How Can You Make Your Own Wood Stove Pellets at Home?
In the quest for sustainable heating solutions, wood stove pellets have emerged as a popular choice among eco-conscious homeowners. These compact, energy-dense pellets not only provide an efficient way to heat your space but also offer a renewable alternative to traditional fossil fuels. Have you ever wondered how these little powerhouses are made? Understanding the process behind crafting wood stove pellets can empower you to embrace a more self-sufficient lifestyle while reducing your carbon footprint. In this article, we’ll explore the fascinating journey from raw materials to finished pellets, revealing the techniques and tools needed to create your own.
Creating wood stove pellets involves a meticulous process that transforms raw wood into a highly efficient fuel source. The journey begins with selecting the right type of wood, which plays a crucial role in the quality of the final product. Once the wood is sourced, it undergoes several steps, including drying, grinding, and compressing, to achieve the ideal consistency and density. Each stage is essential in ensuring that the pellets burn cleanly and efficiently, providing maximum heat output with minimal emissions.
In addition to the technical aspects, making your own wood stove pellets can also be a rewarding endeavor. Not only does it allow you to take control of your heating resources, but it also fosters a deeper connection to
Gathering Materials
To create wood stove pellets, you will need specific raw materials that can be processed into pellets. The primary ingredient is biomass, which can be derived from various sources. Common materials include:
- Wood Sawdust: The most widely used material, providing the necessary density and combustion efficiency.
- Wood Shavings: Often a byproduct of woodworking, these can also be used if they are dry and free from contaminants.
- Agricultural Residues: Materials such as corn stalks, wheat straw, and rice husks can be utilized, though they may require additional processing.
- Bark and Wood Chips: These can be included but should be reduced in size to ensure proper pellet formation.
Preparing the Material
Once you have gathered your raw materials, the next step involves preparing them for pelletization. The preparation process typically includes the following:
- Drying: The moisture content of the biomass should ideally be between 10% and 15%. Excess moisture can lead to poor pellet quality and combustion issues. Use a moisture meter to assess this.
- Grinding: The biomass must be ground to a fine consistency, generally less than 1/4 inch in size. This ensures uniformity during the pellet-making process. A hammer mill or wood chipper can be effective for this purpose.
- Mixing: If using multiple types of biomass, ensure they are mixed thoroughly to achieve a consistent blend.
Pelletizing Process
The pelletizing process involves converting the prepared biomass into pellets. This can be achieved through the following methods:
- Using a Pellet Mill: This machine compresses the biomass through a die to form pellets. It can be set up for home use or purchased from suppliers.
- Extrusion: This method involves forcing the biomass through a die using a screw mechanism, which generates heat and pressure, aiding in the formation of pellets.
Key parameters to monitor during this process include:
- Temperature: Maintaining appropriate temperatures (typically between 120°F to 180°F) is crucial for the lignin in the wood to act as a natural binder.
- Pressure: The pressure applied by the pellet mill should be consistent to ensure uniform pellet size.
Cooling and Storing Pellets
After pelletizing, it is essential to cool the pellets before storage to prevent moisture buildup and deterioration. The cooling process typically includes:
- Cooling System: Implement a cooling system that allows air to circulate around the pellets, lowering their temperature.
- Storage Conditions: Store the pellets in a dry, well-ventilated area to maintain their quality. Use airtight containers or bags to protect them from moisture.
Material Type | Moisture Content (%) | Grinding Size (inches) |
---|---|---|
Wood Sawdust | 10-15 | ≤ 0.25 |
Wood Shavings | 10-15 | ≤ 0.25 |
Agricultural Residues | 10-15 | ≤ 0.25 |
By following these steps, you can successfully create high-quality wood stove pellets, ready for efficient burning in your wood stove.
Understanding the Raw Materials
To create wood stove pellets, it is essential to start with the right raw materials. The primary component is biomass, which can come from various wood sources.
- Types of Wood:
- Hardwoods (e.g., oak, maple)
- Softwoods (e.g., pine, spruce)
- Waste Products: Sawdust, wood shavings, and wood chips are commonly used. They should be free from contaminants such as plastics or metals.
Preparing the Raw Materials
Proper preparation of raw materials is crucial for effective pellet production. The following steps should be taken:
- Drying:
- Aim for a moisture content of 10-15%.
- Use a kiln or natural air-drying methods.
- Grinding:
- Reduce the size of the biomass to increase surface area.
- A hammer mill or wood chipper can be used for this purpose.
Pelletizing Process
The pelletizing process transforms the prepared raw materials into pellets. This involves several key stages:
- Conditioning:
- Mix the ground biomass with steam or water to soften the material.
- This step enhances the binding properties.
- Pelletizing:
- Utilize a pellet mill to compress the conditioned biomass.
- The high pressure and heat allow lignin in the wood to act as a natural binder.
- Cooling:
- Once pellets are formed, they need to be cooled to harden.
- Use a pellet cooler for this purpose, which also reduces moisture content.
Quality Control Measures
To ensure the durability and efficiency of wood stove pellets, several quality control measures should be implemented:
- Testing Moisture Content:
- Regularly check that moisture levels remain between 6-8%.
- Diameter and Length Consistency:
- Pellets should typically be 6-8 mm in diameter and 10-30 mm in length.
- Durability Testing:
- Use a tumble test to evaluate how well pellets hold together during handling.
