How Can You Easily Make Your Own Wooden Planks at Home?
Introduction
Woodworking is a timeless craft that not only connects us to nature but also allows us to create beautiful, functional items from one of the most versatile materials on Earth: wood. Among the foundational skills every woodworker should master is the art of making wooden planks. Whether you’re a seasoned craftsman or a curious beginner, understanding how to transform raw lumber into usable planks opens up a world of possibilities for your projects. In this article, we will explore the essential techniques and tools needed to create wooden planks, guiding you through the process step by step.
To make wooden planks, one must first appreciate the journey from tree to timber. The process begins with selecting the right type of wood, which can vary based on the intended use and desired aesthetic. Once the lumber is sourced, it undergoes a series of transformations, including cutting, planing, and sanding, to achieve the desired thickness and smoothness. Each step is crucial, as it not only affects the final appearance of the planks but also their durability and functionality in various projects.
As we delve deeper into the methods of creating wooden planks, we will discuss the tools required, safety precautions to consider, and tips for achieving the best results. Whether you’re looking to build furniture, craft
Choosing the Right Wood
Selecting the appropriate type of wood is crucial for producing quality wooden planks. Different woods offer varied aesthetics, durability, and workability. Here are some popular choices:
- Pine: Affordable and easy to work with, ideal for beginners.
- Oak: Known for its strength and beautiful grain; suitable for furniture.
- Maple: Offers durability and a fine texture, often used in cabinetry.
- Cedar: Naturally resistant to decay, perfect for outdoor projects.
When choosing wood, consider factors such as availability, budget, and the intended use of the planks.
Tools Required
To create wooden planks, you will need a variety of tools to ensure precision and efficiency. The essential tools include:
- Circular Saw: For cutting large pieces of wood into manageable sizes.
- Planer: To smooth and even out the surface of the wood.
- Table Saw: For making straight cuts and ensuring uniform thickness.
- Sander: To finish the planks and prepare them for staining or sealing.
Using high-quality tools will significantly affect the final product’s quality.
Step-by-Step Process
The process of making wooden planks involves several key steps:
- Select and Prepare the Logs:
- Choose logs free from defects.
- Cut them to a manageable length.
- Debarking:
- Remove the bark using a drawknife or a debarking tool to expose the wood underneath.
- Cutting to Size:
- Use a circular saw to cut the logs into rough planks. Aim for an approximate thickness of 1 inch.
- Drying the Wood:
- Air-drying or kiln-drying is essential to prevent warping. Air-dry in a shaded, ventilated area for several months or use a kiln for quicker results.
- Planing:
- Once dry, pass the planks through a planer to achieve uniform thickness and a smooth surface.
- Sanding:
- Sand the planks with progressively finer sandpaper, starting with coarse grit and finishing with fine grit.
- Finishing:
- Apply a finish such as stain or sealant to protect the wood and enhance its appearance.
Considerations for Quality Control
Maintaining quality throughout the plank-making process is vital. Here are some points to monitor:
- Moisture Content: Ensure that the wood is properly dried to avoid future warping or cracking.
- Thickness Consistency: Use a caliper to check that all planks are of uniform thickness.
- Surface Smoothness: Inspect for any rough patches or blemishes after sanding.
Wood Type | Durability | Cost | Best Use |
---|---|---|---|
Pine | Moderate | Low | Indoor projects |
Oak | High | Medium | Furniture |
Maple | High | Medium | Cabinetry |
Cedar | High | Medium | Outdoor projects |
Materials Required
To create wooden planks, gather the following materials:
- Logs: Select hardwood or softwood depending on the intended use.
- Saw: A chainsaw or a bandsaw is ideal for cutting logs into rough planks.
- Planer: For smoothing the surface and achieving uniform thickness.
- Sander: To finish the edges and provide a polished surface.
- Measuring Tools: A tape measure and square to ensure accuracy.
- Protective Gear: Safety goggles, gloves, and ear protection for safety.
Cutting the Logs
Begin by cutting the logs into manageable lengths. This can be achieved using a chainsaw or bandsaw. Follow these steps for precision:
- Select Log: Choose a log free of defects.
- Measure Length: Use a measuring tape to determine the desired length of the planks.
- Mark the Cuts: Clearly mark the cut lines with a pencil.
- Cut the Log: Carefully saw along the marked lines to create rough planks. Ensure to maintain a steady hand for straight cuts.
Resawing and Smoothing the Planks
After obtaining rough planks, the next step is to resaw them into thinner pieces if necessary. Use the following methods:
- Resawing: Use a bandsaw to cut the thickness of the planks to your specifications.
- Planing: Pass each plank through a planer to achieve a uniform thickness. This step eliminates any uneven surfaces.
Finishing Touches
Once planed, the planks need to be sanded for a smooth finish. Follow these steps:
- Select Sandpaper: Choose appropriate grit sandpaper (start with a lower grit, e.g., 80, and progress to higher grits, e.g., 220).
- Sand the Planks: Sand each plank thoroughly on all sides. Pay special attention to edges and corners.
- Cleaning: Wipe the planks with a cloth to remove dust after sanding.
Optional Treatments
To enhance durability and appearance, consider treating the wooden planks:
- Staining: Apply wood stain to add color and highlight grain patterns.
