How Can You Create Your Own Wooden Surfboard?
Introduction
Surfing is more than just a sport; it’s a lifestyle, a culture, and for many, a form of artistic expression. Among the various types of surfboards, wooden surfboards hold a unique charm and nostalgia, harkening back to the roots of surfing itself. Crafting your own wooden surfboard is not only a rewarding project but also an opportunity to connect with the ocean in a profoundly personal way. Whether you’re a seasoned surfer looking to deepen your craft or a woodworking enthusiast eager to try something new, learning how to make a wooden surfboard can be an exciting journey. In this article, we will explore the essential steps, materials, and techniques involved in creating your very own wooden surfboard, allowing you to ride the waves on a board that reflects your individuality and passion.
Creating a wooden surfboard is a blend of art and science, requiring careful planning, skillful craftsmanship, and an understanding of hydrodynamics. The process begins with selecting the right type of wood, as this choice significantly impacts the board’s performance and aesthetics. From the classic appeal of cedar to the durability of marine plywood, each material offers unique benefits that cater to different surfing styles and preferences. As you delve into the construction process, you’ll discover the importance of shaping
Materials Needed
To create a wooden surfboard, selecting the right materials is crucial for ensuring durability and performance. The following materials are commonly used:
- Laminated Wood: Often made from various types of hardwood or softwood, suitable for the board’s shape and flexibility.
- Epoxy Resin: For waterproofing and strength, epoxy resin is preferred over polyester resin due to its superior bonding properties.
- Fiberglass Cloth: Used to reinforce the board, providing structural integrity while keeping it lightweight.
- Foam Core: A lightweight foam is often integrated to reduce weight without sacrificing buoyancy.
Tools Required
A variety of tools will aid in the construction process. Key tools include:
- Saw: A band saw or circular saw for cutting the wood.
- Sander: A power sander for smoothing the edges and surfaces.
- Router: For shaping the rails and adding contours.
- Clamps: To hold pieces together during the glue-up process.
- Brushes and Rollers: For applying resin evenly.
Tool | Purpose |
---|---|
Saw | Cutting wood into desired shapes |
Sander | Smoothing surfaces |
Router | Shaping edges and curves |
Clamps | Securing pieces during assembly |
Brushes/Rollers | Applying resin |
Shaping the Board
The shaping process is pivotal to the performance characteristics of the surfboard. Follow these steps:
- Design the Template: Create a template of your desired surfboard shape using cardboard or paper. This will serve as a guide for cutting your wood.
- Cutting the Wood: Use the template to mark your wood pieces and cut them accurately with a saw.
- Shaping the Outline: Employ a planer or sander to refine the outline, ensuring smooth curves and edges.
- Creating the Rocker: Achieve the desired rocker by adjusting the thickness of the board at different points. This affects how the board rides on waves.
Assembling the Surfboard
Once the shaping is complete, the next step is assembly. This involves:
- Gluing the Pieces: Apply epoxy resin to bond the wood layers together. Make sure to use clamps to hold them securely as they cure.
- Adding the Foam Core: If using a foam core, insert it into the laminated structure and seal it with additional resin.
- Reinforcing with Fiberglass: Lay fiberglass cloth over the board’s surface, saturating it with resin. This step enhances durability and reduces the risk of water damage.
Finishing Touches
After the assembly has cured, it’s time for the finishing touches:
- Sanding: Smooth the entire surface to eliminate any rough spots from the fiberglass application.
- Applying Final Coats: Apply additional layers of resin for a glossy finish, ensuring a waterproof barrier.
- Installing Fins: Attach fin boxes or permanently install fins based on your design.
By following these detailed instructions, you can craft a functional wooden surfboard tailored to your surfing style. Each step is critical in ensuring the board’s performance and longevity on the waves.
Materials Required
To craft a wooden surfboard, several materials are essential to ensure durability, performance, and aesthetics. Below is a list of the primary materials needed:
- Lumber: Choose high-quality wood such as:
- Paulownia
- Cedar
- Plywood (marine-grade for better water resistance)
- Epoxy Resin: For waterproofing and strength.
- Fiberglass Cloth: For reinforcing the board.
- Foam Blank: If a lightweight core is desired.
- Sandpaper: Various grits for smoothing surfaces.
- Wood Glue: For securing joints and layers.
- Wood Sealer: To protect the wood from moisture.
Designing the Surfboard
Before starting the construction, an effective design is crucial. This includes determining the board’s dimensions and shape. Consider the following:
- Length: Common lengths range from 5’ to 10’.
- Width: Typically between 18” to 24”.
- Thickness: Generally 2” to 3”.
- Tail Shape: Options include square, round, or swallow.
- Nose Shape: Can be pointed, rounded, or blunt.
Create a detailed sketch or use design software for precision.
Shaping the Board
Shaping the wooden surfboard involves cutting and refining the wood to match your design. Follow these steps:
- Cut the Blank: Use a jigsaw or bandsaw to cut the wood according to your design.
- Outline the Shape: Mark the outlines on the board using a pencil.
- Rough Shaping: Use a planer to remove excess material and shape the board.
- Fine Shaping: Employ hand tools like a surform or sanders for detailed shaping.
Applying Fiberglass and Resin
Once the board is shaped, it needs to be reinforced with fiberglass and resin to enhance durability.
- Prepare the Surface: Sand the board to create a rough texture for adhesion.
- Cut Fiberglass Cloth: Measure and cut the cloth to cover the entire board.
- Mix Epoxy Resin: Follow the manufacturer’s instructions for mixing.
- Apply Resin:
- Lay the fiberglass cloth on the board.
