How Can You Successfully Make Your Own Wood Pellets at Home?
In recent years, the demand for renewable energy sources has surged, leading many to explore sustainable alternatives for heating and power generation. Among these, wood pellets have emerged as a popular choice, offering an efficient and eco-friendly fuel option. But have you ever wondered how these small, cylindrical wonders are made? Crafting wood pellets is not just a simple process; it involves a fascinating blend of science, technology, and a commitment to sustainability. In this article, we will delve into the intricate journey of transforming raw wood into high-quality pellets, shedding light on the techniques and equipment that make it possible. Whether you’re a DIY enthusiast, a budding entrepreneur, or simply curious about the process, you’re in for an enlightening exploration.
Overview of Wood Pellet Production
The production of wood pellets begins with the careful selection of raw materials, typically sourced from sawmill residues, wood shavings, and other biomass. These materials are then processed to achieve the right size and moisture content, which are critical factors in ensuring optimal pellet quality. Once prepared, the biomass undergoes a series of mechanical and thermal treatments that compress it into dense, uniform pellets. This transformation not only enhances the energy density of the wood but also makes it easier to transport and store.
After the pellets are formed,
Choosing the Right Materials
Selecting the appropriate raw materials is crucial for producing high-quality wood pellets. The primary ingredient is biomass, commonly sourced from wood byproducts. Here are some materials to consider:
- Wood Sawdust: A fine particle size that compacts well.
- Wood Shavings: Larger than sawdust but still effective.
- Wood Chips: Require additional processing to reach the desired size.
- Agricultural Residues: Such as straw or corn stover, can also be used but may require blending with wood materials for optimal results.
When choosing materials, aim for a moisture content of 10-15% to ensure effective pelletization. Too much moisture can lead to poor pellet quality, while too little can cause excessive dust.
Grinding the Raw Materials
After selecting your materials, the next step involves grinding them into a uniform size. This is essential for consistent pellet formation and ensures efficient compaction. The grinding process typically includes:
- Using a Hammer Mill: This device reduces the size of the raw materials to a fine powder, facilitating the pelletizing process.
- Screen Size Selection: Choose the appropriate screen size based on the desired final product. A 3-5 mm screen is commonly used for wood pellets.
It’s important to monitor the particle size; ideally, the majority should pass through a 6 mm screen for optimal results.
Drying the Material
Proper drying is necessary to achieve the ideal moisture content for pellet production. Excess moisture can hinder the binding process during pelletization. This can be done using:
- Kilns: Efficient for large batches, maintaining consistent temperatures.
- Air Drying: Suitable for smaller quantities but may take longer.
Consider the following drying methods and their pros and cons:
Method | Advantages | Disadvantages |
---|---|---|
Kiln Drying | Fast and efficient; consistent results | Higher energy costs |
Air Drying | Cost-effective; no energy required | Time-consuming; weather dependent |
Pelletizing Process
Once the materials are dried, they are ready for the pelletizing process. This involves compressing the biomass into pellet form using a pellet mill. Key steps include:
- Feeding the Material: Introduce the dried biomass into the pellet mill’s hopper.
- Compression: The material is forced through a die, where it is compressed and shaped into pellets.
- Cooling: Newly formed pellets are hot and must be cooled to maintain their shape and prevent degradation.
Utilizing a counterflow cooler can help to efficiently cool the pellets while removing excess moisture.
Storing the Pellets
Finally, proper storage is critical to maintaining the quality of the wood pellets. Consider the following storage tips:
- Dry Environment: Keep pellets in a moisture-free area to prevent mold and degradation.
- Temperature Control: Store in a temperature-controlled environment to avoid condensation.
- Sealed Containers: Use airtight containers or bags to minimize exposure to air and moisture.
Following these guidelines will help ensure that your wood pellets remain high-quality and ready for use.
Materials Required for Making Wood Pellets
To produce wood pellets efficiently, it is essential to gather the right materials and equipment. The primary materials include:
- Raw Wood Materials: This can include sawdust, wood chips, or shavings. The wood should be clean and free from contaminants.
- Binder: Although wood pellets typically do not require a binder, some formulations may use natural adhesives to improve pellet strength.
- Additives: Optional additives can enhance the properties of pellets, such as burning efficiency or storage stability.
Equipment Needed
Creating wood pellets necessitates specific equipment to process raw materials and shape them into pellets. Key equipment includes:
- Wood Grinder: Reduces wood into fine sawdust, ensuring uniformity.
- Dryer: Lowers moisture content to the optimal level (ideally between 10-15%).
- Pellet Mill: Compresses the sawdust into pellets under high pressure and temperature.
- Cooling System: Reduces the temperature of freshly made pellets to prevent spoilage.
- Packaging Equipment: For storing and distributing the finished pellets.
Step-by-Step Process of Making Wood Pellets
The process of making wood pellets can be broken down into several critical steps:
- Material Preparation
- Collect raw wood materials.
- Use a wood grinder to produce fine sawdust.
- Drying
- Transfer the sawdust to a dryer.
- Monitor moisture levels until they reach approximately 10-15%.
- Pelleting
- Feed the dried sawdust into the pellet mill.
- Adjust the mill settings to ensure optimal pressure and temperature for pellet formation.
- Cooling
- Move the hot pellets to a cooling system.
- Allow them to cool down to room temperature.
- Packaging
- Once cooled, package the pellets in moisture-resistant bags or containers.
- Label packages with necessary information, including production date and moisture content.
