
Author Profile
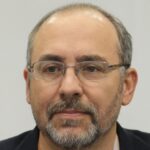
-
Darryl Norman is a seasoned entrepreneur and industry expert with a deep understanding of wood truss manufacturing and construction materials. As the President of Timberlake TrussWorks, LLC, Darryl played a pivotal role in shaping the company’s reputation for quality and precision. His leadership ensured that each truss met rigorous structural standards, providing builders with dependable components essential to their projects.
Beginning in 2025, Darryl Norman has shifted his focus to education and knowledge-sharing through an informative blog dedicated to wood truss manufacturing. Drawing from his extensive experience in the field, he provides in-depth insights into truss design, material selection, and construction techniques. This blog serves as a valuable resource for builders, contractors, and homeowners seeking practical guidance on truss systems and structural integrity.
Latest entries
- March 18, 2025General Wood TopicsWhat Color Is Ebony Wood? Unveiling the Rich Hues of This Luxurious Timber
- March 18, 2025Construction & FrameworkHow Can You Effectively Mount a Headboard to Your Wall?
- March 18, 2025General Wood TopicsCan Bees Really Eat Wood? Unraveling the Myths and Facts
- March 18, 2025General Wood TopicsDo Rabbits Really Chew on Wood? Exploring Their Eating Habits!