How Can You Successfully Sublimate Onto Wood?
Sublimation is a fascinating process that has revolutionized the world of printing, allowing for vibrant, long-lasting designs on a variety of surfaces. While most people are familiar with sublimating onto fabrics or ceramics, the art of sublimating onto wood is an exciting frontier that opens up a wealth of creative possibilities. Imagine transforming plain wooden items into stunning personalized gifts, home decor, or unique art pieces that capture memories and moments in striking detail. If you’ve ever wondered how to elevate your woodworking projects or create custom pieces that stand out, you’re in the right place.
Sublimating onto wood involves a specific set of techniques and materials that ensure the transfer of ink from a printed design onto the wood surface. To achieve the best results, it’s essential to understand the types of wood that work well for sublimation, as well as the preparation and finishing processes that can enhance the final product. This method not only allows for intricate designs but also ensures that the colors remain vibrant and resistant to fading over time.
In this article, we will explore the essential steps and tips for successfully sublimating onto wood, from selecting the right materials to the techniques that yield the best results. Whether you’re a seasoned crafter or a curious beginner, this guide will provide you with the knowledge
Preparing the Wood Surface
To achieve optimal results when sublimating onto wood, proper preparation of the surface is crucial. The wood must be clean, smooth, and free of any contaminants that could interfere with the sublimation process. Follow these steps to prepare the wood:
- Select a wood type that is suitable for sublimation, such as MDF (medium-density fiberboard) or specially coated wood.
- Sand the surface lightly with fine-grit sandpaper to ensure a smooth finish. This step helps to remove any imperfections that could affect the transfer.
- Clean the wood thoroughly using a lint-free cloth and a suitable cleaner, such as denatured alcohol, to remove dust, oils, and other residues.
- If necessary, apply a sublimation coating specifically designed for wood surfaces. This coating enhances the ability of the wood to accept dye during the sublimation process.
Creating and Printing the Design
Once the wood surface is prepared, the next step is to create and print your design. The design should be created in a graphics software that supports sublimation printing. Key considerations include:
- Color Mode: Set your design to CMYK mode, which is standard for sublimation printing.
- Resolution: Ensure a high resolution (300 DPI or higher) for a crisp and clear image.
- Mirroring the Image: Before printing, mirror the image. This is essential, as the design will be transferred in reverse onto the wood.
After completing the design, print it using a sublimation printer and sublimation ink. Ensure that you are using the correct paper for sublimation, as this can significantly impact the quality of the transfer.
Transferring the Design
The transfer process is where the sublimation dye is transferred from the printed paper to the wood surface. Follow these steps for successful transfer:
- Preheat the heat press to the recommended temperature, usually between 350°F and 400°F (175°C to 200°C).
- Position the printed sublimation paper face down on the prepared wood surface.
- Use heat-resistant tape to secure the paper in place to prevent it from shifting during the transfer process.
- Place the wood and printed paper into the heat press, ensuring even pressure is applied. Press for the recommended time, typically around 60 to 90 seconds.
After the pressing time has elapsed, carefully remove the wood from the heat press, allowing it to cool before removing the sublimation paper.
Finishing Touches
To enhance the durability and appearance of the sublimated wood, consider applying a clear coat or sealant. This step not only protects the design but also adds a finishing gloss that can enhance the visual appeal. Options for sealants include:
- Polyurethane
- Acrylic sealants
- Epoxy resin
Choose a sealant that is compatible with sublimation and suitable for the intended use of the wood item.
Sealant Type | Application Method | Drying Time |
---|---|---|
Polyurethane | Brush or spray | 1-4 hours |
Acrylic Sealant | Brush or spray | 30 minutes to 1 hour |
Epoxy Resin | Mix and pour | 24-48 hours |
Applying these finishing touches will ensure that your sublimated wood project is both beautiful and durable.
Understanding Sublimation on Wood
Sublimation is a process in which a solid transforms directly into a gas without becoming liquid, and in the context of printing, it refers to dye sublimation. This method is ideal for transferring vibrant images onto various substrates, including wood. However, not all wood types are suitable for sublimation. The wood must be coated with a special polyester material or treated to accept sublimation inks effectively.
Materials Needed
- Wood substrate (preferably MDF or pre-coated wood)
- Sublimation printer
- Sublimation ink
- Transfer paper
- Heat press machine
- Teflon sheets or parchment paper
- Heat-resistant tape
- Protective gloves
Preparing the Wood for Sublimation
To achieve the best results, proper preparation of the wood is essential. Follow these steps:
- Select the Right Wood: Choose wood that has a smooth surface and is treated with a polyester coating. MDF is often preferred for its uniformity.
- Clean the Surface: Wipe the wood with a lint-free cloth to remove any dust or oils that may affect adhesion.
- Cut to Size: If necessary, cut the wood to your desired dimensions using appropriate tools.
Designing Your Image
Creating a high-quality image is crucial for successful sublimation. Consider these tips:
- Use graphic design software to create or edit your design.
- Set the correct dimensions corresponding to the wood size.
- Ensure the resolution is high (300 DPI is recommended).
- Mirror the image before printing to ensure correct placement during transfer.
Printing the Design
Once the design is ready, follow these guidelines:
- Load Sublimation Ink: Ensure your sublimation printer is loaded with the correct sublimation ink.
- Print on Transfer Paper: Print your mirrored design onto sublimation transfer paper. Allow the ink to dry completely before proceeding.
Heat Pressing the Design onto Wood
The heat press is crucial for the sublimation process. Here’s how to do it properly:
- Preheat the Heat Press: Set the heat press to the recommended temperature (typically around 385°F to 400°F).
- Position the Design: Place the printed transfer paper on the wood, ensuring it is aligned correctly.
