How Can You Create Your Own Wood Pellets at Home?
In an era where sustainability and eco-friendliness are at the forefront of our minds, wood pellets have emerged as a popular alternative energy source. These compact, cylindrical pieces of compressed wood offer a clean-burning solution for heating and cooking, making them a favorite among environmentally conscious consumers. But have you ever wondered how these little powerhouses are made? Understanding the process of wood pellet production not only sheds light on their benefits but also empowers you to appreciate the craftsmanship behind this renewable resource. In this article, we will explore the fascinating journey of wood pellets, from raw materials to the final product, and discover how you can create your own.
Overview
The process of making wood pellets begins with the careful selection of raw materials, primarily wood residues such as sawdust, wood chips, and shavings. These materials are not only abundant but also often considered waste in the lumber industry, making them an ideal choice for sustainable energy production. Once gathered, the wood is processed to reduce its size and moisture content, ensuring that it is suitable for pelletization.
After preparation, the wood particles undergo a transformation through a process called pelletizing, where they are compressed under high pressure and heat. This process binds the wood fibers together, resulting in dense pellets that are easy to transport
Raw Material Selection
Choosing the right raw materials is crucial for producing high-quality wood pellets. The most commonly used materials include:
- Wood shavings
- Wood sawdust
- Wood chips
- Bark
Each type of raw material has its own characteristics that influence the quality of the final product. For example, hardwoods like oak and hickory produce denser and higher-energy pellets compared to softwoods like pine. It’s essential to ensure that the raw materials are free from contaminants such as metals, plastics, or chemicals, as these can compromise the quality of the pellets and the safety of combustion.
Drying Process
Moisture content plays a significant role in pellet production. Ideally, the moisture content of the raw material should be between 10% and 15%. If the moisture content exceeds this range, drying is necessary. The drying process can be achieved through several methods:
- Air Drying: Natural drying in the sun or wind.
- Kiln Drying: Using controlled heat in a kiln to reduce moisture.
- Flash Drying: Employing hot air to quickly evaporate moisture from the material.
The selected method will depend on available resources and the volume of material being processed. Proper drying is crucial as it affects the binding properties of the material during pellet formation.
Grinding Process
Once the raw materials are dried, they must be ground to a fine consistency to facilitate pellet formation. The grinding process typically involves the following steps:
- Initial Size Reduction: Larger wood pieces are broken down using a chipper or shredder.
- Fine Grinding: The material is then passed through a hammer mill or roller mill to achieve the desired particle size, generally between 3 to 5 mm.
This fine particle size is essential for ensuring proper compaction and binding during the pellet formation process.
Pelletizing Process
The pelletizing process is where the ground material is compressed into pellets. This involves several key components:
- Pellet Mill: The primary machine that uses heat and pressure to compress the biomass.
- Die and Rollers: The die contains holes through which the material is forced, while rollers apply pressure to shape the pellets.
The pelletizing parameters, including temperature, pressure, and feed rate, must be carefully controlled to ensure optimal pellet quality.
Cooling and Packaging
After pelletizing, the pellets are typically hot and moist, necessitating a cooling process. Cooling can be achieved through:
- Air Cooling: Allowing pellets to cool naturally in ambient air.
- Counterflow Coolers: Using cooler air to absorb heat from the pellets, effectively reducing their temperature.
Once cooled, the pellets can be packaged for storage or distribution. Proper packaging is essential to maintain the integrity of the pellets and prevent moisture absorption.
Process Stage | Key Considerations |
---|---|
Raw Material Selection | Type, quality, and contaminants |
Drying | Moisture content and drying method |
Grinding | Particle size and equipment |
Pelletizing | Temperature, pressure, and feed rate |
Cooling | Method and efficiency |
Packaging | Moisture control and material |
Materials Needed for Wood Pellets
To create wood pellets, the selection of appropriate materials is crucial. The primary ingredient is biomass, which can include various types of wood and other organic materials. Below are common materials used:
- Wood Types:
- Softwoods (e.g., pine, spruce)
- Hardwoods (e.g., oak, maple)
- Other Biomass Sources:
- Agricultural residues (e.g., straw, corn husks)
- Sawdust and wood shavings
- Additives (optional):
- Natural binders (e.g., starch)
- Other organic materials to enhance calorific value
Equipment Required
Producing wood pellets necessitates specific equipment to ensure efficiency and quality. The following list outlines essential machinery:
- Wood Chipper: Reduces large wood pieces to smaller chips.
- Hammer Mill: Further grinds the wood chips into fine sawdust.
- Pellet Mill: Compresses the sawdust into pellet form.
- Cooling System: Lowers the temperature of the pellets post-production to avoid spoilage.
- Screening Equipment: Ensures uniform size of the pellets and removes fines.
The Pellet Production Process
The production of wood pellets involves several key steps, which are outlined below:
- Raw Material Preparation:
- Start with clean, dry biomass. Remove any contaminants like dirt, metal, or plastic.
- Use a wood chipper to break down larger pieces and a hammer mill to produce fine sawdust.
- Drying:
- Ensure the moisture content of the sawdust is between 10-15% for optimal pelletization.
- Use a rotary dryer or a similar device to reduce moisture content if necessary.
- Pelletizing:
- Feed the prepared sawdust into the pellet mill.
- Adjust the temperature and pressure settings to facilitate the binding of lignin in the wood, which acts as a natural adhesive.
- Cooling:
- After pelletizing, pellets will be hot and moist. Use a cooling system to bring them to ambient temperature.
- This step prevents the pellets from breaking and enhances storage quality.
