How Can You Create Stunning Wooden Masks at Home?
### Introduction
Creating wooden masks is not just an artistic endeavor; it is a journey into cultural expression and craftsmanship that has been celebrated across various societies for centuries. From the vibrant tribal masks of Africa to the intricate designs of the indigenous peoples of the Americas, wooden masks serve as powerful symbols of identity, tradition, and storytelling. Whether you’re an experienced woodworker or a curious beginner, the process of making a wooden mask offers a unique opportunity to connect with these rich histories while unleashing your creativity. In this article, we will explore the essential techniques, tools, and inspirations needed to craft your very own wooden masterpiece.
### Overview
The art of mask-making involves a blend of skill, imagination, and a deep understanding of the materials at hand. Wood, being a versatile and durable medium, allows artisans to create masks that are not only visually striking but also imbued with personal significance. As you embark on this creative journey, you will discover the various types of wood suitable for mask-making, the tools required for shaping and detailing, and the techniques that can transform a simple block of wood into a captivating work of art.
In addition to the technical aspects, the cultural context surrounding wooden masks is equally important. Each mask tells a story, reflecting the beliefs, rituals, and aesthetics of
Choosing the Right Wood
Selecting the appropriate type of wood is crucial for crafting wooden masks. Various wood types offer different characteristics in terms of workability, finish, and durability.
- Softwoods: Such as pine or cedar are easier to carve but may not hold details as well as hardwoods.
- Hardwoods: Like oak or maple provide excellent detail retention and durability, though they require more effort to carve.
Consider the following factors when choosing wood:
Wood Type | Characteristics | Best Use |
---|---|---|
Softwood (Pine) | Lightweight, easy to carve | Beginners, decorative masks |
Hardwood (Oak) | Dense, holds detail well | Professional masks, long-lasting pieces |
Exotic Woods (Mahogany) | Beautiful grain, expensive | High-end artistic masks |
Tools and Materials Needed
To create wooden masks, gather the following essential tools and materials:
- Basic Tools:
- Carving knives
- Chisels (various sizes)
- Sandpaper (grits from coarse to fine)
- Clamps
- Additional Materials:
- Wood glue (for assembly)
- Paint or wood stain (for finishing)
- Varnish or sealant (for protection)
Having a well-organized workspace with all tools accessible will streamline the mask-making process.
Designing Your Mask
Before beginning the carving process, it’s essential to design your mask. This step can significantly influence the final product.
- Sketching: Create several sketches on paper, exploring different shapes and features.
- Templates: Use thick paper or cardboard to create templates for the mask shape and features. This will help in maintaining symmetry and proportion during carving.
Key elements to consider in your design include:
- Facial features (eyes, nose, mouth)
- Style (tribal, decorative, abstract)
- Size (dimensions in relation to the wearer)
Carving the Mask
Once you have your wood and design ready, proceed to carve the mask. Follow these steps for an efficient carving process:
- Transfer the Design: Trace the template onto the wood using a pencil.
- Rough Cutting: Use a saw to cut out the basic shape of the mask.
- Detail Carving:
- Begin with larger chisels for the main features.
- Gradually switch to smaller tools for intricate details.
- Sanding: Smooth the surface using sandpaper, starting with coarse grit and progressing to finer grits for a polished finish.
Always carve away from your body and keep your tools sharp for easier cutting and better control.
Finishing Touches
After carving, apply finishing touches to enhance the beauty and longevity of your mask.
- Painting/Staining: Choose colors that complement your design. Use brushes for detailed work and spray for even coverage.
- Sealing: Protect your mask with a clear varnish or sealant to guard against moisture and wear.
Allow ample drying time between each application to ensure a durable finish.
By following these guidelines, you can create beautifully crafted wooden masks that showcase your creativity and skill.
Materials Needed
Creating wooden masks requires specific materials to achieve the desired artistic effect. Below is a list of essential items:
- Wood: Basswood, pine, or cedar are ideal due to their workability and availability.
- Tools:
- Carving knives
- Chisels
- Sandpaper (various grits)
- Saws (band saw or coping saw)
- Drill with various bits
- Finishing Supplies:
- Wood stain or paint
- Sealer (polyurethane or natural oils)
- Brushes and rags
- Safety Gear:
- Dust mask
- Safety goggles
- Gloves
Designing the Mask
The design process is crucial for creating an effective wooden mask. This phase involves several steps:
- Inspiration: Research various mask styles from different cultures or eras.
- Sketching: Create rough sketches of your ideas, focusing on the shape and features.
- Measurements: Determine the dimensions of the mask based on the intended size and wearability.
- Template Creation: Draw a full-sized template on paper to guide the cutting process.
Carving the Mask
Once the design is finalized, the next step is carving. Follow these guidelines:
- Transfer the Template: Trace the design onto the wood using carbon paper or by freehand drawing.
- Cutting the Shape: Use a saw to cut out the basic shape of the mask.
- Rough Carving: Begin shaping the mask using larger chisels and carving knives. Focus on defining the features such as eyes, nose, and mouth.
- Detailing: Switch to smaller tools for intricate details. Work gradually, refining the mask’s features.
Sanding and Smoothing
After the carving is complete, sanding is essential for a smooth finish:
- Progressive Sanding: Start with coarse grit sandpaper (60-80) and move to finer grits (220-320).
- Focus Areas: Pay attention to edges and detailed areas to remove any roughness or tool marks.
- Final Touches: Ensure the mask is smooth to the touch without any splinters.
