How Can You Create Your Own Wood Veneer at Home?
Wood veneer has long been cherished for its beauty and versatility, allowing artisans and DIY enthusiasts alike to create stunning surfaces that showcase the natural elegance of wood. Whether you’re looking to enhance furniture, craft intricate designs, or add a touch of sophistication to your home décor, understanding how to make wood veneer opens up a world of creative possibilities. In this article, we will explore the fascinating process of transforming solid wood into thin, flexible sheets that can be used in a multitude of applications. Get ready to dive into the art of veneer-making and discover how you can harness this technique to elevate your woodworking projects.
Creating wood veneer is a delicate and skilled process that involves slicing thin layers from a log or plank of wood. These layers, often just a fraction of an inch thick, retain the unique grain patterns and colors of the original wood, making them an ideal choice for a variety of applications. From enhancing the aesthetic appeal of furniture to crafting decorative elements, wood veneer offers a sustainable alternative to solid wood while minimizing waste.
The journey of making wood veneer begins with selecting the right type of wood, as different species provide distinct visual characteristics and durability. Once the wood is chosen, it undergoes a series of precise cuts and treatments to achieve the desired thickness and finish. The result
Choosing the Right Wood
Selecting the appropriate wood species is crucial for creating quality veneer. Different woods offer unique aesthetics, strengths, and workability. Common choices include:
- Oak: Known for its durability and distinct grain patterns.
- Maple: Offers a fine, uniform texture and is easy to work with.
- Cherry: Renowned for its rich color and smooth finish.
- Walnut: Valued for its dark tones and attractive grain.
When choosing wood, consider the final application of the veneer, as well as the wood’s availability and sustainability.
Preparing the Wood
Before slicing the wood, proper preparation is essential:
- Selecting a Log: Choose a log that is free of defects such as knots or significant warping.
- Moisture Content: Ensure the wood is adequately dried to a moisture content between 6% and 8% to reduce the risk of cracking during the slicing process.
- Trimming: Cut the log to a manageable length and remove any bark or rough edges.
Methods of Making Veneer
There are several methods to create wood veneer, each offering distinct characteristics:
Method | Description | Advantages |
---|---|---|
Rotary Cutting | The log is mounted on a lathe and turned against a blade, peeling off a continuous sheet. | Produces wide sheets quickly; ideal for plywood. |
Slicing | The log is sliced lengthwise or across using a knife, resulting in flat sheets. | Preserves grain patterns; ideal for high-quality veneer. |
Sawing | Using a saw to cut thin sheets from a log. | Efficient for thicker veneers; good for rustic looks. |
Cutting the Veneer
Once the wood is prepared and the method selected, cutting can begin. It is vital to use sharp tools to ensure clean cuts that enhance the appearance of the veneer.
- For rotary cutting, adjust the lathe speed and blade angle to achieve the desired thickness.
- In slicing, use a veneer saw or bandsaw for precision, maintaining a consistent thickness of approximately 1/32 inch to 1/16 inch.
Finishing the Veneer
After cutting, the veneer requires finishing to enhance its appearance and durability. Common finishing techniques include:
- Sanding: Smooth the surface using progressively finer grits.
- Staining: Apply stains to achieve the desired color while maintaining the natural grain.
- Sealing: Use a clear sealant to protect the veneer from moisture and wear.
When applying finishes, ensure the environment is dust-free to avoid imperfections in the final product.
Storing the Veneer
Proper storage is critical to maintaining the quality of the veneer. Follow these guidelines:
- Store sheets flat, ideally in a controlled environment with low humidity.
- Use a veneer rack or stack them between sheets of kraft paper to prevent warping and damage.
By adhering to these guidelines, you can produce and maintain high-quality wood veneer suitable for various applications.
Materials Needed for Making Wood Veneer
To create wood veneer, certain materials and tools are essential. Below is a list of items required for the process:
- Wood logs or boards: Choose high-quality wood species such as oak, walnut, cherry, or maple for appealing aesthetics.
- Sawmill or veneer slicer: A specialized saw or slicer is necessary for cutting thin sheets from the wood.
- Clamps: To secure the wood during the slicing process.
- Sandpaper: Different grits for smoothing the veneer edges.
- Finishing tools: Such as brushes, sprays, or rollers for applying wood finish or adhesive.
Preparing the Wood
Before slicing the veneer, it is crucial to prepare the wood properly. Follow these steps:
- Select the Wood: Choose straight-grained wood free from knots or defects.
- Condition the Wood: Soak the wood in water or steam for several hours to make it pliable, allowing for smoother cuts.
- Trim the Edges: Use a saw to trim the ends of the wood logs or boards to remove any roughness.
Cutting Techniques for Veneer
Different cutting techniques can be employed to produce wood veneer. The following methods are commonly used:
Technique | Description |
---|---|
Rotary Cutting | The log is mounted on a lathe and turned against a knife, producing continuous sheets. |
Slicing | A stationary log is sliced with a knife at a specific angle, yielding flat sheets. |
Sawing | The log is cut into thin sheets using a band saw, ideal for thicker veneer applications. |
Finishing the Veneer
Once the veneer has been cut, it requires finishing to enhance its appearance and durability. Steps include:
- Sanding: Use sandpaper to smooth the surface and edges of the veneer.
- Sealing: Apply a wood sealer to protect against moisture and prevent warping.
- Staining: If desired, apply wood stain to achieve the desired color.