- Sealing: Use a wood sealer to protect against moisture and wear.
- Finishing: Apply a finish such as polyurethane or varnish for added protection.
Storage of Wooden Planks
Proper storage is essential to maintain the quality of your wooden planks. Consider the following guidelines:
- Dry Environment: Store planks in a dry area to prevent warping.
- Elevate: Place planks off the ground on pallets or similar supports.
- Ventilation: Ensure good airflow around stored planks to reduce moisture accumulation.
Common Uses for Wooden Planks
Wooden planks have a wide range of applications, including:
Application | Description |
---|---|
Furniture Making | Used for tables, chairs, and cabinets. |
Flooring | Ideal for hardwood or laminate flooring options. |
Construction | Used in framing, sheathing, and decking. |
Craft Projects | Suitable for DIY projects and artistic creations. |
Ensure to choose the right type of wood for your specific application to achieve desired results.
Expert Insights on Crafting Wooden Planks
James Holloway (Master Carpenter, Timber Craft Guild). “The process of making wooden planks begins with selecting the right type of wood. Hardwoods like oak or maple provide durability, while softwoods such as pine are easier to work with. Properly milling the wood to achieve uniform thickness is crucial for quality.”
Linda Chen (Woodworking Instructor, Artisan School of Craft). “Safety should always be a priority when making wooden planks. Using appropriate personal protective equipment and ensuring that your tools are well-maintained can prevent accidents during the cutting and sanding processes.”
Mark Thompson (Sustainable Forestry Consultant, Green Wood Initiative). “Choosing sustainably sourced wood is essential in the plank-making process. Not only does it support environmental conservation, but it also enhances the quality of the final product. Always look for certifications like FSC to ensure responsible sourcing.”
Frequently Asked Questions (FAQs)
How do I select the right type of wood for making wooden planks?
Choosing the right type of wood depends on the intended use of the planks. Hardwoods like oak and maple are ideal for furniture, while softwoods like pine and cedar are suitable for construction and outdoor projects.
What tools do I need to make wooden planks?
Essential tools include a saw (circular or table saw), a planer for smoothing surfaces, a sander for finishing, and safety equipment such as goggles and gloves.
What is the process for cutting wood into planks?
The process involves measuring the desired dimensions, marking the wood, and using a saw to cut along the marked lines. Ensure to cut slowly and steadily for accuracy.
How can I ensure my wooden planks are straight and even?
Using a planer after cutting will help achieve uniform thickness. Additionally, employing a straight edge during the cutting process ensures that the edges remain straight.
What finishing options are available for wooden planks?
Finishing options include sanding, staining, and sealing with polyurethane or varnish. These finishes enhance the appearance and protect the wood from moisture and wear.
How do I store wooden planks to prevent warping?
Store wooden planks in a dry, cool environment, elevated off the ground to allow air circulation. Stacking them flat and using spacers can also help maintain their shape.
In summary, the process of making wooden planks involves several key steps that transform raw timber into usable materials. Initially, selecting the right type of wood is crucial, as different species offer varying qualities and characteristics. Once the wood is chosen, it must be properly cut into logs, which are then debarked to remove the outer layer. Following this, the logs are sawn into planks using specialized equipment, ensuring that the dimensions and thickness meet the desired specifications.
After the sawing process, the planks require drying to reduce moisture content and prevent warping or splitting. This can be achieved through air drying or kiln drying methods, each with its own advantages. Once dried, the planks can be further processed by planing and sanding to achieve a smooth finish, making them ready for various applications in construction, furniture making, and other woodworking projects.
making wooden planks is a systematic process that requires attention to detail at each stage, from selecting the right wood to the final finishing touches. Understanding these steps not only enhances the quality of the planks produced but also ensures their suitability for intended uses. With proper techniques and equipment, anyone can successfully create wooden planks that are both functional and aesthetically pleasing.
Author Profile
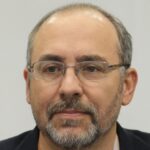
-
Darryl Norman is a seasoned entrepreneur and industry expert with a deep understanding of wood truss manufacturing and construction materials. As the President of Timberlake TrussWorks, LLC, Darryl played a pivotal role in shaping the company’s reputation for quality and precision. His leadership ensured that each truss met rigorous structural standards, providing builders with dependable components essential to their projects.
Beginning in 2025, Darryl Norman has shifted his focus to education and knowledge-sharing through an informative blog dedicated to wood truss manufacturing. Drawing from his extensive experience in the field, he provides in-depth insights into truss design, material selection, and construction techniques. This blog serves as a valuable resource for builders, contractors, and homeowners seeking practical guidance on truss systems and structural integrity.
Latest entries
- March 18, 2025General Wood TopicsWhat Color Is Ebony Wood? Unveiling the Rich Hues of This Luxurious Timber
- March 18, 2025Construction & FrameworkHow Can You Effectively Mount a Headboard to Your Wall?
- March 18, 2025General Wood TopicsCan Bees Really Eat Wood? Unraveling the Myths and Facts
- March 18, 2025General Wood TopicsDo Rabbits Really Chew on Wood? Exploring Their Eating Habits!