Finishing the Mask
Applying a finish not only enhances the appearance but also protects the wood:
- Staining/Painting: Apply wood stain or paint to achieve the desired color. Use brushes for even coverage.
- Sealing: Once the stain or paint dries, apply a sealer to protect the mask from moisture and wear.
- Drying Time: Allow adequate drying time between coats as specified by the product instructions.
Adding Straps and Accessories
To complete the mask, consider adding straps and decorative elements:
- Straps: Attach elastic or fabric straps to the sides of the mask for easy wearing. Ensure they are securely fastened.
- Decorative Elements: Enhance the mask with beads, feathers, or other embellishments as desired.
- Final Assembly: Check all components for stability and comfort.
Displaying or Wearing the Mask
Decide on the mask’s purpose—whether for display or wear:
- Display: Consider mounting options such as wall brackets or stands that suit your aesthetic.
- Wearing: Ensure that the mask fits comfortably and securely for intended use, especially for performance or cultural events.
Expert Insights on Crafting Wooden Masks
Maria Gonzalez (Master Woodworker, Artisan Crafts Journal). “Creating wooden masks requires a deep understanding of both the material and the cultural significance behind the designs. I recommend starting with a softwood like pine, as it is easier to carve and shape, allowing for intricate details that can bring your mask to life.”
James Liu (Cultural Anthropologist, Global Arts Review). “When making wooden masks, it is essential to research the cultural context of the mask you wish to create. Each mask carries its own story and meaning, which can greatly influence the design choices and techniques used in the crafting process.”
Elena Torres (Sculptor and Art Educator, Creative Expressions Magazine). “I advise aspiring mask makers to experiment with different finishing techniques, such as wood stains and paints, to enhance the visual appeal of their masks. A well-finished mask not only showcases the craftsmanship but also protects the wood from damage.”
Frequently Asked Questions (FAQs)
What materials do I need to make wooden masks?
To create wooden masks, you will need a suitable type of wood (such as basswood or pine), carving tools (like chisels and knives), sandpaper, wood glue, and finishing materials (such as paint or varnish).
What tools are essential for carving wooden masks?
Essential tools for carving wooden masks include a set of carving knives, chisels, a coping saw, a rasp, and sandpaper. Additional tools like a mallet and a wood burner can enhance details and finishing.
How do I design a wooden mask before carving?
Begin by sketching your design on paper, considering the mask’s size and shape. Transfer the design onto the wood using carbon paper or by drawing directly on the surface. Ensure the proportions and features align with your vision.
What safety precautions should I take while carving wooden masks?
Always wear safety goggles to protect your eyes from wood chips. Use gloves to prevent cuts and ensure your workspace is well-lit and organized. Maintain a stable grip on the wood and tools, and carve away from your body to minimize injury risk.
How can I finish my wooden mask after carving?
After carving, sand the mask thoroughly to smooth any rough edges. Apply a wood stain or paint for color, followed by a clear varnish or sealant to protect the surface. Allow each layer to dry completely before applying the next.
Can I use power tools for making wooden masks?
Yes, power tools such as rotary tools or power sanders can expedite the carving and finishing process. However, they require careful handling and practice to ensure precision and safety during use.
In summary, creating wooden masks is a rewarding craft that combines artistry with traditional woodworking techniques. The process typically involves selecting the right type of wood, sketching a design, and carefully carving the mask. Tools such as chisels, saws, and sanders play a crucial role in shaping the wood, while finishing techniques like staining or painting enhance the mask’s aesthetic appeal. Understanding the cultural significance of masks can also enrich the crafting experience, allowing artisans to connect with historical and artistic contexts.
Key takeaways from the discussion include the importance of preparation and planning in the mask-making process. Properly selecting materials and tools can significantly impact the final product’s quality. Additionally, safety precautions should always be prioritized when working with sharp tools and machinery. Engaging with the community, whether through workshops or online forums, can also provide valuable insights and inspiration for both novice and experienced mask makers.
Ultimately, making wooden masks is not just about the end result but also about the journey of creativity and skill development. Each mask tells a story and reflects the maker’s unique vision. By embracing both the technical and artistic aspects of this craft, individuals can create meaningful pieces that resonate with both the maker and the audience.
Author Profile
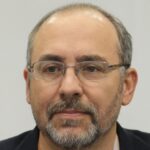
-
Darryl Norman is a seasoned entrepreneur and industry expert with a deep understanding of wood truss manufacturing and construction materials. As the President of Timberlake TrussWorks, LLC, Darryl played a pivotal role in shaping the company’s reputation for quality and precision. His leadership ensured that each truss met rigorous structural standards, providing builders with dependable components essential to their projects.
Beginning in 2025, Darryl Norman has shifted his focus to education and knowledge-sharing through an informative blog dedicated to wood truss manufacturing. Drawing from his extensive experience in the field, he provides in-depth insights into truss design, material selection, and construction techniques. This blog serves as a valuable resource for builders, contractors, and homeowners seeking practical guidance on truss systems and structural integrity.
Latest entries
- March 18, 2025General Wood TopicsWhat Color Is Ebony Wood? Unveiling the Rich Hues of This Luxurious Timber
- March 18, 2025Construction & FrameworkHow Can You Effectively Mount a Headboard to Your Wall?
- March 18, 2025General Wood TopicsCan Bees Really Eat Wood? Unraveling the Myths and Facts
- March 18, 2025General Wood TopicsDo Rabbits Really Chew on Wood? Exploring Their Eating Habits!