- Finishing: Use a clear coat finish such as polyurethane to add a protective layer.
Application of Wood Veneer
Wood veneer can be applied in various ways, depending on the project. Common applications include:
- Furniture: Enhancing surfaces of tables, cabinets, and chairs.
- Wall Paneling: Creating decorative wall features in homes or offices.
- Musical Instruments: Used in the construction of pianos and guitars for aesthetic purposes.
Storage and Care for Wood Veneer
Proper storage and care are vital for maintaining the quality of wood veneer. Consider the following:
- Storage Conditions: Keep veneer in a cool, dry place away from direct sunlight to prevent warping and fading.
- Handling: Handle with care to avoid scratches or dents on the surface.
- Cleaning: Use a soft cloth for cleaning; avoid harsh chemicals that may damage the finish.
Expert Insights on Crafting Wood Veneer
Dr. Emily Carter (Woodworking Specialist, Timber Techniques Journal). “Creating wood veneer requires precision and an understanding of the wood’s grain. The process typically begins with selecting high-quality lumber, which is then sliced or peeled to achieve the desired thickness. Maintaining a consistent thickness is crucial for achieving a professional finish.”
Michael Thompson (Senior Craftsman, Artisan Woodworks). “In my experience, the best results come from using a veneer saw or a bandsaw for slicing. It’s essential to keep the blade sharp and to work slowly to avoid tearing the wood. Additionally, using a veneer press can help ensure that the sheets adhere properly when applied to substrates.”
Susan Lee (Furniture Designer, Eco-Friendly Designs). “When making wood veneer, consider the environmental impact of your materials. Opting for sustainably sourced wood not only enhances your project’s appeal but also contributes to responsible craftsmanship. Finishing techniques, such as applying natural oils or water-based finishes, can also enhance the veneer’s beauty while being eco-conscious.”
Frequently Asked Questions (FAQs)
What materials are needed to make wood veneer?
To make wood veneer, you will need a log of wood, a veneer saw or slicer, clamps, a flat surface, and a sanding block or machine for finishing. Additionally, you may require a moisture meter and a veneer press for optimal results.
What is the best method for slicing wood veneer?
The best methods for slicing wood veneer include rotary slicing, flat slicing, and quarter slicing. Each method produces different grain patterns and thicknesses, so the choice depends on the desired aesthetic and application.
How thick should wood veneer be?
Wood veneer typically ranges from 0.5 mm to 3 mm in thickness. The thickness chosen will depend on the intended use, with thinner veneers suitable for decorative applications and thicker veneers for structural purposes.
Can I make wood veneer at home?
Yes, you can make wood veneer at home with the right tools and techniques. However, it requires careful handling of the wood and precision in slicing to achieve quality results.
What types of wood are commonly used for veneer?
Common types of wood used for veneer include oak, maple, cherry, walnut, and mahogany. Each wood species offers unique grain patterns and colors, making them suitable for various applications in furniture and cabinetry.
How do I finish wood veneer after slicing?
After slicing wood veneer, it should be sanded to achieve a smooth surface. Following sanding, apply a suitable finish such as lacquer, varnish, or oil to protect the veneer and enhance its appearance.
making wood veneer involves a series of precise steps that require attention to detail and the right tools. The process begins with selecting the appropriate wood species, which can significantly influence the appearance and characteristics of the veneer. Once the wood is chosen, it is essential to prepare it properly through cutting and slicing techniques, ensuring that the veneer is thin enough to achieve the desired aesthetic while retaining strength and flexibility.
Furthermore, the methods of slicing, such as rotary cutting, flat slicing, and quarter slicing, each yield different grain patterns and textures, allowing for a variety of design options. After slicing, the veneer sheets must be dried and flattened to prevent warping, ensuring they are ready for application. The final steps include applying adhesives and pressing the veneer onto substrates, which can enhance the overall durability and finish of the project.
Key takeaways from the discussion on making wood veneer include the importance of wood selection, the various slicing techniques that affect the final appearance, and the need for proper drying and application methods. By mastering these elements, one can create high-quality wood veneers that elevate the aesthetic appeal of furniture and other woodworking projects.
Author Profile
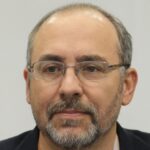
-
Darryl Norman is a seasoned entrepreneur and industry expert with a deep understanding of wood truss manufacturing and construction materials. As the President of Timberlake TrussWorks, LLC, Darryl played a pivotal role in shaping the company’s reputation for quality and precision. His leadership ensured that each truss met rigorous structural standards, providing builders with dependable components essential to their projects.
Beginning in 2025, Darryl Norman has shifted his focus to education and knowledge-sharing through an informative blog dedicated to wood truss manufacturing. Drawing from his extensive experience in the field, he provides in-depth insights into truss design, material selection, and construction techniques. This blog serves as a valuable resource for builders, contractors, and homeowners seeking practical guidance on truss systems and structural integrity.
Latest entries
- March 18, 2025General Wood TopicsWhat Color Is Ebony Wood? Unveiling the Rich Hues of This Luxurious Timber
- March 18, 2025Construction & FrameworkHow Can You Effectively Mount a Headboard to Your Wall?
- March 18, 2025General Wood TopicsCan Bees Really Eat Wood? Unraveling the Myths and Facts
- March 18, 2025General Wood TopicsDo Rabbits Really Chew on Wood? Exploring Their Eating Habits!