- Secure with Tape: Use heat-resistant tape to hold the transfer paper in place.
- Cover with Teflon: Lay a Teflon sheet or parchment paper over the design to protect it during pressing.
- Press the Wood: Close the heat press and apply firm pressure for the suggested time (generally 60-90 seconds).
- Remove the Transfer: Carefully open the heat press and peel away the transfer paper while it’s still warm.
Post-Press Finishing
Once the sublimation process is complete, consider these finishing touches:
- Cooling: Allow the wood to cool down completely before handling.
- Sealing: Apply a clear sealant to protect the design and enhance durability.
- Inspection: Check for any imperfections and make adjustments if necessary.
Troubleshooting Common Issues
If you encounter issues during the sublimation process, consider the following:
Issue | Possible Cause | Solution |
---|---|---|
Faded colors | Low-quality sublimation ink | Use high-quality inks |
Ghosting | Movement during pressing | Ensure proper alignment and secure paper |
Incomplete transfer | Insufficient heat or pressure | Adjust heat settings and increase pressure |
Streaks or lines | Dirty transfer paper or printer head | Clean the printer head and use clean paper |
By following these steps and guidelines, you can successfully sublimate onto wood, achieving vibrant and durable designs suitable for various applications.
Expert Insights on Sublimating onto Wood
Dr. Emily Carter (Materials Scientist, Sublimation Innovations Inc.). Sublimating onto wood requires careful preparation of the surface to ensure optimal adhesion and color vibrancy. It is essential to sand the wood to a smooth finish and apply a suitable coating, such as a polyester-based primer, to create a receptive surface for the sublimation ink.
Mark Thompson (Owner, Creative Sublimation Solutions). The key to successful sublimation on wood lies in the temperature and pressure settings of the heat press. I recommend using a temperature of around 400°F and a pressure of about 40-50 psi for approximately 60 seconds. This combination allows for the ink to transfer effectively into the wood fibers.
Lisa Nguyen (Graphic Designer and Sublimation Expert). Choosing the right type of wood is crucial for sublimation. Hardwoods like maple or birch yield better results compared to softwoods. Additionally, using a sublimation paper specifically designed for wood can significantly enhance the clarity and durability of the final product.
Frequently Asked Questions (FAQs)
What materials do I need to sublimate onto wood?
To sublimate onto wood, you will need sublimation ink, a sublimation printer, transfer paper, a heat press, and specially coated wood that is designed for sublimation.
Can I use any type of wood for sublimation?
Not all wood is suitable for sublimation. It is essential to use wood that has a polyester coating or is specifically designed for sublimation to achieve the best results.
What temperature and time settings should I use for sublimating wood?
Typically, a heat press should be set to around 385°F (196°C) and the transfer should be pressed for approximately 60 to 90 seconds. However, settings may vary based on the specific wood product used.
Do I need to prepare the wood before sublimation?
Yes, it is crucial to ensure that the wood surface is clean and free from dust or oils. If the wood is not pre-coated, applying a polyester spray can help improve the adhesion of the sublimation ink.
Can I sublimate onto unfinished wood?
Unfinished wood is not recommended for sublimation as it lacks the necessary coating. Sublimation requires a polyester surface to transfer the ink effectively.
What should I do if the sublimation image does not transfer properly?
If the image does not transfer correctly, check the temperature, pressure, and time settings on your heat press. Additionally, ensure that you are using the correct sublimation paper and that the wood is properly coated.
sublimating onto wood is a specialized process that requires careful preparation and the right materials. The key steps involve selecting the appropriate type of wood, applying a suitable coating, and utilizing a heat press to transfer the sublimation ink. Understanding the characteristics of the wood and the sublimation process is essential for achieving vibrant and durable results. Proper temperature and pressure settings are critical to ensure that the ink adheres effectively to the wood surface.
Valuable insights include the importance of using specially coated wood products designed for sublimation, as untreated wood may not yield satisfactory results. Additionally, experimenting with different types of coatings can help achieve various finishes and effects. It is also advisable to conduct test runs to fine-tune the settings before committing to a final project. This approach minimizes waste and enhances the quality of the final product.
Ultimately, mastering the art of sublimating onto wood opens up numerous creative possibilities for personalized gifts, home décor, and promotional items. By following best practices and leveraging the right tools, individuals can produce high-quality sublimated wood products that stand out in both aesthetics and durability. As the demand for custom wood items continues to grow, understanding this process will be invaluable for artisans and businesses alike.
Author Profile
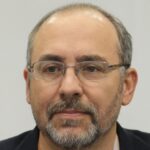
-
Darryl Norman is a seasoned entrepreneur and industry expert with a deep understanding of wood truss manufacturing and construction materials. As the President of Timberlake TrussWorks, LLC, Darryl played a pivotal role in shaping the company’s reputation for quality and precision. His leadership ensured that each truss met rigorous structural standards, providing builders with dependable components essential to their projects.
Beginning in 2025, Darryl Norman has shifted his focus to education and knowledge-sharing through an informative blog dedicated to wood truss manufacturing. Drawing from his extensive experience in the field, he provides in-depth insights into truss design, material selection, and construction techniques. This blog serves as a valuable resource for builders, contractors, and homeowners seeking practical guidance on truss systems and structural integrity.
Latest entries
- March 18, 2025General Wood TopicsWhat Color Is Ebony Wood? Unveiling the Rich Hues of This Luxurious Timber
- March 18, 2025Construction & FrameworkHow Can You Effectively Mount a Headboard to Your Wall?
- March 18, 2025General Wood TopicsCan Bees Really Eat Wood? Unraveling the Myths and Facts
- March 18, 2025General Wood TopicsDo Rabbits Really Chew on Wood? Exploring Their Eating Habits!