How Can You Create Perfect Wooden Wheels at Home?
Wooden wheels have been a staple of craftsmanship for centuries, embodying both functionality and artistry. Whether you’re a seasoned woodworker or a curious beginner, the allure of creating your own wooden wheels is undeniable. From the rustic charm they bring to your projects to their practical applications in toys, furniture, and even vehicles, wooden wheels offer a unique blend of creativity and utility. In this article, we will explore the fascinating world of wooden wheel making, guiding you through the essential techniques and tools needed to bring your vision to life. So, roll up your sleeves and get ready to embark on a rewarding journey into the art of woodworking!
Overview
Making wooden wheels involves a combination of traditional techniques and modern tools, allowing artisans to create pieces that are both beautiful and functional. The process typically begins with selecting the right type of wood, which not only affects the wheel’s durability but also its aesthetic appeal. Once the wood is chosen, various methods can be employed to shape and assemble the wheels, ensuring they are perfectly balanced and ready for use.
In addition to the technical aspects, crafting wooden wheels also invites a deeper appreciation for the craftsmanship involved. Each wheel tells a story, reflecting the skill and creativity of the maker. Whether you’re looking to enhance your woodworking skills or simply
Choosing the Right Wood
Selecting the appropriate type of wood is crucial for making durable wooden wheels. The wood should be strong yet lightweight, with a fine grain for a smooth finish. Some recommended types of wood include:
- Hard Maple: Known for its durability and strength, it can withstand heavy loads.
- Birch: A lighter option that also offers good strength, making it suitable for smaller wheels.
- Oak: Offers excellent strength and aesthetic appeal but can be heavier.
- Pine: A cost-effective choice, though less durable than hardwood options.
Consider the application of your wheels, as this will influence the type of wood you choose.
Tools Required
The following tools are essential for crafting wooden wheels:
- Saw: A band saw or jigsaw for cutting the wood to the desired shape.
- Lathe: For shaping the wheels into a perfect circular form.
- Drill: To create holes for axle fittings.
- Sandpaper: For smoothing the surface and edges.
- Clamps: To hold the wood securely while working.
Having the right tools ensures precision and quality in the finished product.
Designing the Wheel
Designing the wheel involves several considerations, including diameter, width, and the type of hub. The design process can be summarized in the following steps:
- Determine the Wheel Size: Based on the intended use, decide on the diameter and width.
- Sketch the Design: Create a blueprint that includes dimensions and features.
- Choose the Hub Style: The hub can be a solid block or a more intricate design, depending on the wheel’s application.
A simple design table for wheel specifications is as follows:
Diameter (inches) | Width (inches) | Wood Type | Application |
---|---|---|---|
12 | 4 | Hard Maple | Heavy-duty carts |
10 | 2 | Birch | Small toys |
14 | 6 | Oak | Wagons |
8 | 3 | Pine | Garden carts |
Cutting and Shaping the Wheels
Once the design is finalized, proceed to cut and shape the wheels. Follow these steps:
- Cut the Wood: Use your saw to cut the wood into rough circles based on your design dimensions.
- Mount on Lathe: Secure the cut wood on the lathe and begin shaping it into a perfect circle. Ensure that the wheel is symmetrical.
- Create the Hub: Drill a hole in the center for the axle, making sure it fits snugly to prevent wobbling.
Regularly check the balance of the wheel during the shaping process to ensure optimal performance.
Sanding and Finishing
After shaping, sand the wheels thoroughly to smooth out any rough edges or imperfections. Start with a coarse grit sandpaper and gradually move to finer grits for a polished finish.
- Apply Finish: Choose a suitable finish, such as varnish or wood oil, to protect the wood from moisture and wear. This step enhances the aesthetics and longevity of the wheels.
- Final Inspection: Check for any remaining rough spots and ensure the axle hole is clean and precisely cut.
These processes ensure that the wooden wheels are not only functional but also visually appealing.
Materials Required
To craft wooden wheels, specific materials are essential for achieving durability and functionality. The following list outlines the primary materials needed:
- Wood: Hardwoods such as oak, maple, or birch are preferred for strength and wear resistance.
- Wood Glue: For bonding joints securely.
- Wood Finish: To protect against moisture and wear.
- Sandpaper: Various grits for smoothing surfaces.
- Saw: A band saw or hand saw for cutting the wood.
- Drill: To create holes for axles.
- Measuring Tools: Ruler or calipers for precision.
- Clamps: To hold pieces in place while drying.
Designing the Wheels
Before beginning the construction, it is crucial to have a design plan in place.
- Determine Size: Decide on the diameter and thickness based on the intended use.
- Wheel Shape: Standard designs include flat, beveled, or spoked wheels. Each has its own advantages for different applications.
- Axle Hole Placement: Ensure proper positioning of axle holes to maintain balance and allow for smooth rotation.
Cutting the Wood
Once the design is finalized, proceed with cutting the wood to the desired dimensions.
- Marking: Use a measuring tool to mark the circles for the wheels on the wood.
- Cutting: Carefully cut out the circles using a band saw or a jigsaw, ensuring that each wheel is uniform.
- Drilling Axle Holes: Drill a centered hole through each wheel to accommodate the axle.
Sanding and Smoothing
Post-cutting, it is vital to smooth the surfaces to prevent splinters and enhance aesthetics.
- Start with Coarse Grit: Use 80-grit sandpaper to remove any rough edges.
- Progress to Finer Grit: Move to 120-grit and then 220-grit sandpaper for a smooth finish.
- Inspect: Check for any remaining imperfections and sand as needed.