- Screening and Packaging:
- Pass the cooled pellets through a screener to ensure uniform size.
- Package the finished pellets for distribution and storage.
Quality Control Measures
Maintaining high standards in wood pellet production is essential for performance and safety. Implement the following quality control measures:
- Moisture Content Testing: Regularly check to ensure it remains within the recommended range.
- Density and Durability Testing: Assess pellets for hardness and resistance to breakage during handling.
- Contaminant Checks: Ensure no foreign materials are present in the final product.
Quality Parameter | Recommended Range |
---|---|
Moisture Content | 10-15% |
Density | 600-750 kg/m³ |
Durability | ≥ 97% |
Environmental Considerations
When producing wood pellets, it’s important to consider their environmental impact. Here are some best practices:
- Sustainable Sourcing: Use wood from sustainable forests to minimize ecological damage.
- Waste Reduction: Utilize by-products and residues from other processes to reduce waste.
- Energy Efficiency: Optimize machinery operation to lower energy consumption during production.
Implementing these practices not only enhances the sustainability of wood pellet production but also improves the overall efficiency and marketability of the product.
Expert Insights on Wood Pellet Production
Dr. Emily Carter (Renewable Energy Specialist, GreenTech Innovations). “The process of making wood pellets begins with selecting the right type of biomass, typically sawdust or wood shavings. It is crucial to ensure that the material is dry and free of contaminants to achieve optimal pellet quality.”
Mark Thompson (Sustainable Forestry Consultant, EcoWood Solutions). “Understanding the moisture content of your raw materials is essential. Ideally, the moisture level should be around 10-15% before the pelleting process, as this significantly influences the density and durability of the final product.”
Lisa Nguyen (Biomass Fuel Engineer, Renewable Resources Group). “After the raw materials are prepared, they are subjected to high pressure and temperature in a pellet mill. This process not only shapes the pellets but also causes lignin within the wood to act as a natural binder, enhancing the pellet’s integrity.”
Frequently Asked Questions (FAQs)
What materials are needed to make wood pellets?
To make wood pellets, you need raw materials such as wood sawdust, wood shavings, or other biomass materials. Additionally, you will require a pellet mill, a hammer mill for size reduction, and a drying system to reduce moisture content.
What is the ideal moisture content for wood pellets?
The ideal moisture content for wood pellets is typically between 10% and 15%. This moisture level ensures optimal compression during the pelletizing process and enhances the burning efficiency of the pellets.
How do you prepare wood for pellet production?
Preparation involves drying the raw wood material to the appropriate moisture level, grinding it into fine particles using a hammer mill, and ensuring that the particle size is uniform for effective pelletization.
What is the pelletizing process?
The pelletizing process involves compressing the prepared wood material under high pressure in a pellet mill. This process generates heat, which helps to bind the particles together, forming solid pellets as they cool and harden.
How can I ensure the quality of my wood pellets?
To ensure high-quality wood pellets, maintain consistent raw material quality, monitor moisture content, and control the pelletizing temperature. Additionally, conducting regular testing for durability and ash content can help maintain standards.
Can I use other materials besides wood to make pellets?
Yes, other biomass materials such as agricultural residues, grass, and even some types of paper can be used to make pellets. However, the properties of the final product may vary based on the type of material used.
the process of making wood pellets involves several critical steps that ensure the final product is of high quality and suitable for various applications, such as heating and cooking. The initial phase includes selecting the appropriate raw materials, primarily wood residues like sawdust and wood shavings, which should be free of contaminants. Following this, the materials undergo drying to achieve the optimal moisture content, typically around 10-15%, which is essential for effective pelletization.
Once the raw materials are adequately prepared, they are subjected to grinding to achieve a uniform particle size. This is followed by the pelletizing process itself, where the ground material is compressed under high pressure through a pellet mill. The heat generated during this process helps to bind the particles together, resulting in dense, cylindrical pellets. After pelletizing, the pellets must be cooled and stored properly to maintain their quality and prevent degradation.
Key takeaways from the discussion on making wood pellets include the importance of material selection, moisture control, and the pelletizing process. Understanding these factors can significantly influence the efficiency and quality of the wood pellets produced. Moreover, investing in the right equipment and maintaining proper operational conditions can lead to a successful and sustainable wood pellet production process.
Author Profile
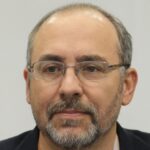
-
Darryl Norman is a seasoned entrepreneur and industry expert with a deep understanding of wood truss manufacturing and construction materials. As the President of Timberlake TrussWorks, LLC, Darryl played a pivotal role in shaping the company’s reputation for quality and precision. His leadership ensured that each truss met rigorous structural standards, providing builders with dependable components essential to their projects.
Beginning in 2025, Darryl Norman has shifted his focus to education and knowledge-sharing through an informative blog dedicated to wood truss manufacturing. Drawing from his extensive experience in the field, he provides in-depth insights into truss design, material selection, and construction techniques. This blog serves as a valuable resource for builders, contractors, and homeowners seeking practical guidance on truss systems and structural integrity.
Latest entries
- March 18, 2025General Wood TopicsWhat Color Is Ebony Wood? Unveiling the Rich Hues of This Luxurious Timber
- March 18, 2025Construction & FrameworkHow Can You Effectively Mount a Headboard to Your Wall?
- March 18, 2025General Wood TopicsCan Bees Really Eat Wood? Unraveling the Myths and Facts
- March 18, 2025General Wood TopicsDo Rabbits Really Chew on Wood? Exploring Their Eating Habits!