How Can You Create Your Own Wood Pellet Fuel at Home?
In an era where sustainability and renewable energy sources are at the forefront of environmental discussions, wood pellet fuel emerges as a compelling solution for both heating and energy generation. This eco-friendly alternative not only reduces waste but also offers a cost-effective way to harness the power of biomass. If you’ve ever wondered how to make wood pellet fuel, you’re in for an enlightening journey. From understanding the raw materials to the intricate processes involved, this guide will equip you with the knowledge to create your own wood pellets, contributing to a greener future while enjoying the warmth and efficiency they provide.
Creating wood pellet fuel is a fascinating blend of science and craftsmanship. At its core, the process involves converting organic materials—primarily wood—into dense, compact pellets that can be easily stored and burned. This transformation not only maximizes the energy content of the wood but also minimizes the volume, making it an efficient choice for both residential and commercial use. As we delve into the specifics, you’ll discover the various types of wood suitable for pellet production, the machinery required, and the steps to ensure high-quality pellets that burn cleanly and effectively.
Moreover, making wood pellet fuel can be a rewarding DIY project for those looking to take control of their energy sources. Whether you’re a seasoned woodworker or
Choosing the Right Wood
Selecting the appropriate type of wood is crucial in the production of high-quality wood pellet fuel. The best choices are hardwoods, which generally offer higher energy content and produce less ash compared to softwoods. However, a blend of both can also be effective, depending on the availability and desired characteristics of the final product.
Factors to consider when choosing wood include:
- Moisture Content: Ideal wood for pellet production should have a moisture content between 10% and 15%. Higher moisture content can lead to inefficient burning and increased emissions.
- Type of Wood: Common hardwoods include oak, maple, and hickory, while softwoods like pine and fir can also be used. Each type imparts different burning characteristics.
- Contaminants: Avoid wood that contains chemicals, such as treated lumber or wood from unknown sources, as these can release harmful emissions when burned.
Preparing the Wood
Once the wood is selected, it must be processed to ensure optimal pellet production. This involves several key steps:
- Debarking: Removing the bark from logs improves pellet quality, as bark can produce higher ash content and lower energy efficiency.
- Chipping: The wood must be chipped into smaller pieces to facilitate drying and grinding. Chips should be uniform in size for consistent processing.
- Drying: Drying the wood chips is essential to achieve the correct moisture content. This can be done using a rotary drum dryer or air drying, depending on the resources available.
Grinding the Wood
After drying, the wood chips are ground into a fine sawdust. This is a critical step, as the particle size affects the density and quality of the pellets. An ideal particle size ranges from 1 to 5 millimeters.
Key equipment for this process includes:
- Hammer mills
- Roller mills
Pelletizing Process
The ground wood is then fed into a pellet mill, where it is compressed under high pressure and temperature, causing the lignin in the wood to melt and bind the particles together. The pelletizing process involves:
- Feeding the Sawdust: The sawdust is fed into the mill through a hopper.
- Compression and Extrusion: The material is forced through a die, shaping it into pellets.
- Cooling: After extrusion, the pellets are hot and must be cooled to improve hardness and storage stability.
Step | Description | Equipment Used |
---|---|---|
Debarking | Removing the bark from logs | Debarker |
Chipping | Cutting wood into smaller pieces | Wood chipper |
Drying | Reducing moisture content | Rotary drum dryer |
Grinding | Producing fine sawdust | Hammer mill |
Pelletizing | Forming pellets under pressure | Pellet mill |
Cooling and Packaging
Once the pellets are formed, they need to be cooled to enhance their structural integrity. Cooling can be achieved using a cooling conveyor, which allows air to circulate around the pellets. After cooling, the pellets are ready for packaging.
The final steps include:
- Packaging: Pellets can be packaged in bags or bulk containers for distribution.
- Storage: Proper storage conditions are essential to prevent moisture absorption and maintain pellet quality.
By following these processes meticulously, producers can create high-quality wood pellet fuel that meets industry standards and consumer expectations.
Materials Needed for Wood Pellet Fuel Production
To produce wood pellet fuel, a selection of quality materials is essential. The primary component is biomass, which can vary in form and type. Key materials include:
- Wood Residues: Sawdust, wood shavings, and wood chips are ideal.
- Agricultural Residues: Corn stalks, wheat straw, and other plant materials can be utilized.
- Bark: The outer layer of trees can also be processed into pellets.
- Additives: Optional substances such as binders or lubricants may enhance pellet durability.
Processing the Raw Materials
The processing phase is critical in preparing the biomass for pelletization. This stage includes several steps:
- Drying: Biomass moisture content should be reduced to around 10-15%. This is often achieved using:
- Rotary dryers
- Conveyor dryers
- Grinding: The dried material needs to be ground into a fine powder. Common equipment includes:
- Hammer mills
- Disc mills
- Mixing: If using multiple materials, they should be thoroughly mixed to ensure uniformity. This step is crucial for consistent pellet quality.
Pelletizing Process
The pelletizing stage involves compressing the processed biomass into dense pellets. The process typically occurs in several phases:
- Conditioning: Before pelletizing, the biomass is conditioned with steam or water to enhance moisture content and temperature, making it easier to form pellets.
- Pellet Mill Operation: The conditioned material is fed into a pellet mill, where it is subjected to high pressure and temperature. Key components of a pellet mill include:
- Die: The circular component that shapes the pellets.
- Roller: Applies pressure against the die to form pellets.
