How Can You Create Strong and Durable Wooden I Beams?
When it comes to constructing sturdy structures, the choice of materials is paramount, and wooden I beams stand out as a popular option among builders and DIY enthusiasts alike. These versatile components combine strength and efficiency, making them ideal for a variety of applications, from residential homes to larger commercial projects. But how exactly do you make wooden I beams that not only meet structural requirements but also reflect your craftsmanship? In this article, we’ll delve into the process of creating these essential building blocks, guiding you through the techniques and considerations that will ensure your beams are both functional and aesthetically pleasing.
Overview
Creating wooden I beams involves a blend of traditional woodworking skills and modern engineering principles. At their core, I beams are designed to efficiently bear loads while minimizing material use, which is why understanding the geometry and mechanics behind their design is crucial. The process typically starts with selecting the right type of wood, as different species offer varying levels of strength, durability, and workability.
Once the materials are chosen, the construction process includes cutting, shaping, and assembling the beams to achieve the desired dimensions and structural integrity. This not only requires precision in measurements but also an understanding of the best joining methods to ensure stability and longevity. Whether you’re a seasoned carpenter or a novice eager to learn
Materials Required
To create wooden I beams, you will need a variety of materials and tools that ensure the structural integrity and durability of the beams. The following items are essential:
- High-quality lumber (preferably structural-grade)
- Plywood or oriented strand board (OSB) for webbing
- Wood glue or construction adhesive
- Screws or nails
- Wood clamps
- Measuring tape
- Circular saw or table saw
- Router (optional for finishing edges)
- Sandpaper or a sander
Design Specifications
Before commencing the construction, it is crucial to design the beams according to the intended load-bearing specifications. The standard dimensions for wooden I beams typically involve a depth-to-width ratio that maximizes strength while minimizing material usage.
Consider the following design parameters:
Dimension | Typical Range |
---|---|
Depth | 6 – 12 inches |
Width | 2 – 4 inches |
Length | Varies based on application |
Construction Steps
The following steps outline the process of constructing wooden I beams:
- Cutting the Lumber: Using a circular saw, cut the lumber to the desired length for the top and bottom flanges of the I beam. For the webbing, cut the plywood or OSB to the appropriate height and length.
- Assembling the Beam:
- Lay the two flange pieces parallel to each other on a flat surface.
- Position the webbing piece between the flanges, ensuring it is centered.
- Apply wood glue to the edges of the webbing and the inner sides of the flanges.
- Securing the Structure:
- Use clamps to hold the assembly in place while the adhesive cures.
- For added strength, drill pilot holes and secure the webbing to the flanges using screws or nails.
- Finishing Touches:
- Once the glue has fully cured, remove the clamps.
- Use a router to smooth any rough edges if desired.
- Sand the entire beam to achieve a clean finish.
Quality Control
After constructing the I beams, it is essential to inspect them for any defects or weaknesses. Consider the following quality control measures:
- Check for any visible cracks or splits in the wood.
- Ensure that all joints are tight and well-secured.
- Test the beam’s load-bearing capacity by applying weight gradually and observing any deflection.
By following these guidelines, you can successfully create sturdy wooden I beams suitable for various construction projects.
Materials Required for Wooden I Beams
To create wooden I beams, it is essential to gather the right materials to ensure structural integrity and longevity. The primary components include:
- Lumber: Select high-quality, straight-grain wood. Common choices are:
- Douglas Fir
- Southern Yellow Pine
- Laminated Veneer Lumber (LVL)
- Adhesives: Use strong wood adhesives to bond the beam components effectively. Options include:
- Polyurethane glue
- PVA (Polyvinyl Acetate) glue
- Fasteners: Utilize screws or nails that are corrosion-resistant. Recommended types are:
- Heavy-duty screws
- Galvanized nails
- Finishing Materials: To protect the beams from moisture and pests, consider:
- Wood sealant
- Paint or stain
Designing Wooden I Beams
The design of wooden I beams significantly affects their performance. Key design aspects include:
- Dimensions: Determine the height and width based on load requirements. Common configurations are:
- Height: 8″ to 12″
- Width: 3″ to 6″
- Flange Thickness: Typically, flanges should be at least 1″ thick for optimal strength.
- Web Depth: The web should be designed to minimize deflection while maintaining lightweight properties. A typical depth is around 1/2″ to 3/4″.
- Load Calculations: It is crucial to calculate the anticipated load to ensure the beam meets structural demands. Consider:
- Dead load (permanent/static load)
- Live load (temporary/moving load)
Step-by-Step Construction Process
The construction of wooden I beams involves several systematic steps:
- Cutting the Lumber:
- Measure and mark the required lengths for the flanges and web.
- Use a table saw or circular saw for precise cuts.
- Assembling the Beam:
- Lay the flanges parallel on a flat surface.
- Position the web vertically between the flanges, ensuring even spacing.
- Apply adhesive generously on the edges of the web and flanges.
- Securing the Components:
- Use clamps to hold the assembly in place while the adhesive sets.
- Reinforce joints with screws or nails for added stability. Space fasteners every 12 to 16 inches.
- Finishing Touches:
- Sand rough edges for a smooth finish.
- Apply protective sealant or paint, allowing adequate drying time.