Quality Control Measures
To ensure the quality of wood pellets, implement the following quality control measures:
- Moisture Content Testing: Regularly check the moisture content to ensure it is within the desired range.
- Pellet Durability Testing: Assess the mechanical durability of pellets to minimize fines during handling.
- Calorific Value Testing: Measure the energy content of the pellets to ensure they meet the desired specifications.
Storage Recommendations
Proper storage of wood pellets is crucial for maintaining their quality. Consider the following:
- Location: Store pellets in a dry, cool environment away from direct sunlight.
- Containers: Use airtight containers or moisture-resistant bags to prevent water absorption.
- Inventory Management: Monitor stock levels to ensure the oldest pellets are used first (FIFO method).
Environmental Considerations
Making wood pellets can have environmental implications. To mitigate negative effects:
- Source Responsibly: Ensure wood materials are sourced sustainably from managed forests.
- Minimize Waste: Optimize production processes to reduce sawdust waste.
- Carbon Footprint: Consider using renewable energy sources for machinery operation to lower the carbon footprint of production activities.
Expert Insights on How to Make Wood Pellets
Dr. Emily Carter (Renewable Energy Specialist, GreenTech Innovations). “The process of making wood pellets begins with selecting the right type of biomass. Hardwoods are preferred due to their higher energy content, but softwoods can also be used. Proper drying and milling of the raw material are crucial steps to ensure optimal pellet quality.”
Mark Thompson (Wood Processing Engineer, TimberTech Solutions). “When producing wood pellets, it is essential to maintain a consistent particle size during the milling process. This uniformity aids in the compression stage, where the wood fibers are transformed into pellets under high pressure and temperature.”
Linda Zhang (Sustainability Consultant, EcoFuel Advisors). “Quality control is vital throughout the wood pellet manufacturing process. Regular testing for moisture content, density, and durability ensures that the final product meets industry standards and performs efficiently in heating applications.”
Frequently Asked Questions (FAQs)
What materials are suitable for making wood pellets?
Wood pellets can be made from various types of biomass, primarily hardwood and softwood sawdust, wood shavings, and wood chips. Other organic materials like agricultural residues and certain types of paper can also be used.
What equipment is needed to make wood pellets?
The essential equipment includes a wood pellet mill, a hammer mill for size reduction, a dryer to reduce moisture content, and a cooler to stabilize the pellets after production. Additional equipment may include conveyors and storage systems.
What is the ideal moisture content for wood pellets?
The ideal moisture content for wood pellets is between 10% and 15%. This range ensures optimal pellet formation and combustion efficiency while minimizing the risk of spoilage.
How do I ensure the quality of the wood pellets?
Quality can be ensured by using clean, dry raw materials, maintaining proper moisture levels, and controlling the pelletizing process parameters, such as temperature and pressure. Conducting regular tests for density, durability, and ash content is also recommended.
Can wood pellets be made at home?
Yes, wood pellets can be made at home using smaller-scale equipment, such as a pellet mill designed for personal use. However, achieving consistent quality may require careful attention to material preparation and processing conditions.
What are the benefits of using wood pellets for fuel?
Wood pellets are a renewable energy source, producing lower emissions compared to fossil fuels. They provide high energy density, are easy to store and transport, and can be used in various heating systems, making them an efficient and environmentally friendly fuel option.
the process of making wood pellets involves several critical steps that ensure the final product is of high quality and suitable for use as a renewable energy source. Initially, the selection of appropriate raw materials, such as sawdust or wood shavings, is essential. These materials should be dry and free from contaminants to achieve optimal pellet formation. The subsequent steps include grinding the raw materials to a fine consistency, which facilitates the pelleting process.
After grinding, the wood particles must be conditioned with heat and moisture, which helps to soften the lignin in the wood. This lignin acts as a natural binder during the pelleting process. The conditioned material is then fed into a pellet mill, where it is compressed through a die to form pellets. Cooling and packaging follow, ensuring that the pellets maintain their integrity and are ready for storage or distribution.
Key takeaways from the discussion on making wood pellets include the importance of material selection, the need for proper conditioning, and the role of the pellet mill in shaping the final product. Understanding these elements can significantly enhance the efficiency of the pelleting process and the quality of the wood pellets produced. By adhering to these best practices, individuals and businesses can effectively contribute to sustainable energy solutions through the
Author Profile
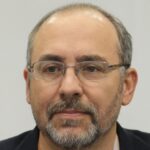
-
Darryl Norman is a seasoned entrepreneur and industry expert with a deep understanding of wood truss manufacturing and construction materials. As the President of Timberlake TrussWorks, LLC, Darryl played a pivotal role in shaping the company’s reputation for quality and precision. His leadership ensured that each truss met rigorous structural standards, providing builders with dependable components essential to their projects.
Beginning in 2025, Darryl Norman has shifted his focus to education and knowledge-sharing through an informative blog dedicated to wood truss manufacturing. Drawing from his extensive experience in the field, he provides in-depth insights into truss design, material selection, and construction techniques. This blog serves as a valuable resource for builders, contractors, and homeowners seeking practical guidance on truss systems and structural integrity.
Latest entries
- March 18, 2025General Wood TopicsWhat Color Is Ebony Wood? Unveiling the Rich Hues of This Luxurious Timber
- March 18, 2025Construction & FrameworkHow Can You Effectively Mount a Headboard to Your Wall?
- March 18, 2025General Wood TopicsCan Bees Really Eat Wood? Unraveling the Myths and Facts
- March 18, 2025General Wood TopicsDo Rabbits Really Chew on Wood? Exploring Their Eating Habits!