- Cooling: After pelletizing, the hot pellets must be cooled to harden and reduce moisture content. Cooling can be done using:
- Air cooling systems
- Pellet coolers
Quality Control Measures
Ensuring the quality of wood pellets is essential for performance and customer satisfaction. Key quality control measures include:
- Moisture Content Testing: Utilize moisture meters to verify that pellets maintain an optimal moisture level.
- Durability Testing: Conduct tests to determine the mechanical durability of the pellets, ensuring they withstand handling and transportation.
- Ash Content Analysis: Test for ash content to meet standards for combustion efficiency.
Packaging and Storage
Proper packaging and storage of wood pellets are vital for maintaining quality. Consider the following:
- Packaging Options:
- Bagging: Use moisture-resistant bags for retail distribution.
- Bulk Storage: Store pellets in silos or bulk containers for wholesale distribution.
- Storage Conditions:
- Keep pellets in a dry environment to prevent moisture absorption.
- Ensure ventilation to avoid mold growth.
By adhering to these methods and practices, the production of wood pellet fuel can yield a high-quality, efficient product suitable for various applications.
Expert Insights on Producing Wood Pellet Fuel
Dr. Emily Carter (Renewable Energy Specialist, GreenTech Innovations). “Producing wood pellet fuel requires a meticulous approach to sourcing raw materials. It is essential to use clean, dry wood residues to ensure high-quality pellets that burn efficiently and produce minimal emissions.”
Mark Thompson (Sustainability Consultant, EcoFuel Solutions). “The process of making wood pellets involves grinding the wood into fine sawdust, followed by drying and compressing it under high pressure. This not only enhances the energy density but also helps in achieving a uniform pellet size, which is crucial for consistent combustion.”
Linda Martinez (Bioenergy Analyst, Wood Energy Association). “Quality control is paramount in wood pellet production. Regular testing for moisture content and ash levels ensures that the final product meets industry standards, providing users with a reliable and efficient fuel source for heating and energy generation.”
Frequently Asked Questions (FAQs)
What materials are needed to make wood pellet fuel?
To make wood pellet fuel, you need raw materials such as sawdust, wood shavings, or wood chips. Additionally, a pellet mill, a hammer mill for grinding, and a drying system may be required to achieve the desired moisture content.
What is the process of making wood pellets?
The process involves several steps: drying the raw material to reduce moisture, grinding it into a fine powder, conditioning the material with steam, and then compressing it in a pellet mill to form pellets. Finally, the pellets are cooled and packaged for storage.
What is the ideal moisture content for wood pellets?
The ideal moisture content for wood pellets is typically between 8% and 10%. This range ensures optimal combustion efficiency and minimizes the risk of mold growth during storage.
Can I use treated wood to make wood pellets?
It is not advisable to use treated wood for making wood pellets. Treated wood may contain harmful chemicals that can be released during combustion, posing health risks and potentially damaging heating appliances.
How do I store homemade wood pellets?
Homemade wood pellets should be stored in a cool, dry place, ideally in airtight containers or bags to prevent moisture absorption. Proper storage helps maintain their quality and extends their shelf life.
What are the benefits of using wood pellets as fuel?
Wood pellets are a renewable energy source that burns cleaner than fossil fuels, producing fewer emissions. They are also more efficient, with a higher energy density, making them a cost-effective option for heating and power generation.
the process of making wood pellet fuel involves several key steps that ensure the production of high-quality pellets suitable for energy generation. The initial phase includes sourcing appropriate raw materials, such as sawdust or wood shavings, which should be free from contaminants and have a low moisture content. Following this, the materials undergo drying and grinding to achieve the desired consistency, which is crucial for efficient pelletizing.
Once the raw materials are prepared, they are subjected to the pelletizing process, where they are compressed under high pressure to form pellets. This stage is critical as it not only shapes the pellets but also helps to bind them together through the natural lignin present in the wood. After pelletizing, the pellets must be cooled and stored properly to maintain their integrity and prevent moisture absorption.
Key takeaways from the discussion on wood pellet fuel production include the importance of selecting high-quality raw materials, the necessity of proper drying and grinding techniques, and the significance of maintaining optimal conditions during the pelletizing and storage processes. By adhering to these guidelines, individuals and businesses can produce efficient and environmentally friendly wood pellets that serve as a sustainable energy source.
Author Profile
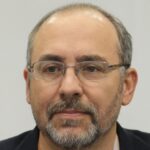
-
Mahlon Boehs is a seasoned entrepreneur and industry expert with a deep understanding of wood truss manufacturing and construction materials. As the President of Timberlake TrussWorks, LLC, Mahlon played a pivotal role in shaping the company’s reputation for quality and precision. His leadership ensured that each truss met rigorous structural standards, providing builders with dependable components essential to their projects.
Beginning in 2025, Mahlon Boehs has shifted his focus to education and knowledge-sharing through an informative blog dedicated to wood truss manufacturing. Drawing from his extensive experience in the field, he provides in-depth insights into truss design, material selection, and construction techniques. This blog serves as a valuable resource for builders, contractors, and homeowners seeking practical guidance on truss systems and structural integrity.
Latest entries
- March 18, 2025General Wood TopicsWhat Color Is Ebony Wood? Unveiling the Rich Hues of This Luxurious Timber
- March 18, 2025Construction & FrameworkHow Can You Effectively Mount a Headboard to Your Wall?
- March 18, 2025General Wood TopicsCan Bees Really Eat Wood? Unraveling the Myths and Facts
- March 18, 2025General Wood TopicsDo Rabbits Really Chew on Wood? Exploring Their Eating Habits!