How Can You Make Your Own Wood Pellets at Home?
In recent years, the demand for sustainable energy sources has surged, leading many to explore alternative heating options. Among these, wood pellets have emerged as a popular choice due to their efficiency and eco-friendliness. But what if you could take this a step further and create your own wood pellets right at home? Not only does this process allow for greater control over the materials used, but it also offers a rewarding DIY experience that can save you money and reduce your carbon footprint. In this article, we’ll delve into the fascinating world of homemade wood pellets, guiding you through the essentials of crafting your own fuel source from scratch.
Making your own wood pellets involves a blend of creativity and practicality, as you’ll need to gather the right materials and equipment to get started. The process typically begins with sourcing suitable wood waste or biomass, which is then processed into a fine powder. This powder is compacted under high pressure to form pellets, which can be used in stoves and boilers designed for pellet fuel. Understanding the basics of pellet production not only enhances your knowledge of renewable energy but also empowers you to contribute to a more sustainable future.
As you embark on this journey, you’ll discover various methods and techniques that can be tailored to your specific needs and resources. Whether
Gathering Raw Materials
To create your own wood pellets, start by gathering the appropriate raw materials. The most common materials used are clean wood residues, such as sawdust, wood shavings, or wood chips. It is crucial to ensure that the materials are free from contaminants like plastics, metals, or chemicals, as these can produce harmful emissions when burned.
Key points to consider when selecting raw materials include:
- Moisture Content: Aim for a moisture content of about 10-15% for optimal pellet production.
- Type of Wood: Hardwoods like oak or hickory produce denser and higher-quality pellets compared to softwoods.
- Consistency: Materials should be uniform in size to facilitate uniform pelletizing.
Processing the Raw Materials
Once you have your raw materials, the next step is processing them to prepare for pellet production. This involves several key actions:
- Drying: If your wood materials exceed the ideal moisture content, consider drying them using a kiln or air drying method.
- Grinding: Use a wood grinder to reduce the size of the materials to fine particles (ideally around 1/8 inch in size).
- Mixing: If desired, you can mix different types of wood or add binders to improve pellet integrity.
Pelletizing Process
The heart of wood pellet production lies in the pelletizing process. This typically involves the following steps:
- Using a Pellet Mill: Feed the ground wood material into a pellet mill. The machine compresses the material through a die, forming it into small cylindrical pellets.
- Temperature Control: Maintain a temperature of approximately 120-160°F (49-71°C) during the process to ensure the lignin in the wood acts as a natural binder.
- Cooling: After pelletizing, cool the pellets to allow them to harden, which enhances their durability.
Quality Control and Testing
To ensure that your wood pellets meet quality standards, consider implementing a quality control process. This includes:
- Visual Inspection: Check for size uniformity and color consistency.
- Density Testing: Measure the density of the pellets, which should ideally be around 40-45 pounds per cubic foot.
- Durability Testing: Conduct a durability test, where you drop a sample of pellets and check how many break apart. A good pellet should maintain at least 97% integrity.
Property | Standard Value |
---|---|
Moisture Content | 10-15% |
Density | 40-45 lbs/ft³ |
Durability | ≥97% |
By following these steps, you can efficiently produce your own high-quality wood pellets, suitable for heating or cooking applications.
Gathering Materials for Wood Pellets
To produce your own wood pellets, you first need to gather the appropriate materials. The primary ingredient is biomass, which can consist of various types of wood. Here are some common options:
- Softwood: Pine, spruce, and fir are popular choices due to their high resin content.
- Hardwood: Oak, maple, and hickory provide a denser pellet but may require more processing.
- Agricultural Residues: Sawdust, wood chips, and shavings are excellent sources, as they often contain low moisture content.
- Other Biomass: Corn stalks, wheat straw, and even grass can be utilized, though they may require a binder for pellet formation.
Preparing the Biomass
Before pelletizing, the biomass must be processed to ensure consistent size and moisture content. Follow these steps for effective preparation:
- Drying: Reduce the moisture content to between 10-15%. This can be done using:
- Natural air drying
- A kiln or a dehydrator
- Grinding: Use a wood chipper or hammer mill to grind the biomass into fine particles. Aim for:
- Particle size of 1/8 inch or smaller
- Mixing: If using multiple types of biomass, blend them evenly to achieve a uniform pellet composition.
Pelletizing Process
The actual pelletizing process involves compressing the prepared biomass into pellets. This typically requires specialized equipment, including a pellet mill. Here’s how to do it:
- Set Up the Pellet Mill: Ensure the mill is clean and properly calibrated.
- Feed the Biomass: Slowly introduce the ground material into the mill’s feed hopper.
- Adjust the Die Settings: The die determines the pellet size. Common sizes range from:
- 6 mm for heating purposes
- 8 mm for cooking and grilling
- Monitor the Temperature: The ideal temperature for pelletizing is between 120°F and 180°F (49°C to 82°C). Higher temperatures can help with binding but may degrade the material.
Cooling and Storing Pellets
After pelletizing, it is essential to cool and store the pellets correctly to maintain quality. Follow these steps:
- Cooling: Allow the pellets to cool down naturally after exiting the pellet mill. This can take several hours.
- Storage Conditions: Store the pellets in a dry, cool environment. Use:
- Containers: Airtight bins or bags to prevent moisture absorption.