Assembling the Wheels
After sanding, the next step is assembling the wheels.
- Glue Joints: If using multiple pieces (for spoked wheels), apply wood glue to the joints and clamp them until dried.
- Finishing: Apply a wood finish to protect the wheels from moisture and wear, ensuring even coverage.
- Final Touches: Sand any areas where glue has seeped out and ensure a smooth finish.
Installing the Wheels
Once the wheels are fully assembled and dried, they can be installed on the desired structure.
- Select Axle: Choose an appropriate axle material, ensuring it fits snugly through the wheel holes.
- Attach Wheels: Slide the wheels onto the axle, ensuring they rotate freely.
- Secure: Use washers or cotter pins to secure the wheels in place, preventing them from sliding off.
Maintenance Tips
To prolong the life of wooden wheels, regular maintenance is necessary. Consider the following:
- Inspect Regularly: Check for signs of wear or damage and address immediately.
- Reapply Finish: Depending on usage, reapply wood finish annually to protect against environmental elements.
- Store Properly: Keep wheels in a dry area to prevent moisture damage.
By following these detailed steps, you can successfully create wooden wheels tailored to your specific needs. Whether for a project, craft, or functional use, the quality of your wheels will reflect the care taken during the construction process.
Expert Insights on Crafting Wooden Wheels
Emily Carter (Master Woodworker, Artisan’s Guild). “When creating wooden wheels, it is essential to select the right type of wood. Hardwoods like oak or maple provide durability and strength, which are crucial for the wheel’s longevity and performance.”
James Thompson (Mechanical Engineer, Vintage Vehicle Restoration). “Precision in measurement and cutting is vital. Utilizing a lathe can ensure that the wheels are perfectly round, which minimizes friction and enhances the overall efficiency of the vehicle.”
Linda Garcia (Historian and Craft Specialist, Heritage Crafts Society). “Understanding historical techniques can greatly enhance your craftsmanship. Many traditional methods involve hand-carving and steam-bending, which not only produce aesthetically pleasing wheels but also connect you to the rich history of woodworking.”
Frequently Asked Questions (FAQs)
What materials are needed to make wooden wheels?
To make wooden wheels, you will need hardwood or softwood lumber, wood glue, clamps, sandpaper, a saw (preferably a band saw or jigsaw), a drill, and dowels or axles for assembly.
What tools are essential for crafting wooden wheels?
Essential tools include a band saw or jigsaw for cutting the wheel shape, a drill for creating axle holes, clamps for securing pieces while the glue dries, and sandpaper for smoothing the edges.
How do I determine the size of the wooden wheels?
The size of the wooden wheels depends on the intended use. For toy vehicles, wheels typically range from 2 to 4 inches in diameter, while larger projects may require wheels up to 12 inches or more.
What is the best method for shaping wooden wheels?
The best method for shaping wooden wheels involves cutting a circular pattern using a band saw or jigsaw, followed by sanding to achieve a smooth, even surface. A router can also be used for decorative edges.
How can I ensure the wheels are balanced?
To ensure the wheels are balanced, measure and cut each wheel to the same diameter and thickness. After shaping, test the balance by spinning the wheel on a flat surface; adjust as necessary by sanding uneven areas.
What finishing options are available for wooden wheels?
Finishing options include applying wood stain for color, using polyurethane or varnish for protection, or oil finishes for a natural look. Ensure the finish is compatible with the intended use of the wheels.
In summary, making wooden wheels involves a series of well-defined steps that require careful planning and execution. The process typically begins with selecting the appropriate type of wood, which should be durable and suitable for the intended use of the wheels. Common choices include hardwoods like oak or maple, which provide strength and longevity. Proper measurements and designs are crucial to ensure that the wheels fit their intended application, whether for toys, carts, or other projects.
After selecting the wood, the next steps involve cutting the wood into the desired shapes, sanding the edges for smoothness, and drilling holes for the axle. Each of these steps is vital to ensure that the wheels function correctly and are aesthetically pleasing. Additionally, applying finishes or sealants can enhance the durability of the wheels and protect them from environmental factors.
Key takeaways from the discussion include the importance of precision in measurements and cuts, as well as the selection of high-quality materials. Understanding the intended use of the wheels can guide the choice of wood and the design process. Lastly, safety precautions should always be followed when using tools and machinery to ensure a successful and safe woodworking experience.
Author Profile
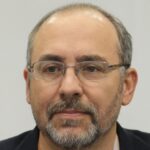
-
Darryl Norman is a seasoned entrepreneur and industry expert with a deep understanding of wood truss manufacturing and construction materials. As the President of Timberlake TrussWorks, LLC, Darryl played a pivotal role in shaping the company’s reputation for quality and precision. His leadership ensured that each truss met rigorous structural standards, providing builders with dependable components essential to their projects.
Beginning in 2025, Darryl Norman has shifted his focus to education and knowledge-sharing through an informative blog dedicated to wood truss manufacturing. Drawing from his extensive experience in the field, he provides in-depth insights into truss design, material selection, and construction techniques. This blog serves as a valuable resource for builders, contractors, and homeowners seeking practical guidance on truss systems and structural integrity.
Latest entries
- March 18, 2025General Wood TopicsWhat Color Is Ebony Wood? Unveiling the Rich Hues of This Luxurious Timber
- March 18, 2025Construction & FrameworkHow Can You Effectively Mount a Headboard to Your Wall?
- March 18, 2025General Wood TopicsCan Bees Really Eat Wood? Unraveling the Myths and Facts
- March 18, 2025General Wood TopicsDo Rabbits Really Chew on Wood? Exploring Their Eating Habits!