Storage and Handling
Proper storage and handling are essential to maintain the quality of wood stove pellets:
- Storage Conditions:
- Keep pellets in a dry, cool place to prevent moisture absorption.
- Use breathable bags or bins to allow for air circulation.
- Handling:
- Use gloves and ensure safe lifting practices to avoid injury.
- Consider using a pellet dispenser for easy access to the stored pellets.
Environmental Considerations
Producing wood stove pellets can have environmental impacts, which should be minimized:
- Sustainable Sourcing:
- Ensure that wood is sourced from sustainably managed forests.
- Emissions Control:
- Implement measures to reduce dust and emissions during production.
- Waste Management:
- Recycle any waste products generated during the pelletizing process.
Regulatory Compliance
Adhering to local regulations is necessary for the production of wood stove pellets:
- Standards and Certifications:
- Familiarize yourself with industry standards (e.g., ENplus, PFI) that govern pellet quality.
- Local Laws:
- Research and comply with local laws related to biomass production and environmental protection.
Expert Insights on Making Wood Stove Pellets
Dr. Emily Carter (Renewable Energy Specialist, GreenTech Innovations). “The process of making wood stove pellets begins with selecting the right type of biomass, ideally hardwoods, which provide a higher energy content. Properly drying the wood to a moisture content of around 10-15% is crucial for efficient pellet production.”
James Thompson (Sustainable Forestry Consultant, EcoWood Solutions). “When creating wood stove pellets, it is essential to utilize a pellet mill that can handle the specific feedstock. The compression process not only shapes the pellets but also increases their density, enhancing combustion efficiency.”
Linda Garcia (Biomass Technology Researcher, Renewable Resources Institute). “Quality control is paramount in pellet production. Regular testing for ash content and pellet durability ensures that the final product meets industry standards and provides optimal performance in wood stoves.”
Frequently Asked Questions (FAQs)
What materials are needed to make wood stove pellets?
To make wood stove pellets, you need dry wood sawdust, a pellet mill, and possibly a binder such as starch, depending on the type of wood and desired pellet quality.
How do I prepare the wood sawdust for pellet production?
The wood sawdust must be thoroughly dried to a moisture content of around 10-15%. This can be achieved using a kiln or air drying, ensuring that the sawdust is fine and free from contaminants.
What is the process of making wood stove pellets?
The process involves drying the wood sawdust, compressing it using a pellet mill, and then cooling the pellets. The compression causes lignin in the wood to melt and bind the particles together, forming solid pellets.
How long does it take to make wood stove pellets?
The entire process of making wood stove pellets can take several hours, depending on the scale of production, equipment efficiency, and drying time of the sawdust.
Can I use any type of wood to make pellets?
While most hardwoods and softwoods can be used, it is advisable to avoid treated or painted wood, as these can release harmful chemicals when burned. Clean, untreated wood is preferred for optimal pellet quality.
What is the ideal size for wood stove pellets?
The ideal size for wood stove pellets is typically around 6-8 mm in diameter and 10-30 mm in length. This size ensures efficient burning and easy handling during storage and feeding into the stove.
making wood stove pellets involves a systematic process that begins with selecting the right raw materials, typically wood sawdust or shavings. The quality of the pellets largely depends on the type of wood used, as different species can affect the burn efficiency and heat output. It is crucial to ensure that the wood is dry and free from contaminants to achieve optimal results. The preparation of the raw materials includes drying, grinding, and possibly mixing with additives to enhance the pellet’s properties.
The next step is the pelleting process, which involves compressing the prepared wood material through a pellet mill. This process requires careful control of temperature and pressure to ensure that the lignin in the wood binds the particles together effectively. After pelleting, the pellets must be cooled and stored properly to maintain their integrity and prevent moisture absorption. Proper storage is essential to prolong the shelf life of the pellets and ensure they remain ready for use in wood stoves.
Key takeaways from the discussion include the importance of material selection and preparation, as well as the technical aspects of the pelleting process. Understanding the characteristics of different wood types and the impact of moisture content can significantly influence the quality of the final product. Additionally, attention to storage conditions is vital for maintaining
Author Profile
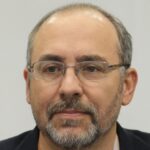
-
Mahlon Boehs is a seasoned entrepreneur and industry expert with a deep understanding of wood truss manufacturing and construction materials. As the President of Timberlake TrussWorks, LLC, Mahlon played a pivotal role in shaping the company’s reputation for quality and precision. His leadership ensured that each truss met rigorous structural standards, providing builders with dependable components essential to their projects.
Beginning in 2025, Mahlon Boehs has shifted his focus to education and knowledge-sharing through an informative blog dedicated to wood truss manufacturing. Drawing from his extensive experience in the field, he provides in-depth insights into truss design, material selection, and construction techniques. This blog serves as a valuable resource for builders, contractors, and homeowners seeking practical guidance on truss systems and structural integrity.
Latest entries
- March 18, 2025General Wood TopicsWhat Color Is Ebony Wood? Unveiling the Rich Hues of This Luxurious Timber
- March 18, 2025Construction & FrameworkHow Can You Effectively Mount a Headboard to Your Wall?
- March 18, 2025General Wood TopicsCan Bees Really Eat Wood? Unraveling the Myths and Facts
- March 18, 2025General Wood TopicsDo Rabbits Really Chew on Wood? Exploring Their Eating Habits!