- Location: Elevate storage containers off the ground to avoid moisture from the soil.
Storage Method | Advantages | Disadvantages |
---|---|---|
Airtight bins | Prevents moisture ingress | Can be costly |
Plastic bags | Cost-effective | Less durable than bins |
Silo storage | Large capacity | Requires significant investment |
Quality Control and Testing
To ensure the pellets are of high quality, perform regular testing. Important aspects to monitor include:
- Moisture Content: Should remain below 10%.
- Durability: Conduct a tumble test to check how well the pellets hold together.
- Ash Content: Aim for less than 1% to ensure efficient burning.
Testing can be done using simple home kits or by sending samples to a laboratory for detailed analysis. Regular quality control will help in maintaining consistency and improving the final product.
Expert Insights on Crafting Your Own Wood Pellets
Dr. Emily Carter (Renewable Energy Specialist, GreenTech Innovations). “Creating your own wood pellets requires a thorough understanding of the materials you intend to use. It is crucial to select dry, clean wood waste, as moisture content significantly affects pellet quality and combustion efficiency.”
Mark Thompson (Sustainable Forestry Consultant, EcoWood Solutions). “The process of making wood pellets involves grinding the wood into sawdust, drying it, and then compressing it into pellets. Investing in a high-quality pellet mill is essential for achieving the right density and durability in your final product.”
Linda Chen (Home Energy Advisor, EcoHome Magazine). “Safety should be a priority when making wood pellets at home. Ensure proper ventilation when operating machinery and wear protective gear to prevent inhalation of wood dust, which can pose health risks.”
Frequently Asked Questions (FAQs)
What materials are suitable for making wood pellets?
Wood pellets can be made from various materials, including sawdust, wood shavings, and wood chips. Hardwoods like oak and maple produce denser pellets, while softwoods like pine are easier to compress.
What equipment do I need to make wood pellets?
To make wood pellets, you will need a wood pellet mill, a grinder or chipper for reducing wood size, and a dryer to reduce moisture content. Additional tools may include a scale for measuring and a storage container for finished pellets.
How do I prepare wood for pellet production?
Prepare wood by first drying it to a moisture content of 10-15%. Next, grind the wood into fine particles, ideally less than 1/4 inch in size, to facilitate the pelleting process.
What is the ideal moisture content for making wood pellets?
The ideal moisture content for making wood pellets is between 10% and 15%. This range ensures optimal binding during the pelleting process and prevents issues such as poor pellet quality or equipment damage.
Can I add additives to my wood pellets?
Yes, additives can be included to enhance pellet quality or performance. Common additives include binders, which help in pellet formation, and lubricants, which reduce wear on machinery. Always ensure that additives are safe and suitable for your intended use.
How do I store homemade wood pellets?
Store homemade wood pellets in a cool, dry place to prevent moisture absorption. Use airtight containers or bags to maintain quality and prevent degradation. Ensure the storage area is well-ventilated to avoid condensation.
In summary, making your own wood pellets involves several key steps that require careful planning and execution. The process begins with selecting the appropriate raw materials, typically wood sawdust or other biomass, which must be free from contaminants. Proper drying and grinding of the material are crucial to achieving the right moisture content and particle size, which are essential for pellet formation. Once prepared, the material is compressed using a pellet mill, where heat and pressure transform it into dense pellets. Finally, cooling and storing the pellets correctly ensures their longevity and optimal performance for use in heating or cooking applications.
One of the most significant advantages of making your own wood pellets is the ability to control the quality and composition of the fuel. This not only allows for customization based on specific heating needs but also promotes sustainability by utilizing waste materials that might otherwise go unused. Additionally, producing your own pellets can lead to cost savings over time, especially for those who regularly use wood as a primary energy source.
Ultimately, the process of making wood pellets can be both rewarding and practical. It requires a combination of the right equipment, knowledge of the materials, and adherence to safety protocols. By following the outlined steps and understanding the importance of each stage, individuals can successfully produce high-quality wood
Author Profile
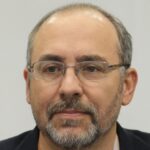
-
Darryl Norman is a seasoned entrepreneur and industry expert with a deep understanding of wood truss manufacturing and construction materials. As the President of Timberlake TrussWorks, LLC, Darryl played a pivotal role in shaping the company’s reputation for quality and precision. His leadership ensured that each truss met rigorous structural standards, providing builders with dependable components essential to their projects.
Beginning in 2025, Darryl Norman has shifted his focus to education and knowledge-sharing through an informative blog dedicated to wood truss manufacturing. Drawing from his extensive experience in the field, he provides in-depth insights into truss design, material selection, and construction techniques. This blog serves as a valuable resource for builders, contractors, and homeowners seeking practical guidance on truss systems and structural integrity.
Latest entries
- March 18, 2025General Wood TopicsWhat Color Is Ebony Wood? Unveiling the Rich Hues of This Luxurious Timber
- March 18, 2025Construction & FrameworkHow Can You Effectively Mount a Headboard to Your Wall?
- March 18, 2025General Wood TopicsCan Bees Really Eat Wood? Unraveling the Myths and Facts
- March 18, 2025General Wood TopicsDo Rabbits Really Chew on Wood? Exploring Their Eating Habits!