Quality Control and Testing
After construction, ensure the wooden I beams meet quality standards through rigorous testing:
- Visual Inspection: Check for any defects such as warping, knots, or cracks.
- Load Testing: If possible, perform a load test to confirm the beam’s capacity.
- Moisture Content Check: Use a moisture meter to ensure wood is adequately dried, ideally below 15% moisture content.
Test Type | Purpose | Frequency |
---|---|---|
Visual Inspection | Identify defects | Before installation |
Load Testing | Confirm load capacity | Before use |
Moisture Check | Prevent rot and mold growth | During construction |
Applications of Wooden I Beams
Wooden I beams are versatile and used in various applications, including:
- Residential Construction: For floors, roofs, and walls.
- Commercial Buildings: As primary structural components.
- Bridges: In smaller, less trafficked designs.
- Furniture: For sturdy and aesthetic pieces.
Choosing the right application ensures the longevity and performance of wooden I beams in structural engineering.
Expert Insights on Crafting Wooden I Beams
James Whitaker (Structural Engineer, Timber Innovations). “When constructing wooden I beams, it is crucial to select high-quality lumber that is free from defects. The integrity of the beam relies heavily on the material used, as any knots or splits can compromise its strength.”
Linda Chen (Woodworking Specialist, Craftsmanship Journal). “Precision in cutting and assembling the flanges and web of the I beam is essential. Utilizing a table saw for clean cuts and ensuring that the glue joints are properly aligned will enhance the overall stability and performance of the beam.”
Mark Thompson (Construction Project Manager, Green Building Solutions). “Incorporating engineered wood products can significantly improve the load-bearing capacity of wooden I beams. It is advisable to consult with a structural engineer to determine the best design and materials for your specific application.”
Frequently Asked Questions (FAQs)
What materials are needed to make wooden I beams?
To construct wooden I beams, you will need high-quality lumber for the flanges (top and bottom) and engineered wood or plywood for the web. Additionally, wood glue, screws, clamps, and a saw are essential for assembly.
What are the dimensions typically used for wooden I beams?
The dimensions of wooden I beams can vary based on the specific application. Common sizes include heights ranging from 6 to 12 inches and widths of 1.5 to 3 inches for the flanges. The web thickness usually measures around 0.5 inches.
How do I ensure the structural integrity of wooden I beams?
To ensure structural integrity, use properly graded lumber, adhere to design specifications, and follow local building codes. Additionally, consider the load-bearing capacity and spacing of the beams during installation.
Can I make wooden I beams without specialized tools?
While it is possible to make wooden I beams with basic tools, using specialized equipment like a table saw and a router can enhance precision and efficiency. However, basic hand tools can suffice for smaller projects.
What are the advantages of using wooden I beams over traditional lumber?
Wooden I beams provide superior strength-to-weight ratios, reduced material usage, and greater design flexibility. They also minimize warping and shrinkage compared to traditional solid lumber, making them ideal for various construction applications.
Are there any safety precautions to consider when making wooden I beams?
Yes, always wear safety goggles and a dust mask when cutting wood. Ensure proper ventilation in your workspace and follow manufacturer guidelines for tools and adhesives to prevent accidents and health risks.
creating wooden I beams involves a systematic approach that emphasizes precision and quality materials. The process typically begins with selecting the right type of wood, which should be strong and durable, such as laminated veneer lumber or engineered wood products. Proper measurements and cutting techniques are crucial to ensure that the beams fit together seamlessly and provide the necessary structural support.
Furthermore, assembling the I beams requires attention to detail, particularly in the application of adhesives and fasteners. Utilizing the correct bonding agents and ensuring proper alignment during assembly can significantly enhance the strength and longevity of the beams. Additionally, it is essential to follow local building codes and regulations to ensure safety and compliance in construction projects.
Overall, the key takeaways from the discussion on making wooden I beams include the importance of material selection, precision in measurements and cuts, and adherence to safety standards. By following these guidelines, individuals can successfully create wooden I beams that meet their structural needs while also ensuring durability and reliability in their construction endeavors.
Author Profile
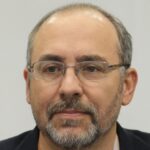
-
Darryl Norman is a seasoned entrepreneur and industry expert with a deep understanding of wood truss manufacturing and construction materials. As the President of Timberlake TrussWorks, LLC, Darryl played a pivotal role in shaping the company’s reputation for quality and precision. His leadership ensured that each truss met rigorous structural standards, providing builders with dependable components essential to their projects.
Beginning in 2025, Darryl Norman has shifted his focus to education and knowledge-sharing through an informative blog dedicated to wood truss manufacturing. Drawing from his extensive experience in the field, he provides in-depth insights into truss design, material selection, and construction techniques. This blog serves as a valuable resource for builders, contractors, and homeowners seeking practical guidance on truss systems and structural integrity.
Latest entries
- March 18, 2025General Wood TopicsWhat Color Is Ebony Wood? Unveiling the Rich Hues of This Luxurious Timber
- March 18, 2025Construction & FrameworkHow Can You Effectively Mount a Headboard to Your Wall?
- March 18, 2025General Wood TopicsCan Bees Really Eat Wood? Unraveling the Myths and Facts
- March 18, 2025General Wood TopicsDo Rabbits Really Chew on Wood? Exploring Their Eating Habits!