- Pour resin over the cloth and spread it evenly using a squeegee.
- Cure Time: Allow the resin to cure as per the product’s guidelines, typically 24 hours.
Finishing Touches
After the resin has cured, focus on the finishing touches that enhance both appearance and performance.
- Sanding: Smooth the surface using progressively finer sandpaper.
- Sealing: Apply a wood sealer to protect against water damage.
- Painting or Varnishing: Optional decorative finishes can be added at this stage.
- Installing Fins: Choose fin boxes that suit your surfing style and install them securely.
Testing the Surfboard
Before hitting the waves, conduct a series of tests to ensure your surfboard is seaworthy.
- Visual Inspection: Check for any cracks or weak spots.
- Weight Test: Assess buoyancy and stability by holding it in water.
- Trial Run: Take the surfboard for a short ride in calm waters to evaluate performance.
This process will help confirm that your wooden surfboard is ready for surfing adventures.
Expert Insights on Crafting Wooden Surfboards
Mark Thompson (Master Surfboard Shaper, SurfCraft Designs). “When making a wooden surfboard, selecting the right type of wood is crucial. I recommend using lightweight woods like Paulownia or Cedar, as they provide the perfect balance of strength and buoyancy, ensuring optimal performance in the water.”
Lisa Chen (Marine Engineer, Oceanic Innovations). “The shaping process is where the magic happens. Utilizing a combination of hand tools and power tools allows for precision in creating the board’s contours. Pay close attention to the rocker and rail design, as these elements significantly affect the board’s maneuverability and speed.”
James Rivera (Sustainable Materials Specialist, EcoSurf Co.). “Incorporating sustainable practices is essential when building wooden surfboards. Opting for reclaimed wood not only reduces waste but also adds character to each board. Additionally, using eco-friendly resins can enhance durability while minimizing environmental impact.”
Frequently Asked Questions (FAQs)
What materials are needed to make a wooden surfboard?
To make a wooden surfboard, you will need marine-grade plywood or solid wood, epoxy resin, fiberglass cloth, a saw, sandpaper, clamps, and a heat gun. Additional tools may include a router, planer, and a measuring tape.
What is the best type of wood for crafting a surfboard?
The best types of wood for crafting a surfboard include cedar, mahogany, and balsa. These woods are lightweight, durable, and provide excellent buoyancy, making them suitable for surfboard construction.
How do I shape the wooden surfboard?
Shaping the wooden surfboard involves cutting the wood to the desired dimensions, then using a planer and sandpaper to refine the shape. The goal is to create a smooth, hydrodynamic profile that enhances performance on the water.
What is the process for sealing and finishing the surfboard?
The surfboard should be sealed with epoxy resin to protect it from water damage. Apply multiple coats, allowing each to cure fully before sanding and polishing the surface to achieve a smooth, glossy finish.
How long does it take to make a wooden surfboard?
The time required to make a wooden surfboard can vary significantly, but typically it takes between 20 to 40 hours spread over several days. This includes shaping, sealing, and finishing processes.
Can I customize the design of my wooden surfboard?
Yes, you can customize the design of your wooden surfboard. You can incorporate different wood types, colors, and patterns, as well as unique shapes and sizes to suit your personal style and performance preferences.
making a wooden surfboard is a rewarding and intricate process that combines craftsmanship with an understanding of surfboard design. The journey begins with selecting the right type of wood, typically lightweight and durable options such as cedar or mahogany, which will contribute to the board’s performance and longevity. Properly preparing the wood involves cutting, shaping, and sanding to achieve the desired dimensions and contours, ensuring that the board is both functional and aesthetically pleasing.
Furthermore, the construction phase includes assembling the wooden pieces, applying fiberglass for added strength, and finishing the board with a protective sealant. Each step requires attention to detail, as the quality of materials and craftsmanship directly influences the board’s performance in the water. It is essential to follow safety protocols and use the appropriate tools to achieve the best results while minimizing risks during the construction process.
Ultimately, the satisfaction derived from crafting a wooden surfboard lies not only in the final product but also in the skills acquired throughout the process. This endeavor fosters a deeper appreciation for the art of surfboard making and enhances the overall surfing experience. By investing time and effort into creating a unique wooden surfboard, individuals can enjoy a personalized ride that reflects their style and dedication to the sport.
Author Profile
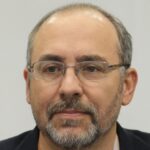
-
Darryl Norman is a seasoned entrepreneur and industry expert with a deep understanding of wood truss manufacturing and construction materials. As the President of Timberlake TrussWorks, LLC, Darryl played a pivotal role in shaping the company’s reputation for quality and precision. His leadership ensured that each truss met rigorous structural standards, providing builders with dependable components essential to their projects.
Beginning in 2025, Darryl Norman has shifted his focus to education and knowledge-sharing through an informative blog dedicated to wood truss manufacturing. Drawing from his extensive experience in the field, he provides in-depth insights into truss design, material selection, and construction techniques. This blog serves as a valuable resource for builders, contractors, and homeowners seeking practical guidance on truss systems and structural integrity.
Latest entries
- March 18, 2025General Wood TopicsWhat Color Is Ebony Wood? Unveiling the Rich Hues of This Luxurious Timber
- March 18, 2025Construction & FrameworkHow Can You Effectively Mount a Headboard to Your Wall?
- March 18, 2025General Wood TopicsCan Bees Really Eat Wood? Unraveling the Myths and Facts
- March 18, 2025General Wood TopicsDo Rabbits Really Chew on Wood? Exploring Their Eating Habits!